Leading Indian manufacturing sector into a more self-reliant tomorrow
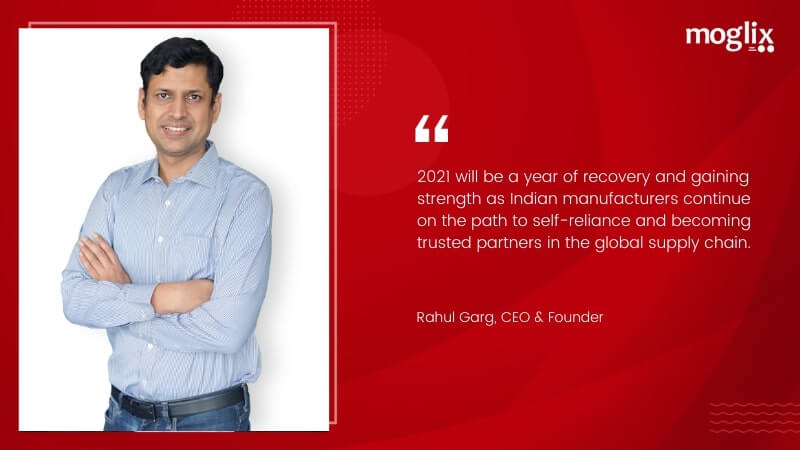
Leading Indian manufacturing sector into a more self-reliant tomorrow
2020 has been a once-in-a-lifetime year, bringing massive supply chain disruptions, innovation, and grit from the Indian manufacturing industry. The pandemic demonstrated the importance of digital and will further accelerate the offline to online shift. Manufacturing companies also experienced how data and analytics can help them to forecast the next to survive and thrive during challenges. MSMEs have been the backbone of this sector, and it will be critical to equip them with the right technology and supply chain financing to develop their strengths. Technology will be a critical lever for Indian manufacturers for MSMEs to adapt, innovate, and scale.
Also Read: Add to cart: Digital Procurement for B2B is the New Normal
B2B e-commerce platforms will provide a cost-efficient and seamless digital interface between MSMEs and enterprise customers in manufacturing. It will also connect the former to more opportunities to sell higher and better.
B2B e-commerce platforms can create alternate risk assessment models by analyzing MSMEs’ cash flow, turnover, customer portfolio, supplier ratings by leading OEM customers, and records of bad-debts, if any, and provide agile supply chain credit to them.
Listen to Moglix Podcast on Decoding The Digital in Supply Chains
2021 will be a year for recovery and gaining strength as Indian manufacturers continue on the path of self-reliance and becoming trusted partners in the global supply chain.
The Indian economy is all set to bounce back and emerge stronger from the year gone by. We should get ready to move to the next phase of growth and lead India’s manufacturing sector into a more self-reliant tomorrow. Wish you a happy and healthy new year!
Rahul Garg is Founder & CEO at Moglix.
To learn more about manufacturing and supply chain trends in 2021, download our ebook titled Road to Self-Reliant Manufacturing: Procurement and Supply Chain Insights for 2021 here.
Supply Chain Finance in 2021: Opportunity for MSMEs
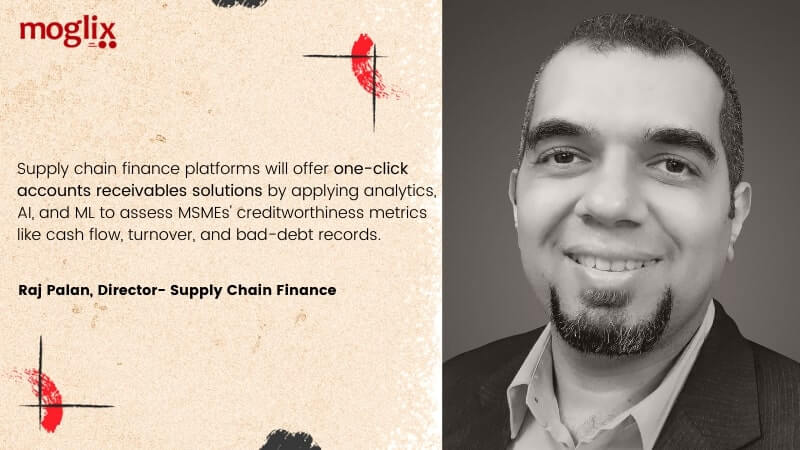
Supply Chain Finance in 2021: Opportunity for MSMEs
How can companies to manage liquidity better and strengthen their balance
MSMEs in India today accounts for 30% of the GDP, 33% of the manufactured output, and employ approximately 120 million people. Unfortunately, 5.4 million MSMEs are not registered with the government. Despite the best efforts of the Ministry of Finance to address liquidity issues through RS 3 lakh crore liquidity injection, MSMEs will step into 2021 with a more conservative outlook. Data available from the All India Manufacturers’ Organisation asserts that 43% of MSME units face the risk of closure due to delayed payments, longer than usual order to cash cycles, and ineligibility for access to collateral-free debt.
Read: MSMEs in 2021: Six key trends in B2B e-commerce
Both the MSME and OEM sectors in India will walk into 2021 with their respective legacy issues as they look to boost partnerships. However, digital supply chain finance will be a game-changer in OEM-MSME relationships and is likely to enable easier liquidity flow on demand.
2021 is likely to be the year when supply chain finance in India takes center stage. With the government taking policy initiatives to secure MSMEs’ payments within 45 days and redefining the investment brackets for micro, small, and medium enterprises, the liquidity strapped sector is likely to see a new sunrise on the heels of innovation in supply chain financing.
Blog: MSMEs, Is Your Supply Chain Finance Prepared?
While banks will continue to apply due diligence for approvals of collateral-based debt to MSMEs, new-age supply chain financing platforms will bring alternative risk assessment models in 2021. These new-age supply chain finance platforms through the application of analytics to assess MSMEs’ creditworthiness will offer one-click purchase invoice discounting, and also many more credit & neo banking solutions.
With digital receivables financing, MSMEs will have the opportunity to seek early payments from OEMs in lieu of token discounts on the total invoiced amount. For OEMs, advance payments will unlock an opportunity to leverage idle working capital to make their operating expenses (OPEX) more cost-efficient.
Raj Palan is Director – Supply Chain Finance at Moglix
To learn more about manufacturing and supply chain trends in 2021, download our ebook titled Road to Self-Reliant Manufacturing: Procurement and Supply Chain Insights for 2021 here.
MRO in 2021: Digital Supply Chain Models on the Rise
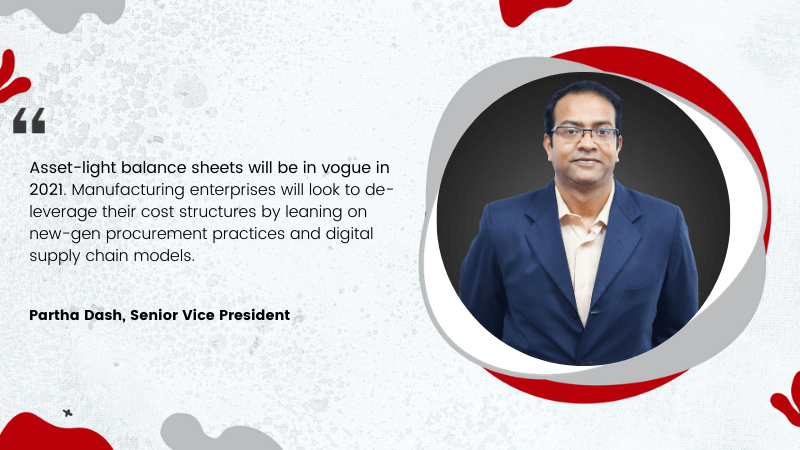
MRO in 2021: Digital Supply Chain Models on the Rise
No other category of industrial supplies succinctly depicts the difference between cost and value in manufacturing as MRO does. While MRO accounts for only 20% of the total procurement spending of manufacturing enterprises, the value of the finished goods that it supplies is 5 to 6 times greater than the unit costs. If 2020 saw manufacturing enterprises being hit by disruptions in the MRO supply chain, 2021 will see manufacturing enterprises take a radically different approach to MRO procurement with a focus on cost-efficiency, agility, and risk mitigation. E-procurement solutions for MRO will transform from being good to have to a need to have.
Manufacturing enterprises will start in 2021 with a sharp focus on exploring ways to be more cost-efficient. Stressed balance sheets coupled with losses of supplier downtime and man-hours on the factory floor from 2020 will require procurement leaders to broaden the lens of cost-efficiency to include both operational and capital expenditures.
Also Read: Spending up to 15% More on MRO? Fragmented Supply Chain is the Reason
Reduction in operational expenditure on indirect procurement like MRO will require procurement leaders to get more visibility into MRO spending, product category spending, consumption-reconciliation rates, and ordering and carrying costs. The demand for higher transparency into indirect procurement spending and OPEX reduction will manifest a shift towards e-procurement solutions. E-procurement solutions that will enable manufacturers to aggressively control their indirect procurement outlay in 2021 will include e-requisition, e-catalogs, supplier volumes-value spread, and inventory management.
Listen to Moglix Podcast on Decoding The Digital in Supply Chains
Manufacturing enterprises that work with a large spread of suppliers for MRO procurement will have opportunities to generate 2-3% cost savings by analyzing big data with artificial intelligence and machine learning capabilities to resolve the challenges of 3Vs: volumes, velocity, and variety of procurement data, and consolidate their supplier bases.
Furthermore, MRO procurement costs are likely to inflate at the rate of 0.2% per annum till 2023 even as policymakers and health regulators will continue to monitor the effectiveness of the COVID19 vaccines. Given the supply chain disruptions in 2020, manufacturing enterprises are likely to move towards annual rate contracts to seek effective insulation from the projected inflationary pressures on MRO.
Asset-light balance sheets will be in vogue in 2021. Manufacturing enterprises will look to de-leverage their fixed and operating cost structures through CAPEX and inventory optimization. In 2021, manufacturing enterprises will have the opportunity to achieve this goal by building new-gen procurement practices and digital supply chain models. Cloud-based solutions in MRO procurement will become the norm in 2021 and organizations will focus on digitizing their workflows to increase transparency and visibility of data.
Cloud-based delivery models in MRO procurement will become the norm in 2021 because these can host the software application, procurement data, and AI & ML algorithms on a centralized repository. Most importantly, cloud-based delivery models for MRO e-procurement require zero CAPEX on additional digital infrastructure.
Partha Dash is Senior Vice President, Enterprise Business at Moglix.
To learn more about manufacturing and supply chain trends in 2021, download our ebook titled Road to Self-Reliant Manufacturing: Procurement and Supply Chain Insights for 2021 here.
Procurement in 2021: Leveraging Technology-led Procurement
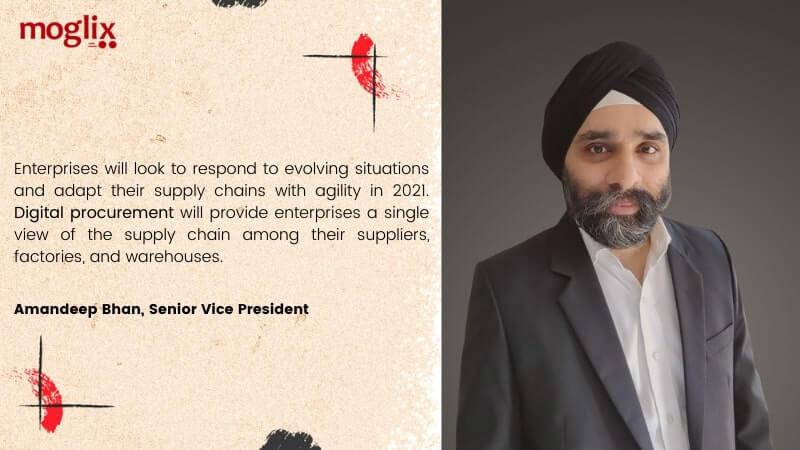
Procurement in 2021: Leveraging Technology-led Procurement
Every manufacturing company navigates make vs. buy decisions. Cost-efficient procurement at each level in the supply chain is essential to generate a desirable bottom-line impact for large OEMs and end consumers. Cost-efficient procurement is the key to stimulating the demand for goods made in India. One of the easiest ways to achieve this is via technology-enabled procurement. While cost efficiency has always been a critical theme for procurement leaders and managers, 2021 will see enterprises broadening the horizons of procurement costs. They will move from the earlier view of savings on product costs to savings on the total cost of ownership (TCO) of procurement. What will drive this transition towards digital procurement in 2021?
2021 will see procurement leaders search for new avenues of agile cost reduction in the supply chain upstream to achieve the desired balance sheet impact. Robotic process automation will enable enterprises to reduce procurement costs by up to 65%; that too within a few financial quarters. As such robotic process automation will be one of the significant technologies to impact digital procurement in 2021.
Read More: Procure-to-Pay: Your Time Machine to a Future of Automation
Enterprises that were still in the pilot purgatory stages will commit more resources and outlay to their digital procurement initiatives in 2021. Enterprises have learned about the value of uninterrupted supplies and will lean towards risk-averse procurement practices in 2021. Having learned that digitization is the need of the hour, they will step into 2021, choosing from the digital technologies that can make their supply chains more robust and transparent.
Risk-averse procurement behavior in 2021 will see enterprises investing in technology that will digitally connect business processes to physical assets. It will also ensure all-weather procurement continuity.
Enterprises will step into 2021 with a cognizance of the need to respond to incremental information on evolving situations with agility and adapt their supply chains accordingly.
Read More: Digital Procurement for B2B is the New Normal
Leaning on digital procurement will allow enterprises to achieve this agility by enabling a single view of the supply chain among their suppliers, factories, warehouses, and logistics services providers. The digital connect will happen across three levels of the B2B order fulfillment cycle: procurement to engineering, engineering to manufacturing and manufacturing to order fulfillment
Amandeep Bhan is Senior Vice President at Moglix.
To learn more about manufacturing and supply chain trends in 2021, download our ebook titled Road to Self-Reliant Manufacturing: Procurement and Supply Chain Insights for 2021 here.
Infrastructure in 2021: Heavy Lifting of Infrastructure with Technology

Infrastructure in 2021: Heavy Lifting of Infrastructure with Technology
Leading the charge towards bolstering India’s economic immunity in 2021 will be infrastructure sub-sectors of Indian manufacturing. India’s infrastructure verticals have identified a requirement of INR 50 lakh crore worth of investment.
2021 marks a paradigm shift in India towards the creation of Infrastructure which acts as an economic and jobs multiplier. The four megatrends in terms of Government initiatives seem to bode well for EPC companies. These are the INR 100 lakh crore National Infrastructure Pipeline, the INR 100,000 crore MGNREGA outlay, structural reforms in 8 sub-sectors, and health infrastructure. These eight sub-sectors are coal, minerals, defense production, airspace management, MRO, and power distribution.
Listen to Podcast: Now and Next in the Infrastructure Sector
The multiplier effect of investments in the infrastructure space will drive up the demand for direct and indirect materials. 2021 will also see the rise of agile procurement in the infrastructure sector. Companies in the infrastructure sector in India have traditionally faced high project overrun costs to the tune of INR 4 lakh crores, which is 44% higher than their planned project costs. With infrastructure spending being a defining theme of India’s supply chain overhaul, the demand for agile procurement of industrial supplies from EPC companies will be higher than ever before.
Furthermore, EPC companies are also likely to switch away from their previous obsession with the JIT model and move towards a more de-risked model. EPC companies are more likely to maintain higher buffer stocks of MRO in 2021 to ward off the risks of supplier disruptions.
While 2021 is likely to see India’s infrastructure engines roaring back to growth, taking advantage of an expansionary fiscal policy. As a result, investments are likely to see headwinds for EPC companies.
Download Case Study: MRO Procurement at Scale through Workflow Digitization of large EPC company
Abheet Dwivedi is Director, Infrastructure at Moglix.
To learn more about manufacturing and supply chain trends in 2021, download our ebook titled Road to Self-Reliant Manufacturing: Procurement and Supply Chain Insights for 2021 here.
Moglix in 2020: The Year of Supply Chain
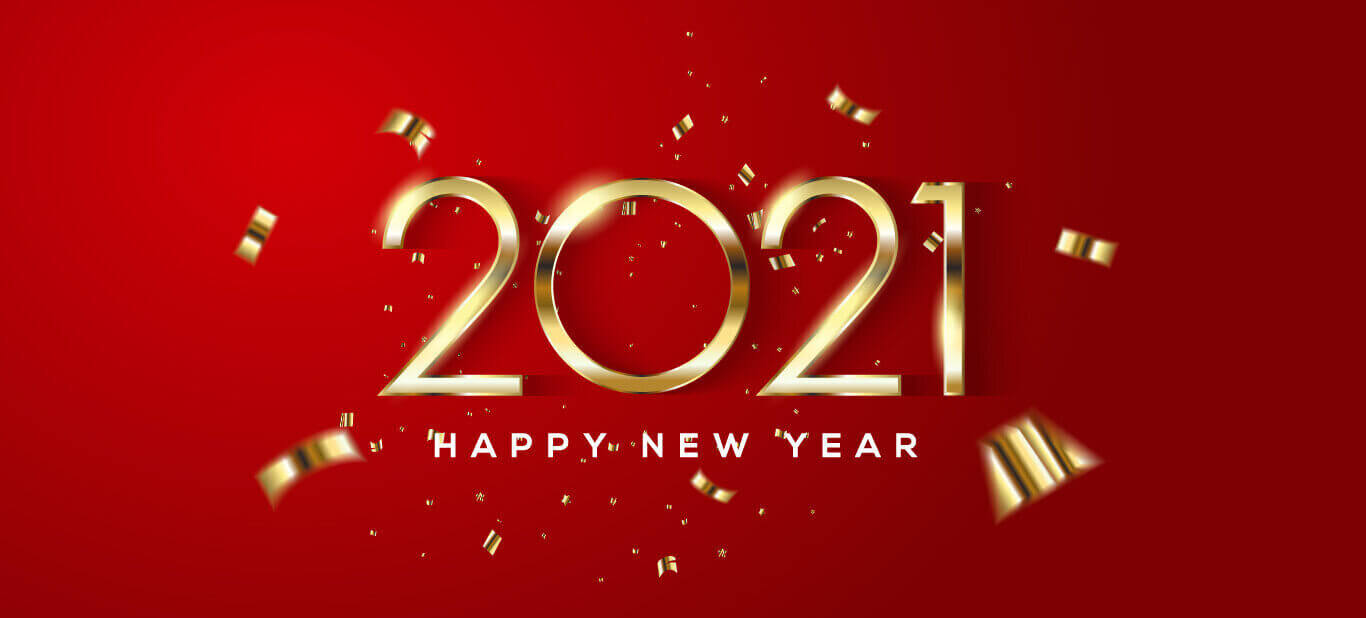
Moglix in 2020: The Year of Supply Chain
Everything that we reimagined at Moglix in 2020Read More
Packaging in 2021: Contactless Packaging is the New Normal
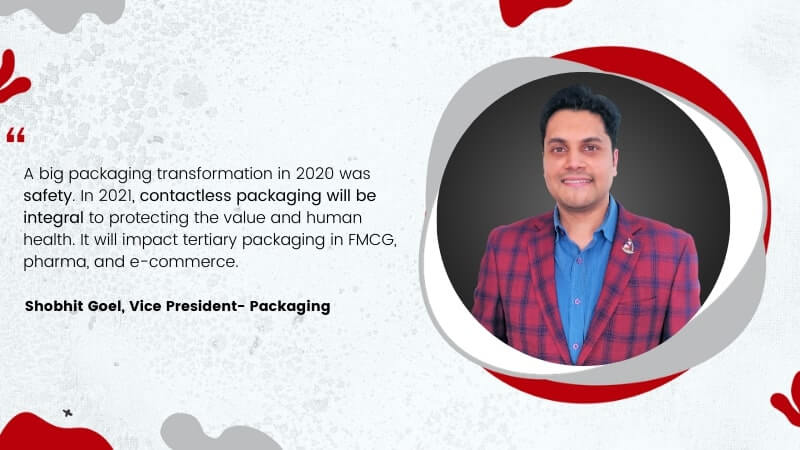
Packaging in 2021: Contactless Packaging is the New Normal
A big packaging transformation for businesses and consumers in 2020 was safety. In 2021, the contactless packaging of goods will be integral to protecting the value and human health across all supply chain journeys. The evolution in the packaging industry is likely to change the tertiary packaging of goods, especially in the FMCG, pharma, and e-commerce sectors.
People will step into 2021 with a sense of renewed hope and expectations around the multiple variants of the vaccine for COVID19. The successful rollout of the vaccine for COVID19 will require drug manufacturers, packaging businesses, logistics services providers, and warehousing businesses to seamlessly collaborate in the supply chain journey.
Traditionally drug makers and distributors have trusted vials for pharmaceuticals packaging. However, pharmaceuticals packaging businesses will have to reimagine the status quo for the vaccine. First, despite being the standard packaging solution, vials are impacted by sodium borate concentrates that may alter drug effectiveness. Second, the vaccines will require secure primary packaging solutions for storage and mobility in temperature-controlled environments.
Read: How can sustainable packaging enable cost reduction during covid19
Innovations in frozen food and beverage packaging solutions will be integral to increasing the food shelf life, reducing food wastage, and addressing the challenges of global hunger and malnutrition in 2021.
What will also be integral to enterprises’ efforts to build consumer confidence will be their e-commerce enablement. People will continue to maintain social distancing and be careful about the safety of their goods in 2021. As a result, manufacturers will have to explore ways to package their goods for e-commerce enablement. They will also have to ensure that goods are insulated from direct contact with people.
Download Case Study: 4PL Packaging Solutions Enabled Last-Mile Supply Chain Efficiencies for the World’s Largest E-Commerce Enterprise
E-commerce packaging, especially primary packaging will continue to be in demand in 2021. Packaging solutions providers will have to offer packaging solutions that will be more ergonomic, consume less shelf space, and lightweight, in order to optimize cost, insurance, and freight charges.
Shobhit Goel is Vice President, Packaging at Moglix.
To learn more about manufacturing and supply chain trends in 2021, download our ebook titled Road to Self-Reliant Manufacturing: Procurement and Supply Chain Insights for 2021 here.
MSMEs in 2021: Six key trends in B2B e-commerce
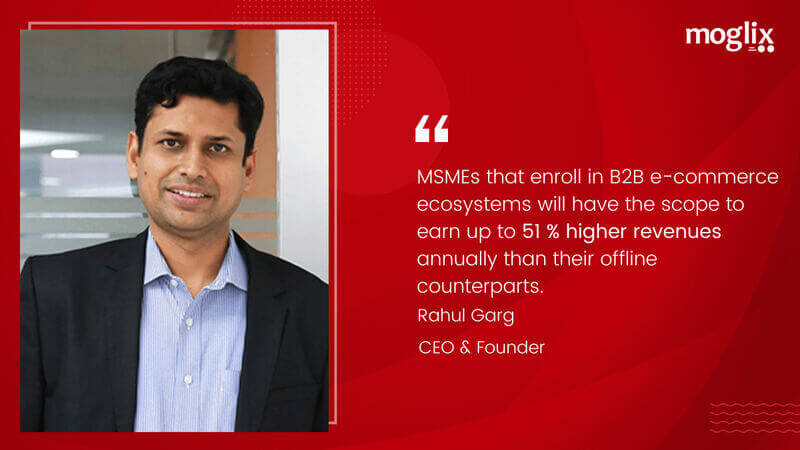
MSMEs in 2021: Six key trends in B2B e-commerce
Rahul Garg, our CEO & Founder shares insights on MSMEs in 2021. He discusses the six key trends emerging in B2B e-commerce that will jumpstart small business recovery. The B2B platforms will enable MSMEs to expand smoothly, penetrate deep into remote locations across the country, get a hold of their cash flow and finances, and add value to the global value chain.
‘MSMEs that enroll in B2B e-commerce ecosystems will have the scope to earn up to 51 per cent higher revenues annually than their offline counterparts.’
Rahul also explains the challenges that the sector has faced during 2020 and how these could be prevented in the future. Digitization, agility, and resilience are the keywords for 2021.
B2B e-commerce platforms will provide a cost-efficient and seamless digital interface between MSMEs and enterprise customers in manufacturing and connect the former to more opportunities to sell higher and better, thanks to the 5G digital infrastructure.
Delayed payments have been a source of concern for MSMEs through the pandemic. While the government’s plan to secure MSMEs’ payments within 45 days is laudable, they will require short-term supply chain credit sources. Banks have to follow due diligence to optimize the risks of NPAs in their balance sheets and therefore have to anchor MSME debt offerings to collaterals.
On the other hand, B2B e-commerce platforms can use analytics and big data and create alternative risk, assessment models. They can use digital capabilities to analyze MSMEs’ cash flow, turnover, customer portfolio, supplier ratings by leading OEM customers, and records of bad-debts, if any, and provide agile supply chain credit to them.
Read MoreHR Priorities for 2021: Director- Human Capital
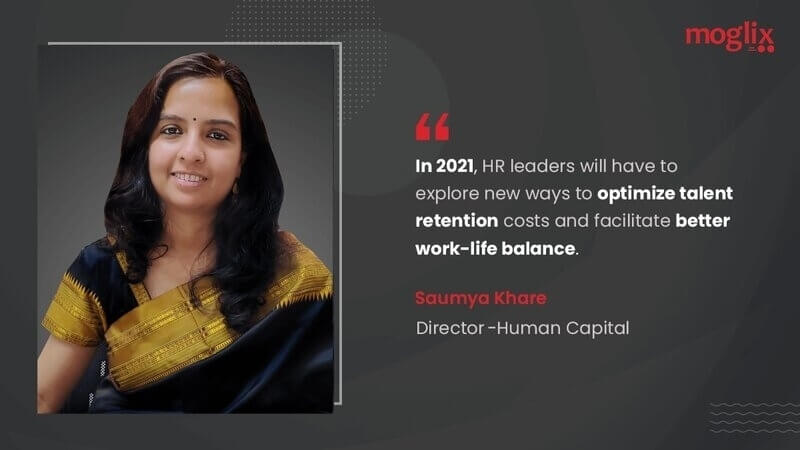
HR Priorities for 2021: Director- Human Capital
Saumya Khare, Director of Human Capital talks about the HR priorities for 2021. She throws light on the learnings from 2020, the growing need for adaptation
In 2021, HR leaders will have to explore new ways to optimize talent retention costs and facilitate better work-life balance.
Saumya elaborates on the growing need for digitization and analytics in the existing models, to not only revamp the current processes but to also innovate methods to grow the organization as a whole. what the future workplaces would look like and the best practices they should start following in order to build workplace 4.0.
Read MoreHR leaders will have to ensure that functional teams build the strength to sustain sudden changes to team structures, health risks, and logistical disruptions. They will have to provide greater multi-tasking, learning by doing, and familiarize the staff with the new roles as contingency measures.
My First Job: Amandeep Bhan, Sr.VP- Strategic Partnerships
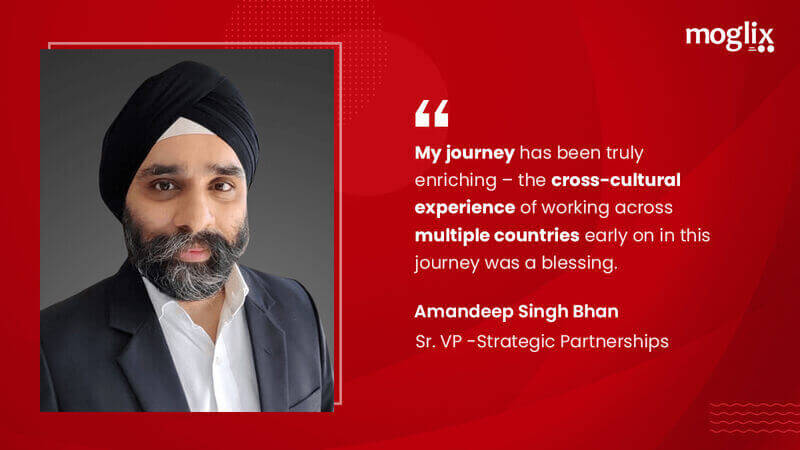
My First Job: Amandeep Bhan, Sr.VP- Strategic Partnerships
Amandeep Bhan, Senior Vice President- Strategic Partnerships talks about his career path. He shares his experience right from his family business to being with TCS, SAP, and now, Moglix. In this candid conversation with TimesJobs, Amandeep also shares the skills he acquired, his learnings from the people he worked with, the turning point in his career, and the most crucial step he took.
Read MoreI have continued to learn over the years, and my first learning is to stay curious and humble.