Employee Engagement and Wellbeing: The First Priority
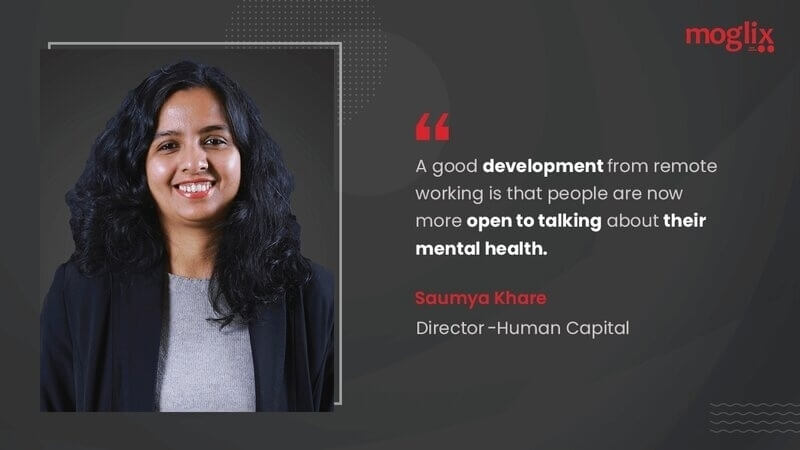
Employee Engagement and Wellbeing: The First Priority
Saumya Khare, Director-Human Capital talks about employee engagement & wellbeing. She emphasizes the importance of taking care of employees’ mental health, whenever and however you can. There is a bunch of new initiatives taking place across organizations, the first priority is keeping up with employee engagement & well-being. She shares the best practices that HR can take, the top being
Whether working from home, remote locations, or the workplace, digitization has now become integral to the way we communicate. While businesses differ in terms of their digital maturity, all businesses are now realizing the value of online workflow platforms.
Saumya throws light on the benefits of making digital HR processes to not only stay connected but to also build the organization stronger, which in itself is a cultural change. Every organization which truly aims to be the business of tomorrow and build a resilient future needs to re-imagining its way of working and try to then ease it out for everyone by being more inclusive and proactive.
Read MoreSelf-Reliance: An Agenda for Indian Manufacturing in 2021 and Beyond
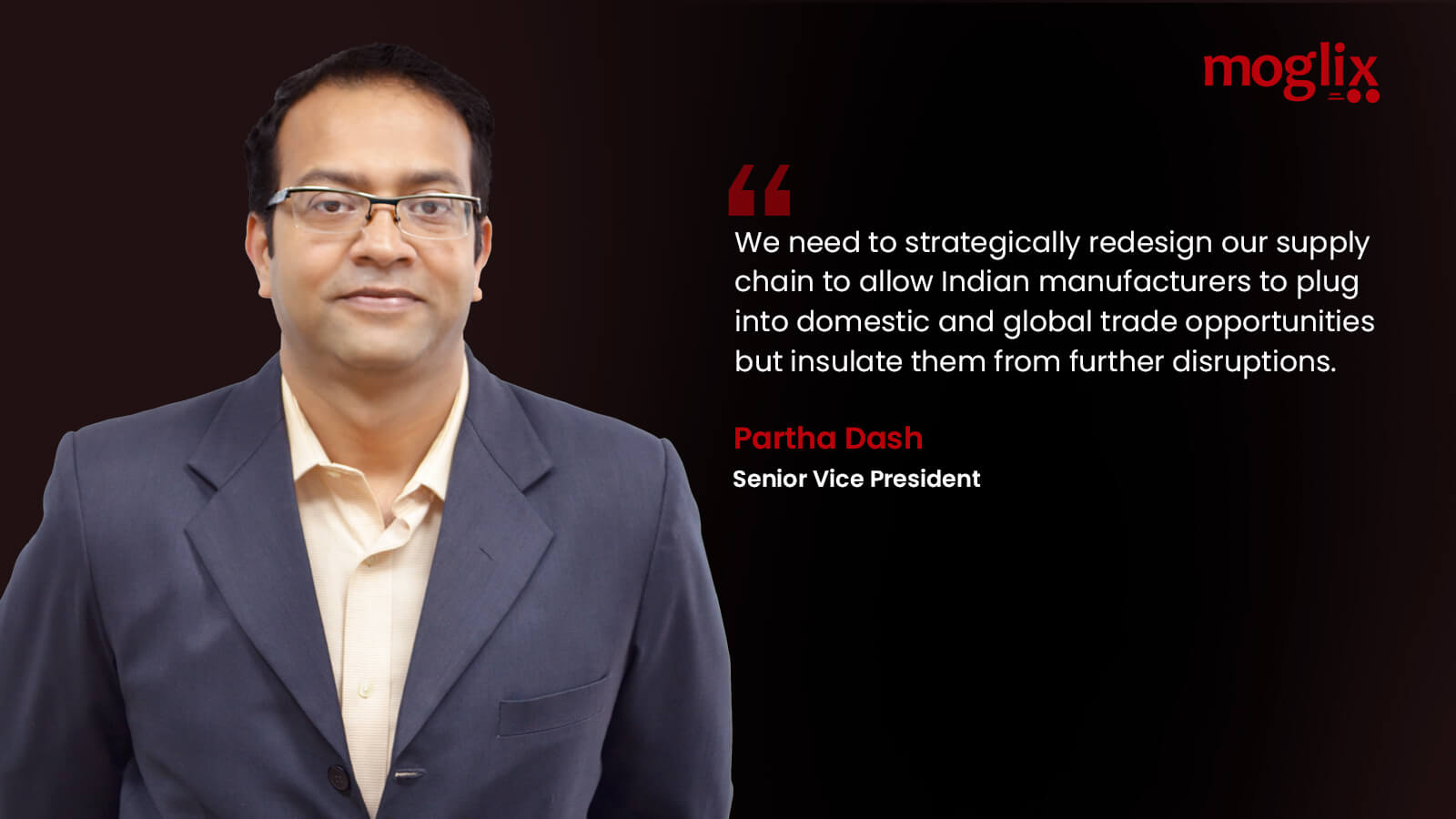
Self-Reliance: An Agenda for Indian Manufacturing in 2021 and Beyond
Self-reliance is the agenda for Indian Manufacturing in 2021 and beyond. Partha Dash, Senior Vice President, Moglix Business shares his insights on how the current year has promoted the of being self-reliant, agile, and resilient.
India’s quantum leap to the 63rd position in the Ease of Doing Business rankings bears testimony to how far we have come. Now is the time to take the next steps. We need to bring agility and visibility to the procedures covering the starting of a new business to the compliance with regulatory requirements such as land acquisition, getting clearances for capacity expansion and obtaining permits and licenses.
Partha also discusses the dire need
Read MoreWe need to strategically redesign our supply chain to allow Indian manufacturers to plug into domestic and global trade opportunities but insulate them from further disruptions.
Moglix Founder on Whether You Should Go Solo or Get Co-Founders
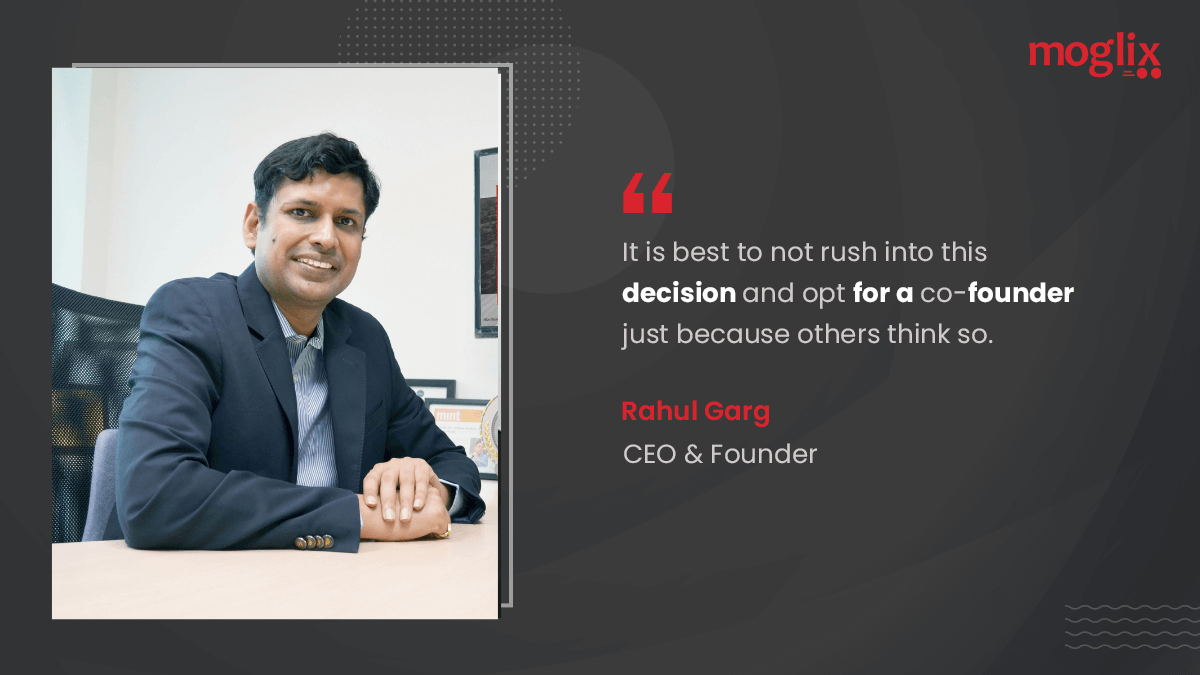
Moglix Founder on Whether You Should Go Solo or Get Co-Founders
Rahul Garg, CEO & Founder, Moglix Business speaks on the classic entrepreneur conundrum – Go Solo or get Co-founders? He shares his journey and experience as a solo founder of Moglix.
It is best to not rush into this decision and opt for a co-founder just because others think so.
Rahul also talks about scaling up the founding team.
Read MoreYou need to have a proper HR perspective when hiring, even in the early days. My hiring bar was very high even early on. I think the people I hired then, still are among the smartest people in the country. No wonder then that of the six founding team members, five remain at Moglix even after five years since the company’s founding.
Podcast E10: Decoding The Digital in Supply Chains
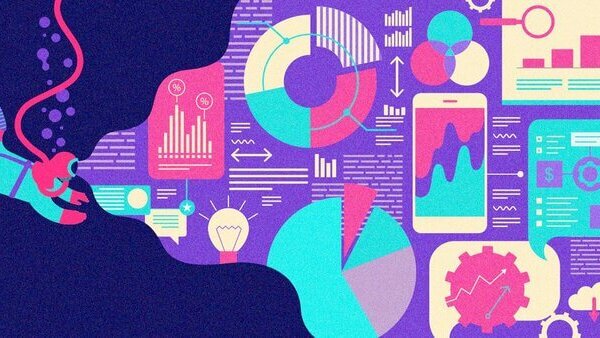
Podcast E10: Decoding The Digital in Supply Chains
Podcast E9: Moglix CEO on Growth, Profitability and Future Plans of the Company
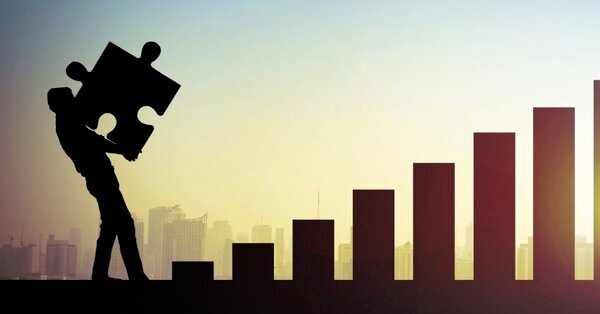
Podcast E9: Moglix CEO on Growth, Profitability and Future Plans of the Company
Interview: Moglix CEO on Future Plans and Acquisitions
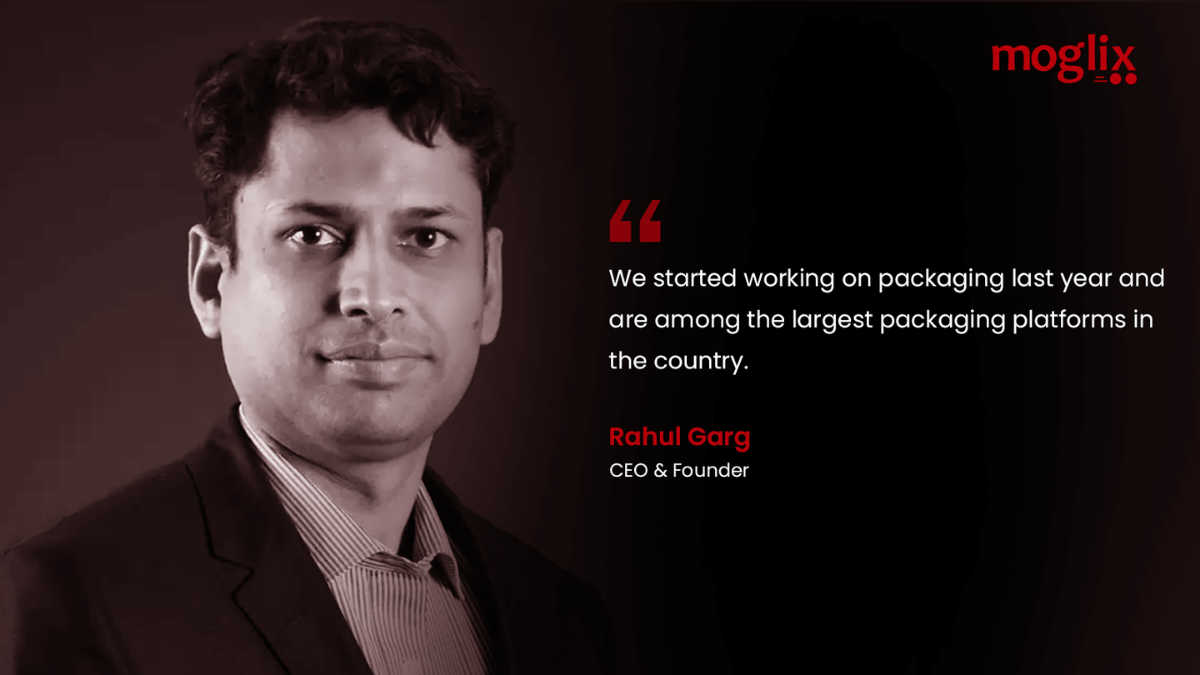
Interview: Moglix CEO on Future Plans and Acquisitions
Rahul Garg, CEO & Founder, Moglix business talks about future plans and Moglix marking its presence across 35 locations in India with its recent expansion to Goa & Guwahati. Rahul shares his insights on the manufacturing sector, the impact of the ongoing crises on it, and how its supply chains are under a major transformation.
Moglix has captured 80% of the manufacturing hubs and is now aiming to go for smaller businesses in order to strengthen the network and spread its roots in smaller cities too.
Saumya Khare, Director of Human Capital on Career At Moglix
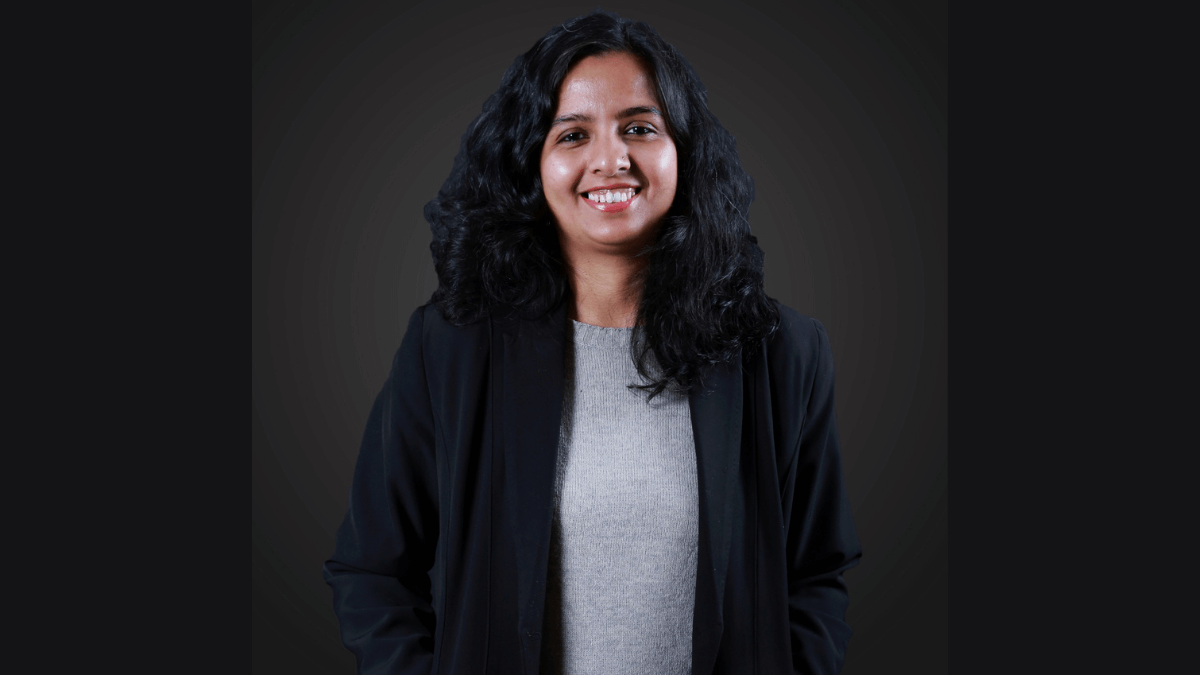
Saumya Khare, Director of Human Capital on Career At Moglix
Saumya Khare, Director- Human Capital, Moglix Business discusses the career at Moglix. She elaborates on the tips that one can use while preparing to join Moglix and what the hiring process is.
Along with this, Saumya also shares her insights on the job market in e-commerce sector and how things are keeping up with the ongoing crises. She emphasizes on certain trends coming up in the new normal and what is that organizations demand.
Read MoreMoglix Expands Its Supply Chain Operations in Goa and Assam
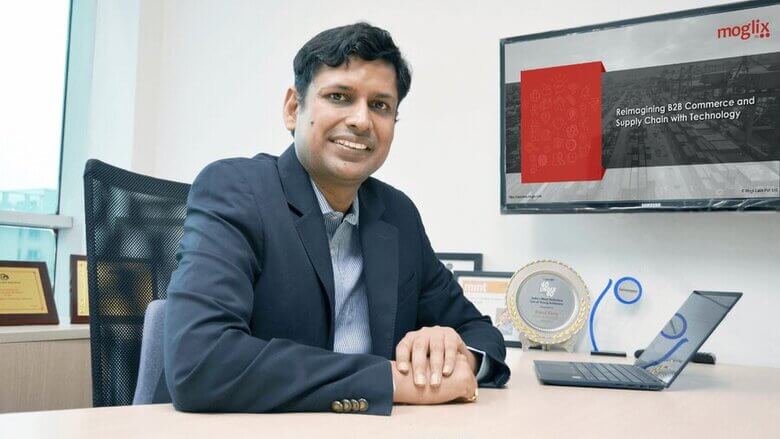
Moglix Expands Its Supply Chain Operations in Goa and Assam
Moglix expands its supply chain operations to Goa & Assam in order to further strengthen its mission of creating digital-enabled supply chains. Moglix is now present across 35 locations PAN India, forever changing the face of manufacturing, offering digitally enabled supply chain solutions for indirect procurement to its customers in the enterprise and SME segments.
Moglix has been keeping the B2B supply chain up and running for its customers in the manufacturing sector as the economy looks to regain lost momentum ahead of the festive season of Diwali.
Read More4 Essential Packaging Supply Chain Solutions for Manufacturers Ahead of Diwali in 2020
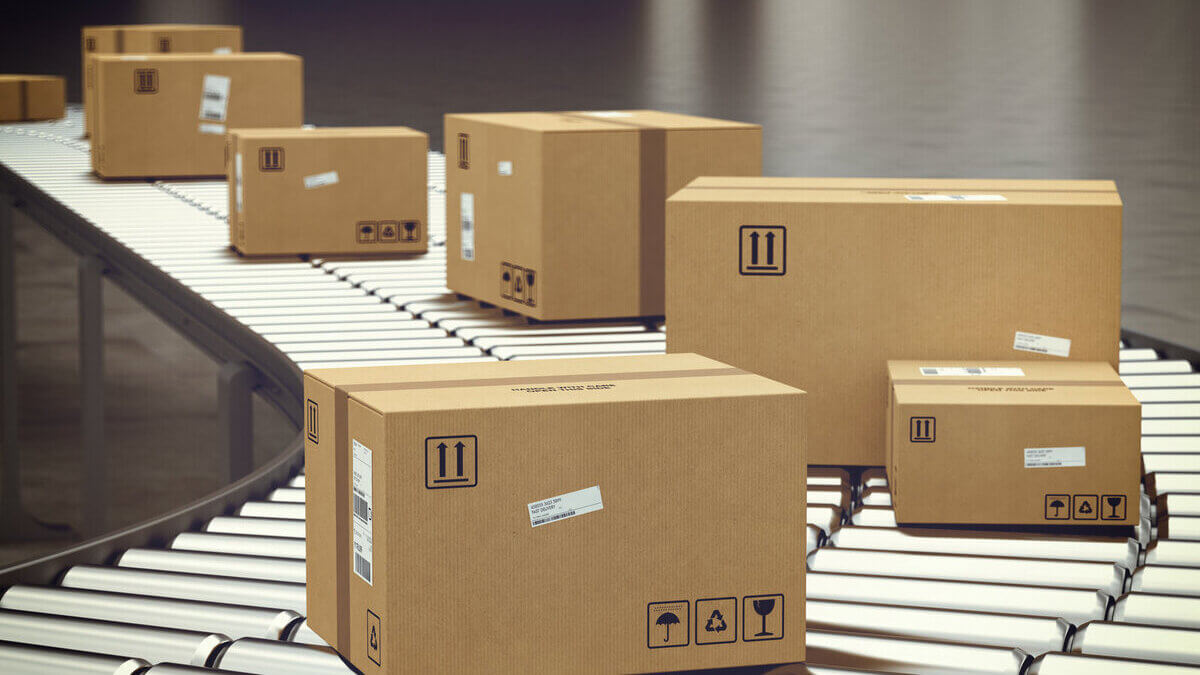
4 Essential Packaging Supply Chain Solutions for Manufacturers Ahead of Diwali in 2020
Exactly how robust are your packaging supply chain solutions? If you are a manufacturer, you understand that Diwali 2020 is going to put your packaging supply chain solutions to the ultimate test.
On the one hand, health and supply chain risks due to the COVID19 pandemic loom large. Sourcing the right packaging SKUs, optimising quality and cost, warehousing, and reducing last-mile friction are four major challenges this year. On the other hand, Diwali 2020 is the beginning of yet another busy festive season in India.
You and your team of supply chain managers need to map the pain points and make contingency plans. You also need to optimize your packaging supply chain management systems and be prepared to create great customer experiences. Here, we share a compact list of four essential packaging supply chain solutions that will help you prepare. Let’s explore.
Challenge 1: Sourcing the Right Packaging SKUs
Share the types of packaging solutions that you require with your packaging suppliers. Communicate your custom packaging solution specifications and ask for relevant samples and new product development capabilities.
Share the details of your brand persona and an outline of who your customers are. What are your unique supply chain challenges? Does your packaging resonate with your brand’s value proposition?
If you operate at the point of origin of the supply chain, prioritize the primary packaging SKUs that will contain the contents of your product. If you are a distributor, you need to focus on secondary packaging. If you have a country-wide distribution network, map the last-mile challenges and ask for relevant tertiary packaging solutions.
Pro-Tip: Look for an integrated packaging supply chain solutions provider that has a large network of local packaging suppliers across the country. Yoru supply chain managers will get a single point-of-contact and can get turnkey packaging solutions on-demand. Further, you will save big on procurement costs and supplier collaboration efforts.
Challenge 2: Quality and Cost Optimization
Create a list of quality specifications for your packaging SKUs. Map the overall order size and procurement costs. Share your packaging quality and cost requirements with your supplier. Furthermore, seek new ideas to save costs on your packaging from your suppliers.
While optimizing costs, also look at how your total packaging costs impact the unit economics and pricing of your products. Explore ergonomic packaging designs and products that allow you to accommodate more volumes per packaging unit.
Furthermore, give due consideration to the weight of the packaging materials and its direct bearing on the cost, insurance, and freight (CIF) of your supply chain. For instance, corrugated cardboard boxes, paper bags and paper boxes are lightweight and allow supply chain and logistics personnel to add more cargo per packaging unit. Doing so makes the shipping process more cost-effective.
If your enterprise is bound by environmental compliance regulations, ask your packaging suppliers to demonstrate their sustainable packaging offerings along with the corresponding impact on the carbon footprint.
Pro-Tip: Conduct a packaging audit at your plant locations periodically. A packaging audit entails a thorough diagnosis of your packaging supply chain and spend-analysis. You can derive intuitive insights from your data analytics to optimise the quality, costs, and risks in your packaging supply chain. A packaging audit is especially recommended to maintain smooth business continuity throughout the year and peak load seasons like Diwali.
Challenge 3: Warehousing and Inventory Stock-Out
The shortage of warehousing space and inventory stock-out are two pertinent challenges during the festive season. Map your warehouse capacity in advance and ask your supply chain managers to share data on the packaging consumption rates during the peak season. Engage with your packaging suppliers. Seek the details of the expected time of arrival (ETA), lead time and order processing time that they need to deliver any unplanned packaging orders in the face of an inventory stock-out.
Furthermore, opt for local sourcing options this year to steer clear of the risks of supply chain disruptions. Prioritize the location of your packaging solutions suppliers and their access to multimodal transport. Search for a packaging vendor with integrated logistics and supply chain management capabilities across India.
Pro-Tip: Choose an integrated supply chain solutions provider as your packaging partner with a large network of logistics partners and warehouses. If you are a multi-plant manufacturer opt for a captive supplier. A captive supplier is one that will hold your packaging inventories on their account books at your site location. Partnering with a captive supplier will ensure you JIT delivery of all types of packaging units at your site on demand.
Challenge 4: Last-Mile Friction
While last-mile delivery has always been a challenge in the B2B supply chain, this year’s COVID19 pandemic only compounds its magnitude. With social distancing norms in place and customers demanding access to products from the comfort of their homes, you need to reimagine the last-mile of your supply chain journey.
This is especially true for consumer goods, pharmaceuticals, e-commerce, food & beverages, and chemicals because of the limitations of shelf-life and expiration date. Gaining visibility into the last-mile journey is the key to ensuring that your products reach customers fresh, compact, and safe. Opt for cost-effective and smart packaging solutions like RFID tagging. Use digital packaging systems to ramp up your tertiary packaging, track the movement of your products, and reimagine the customer experience.
Pro-Tip: Leverage smart packaging technology to zero down the gaps with your customers. You can map end-user trends, consumption patterns, and purchase volumes. You can also adopt reusable and recyclable packaging by integrating technology with your packaging.
For instance, you can insert a sensor in standard wooden packaging boxes and track their reverse logistics, recycling, and reuse. Doing so, you can reduce both your carbon footprint and packaging costs.
Prepare for the New Normal and New Possibilities in Packaging Supply Chain This Diwali
This year’s Diwali will be different from yesteryears. Prepare your supply chain for the new normal. Ramp up your packaging supply chain in advance and be open to new possibilities during the festive and holiday seasons. Browse Moglix Packaging Solutions and connect with our experts to learn more.
Startup Of The Year Award 2020
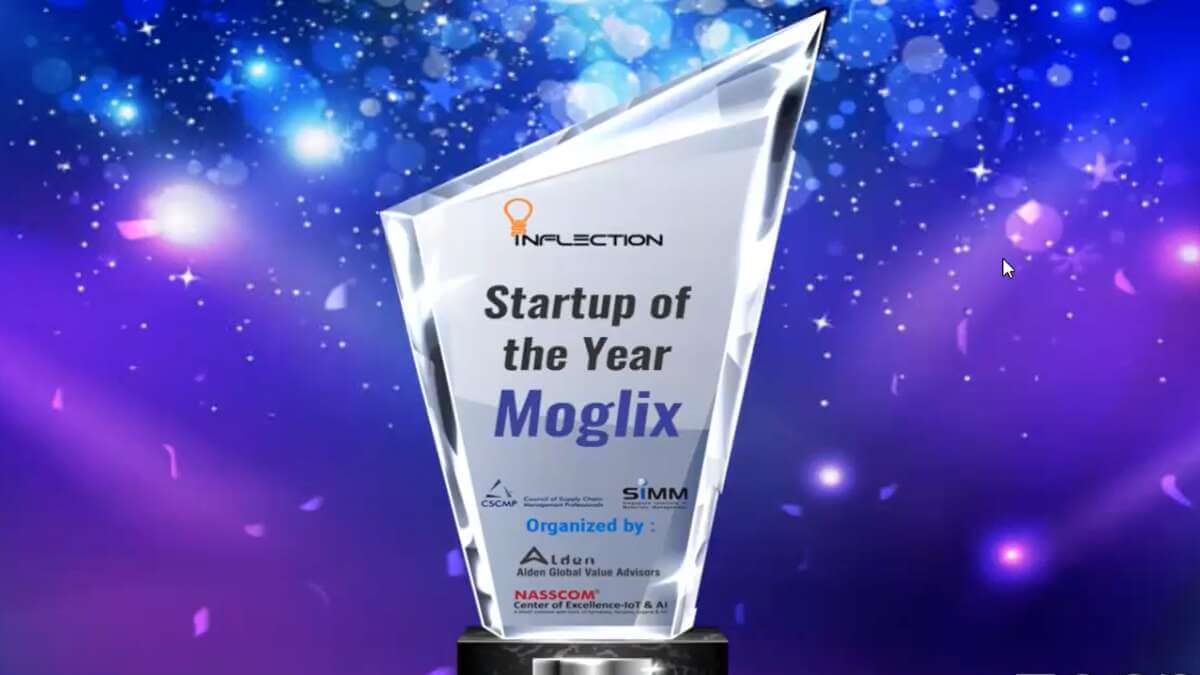
Startup Of The Year Award 2020
We are humbled and delighted to be honored with the Startup of the Year Award at the 22nd Inflection Manufacturing Supply Chain Innovation Web Conference and Awards 2020, co-organized by Alden Global and NASSCOM.
While accepting the award on behalf of team Moglix, Rahul Garg, CEO & Founder, said, “We are working to bring the B2C experience in ecommerce back to the manufacturing sector and we are delighted to continue to work with more than 500+ large organizations in this digitization drive.”
Read More