40 key Industrial Valve terms that you should know
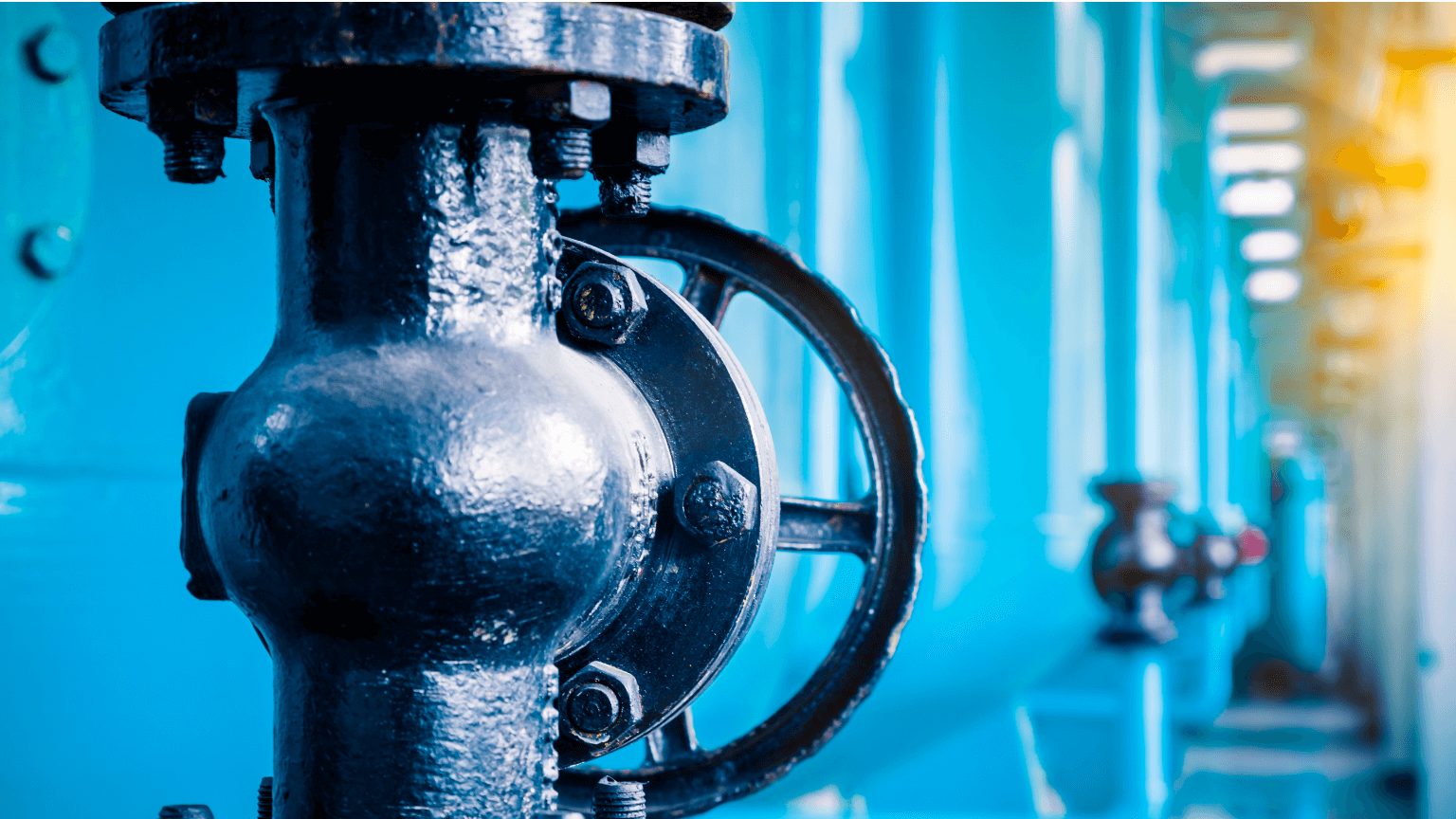
Industrial valves are essential components in controlling the flow of fluids within various industries. Understanding the terminology associated with industrial valves is crucial for effectively communicating, selecting, and operating these vital devices. In this comprehensive guide, we will touch upon the key terminologies related to industrial valves, shedding light on their definitions and significance.
- Valve: A device used to control the flow of fluids (liquids, gases, or slurries) through a piping system by opening, closing, or partially obstructing the passage.
- Ball valve: A type of valve with a ball-shaped disc that rotates to control the flow.
- Gate valve: A valve with a flat or wedge-shaped gate that moves up or down to control the flow.
- Globe valve: A valve with a disc that moves linearly to control the flow, typically used for throttling applications.
- Butterfly valve: A valve with a rotating disc in the shape of a butterfly that controls the flow.
- Check valve: A valve that allows fluid flow in one direction and prevents backflow in the opposite direction.
- Smart valve: A valve equipped with sensors, actuators, and communication capabilities, allowing for remote monitoring, control, and integration into digital systems for enhanced performance and diagnostics.
- Actuator: A mechanism that operates the valve, converting an input signal into a physical motion to open or close the valve.
- Flow rate: The volume of fluid passing through a valve per unit of time, typically measured in gallons per minute (GPM) or cubic meters per hour (m³/h).
- Pressure drop: The decrease in pressure across a valve caused by flow resistance. It is the difference between the pressure upstream and downstream of the valve.
- Trim: The internal components of a valve that come into contact with the flowing fluid, including the disc, seat, stem, and other sealing elements.
- Bonnet: The top portion of a valve that houses the stem and packing, providing a protective enclosure and sealing against leaks.
- Seat: The sealing surface inside the valve where the disc comes into contact to provide shutoff and control the flow.
- Disc: The movable part of the valve that controls the flow by opening or closing against the seat.
- Body: The main casing or housing of the valve that contains the internal components and provides the inlet and outlet connections.
- Cv (Flow Coefficient): A numerical value representing the flow capacity of a valve, indicating the flow rate of water in gallons per minute (GPM) at a specified pressure drop across the valve.
- Stem: The elongated shaft that connects the actuator to the disc or other closure element, transmitting the motion to open or close the valve.
- Stem packing: The material used to seal the area around the stem where it passes through the valve bonnet, preventing leakage.
- Trim materials: The materials used for the internal components of the valve, such as the disc, seat, and stem, selected based on the fluid properties and operating conditions.
- Leakage class: A classification system that defines the allowable level of leakage through a closed valve, typically specified as per industry standards (e.g., API 598).
- Valve size: The nominal size of the valve, which refers to the diameter of the inlet/outlet connections or the internal flow passage.
- Valve positioner: A device used to precisely control the position of the valve actuator, ensuring accurate and reliable valve operation.
- Valve types: Different categories of valves based on their design and operation, such as gate valves, globe valves, ball valves, butterfly valves, plug valves, and check valves.
- Multi-turn valve: A valve that requires multiple rotations of the stem to fully open or close the valve, typically used for isolation or throttling applications.
- Quarter-turn valve: A valve that requires only a quarter turn of the stem to fully open or close the valve, commonly used for quick shut-off or on/off applications.
- Deadband: The range of control signal variation that does not produce any change in valve position or flow rate.
- Anti-cavitation: Measures taken to prevent or minimize the formation and damage caused by cavitation, which occurs when the pressure of a fluid drops below its vapor pressure and then rapidly rises.
- Fail-safe: A feature or mechanism in a valve that ensures it returns to a specified position (e.g., fully open or fully closed) in the event of power loss or actuator failure.
- Pressure rating: The maximum pressure that a valve can withstand without failure, typically expressed in pounds per square inch (psi) or bar.
- End connections: The type of connections at the valve’s inlet and outlet, such as threaded, flanged, welded, or socket-welded, which determine how the valve is connected to the piping system.
- Seat leakage: The amount of fluid that can pass through the closed valve, typically measured in drops per minute, and categorized into different classes based on acceptable leakage levels.
- Trim characteristic: The relationship between the valve position (e.g., stem travel) and the resulting flow rate, which can be linear, equal percentage, or modified equal percentage.
- Cavitation: The formation and collapse of vapor bubbles in a flowing liquid due to localized low-pressure zones, causing erosion and damage to valve components.
- Erosion: The gradual wear and removal of valve materials caused by the impact of high-velocity fluid flow, particularly in applications with abrasive or corrosive fluids.
- Fouling: The accumulation of unwanted deposits or substances on the internal surfaces of the valve, which can affect its performance and efficiency.
- Low flow trim: Additional components or modifications in the valve design to improve control accuracy and stability at low flow rates.
- Lockout/tagout: Safety procedures followed to isolate and lockout valves during maintenance or repair activities to prevent accidental operation and ensure the safety of personnel.
- Valve sizing: The process of determining the appropriate valve size based on the required flow rate, pressure drop, and other factors to achieve optimal system performance.
- Anti-static design: Measures taken to prevent the build-up of static electricity on the valve, reducing the risk of sparks in potentially hazardous environments.
- Blowdown: The process of reducing the pressure within a valve or piping system by allowing a controlled discharge of fluid, typically used to release pressure before maintenance or to prevent over-pressure situations
Familiarity with the terminologies related to industrial valves is vital for effective communication and understanding within the industry. By grasping these terms, professionals in the field can enhance their knowledge and make informed decisions when it comes to selecting, operating, and maintaining industrial valves. Like any industry industrial valves is also an evolving industry, terms mentioned here might change and evolve as and when innovations in this industries happen with respect to process, raw materials etc. Stay curious, explore further, and keep building your expertise in this critical field of fluid control.
At Moglix you have access to the most comprehensive range industrial valve solutions coupled with a team of industry experts who understand your requirement and customise and reverse engineer solutions that justify your requirements, budgets and timelines