Hydrogen Pipelines: A New Frontier for EPC Project Heads
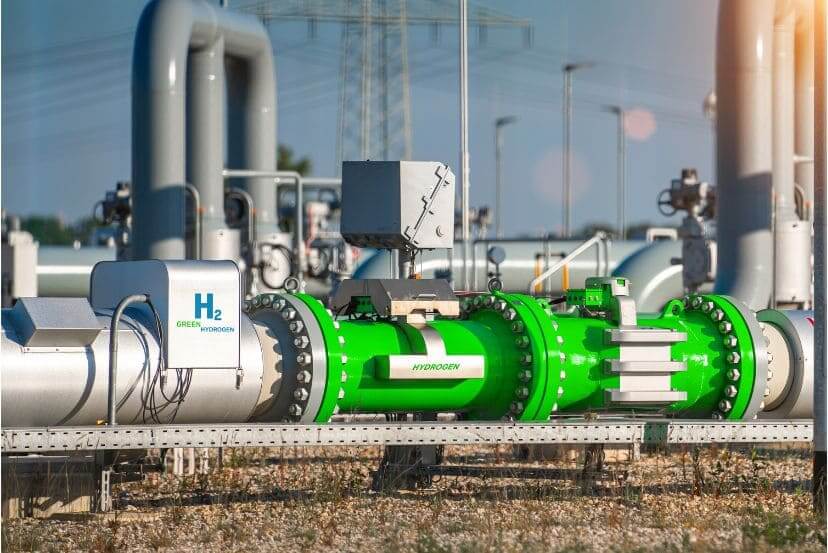
With the world rapidly shifting towards green energy, hydrogen stands out as the next big revolution in decarbonizing industries—bringing with it massive opportunities for EPC project heads who can lead in the creation of hydrogen pipelines.
Central to this shift is the development of hydrogen pipelines—an emerging frontier for project heads in the EPC (Engineering, Procurement, and Construction) sector. With custom fabrication playing a crucial role in the production and installation of these pipelines, the opportunities for innovation and growth in this space are immense.
The Rise of Hydrogen Pipelines
Hydrogen pipelines are designed to transport hydrogen over long distances, connecting production sites to consumption centers. These pipelines are essential for scaling up the use of hydrogen in industries such as manufacturing, energy, and transportation. While hydrogen’s potential as a clean energy source has long been recognized, its successful integration into infrastructure requires specialized fabrication and welding techniques.
As project heads take the lead on these transformative projects, there is a growing need for custom fabrication solutions tailored to the unique requirements of hydrogen pipelines. Unlike traditional pipelines that transport natural gas or oil, hydrogen pipelines face unique challenges such as hydrogen embrittlement, requiring advanced materials and welding expertise.
Custom Fabrication in Hydrogen Pipeline Development
Unlike traditional natural gas pipelines, hydrogen pipelines require custom fabrication due to hydrogen’s unique properties, such as its tendency to embrittle certain metals, making material selection and welding precision crucial.
Project heads working on hydrogen infrastructure must collaborate with fabrication experts to ensure pipelines are made with materials that can withstand hydrogen’s specific properties. Key factors include:
- Material Selection: Hydrogen’s small molecular size can cause embrittlement in certain metals, making it critical to select materials that can handle high pressures without degradation.
- Welding Precision: Given hydrogen’s high diffusivity, welding techniques must be impeccably executed, using methods such as autogenous welding or electron beam welding to eliminate micro fissures that could compromise pipeline integrity.
- Corrosion Resistance: Hydrogen pipelines must be designed to resist corrosion over time, especially in environments where moisture and other elements may be present.
Custom fabrication solutions offer the flexibility to design and manufacture these pipelines according to the exact specifications needed, ensuring they meet safety and performance standards. This presents a major opportunity for EPC project heads to leverage custom fabrication as a strategic tool for success in the hydrogen sector.
Challenges and Opportunities for EPC Project Heads
The shift toward hydrogen pipelines brings a new set of challenges for project heads. From selecting the right materials and welding techniques to navigating regulatory frameworks, the complexity of hydrogen pipeline projects cannot be overstated. However, with challenges come opportunities:
- Collaboration with Custom Fabricators: Collaborating with experts in hydrogen fabrication, such as those specializing in precision welding and advanced corrosion resistance, is essential for ensuring that hydrogen pipelines meet stringent industry standards. By working with experts who specialize in custom fabrication, EPC project heads can ensure their projects are optimized for both safety and efficiency.
- Sustainability Leadership: Hydrogen pipelines represent a significant step towards sustainability, helping industries reduce their carbon footprints. Project heads who take the lead in these projects position themselves as pioneers in the green energy revolution.
- Scalability: To scale successfully, project heads must invest in adaptable fabrication processes that can quickly pivot to meet expanding demands, positioning themselves at the forefront of the hydrogen infrastructure boom. This opens up new business opportunities for EPC project heads, particularly those who are prepared to scale their operations quickly and efficiently.
Why Custom Fabrication Is Key
Custom fabrication goes beyond traditional methods, incorporating innovative welding technologies like laser or friction stir welding to ensure leak-proof, high-integrity pipelines designed specifically for hydrogen. This requires expertise in welding, materials science, and pressure management. Project heads must ensure that their fabrication partners can deliver high-quality, durable solutions that meet safety regulations.
By opting for custom fabrication, EPC project heads can address the unique challenges posed by hydrogen transport. From material selection to welding precision, custom fabrication ensures that each pipeline is designed and built to last, minimizing maintenance costs and maximizing safety over time.
The Road Ahead: Hydrogen Pipelines and EPC Projects
As the world moves toward a hydrogen-powered future, EPC project heads are in a prime position to lead the charge. Hydrogen pipelines are set to revolutionize the way energy is transported, and custom fabrication will be critical in making these pipelines a reality. Those who embrace this opportunity and partner with custom fabrication experts will be well-positioned to succeed in this fast-growing sector.
Conclusion: The Future of Custom Fabrication in Hydrogen Pipelines
Now is the time for EPC project heads to seize the hydrogen revolution. By investing in custom fabrication and aligning with industry innovators, they can lead the charge in building a cleaner, more sustainable energy infrastructure. By leveraging custom fabrication solutions, project heads can ensure the pipelines they build are safe, efficient, and durable, driving the success of hydrogen infrastructure projects.
Explore Moglix Business Custom Fabrication Solutions: Custom Fabrication Solutions