Seamless Excellence: Exploring the Seamless Pipe Manufacturing Process
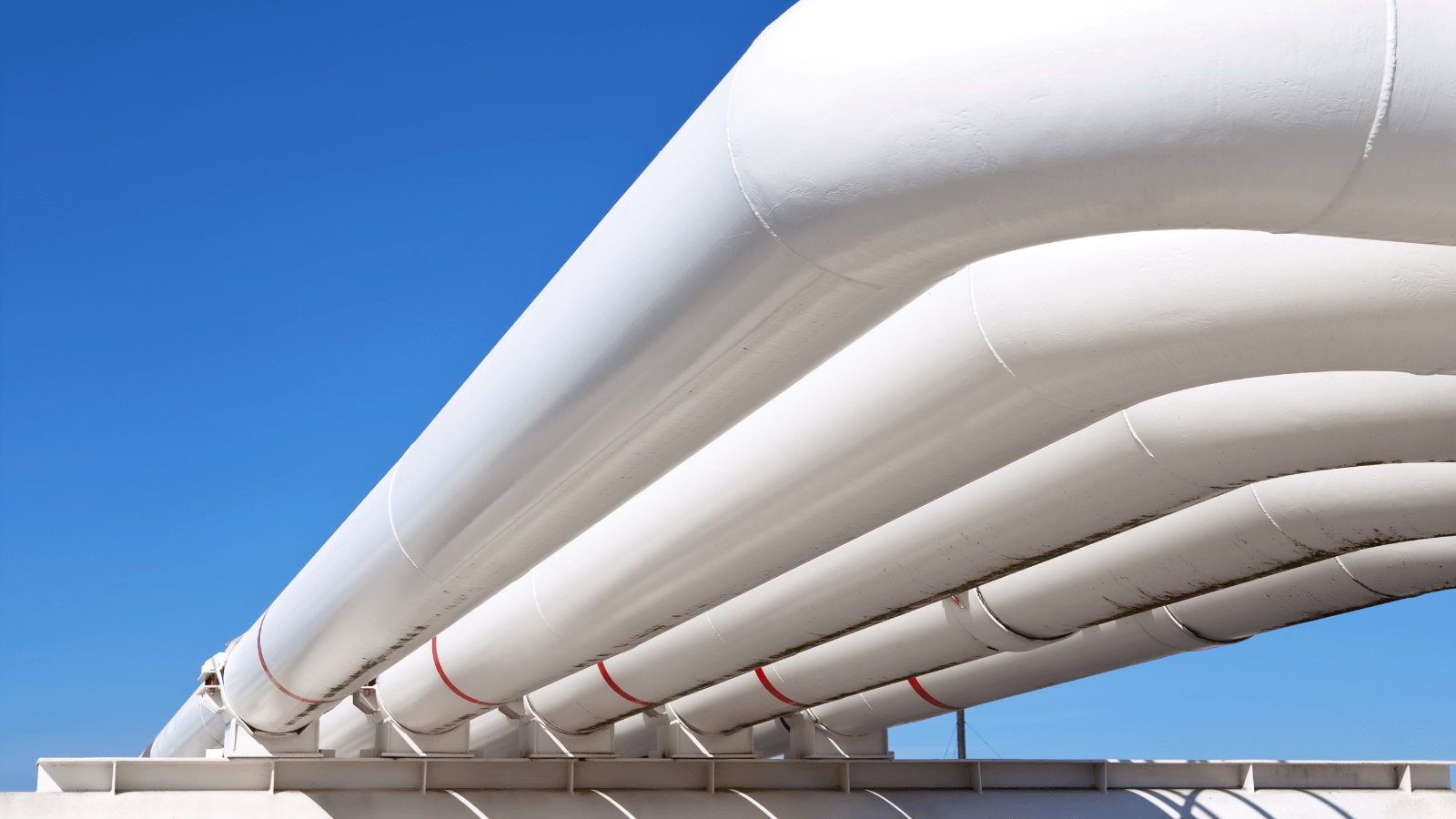
According to a report by Grand View Research, the global seamless pipe market size is projected to reach USD 114.8 billion by 2028, with a compound annual growth rate (CAGR) of 3.6%. They are known for their superior performance and are free from welding seams, making them stronger and more resistant to pressure and corrosion. They play a crucial role in industries worldwide such as oil and gas, construction, and automotive, providing strength, durability, and reliability. Manufacturing seamless pipes is an intricate process that transforms molten metal into seamless excellence.
Seamless Manufacturing
The manufacturing process of seamless pipes usually involves the following steps:
- Raw Material Selection: High-quality steel billets or solid ingots are carefully chosen as the raw materials for seamless pipes. The selection process ensures that the material meets specific requirements for composition, purity, and structural integrity.
- Heating and Piercing: The selected raw material is heated to a high temperature using a furnace. Once heated, the material is pierced by a piercing mill or a rotary piercing machine to create a hollow cylindrical shape known as a shell.
- Shell Rolling: The pierced shell is then rolled by a mandrel mill or a plug mill. This process reduces the outer diameter and increases the length of the shell while maintaining a consistent wall thickness.
- Sizing: After rolling, the pipe is subjected to a sizing mill. This mill further reduces the diameter and refines the wall thickness to achieve the desired dimensions and tolerances.
- Heat Treatment: Heat treatment is often employed to enhance the mechanical properties and remove residual stresses from the pipe. This involves processes like normalizing, annealing, or quenching and tempering, depending on the specific requirements of the pipe.
- Straightening and Cutting: The pipe undergoes a straightening process to remove any residual curvature and ensure it has a straight and uniform shape. It is then cut to the desired length using either a flying saw or a cutting torch.
- Surface Treatment: The surface of the seamless pipe may be treated to improve corrosion resistance, appearance, or other specific requirements. This can involve processes such as pickling, passivation, or coating.
- Inspection and Testing: The finished seamless pipes undergo rigorous inspection and testing to ensure they meet the required quality standards. This can include visual inspection, dimensional checks, non-destructive testing, and mechanical property testing.
Marking and Packaging: The pipes are marked with relevant information, such as size, material, and heat number, for identification purposes. They are then carefully packaged for transportation, storage, and delivery to customers.
From the precise selection of raw materials to the rigorous quality control measures, the seamless pipe manufacturing process demands meticulous attention to detail. By understanding this process, we gain insights into the exceptional qualities and widespread applications of seamless pipes. As industries continue to rely on seamless excellence, their impact on safety, efficiency, and cost savings becomes increasingly evident. At Moglix, we have been working with organisation big and small to help them with industrial pipe procurement. We have the most comprehensive range of certified seamless pipes, from all brands which cater to all budgets. Know More