Sheet Metal Fabrication: Why Material Selection Matters for Manufacturers & Procurement Professionals
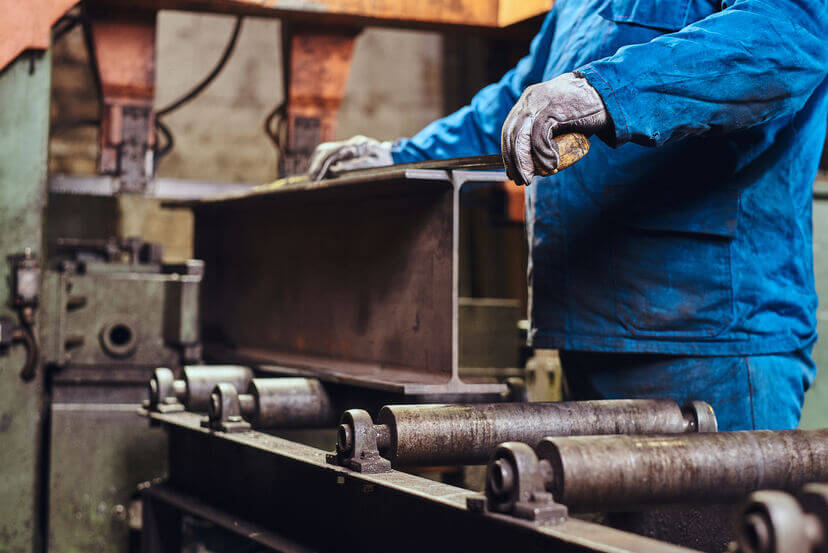
In the realm of sheet metal fabrication, material selection is a pivotal factor influencing the quality, performance, and cost-effectiveness of the final product. Choosing the appropriate material ensures that the fabricated component meets industry standards and functions optimally in its intended application. In sectors such as infrastructure, public sector undertakings (PSUs), automotive, and aerospace, the right material choice can define the success of a project.
This article delves into the significance of material selection, exploring key considerations, common materials, and industry best practices to ensure efficiency and durability in sheet metal fabrication.
The Importance of Material Selection
Material selection is integral to the fabrication process, impacting various aspects such as manufacturability, durability, and overall performance. Here’s why it matters:
- Compliance with Industry Standards: Various industries follow strict regulatory standards for materials used in fabrication. For instance, the automotive sector adheres to ISO/TS 16949, while the aerospace sector follows AS9100 standards. The wrong material selection can lead to compliance issues, product failures, and financial losses.
- Structural Integrity: The selected material must possess mechanical properties like tensile strength, hardness, and impact resistance to ensure the component withstands operational stresses over time. Industries such as construction, railways, and defense require materials that can endure harsh conditions without compromising integrity.
- Manufacturing Efficiency: Different materials respond differently to fabrication processes such as cutting, bending, welding, and forming. A material that is easier to process contributes to efficient production workflows, reducing lead times and minimizing material waste.
- Cost Management: Balancing performance with cost-effectiveness is critical. While high-performance materials like stainless steel offer superior benefits, they may not be feasible for budget-sensitive projects. Smart material selection allows manufacturers to optimize costs without compromising quality.
- Environmental Resistance: Industries such as marine, aerospace, and infrastructure require materials with high x to withstand environmental exposure. The right choice ensures longevity, reducing maintenance costs and preventing premature failure.
Factors Influencing Material Selection
Selecting materials for sheet metal fabrication involves evaluating multiple parameters:
- Mechanical Properties
Understanding a material’s tensile strength, hardness, ductility, and impact resistance is crucial to ensuring it meets the performance demands of the application.
- Formability & Ductility
A material’s ability to be bent, stretched, or formed without breaking determines its suitability for complex shapes and intricate designs. Industries like automotive and consumer electronics rely heavily on materials that offer excellent formability.
- Weldability
Many fabrication projects require welding for assembly and reinforcement. Materials must be compatible with welding techniques like TIG, MIG, or resistance welding to ensure strong, defect-free joints.
- Surface Finish Requirements
For industries where aesthetics matter, such as architecture, interior design, and appliances, materials must be capable of achieving desired surface finishes like polishing, anodizing, or powder coating.
- Environmental & Chemical Resistance
Projects in chemical plants, oil & gas, and marine industries demand materials that can resist corrosion, oxidation, and chemical exposure to enhance longevity and performance.
Common Materials in Sheet Metal Fabrication
Several materials are commonly used in sheet metal fabrication, each offering unique properties suitable for various applications:
Carbon Steel
- Strength & Durability: Ideal for structural applications.
- Cost-Effective: More affordable compared to stainless steel.
- Requires Coatings: Susceptible to rust if left untreated.
- Used In: Construction, heavy machinery, automotive.
Stainless Steel
- Corrosion & Heat Resistance: Ideal for harsh environments.
- Hygienic: Used in food processing and medical applications.
- High Strength: Withstands mechanical stress.
- Used In: Food industry, aerospace, medical equipment.
Aluminum
- Lightweight & Corrosion-Resistant: Perfect for weight-sensitive applications.
- High Conductivity: Used in electronics and heat exchangers.
- Excellent Formability: Easily shaped into complex designs.
- Used In: Aerospace, automotive, consumer electronics.
Copper
- Superior Electrical & Thermal Conductivity: Essential for electrical applications.
- Antimicrobial: Suitable for hospitals and public spaces.
- High Malleability: Allows intricate designs.
- Used In: Electrical components, HVAC, medical applications.
Brass
- Corrosion-Resistant & Aesthetic Appeal: Common in decorative applications.
- Good Machinability: Allows precise detailing.
- Used In: Plumbing, musical instruments, hardware fittings.
Industry Best Practices for Material Selection
1. Project-Specific Selection
Different industries have unique material requirements. Conducting a thorough analysis of project needs ensures that materials align with performance expectations.
2. Supplier Collaboration
Engaging with reliable material suppliers helps in sourcing high-quality materials with consistent properties and certified compliance.
3. Material Testing & Prototyping
Before full-scale fabrication, materials should undergo testing for mechanical performance, formability, and resistance to environmental stressors.
4. Sustainability Considerations
With industries shifting toward eco-friendly practices, selecting recyclable materials like aluminum and stainless steel contributes to sustainable manufacturing.
Case Study: Moglix Business’s Approach to Custom Fabrication
Moglix Business demonstrates the importance of material selection in custom fabrication. Their end-to-end fabrication solutions encompass:
- Material sourcing aligned with project specifications.
- Design engineering with a focus on cost-effective, durable materials.
- Onsite fabrication & assembly backed by robust quality assurance.
Moglix Business has contributed to infrastructure projects of national importance, such as India’s first bullet train corridor, showcasing expertise in strategic material selection to enhance project success.
Conclusion
Material selection is a cornerstone of successful sheet metal fabrication, influencing performance, durability, and cost-effectiveness. By carefully considering factors like mechanical properties, manufacturability, and environmental resistance, manufacturers can ensure optimal results for their applications.
Contact Moglix Business for Your Custom Fabrication Needs
Looking for a custom fabrication partner that prioritizes material selection and quality assurance?
📩 Email: info@moglixbusiness.com
Discover how Moglix Business can enhance your fabrication projects with industry-leading expertise!