Supply Chain and Logistics Excellence (SCALEX) conference
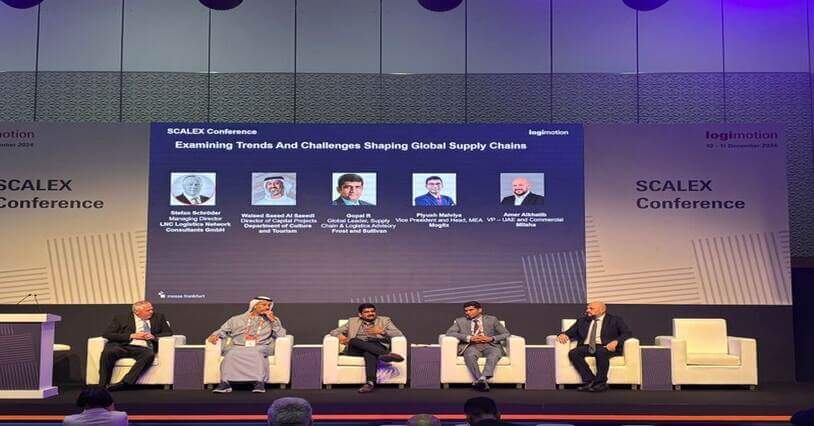
Supply Chain and Logistics Excellence (SCALEX) conference
Date: 10th – 11th December’2024
Organizer: Messe frankfurt
About the Event: Mr. Piyush Malviya, Vice President & Head – MEA at Moglix, recently participated in a session at the Supply Chain and Logistics Excellence (SCALEX) Conference, hosted by Messe Frankfurt Middle East.Titled “Examining Trends and Challenges Shaping Global Supply Chains,” the session highlighted:
✅ Impacts of evolving trade policies.
✅ Adapting to e-commerce and consumer demands.
✅ Driving sustainability and compliance in supply chains.
12th Edition Procurement Excellence Summit and Awards 2024
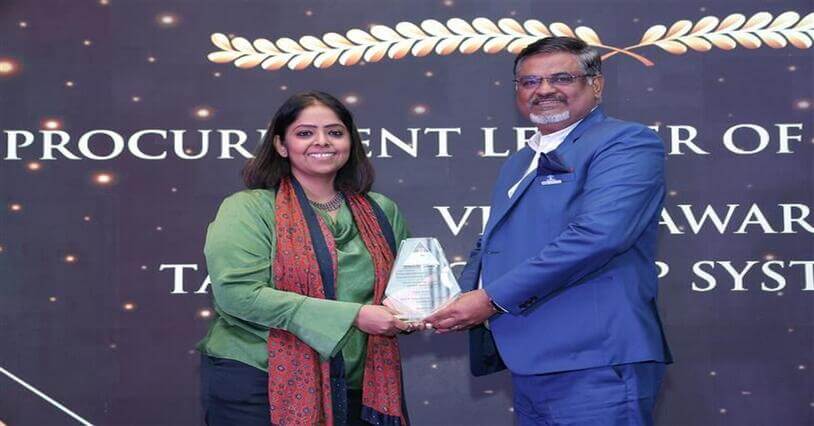
12th Edition Procurement Excellence Summit and Awards 2024
Date: 10th December’2024
Organizer: CII
About the Event: Ms. Jigyasa Kishore (she/her), Vice President at Moglix, recently addressed the 12th Edition Procurement Excellence Summit and Awards 2024, organized by UBS Forums Pvt. Ltd. In the session, ‘Beyond Cost Savings: Measuring Procurement’s Strategic Impact,’ she highlighted how procurement goes beyond cost reduction, emphasizing its role in driving organizational growth through strategic partnerships and innovation. At Moglix, we remain dedicated to transforming procurement into a strategic enabler of measurable business outcomes. We were happy to felicitate awards to industry stalwarts. Congratulations to all winners!
Bharat Mobility Global Expo 2025 (Auto Component)
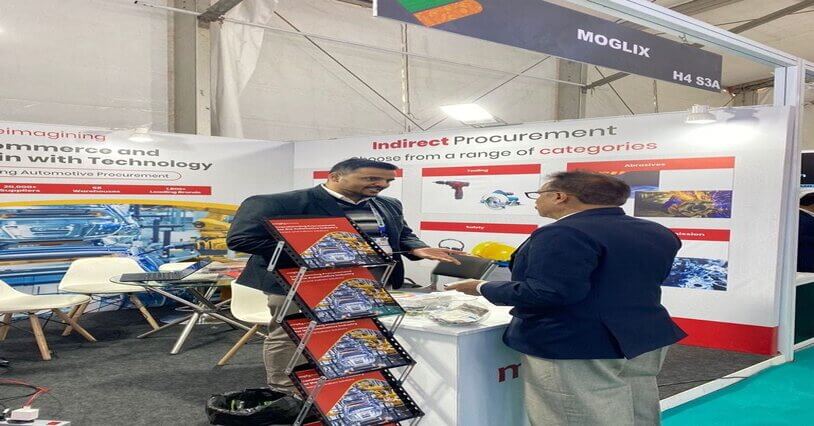
Bharat Mobility Global Expo 2025 (Auto Component)
Date: 18th – 21st January
Organizer: ACMA, CII, SIAM
About the event: Moglix participated in Bharat Mobility: Components Show 2025 at Yashobhoomi, Dwarka. The event provided a platform to engage with industry leaders and discuss transformative strategies for India’s mobility and EV revolution.We showcased how our innovative procurement and supply chain solutions are empowering the automotive ecosystem and driving sustainability.
Redefining global supply chains: India’s strategy to capitalise on emerging opportunities
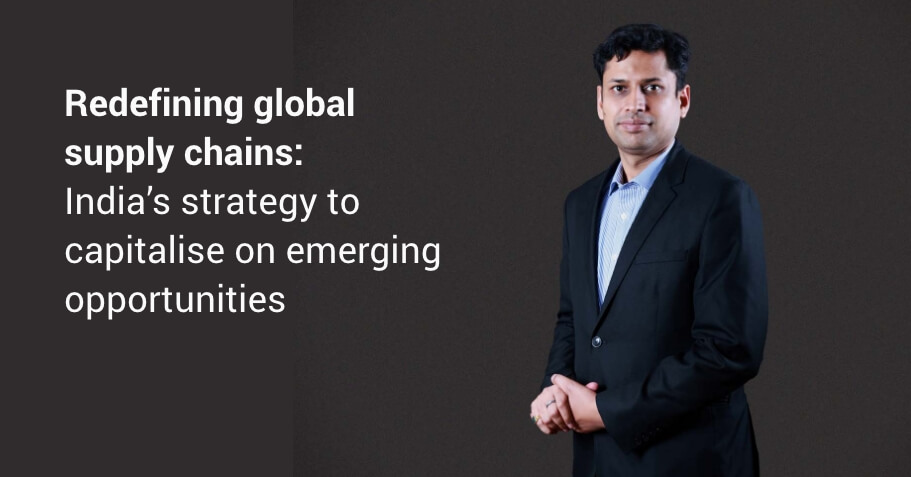
Redefining global supply chains: India’s strategy to capitalise on emerging opportunities
India is witnessing a defining moment in the global supply chain landscape, as shifts driven by geopolitical dynamics, sustainability imperatives, and rapid technological innovation redefine how the world manufactures and moves goods. In a feature for Manufacturing Today, Rahul Garg shares his views on how these global trends are opening up a powerful window of opportunity for India. With its expanding industrial base, skilled workforce, and growing digital infrastructure, India is well-positioned to emerge as a central player in the global supply chain ecosystem—driving resilience, innovation, and long-term competitiveness.
Read MoreDPIIT Partners Moglix To Boost Manufacturing Startups In India
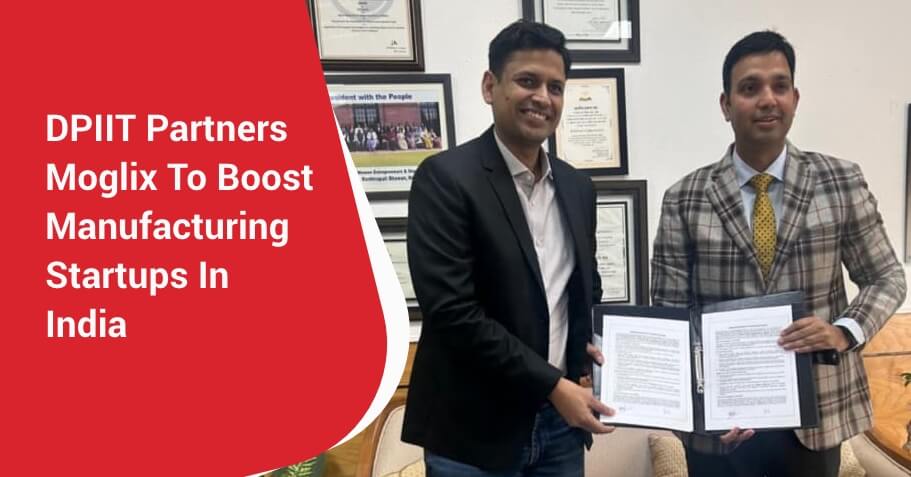
DPIIT Partners Moglix To Boost Manufacturing Startups In India
Moglix partners with the Department for Promotion of Industry and Internal Trade (DPIIT) to empower over 25 growth-stage manufacturing startups across key sectors such as chemicals, automotive, infrastructure, and green energy. Through this collaboration, Moglix aims to enable these startups with access to capital, industry partnerships, and critical resources, helping them innovate and build globally competitive products while contributing to India’s vision of becoming a self-reliant and future-ready manufacturing powerhouse.
Read MoreThe Rise of Autonomous Procurement: Opportunities and Challenges
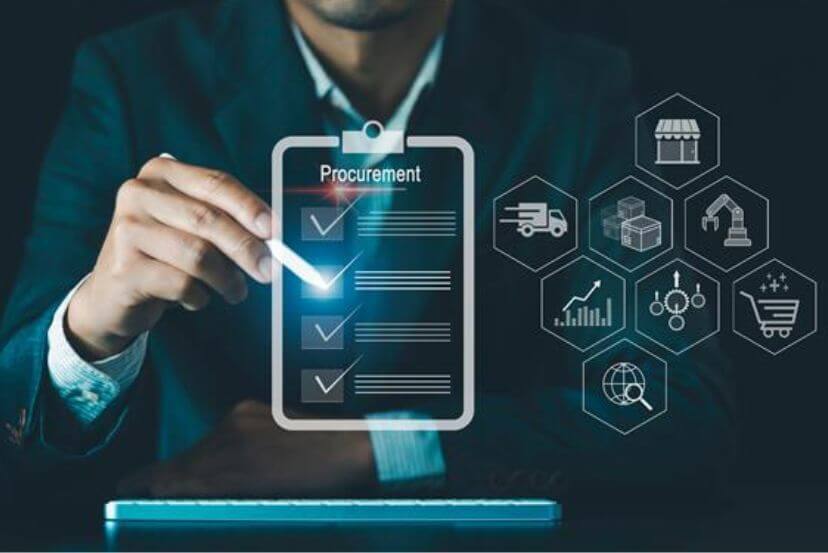
The Rise of Autonomous Procurement: Opportunities and Challenges
Procurement, traditionally a complex and time-consuming process, is facing increasing demands.
According to Hackett Group’s 2023 report, procurement workloads are expected to surge by 10.6%, highlighting the urgent need for greater efficiency.
But what if these challenges and inefficiencies can be solved with minimal human intervention? What if a single software can automate the procurement process?
These questions give rise to autonomous procurement.
Autonomous procurement is a data-driven model that leverages advanced technologies such as Artificial Intelligence (AI), Machine Learning (ML), and Robotic Process Automation (RPA). These technologies help businesses identify and procure the best suppliers, products, or services at reasonable prices.
For instance, Walmart leveraged autonomous procurement to automate the negotiation process, save time and resources, and enhance the overall resilience of its procurement operations.
Autonomous procurement isn’t just a buzzword anymore. It has become an instrumental tool for procurement teams in automating complex and time-consuming processes, managing supply chains, making informed data-driven decisions, and enhancing overall effectiveness.
It’s a breakthrough that promises to streamline and enhance procurement operations, using historical and real-time data such as consumer preferences, market trends, and past purchases.
But is automation the answer to all your procurement challenges?
We’ll explore the emerging trends of autonomous procurement, its benefits, the opportunities it offers, and the challenges that must be overcome to implement its benefits entirely.
So without any further ado, let’s get the ball rolling.
4 Emerging Trends In Autonomous Procurement
Autonomous procurement is gaining traction among companies looking to enhance the efficiency, accuracy, and scalability of their procurement processes. Here are some key trends that are shaping the future of autonomous procurement:
1. Artificial Intelligence (AI)
AI analyzes massive amounts of data, including historical and current purchasing patterns, market trends, and supplier performance. Later leverages its ability to generate smarter purchasing decisions, leading to informed data-driven decisions.
For instance, Unilever, a global leader in consumer goods benefitted from AI in its supply chain, boosting their sales by 15-35%.
2. Predictive Analytics
This tech leverages historical data to predict future and current demands. This forecasting helps businesses to manage their stocks and inventory more effectively. Additionally, it helps to anticipate market fluctuations in advance and avoid situations like stock-out or over-stock.
Starbucks leverages this approach for demand forecasting to optimize store locations. By analyzing several variables like demographic data and foot traffic patterns, Starbucks identify the most suitable location for installing new stores. This helps expand their stores and potentially increase their success.
3. Robotic Process Automation (RPA)
This trend enables businesses to automate repetitive tasks in procurement such as order processing, invoice management, and reduction of human errors.
For example, Siemens- a global industrial manufacturing company implemented RPA to automate its procurement process, leading to a 20% cost reduction in procurement cycle time and a significant reduction in manual errors.
4. Blockchain
Blockchain technology is an emerging trend that brings transparency and traceability to the supply chain. It offers a decentralized ledger that enables secure and fair transactions without the need for intermediaries such as banks. It also helps to verify the authenticity of products/services, track deliveries, and ensure compliance with sustainable and ethical sourcing practices.
Nestle, one of the world’s biggest food and beverage giants leverages blockchain in its procurement process. Since 2017, the company has been utilizing this trend to track the origin of its cocoa beans and achieve end-to-end traceability of its food items.
Benefits Of Autonomous Procurement
The main objective of autonomous procurement is to analyze past experiences, real-time data, and market trends for accurate decision-making in the supply chain systems. By leveraging that information and insights businesses can get the following benefits:
1. Streamline Supplier Selection
Choosing the right suppliers is often time-consuming and error-prone. With AI-driven tools, businesses can automate the process by analyzing bidders’ past performance and contracts, leading to faster, more accurate supplier onboarding. Companies using AI in procurement are 90% more likely to find the right suppliers, according to McKinsey & Company Reports.
2. Analyzes Massive Data
Previously, procurement professionals used to rely on networking and online research to gather supplier information. This massive data was reflected in informed decision-making, leading to the demand for data cleaning. Now, with the integration of our data cleaning solutions, companies can save up to 6% in TCO (Total Cost of Ownership), 95% in OTIF (On-Time, In Full) delivery, 15% reduction in lead times, and 20% reduction in PR-PO (Purchase Requisition, Purchase Order) Cycle Time.
3. Increases Productivity and Efficiency
A new study by Hackett Group quantifies that AI can increase employee productivity by 44%. Implementing AI in procurement can automate the system, cut down cycle times, and reduce the chances of errors. This approach enables teams to handle complex procurement tasks precisely and accurately. Additionally, by leveraging AI in procurement, businesses can potentially speed up all the processes efficiently, freeing up teams for strategic activities.
4. Saves Cost
According to a Deloitte study, companies using AI in procurement can reduce their costs by almost 40%. By implementing AI, businesses can minimize errors in data entry & billing processes and optimize supplier selection to ensure more profitable deals. This approach can cut down on unnecessary expenses and increase profitability.
Opportunities in Autonomous Procurement
Autonomous procurement is continuously evolving, opening doors to strategic approaches that drive long-term business success. These strategic approaches include supplier relationship management, better collaboration and innovation, optimized inventory management, and improved supplier negotiations.
By integrating AI in procurement, teams can automate routine tasks and redirect their focus on priority activities that demand attention, including:
1. Focus on strategic supplier relationships.
2. Drive innovation through supplier collaboration
3. Enhancing supply chain flexibility
4. Supporting sustainability
5. Prioritize Corporate Social Responsibility (CSR) Initiatives
6. Derive informed data-driven decisions.
In short, autonomous procurement has the potential to enhance supply chain visibility and transparency by leveraging trends and technologies.
Challenges Faced in Autonomous Procurement Implementation
As we discussed the benefits and opportunities of automating procurement, it would be unfair to tell you about the challenges that come along with it.
The procurement industry often operates traditionally and implementing technology in it is a big change. With the growing potential of AI capabilities, many companies have already adopted autonomous procurement but still hesitate to some degree of insecurity.
Let’s discuss the challenges faced by procurement teams while implementing technologies in procurement and ways to overcome them.
1. Output Accuracy
The procurement processes heavily rely on precise data and a single inaccuracy can impact the entire process. AI can gather past and real-time data of suppliers, but even a tiny mistake can lead to poor purchasing decisions, supplier disputes, financial losses, or severe situations. Decisions based on this data directly affect business-supplier relationships.
Here’s how we can overcome the challenge
It’s important to note that AI is a technology without human emotions. Relying solely on AI decisions might result in huge mistakes. Therefore, procurement teams should incorporate AI into their systems, but under human supervision, the final decision should be made.
2. Privacy Concerns
AI constantly crawls external sources and internal data to collect as much information as possible as part of its machine-learning capabilities. Lack of belief in AI privacy and security systems is a major concern and challenge for procurement experts.
The only way to address this challenge and overcome the fear of AI privacy and security breaches is through constant monitoring of AI functioning. Companies can implement cybersecurity measures like encryption and biometrics to avoid attackers. Developers are also trying to build robust systems that can be trusted without fear.
3. Adoption By Workforce
Employees accustomed to traditional procurement methods may struggle to adapt to technology, and automation may generate fear of redundant roles in employees.
Furthermore, training all the employees and making them comfortable with the new technology is a big challenge and will require considerable time and resources. For the long-term success and effectiveness of the implementation of autonomous procurement, it is critical to ensure that every employee fully understands, learns, and adopts the technology.
Conclusion
The rise of autonomous procurement is significantly transforming the way businesses operate while presenting both opportunities and challenges. As companies navigate these challenges and benefits, the key to successful implementation of technologies lies in balancing technology with human intervention.
With AI promising enhanced efficiency and innovation, careful planning and strategic implementation are also crucial. Companies that strategically implement and leverage autonomous procurement are well-positioned for future success.
Ready to automate your procurement processes?
Explore how at Moglix our team can help you implement autonomous procurement strategies that align with your business objectives and drive efficiency and innovation.
Leveraging AI and Machine Learning for Predictive Procurement Analytics
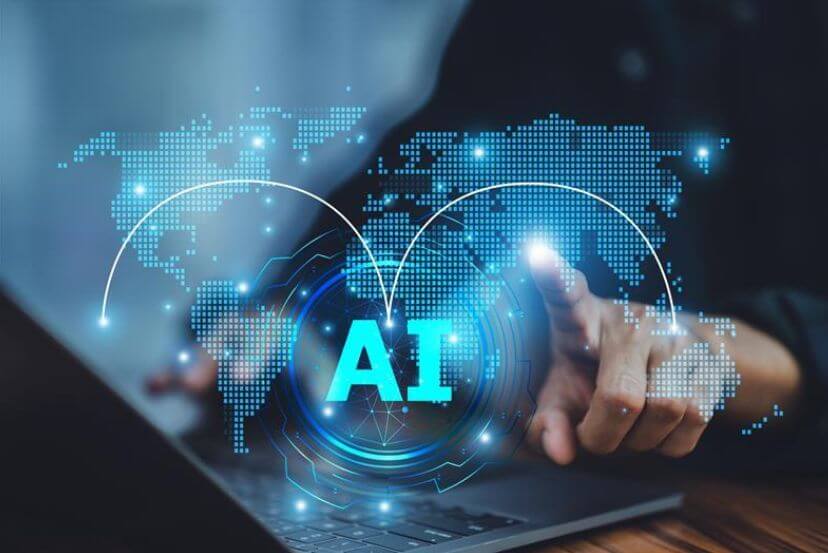
Leveraging AI and Machine Learning for Predictive Procurement Analytics
Imagine being able to predict supply chain disruptions, optimize sourcing strategies, and generate data-driven decisions with pinpoint accuracy– all in one go.
Wouldn’t that be transformative for your business?
Yes, this transformation is not just possible– it’s happening now with the power of Artificial Intelligence (AI) and Machine Learning (ML) technologies.
AI and ML have been revolutionizing industries for decades. Still, these technologies always succeeded in bringing something new and innovative to the table. Their ability to automate complex tasks, enhance decision-making, and drive efficiency makes what was once impossible, possible.
As AI gains traction in multiple aspects of businesses, the procurement process is no exception. It’s undergoing a transformational shift with AI and ML at the forefront. Businesses can use these technologies to optimize procurement operations, generate deeper insights, automate mundane tasks, and make smarter, data-driven decisions.
In this blog, we’ll delve into the transformative potential of AI and Machine Learning in the procurement process. We’ll also explore practical examples and provide actionable insights to help your business stay ahead of the competition.
Current State in Procurement
The procurement process is responsible for keeping the wheels of business operations running. This process facilitates prompt and budget-friendly acquisition of goods and services.
In almost every business, procurement teams encounter challenges like inefficient inventory management and supply chain disruptions. Solving these issues in the context of evolving consumer demands remains a difficult task.
Traditional manual prediction methods are time-consuming, often inaccurate, and prone to errors. However, by integrating AI, procurement teams can overcome these issues and turn challenges into opportunities.
AI in Procurement
AI is a rapidly evolving concept for procurement. By leveraging AI in procurement, teams can optimize their supply chain to maximize efficiency, solve powerful algorithms to make smarter purchasing decisions, and predict future demands.
We at Moglix, have already integrated AI to streamline our procurement processes, resulting in significant cost savings and improved operational efficiency.
From supplier credentials, performance metrics, historical insights, and market trends to purchasing data and other complex datasets, AI-powered predictive analytics and ML can study, analyze, interpret, and draw meaningful conclusions from vast data.
By applying ML, predictive analytics, and real-time pattern recognition to procurement processes, AI can develop patterns and predict future demands. Additionally, these models continuously learn from the incoming data, refining their predictions, optimizing inventory management, and empowering teams to make more informed decisions.
Benefits of AI & ML in Predictive Procurement Analytics
Here are some key benefits of AI and ML in procurement using historical data to derive predictive procurement analytics:
1. Predictive Insights
AI leverages historical data and market trends to predict future demands, pricing changes, and supplier performance.
As per McKinsey research, companies using AI-driven predictive analytics for demand forecasting can reduce forecasting errors by 20-50%. This reduction can lead to significant cost savings.
This benefit helps procurement teams plan ahead and make proactive decisions instead of reacting to issues when they arise. Procurement teams can now focus on implementing solutions rather than worrying about future disruptions. This allows them to ensure efficient supply chain management.
2. Enhancing decision-making
Procurement teams can gain actionable insights using AI’s ability to study complex datasets and analyze comprehensive information.
These technologies can process massive quantities of information within seconds, providing insights that would take days for humans to uncover. Whether it’s choosing suppliers, negotiating contracts, or planning procurement strategy, AI-driven decision-making tools enable better supplier relation management and more informed choices. For instance,
At Moglix, our AI-powered procurement platform has enabled businesses to reduce their procurement cycle times by up to 50% and upto 40% savings and reduction in inventory.
3. Optimizing Sourcing Strategies
AI analyzes factors, such as pricing, quality, quantity, delivery times, reliability, and risks to optimize sourcing strategies. It can also interpret supplier performance data, market trends, and other relevant information to select the most suitable sourcing options.
For example, AI can identify suppliers that consistently deliver high-quality goods on time, which helps businesses maintain high standards while reducing costs. These insights help businesses build stronger supplier relationships and maintain a competitive edge in their sourcing strategies.
4. Risk Mitigation
AI can detect potential risks, such as suppliers’ financial instability, geopolitical concerns, supply chain disruptions, and fluctuating market conditions, often before they happen.
According to a Deloitte report, companies using AI for risk management can detect potential threats up to 90% faster than those relying on traditional methods.
By continuous analysis and monitoring data, AI can provide early warnings and suggest preventive measures. Procurement professionals can use these insights to avoid or minimize the impact of risks, ensuring continuity in the supply chain and saving time and resources.
5. Improved Efficiency
ML and AI technologies are advanced tools that ensure a smooth and efficient procurement process. These tools can automate routine tasks such as invoice processing, contract management, and shipment tracking.
This automation enables procurement teams to save time, reduce the chances of human error, and focus on more strategic activities. Additionally, it improves efficiency and ensures smart and accurate procurement operations.
6. Augmented Expertise
AI can’t replace humans but enhances their capabilities. By acting as a digital consultant, AI equips procurement teams with advanced tools, insights, and recommendations in an easily understandable format.
These tools can analyze complicated data and provide data-driven insights, enabling teams to tackle challenges and drive better business results. This augmented expertise is particularly valuable in complex procurement environments where quick, informed decisions are critical.
Ways Businesses Can use AI & ML to Stay relevant in the Competition
Let’s look at ways businesses can use AI and ML to transform their procurement process and stay ahead of the curve.
1. Supplier Management
Companies can use ML to evaluate their suppliers. AI can rank these suppliers based on delivery times, quality, and pricing, enabling businesses to negotiate better deals and optimize their supplier base.
For example, a leading automotive company used AI-driven supplier management to reduce procurement costs by 20% within a year.
2. Demand Forecasting
Businesses can use these technologies to predict which products are in high demand based on historical sales data. This will help procurement teams manage their inventory better and avoid stockouts during peak times. This demand forecasting can help businesses generate huge revenue.
3. Cost Analysis
AI can analyze business spending data and identify opportunities to consolidate purchases with selected suppliers, leading to significant cost savings.
For instance, a Fortune 500 company, using AI-driven cost analysis, reduced its procurement spend by 15% by identifying overlapping supplier contracts.
4. Fraud Detection
The AI system can analyze procurement transactions in real-time, detecting unusual patterns or activities that may indicate fraud. By flagging suspicious activities early, AI helps protect businesses from financial loss and reputational damage.
A global manufacturing firm saved over $5 million annually by implementing AI-based fraud detection in its procurement process.
5. Market Intelligence
ML and AI tools can scan massive amounts of data, such as news articles, financial reports, and market fluctuation insights, from the Internet. Later, these gathered data will be analyzed to equip procurement teams with real-time marketing intelligence. Teams can utilize this intelligence to derive better results and stay ahead of their competitors.
6. Predictive Maintenance
Businesses can use AI and ML tools to predict potential machinery failures or equipment issues before they occur. These tools analyze machinery usage patterns and historical data, enabling the procurement team to order new parts quickly. This predictive maintenance approach reduces downtime and ensures a smooth production process.
Rolls-Royce implemented AI-driven predictive maintenance and saw a 25% reduction in impromptu downtime and a 10% surge in engine life.
Conclusion
Integrating ML and AI in the procurement process is an enhancement and a transformation. By utilizing these technologies, businesses can empower their procurement teams, optimize operations, and gain a competitive edge.
With the ever-evolving business environment, businesses that embrace AI and ML in their procurement processes will be better positioned. Now is the right time to leverage AI and ML’s potential and advance your procurement strategy.
For more insights, check out our case studies.
Pipe Replacement Analysis Guide for Procurement Managers
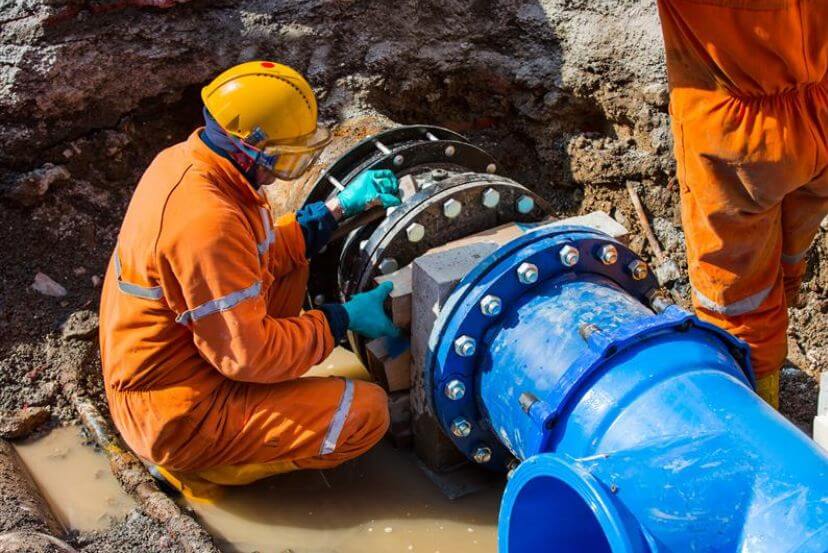
Pipe Replacement Analysis Guide for Procurement Managers
When Should Procurement Managers Procure Pipes?
Procurement managers in industries like oil & gas, irrigation, and energy frequently encounter a pivotal choice: replacing existing pipes or procuring new ones. This decision requires careful analysis of performance metrics, industry needs, and cost implications.
This decision hinges on understanding performance metrics, industry requirements, and cost-effectiveness. The first step is identifying the right time to act. Pipes need replacement or procurement in the following scenarios:
- Existing infrastructure shows signs of reduced performance.
- Task requirements evolve due to industry advancements or regulatory changes.
- The technology used in current pipes becomes obsolete.
Purchasing New Pipes
When procuring new pipes, procurement managers should collaborate closely with planning engineers and reference the Bill of Quantities (BoQ) to align with project requirements. Key considerations include:
- Brand and Specifications: Choose pipes that adhere to specific ASTM codes or international standards.
- Material Types:
- Metallic Pipes: Ferrous (e.g., steel) or non-ferrous (e.g., copper, aluminum).
- Non-Metallic Pipes: PVC, HDPE, or composite materials.
Matching these specifications ensures the pipes meet the demands of EPC infrastructure projects and industrial applications.
Deciding to Replace Existing Pipes
Replacing pipes is necessary when performance and efficiency no longer meet operational requirements. Factors to evaluate include:
- Reduced Performance: Diminished flow rate, leaks, or corrosion.
- Altered Task Requirements: Changes in pressure handling, temperature resistance, or flow capacity.
- Obsolescence of Technology: Older pipes may not support modern operational needs or compliance requirements.
Procurement managers must rely on metrics like the Equivalent Uniform Annual Worth (EUAW) to decide whether to replace or retain a pipe.
Understanding the EUAW Curve Over Time
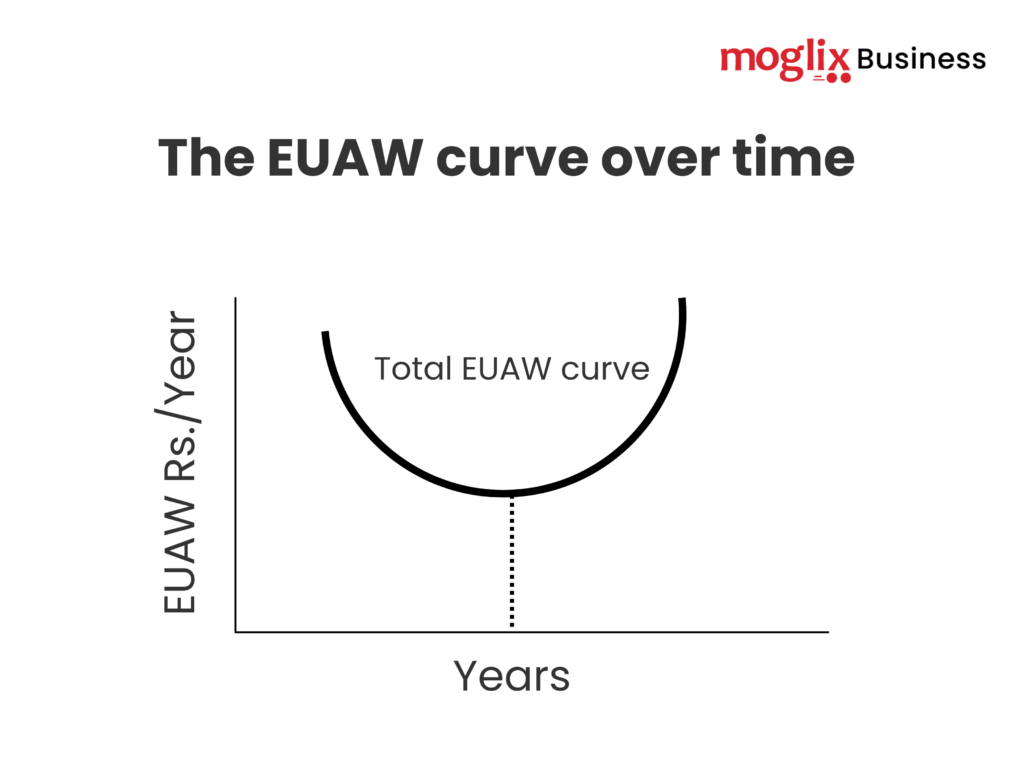
The Equivalent Uniform Annual Worth (EUAW) metric evaluates a pipeline’s economic value throughout its lifecycle, assisting managers in balancing operational reliability and cost efficiency.
- Initial Ownership Costs: Decrease over time as initial investments depreciate.
- Annual Operations and Maintenance (O&M) Costs: Increase with aging infrastructure due to repairs and inefficiencies.
- Salvage Value: Declines as the pipe reaches the end of its usable life.
Analyzing the EUAW curve empowers managers to make data-driven decisions, optimizing cost efficiency while maintaining operational dependability.
Case Study: Evaluating Pipe Replacement
Problem Statement:
A pipeline in an energy project has been in service for three years, with an EUAW of Rs. 5,210 per year and a remaining life of five years. A replacement option has the following parameters:
- First Cost: Rs. 25,000
- Salvage Value: Rs. 3,800
- Life Span: 12 years
- Annual Operating Cost: Rs. 720
Analysis:
Using a 10% Minimum Attractive Rate of Return (MARR), calculate the EUAW for the existing and replacement pipes:
- EUAW of Existing Pipe (EUAWD): Rs. 5,210
- EUAW of New Pipe (EUAWC):
- Rs. 25,000(A/P, 10%, 12) + Rs. 720 – Rs. 3,800(A/F, 10%, 12)
- Result: EUAWC = Rs. 4,211
Decision:
Since the EUAW of the replacement (Rs. 4,211) is lower than the current pipe’s EUAW (Rs. 5,210), the new pipe should be purchased.
Procure New Pipes for your Next Pipe Replacement Project
Strategic pipe procurement is a vital responsibility for procurement managers in industries like oil & gas, manufacturing, and water management. Informed decisions drive efficiency and sustainability.
Decisions should be driven by technical specifications, cost analyses like EUAW, and long-term performance needs.
Moglix provides a comprehensive selection of metallic (ferrous and non-ferrous) and non-metallic pipes to cater to varied industrial needs.
With competitive pricing, pan-India delivery, expert project management, and supply chain financing, we serve sectors like oil & gas, energy, automotive, irrigation, and construction.
Partner with Moglix to ensure optimal procurement solutions for your next project.
7 Pipe Procurement Tips for Procurement Managers for Urban Construction Projects
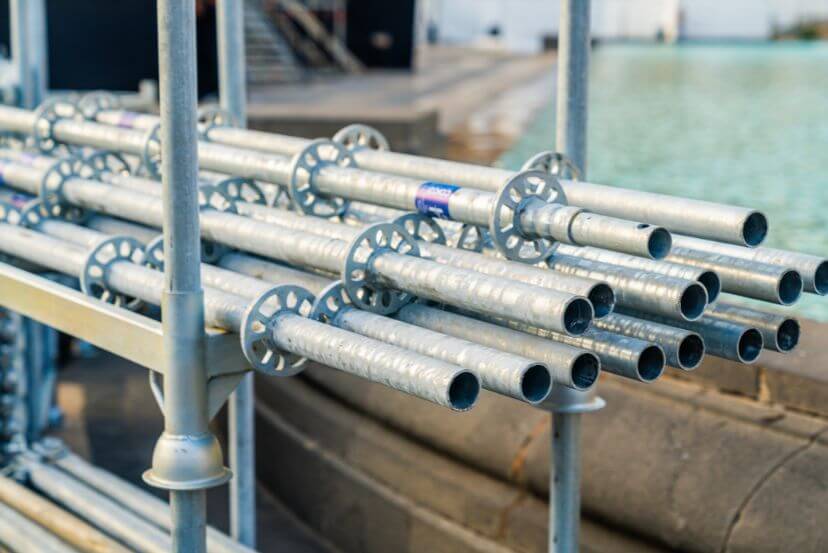
7 Pipe Procurement Tips for Procurement Managers for Urban Construction Projects
Pipe procurement is a cornerstone of urban construction, demanding precision, efficiency, and sustainability.
From drainage systems to essential infrastructures like EPC projects, oil & gas facilities, drinking water pipelines, and manufacturing plants, selecting the right pipes can profoundly impact cost-efficiency, durability, and operational success.
For procurement managers, making informed decisions about pipes is essential to ensure the foundation of robust and sustainable infrastructure.
This blog outlines seven practical and effective tips that procurement managers must consider for streamlining their pipe procurement process and delivering long-lasting results for urban construction projects. Let’s get started.
Use Drainage Systems With 3 Layer Technology
Drainage systems featuring 3-layer technology offer versatility and can be installed both above and below ground.
These systems feature a smooth inner surface for optimal water flow and are easy to install, making them ideal for locations such as restaurants, hospitals, office buildings, and laboratories.
Made from durable materials and reinforced with external ribs for extra strength, these pipes offer the toughness of metal.
Their ability to resist hot water and chemicals makes them a dependable choice for long-term use in various urban construction projects.
Avoid Low-Density, High Noise PP Drainage Systems
Low-density polypropylene (PP) pipes might seem cost-effective initially, but they often compromise performance. These systems tend to produce high noise levels, which can be disruptive in residential and commercial areas.
Urban areas demand silent and efficient drainage systems, especially in EPC infrastructure projects where noise disruptions can affect nearby communities.
Opt for high-density and low-noise PP drainage systems that provide both durability and noise reduction.
Use Lightweight uPVC Drainpipe System
Unplasticized Polyvinyl Chloride (uPVC) pipes are a top choice for urban drainage projects. These pipes are lightweight which makes them easy to transport and install, thereby reducing labor and logistics costs.
uPVC pipes are also resistant to chemicals, corrosion, and weather elements, making them suitable for applications in oil & gas facilities, drinking water systems, and irrigation networks. Their lightweight nature does not compromise their durability, ensuring long-term performance.
Create Drainage Systems for Rainwater Management
Urban construction projects often face challenges with rainwater management.
Rainwater management is especially crucial for EPC infrastructure and energy projects, where water management can directly impact operational safety and efficiency.
Integrating drainage systems specifically designed to collect rainwater can mitigate flooding and waterlogging issues.
Corrosion-resistant, UV-stabilized pipes with high flow capacity and sturdy construction ensure durability and reliable performance, even in extreme weather.
Utilize Advanced Sub-Surface Dewatering System
Advanced sub-surface dewatering pipes are designed to prevent clogging and provide excellent waterproofing, making them a reliable choice for extending the life of buildings.
Their ease of installation adds to their appeal, saving time and effort during projects.
Procurement managers should opt for pipes with superior permeability and clog resistance to maximize system efficiency.
These pipes are commonly used for creating drainage foundations, fixing leaking basements, and supporting agriculture and gardening needs.
Their versatility makes them an essential solution for managing groundwater efficiently.
This tip is especially vital for projects involving manufacturing plants and large-scale EPC infrastructure.
Use Double Walled Corrugated Underground Drainage Systems
Double-walled corrugated pipes are a robust solution for underground drainage. These pipes offer superior strength, flexibility, and load-bearing capacity, making them ideal for urban settings with heavy vehicular traffic.
These systems stand out as they require minimal maintenance compared to traditional drainage solutions. Their inner smooth layer ensures high flow efficiency, while the corrugated outer layer provides structural integrity.
These features make them a preferred choice for procurement managers involved in oil & gas, irrigation, and energy projects.
Integrate PVC Underground Drainage Systems
PVC pipes are a lightweight, versatile, and cost-effective solution, they are an affordable option for underground drainage systems in urban construction.
They are highly durable, resistant to chemical erosion, and offer high water flow capacity.
PVC pipes are commonly used in a variety of applications, including hospitals, townships, resorts, commercial complexes, and industries.
Easy to install and requiring minimal maintenance, PVC pipes are an excellent choice for procurement managers aiming to balance performance and cost in urban construction.
Procure Pipes for Your Next Urban Construction Project
Choosing the right pipes is both a technical and strategic decision. Procurement managers must balance cost-efficiency, durability, and environmental sustainability while meeting the specific demands of urban construction projects.
The tips outlined in this blog offer procurement managers actionable strategies to optimize their decision-making process. With the right pipe systems in place, urban construction projects can achieve both operational excellence and long-lasting results. By implementing these considerations, procurement managers can significantly contribute to resilient, sustainable, and cost-effective urban infrastructure.
How Procurement Managers Can Negotiate Better Prices for Ferrous Pipes?
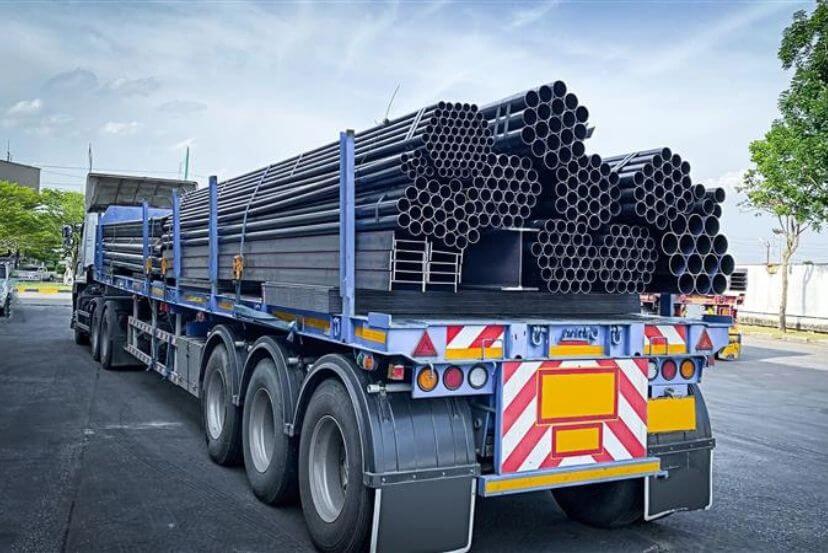
How Procurement Managers Can Negotiate Better Prices for Ferrous Pipes?
Procurement managers play a crucial role in securing quality materials at the best possible prices. Negotiating for ferrous pipes, particularly GI (Galvanized Iron) pipes, requires a balance of knowledge, preparation, and strategy.
This blog outlines actionable strategies to help procurement managers negotiate effectively for ferrous pipes, ensuring an optimal balance of cost efficiency and quality.
1. Research Market Trends and Pricing
Staying informed about market trends and price fluctuations is critical for successful negotiations. Keep track of raw material costs, industry demand, and supplier competition.
- Why it matters: Suppliers often set prices based on market dynamics. Having up-to-date information gives you an upper hand in negotiations.
- How to research: Utilize industry reports, network with procurement peers, and employ digital tools to monitor ferrous material pricing trends.
Tip: Always compare prices from multiple suppliers to establish a baseline before initiating talks.
2. Build Long-term Supplier Relationships
Establishing trust and rapport with suppliers can lead to better deals over time. Suppliers often provide better discounts and terms to loyal and trusted customers.
- Key actions: Communicate regularly with suppliers and make timely payments.
- Value of partnerships: Strong relationships can help you secure exclusive offers or priority delivery during high-demand periods.
Tip: Aim for mutually beneficial arrangements that strengthen supplier relationships.
3. Bulk Purchases and Volume Discounts
Procuring in bulk can significantly lower per-unit costs, making it a key strategy for effective negotiations.
- Plan ahead: Forecast your organization’s pipe requirements and place larger orders when feasible.
- Leverage economies of scale: Suppliers prefer larger contracts as they provide stability, making them more willing to offer discounts.
Tip: If storage is a concern, explore staggered delivery options to manage inventory without compromising on discounts.
4. Evaluate Quality Standards
Quality often drives pricing in the ferrous pipes market. Make sure to specify your quality requirements upfront.
- Why it matters: Suppliers might charge extra for superior coatings, higher tensile strength, or corrosion resistance.
- Actionable approach: Ensure the supplier meets industry standards (e.g., IS or ASTM specifications). Compare the cost-benefit ratio of premium pipes versus standard ones.
Tip: Request quality certifications and conduct thorough inspections of samples before finalizing an order.
5. Negotiate Beyond Price
Price isn’t the only factor that can optimize costs. Expand negotiations beyond price to include aspects like:
- Payment terms (e.g., extended credit periods).
- Free or discounted shipping.
- Additional services like customized sizes or pre-cut lengths.
Tip: Prioritize the overall value proposition rather than solely focusing on the price.
6. Time Your Purchases Strategically
The timing of your purchase can significantly impact pricing.
- Optimal timing: Suppliers often offer discounts during off-peak seasons or at the end of a financial quarter/year.
- Market observation: Monitor when raw material costs dip or when suppliers run promotional offers.
Tip: Be proactive and place orders before high-demand periods, such as infrastructure project launches or peak construction seasons.
7. Prepare for Negotiations
Effective negotiation requires thorough preparation. Engage suppliers confidently, backed by data and a well-defined strategy.
- Preparation checklist:
- Define your budget and acceptable price range.
- Highlight your potential as a repeat customer.
- Present alternative quotes to validate your position.
Tip: Adopt a professional tone and remain open to compromise when necessary to secure long-term benefits.
Negotiate Best Prices for Your Next Ferrous Pipes Purchase
Effective negotiation for ferrous pipes involves balancing cost savings with quality and fostering strong supplier relationships. By researching the market, building partnerships, and employing strategic negotiation techniques, procurement managers can achieve optimal outcomes.
Ready to enhance your procurement process? Discover our extensive selection of high-quality GI pipes and request competitive quotes today.