The PPE Shortage of 2020: 4 Insights for Your Supply Chain
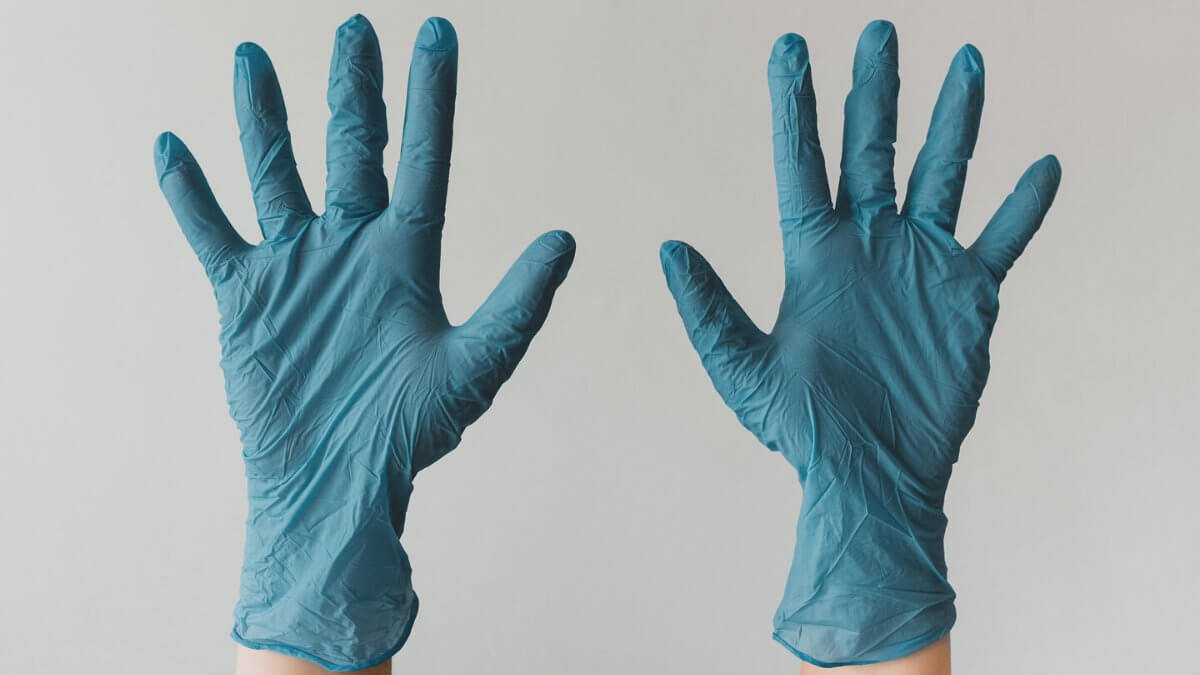
The PPE Shortage of 2020: 4 Insights for Your Supply Chain
A recent press release published by the Department of Health and Social Care in the UK on 25 June suggested that about 2 billion PPE items were delivered to the frontline workers since the start of the pandemic. This outcome, the release said, was a collaborative effort of the government, NHS, industry bodies and the armed forces, to massively scale-up distribution networks. In the last two months, this news has come as a welcome relief to everyone, especially, frontline workers. What the government says it has achieved is no small feat.
However, some reports such as the British Medical Association suggest that about 1 in every 2 frontline UK doctors surveyed had to source their own PPE. Even Italy, which has one of the best public health systems in the world, was dependent on imports and donations of protective equipment and they didn’t have enough to fight the pandemic.
Could many of these have been prevented if they had access to effective and adequate PPE? The answer is a resounding yes. However, our unpreparedness to handle the PPE demand was largely due to the global nature of the crisis. In a scenario where a particular country or a continent were only affected, the rest of the world could have replenished the PPE demand. The global nature of this crisis has accentuated this shortage of PPE around the world. This does not mean that there are gaps in all global supply chains. Even before coronavirus struck, global trade volumes were falling for the first time since the 2008-2009 financial crisis.
In fact, what the pandemic has really done is reinforced the focus on the importance of medical supplies and products in the supply chain. According to a report by WTO, trade in medical products (personal protective products, hospital and laboratory supplies, medicines and medical technology) which have been described as critical and in severe shortage during the COVID-19 crisis totaled about USD 597 billion in 2019, accounting for 1.7% of total world merchandise trade.
Read: COVID19: The Three Phases of Recovery in Manufacturing
Today in the aftermath of the pandemic, it is now estimated that the global personal protective equipment (PPE) market, which was valued at USD 52.7 billion in 2019, is expected to reach USD 92.5 billion by 2025. A number of countries and companies, including us, have repurposed their supply chains to meet demands of masks, sanitizers and medical equipment locally and globally.
To ensure this demand continues to be met, organizations need to invest in increasing visibility and customise the operability of their supply chains if they intend to meet the complex demand patterns across countries and companies alike. These are a few lessons that we have learned from the disruption caused by the coronavirus. These practices will go a long way into exemplifying supply chains of the future.
Listen: How We are Enabling UK Businesses to Get Back to Work.
1) Adapt and learn
The modern supply chain is long and complex with multiple links. Therefore, it is important to establish accurate and timely communication between the suppliers and end-consumers. To ensure that it happens, and that the transfer of information doesn’t get lost in translation, there needs to be open communication between countries where the disruption of one supply chain can be overcome by another in the future. Localisation of supply chains is one thing, but tighter supply networks could also lend better enforcement of supplier standards and improve product quality. Take for instance, Since the 2011 disaster in Japan, global auto suppliers have changed the way they produce and source the auto parts required to assemble a single car, including raising stocks, diversifying production and creating alternative manufacturing capabilities.
2) Keep your customers close, keep your suppliers closer
Let’s consider the example of the NHS. The Category Tower Service Providers (CTSPs), which are responsible for approving the companies that appear on the Secretary of State for Health and Social Care (SCCL) catalogue, are not required to diversify the supplier base for the products in their “category tower”. This is done so, in part, to create an oligopoly or limit the competition. However, in the current circumstances like these, the NHS has the opportunity to expand the SCCL catalogue so that procurement of scarce goods in bulk can take place. This means that more suppliers will have the opportunity to enter the category tower and increase reliability of supply during disruptions.
3) Increase visibility across the supply chain
The modern supply chain is long and complex, but it doesn’t have to be opaque. Investing in increasing visibility across the supply chain will enable executives to make decisions in real-time, conducting an end-to-end risk assessment, identifying potential problem areas, and devising crisis management strategies. Visibility across the supply chain is also critical for making decisions around how to restart lines, prioritize products, and manage relationships with suppliers. A large networking solutions company provides data on changes in supply and demand to partners continuously so they can respond quickly with the help of an technology platform, to connect suppliers and the company. This allows all the firms to have the same demand and supply data at the same time, and keep track of changes in supply or demand immediately.
4) Invest in monitoring tools and analytics
The companies that have responded well to the crisis are ones that took a digital-first approach. They invested in monitoring tools and analytics to forecast the changing demand patterns using market, economic, and social media indicators at the beginning of the pandemic and adjusted their operations appropriately to avoid overstocks and stockouts.
The coronavirus pandemic has given us a lot of food for thought. If nothing else, it has proved that our supply chains need to be more resilient to such unplanned disruptions. Business leaders need to get together to discuss all the possible “what-if” scenarios and the plan of action for the same. The one thing that will aid them in making these decisions? Investing in making their supply chains more transparent and technology-driven.
Moglix has extensive experience in streamlining the supply chains of some of the biggest companies in the world. Our range of solutions including Optimize MRO, Digitize procurement, Simplify packaging, SaaS, and now PPE has helped us in supporting businesses to handle this unprecedented crisis.
Decoding Workplace Implications for Enterprises From the Guidelines for Lockdown 4.0
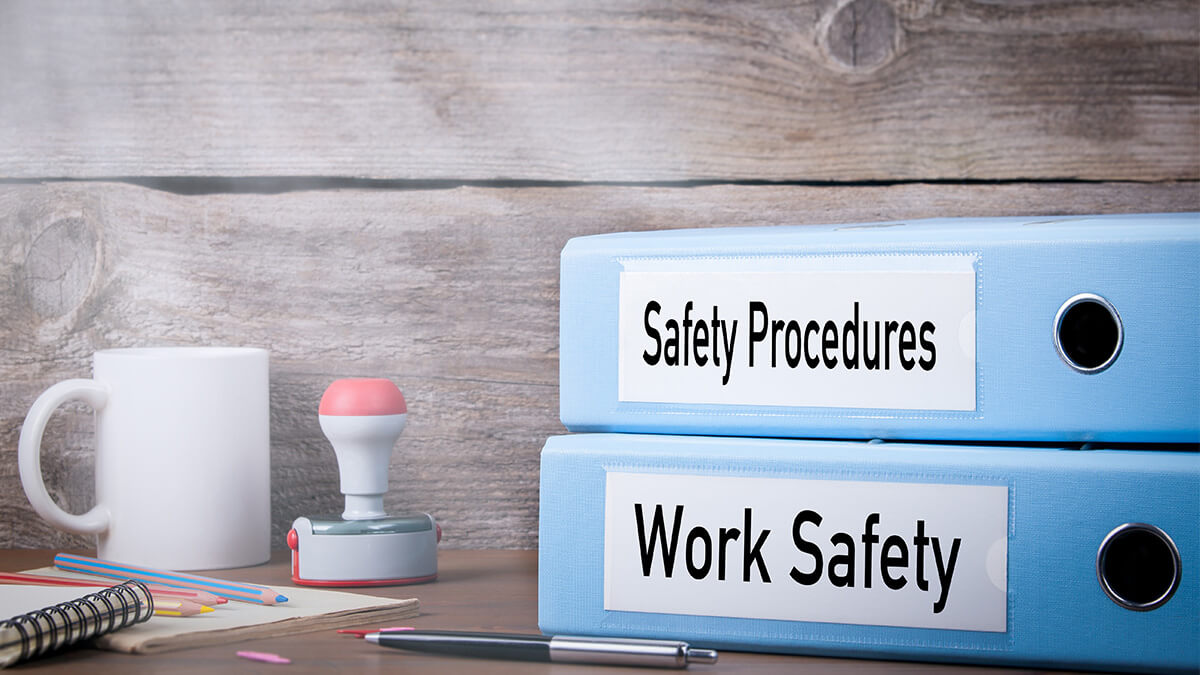
Decoding Workplace Implications for Enterprises From the Guidelines for Lockdown 4.0
In the wake of the lockdown 4.0, business enterprises are planning to invest efforts and time now to map their requirements of PPE kits afresh as they aim to restart and ramp-up commercial activity. In the wake of the evolving contours of the efforts to combat the COVID19 pandemic in India through an extension of the lockdown up to 31st May 2020, the Ministry of Home Affairs, Government of India has issued revised guidelines for gradually reopening chosen industry verticals and sectors in the economy while ensuring adherence to:
- Basic preventive measures
- Preventive measures for offices
- Measures to be taken on the occurrence of cases
- Disinfection procedures to be implemented in case of occurrence of suspect/confirmed cases
While business enterprises located in such buffer zones and containment zones are not yet allowed to resume commercial operations, the MHA guidelines for the resumption of economic activity during lockdown 4.0 apply to all enterprises located in green, orange and red zones and assume significance from the standpoint of people, operations, and supply chain.
What Do the Basic Preventive Measures Imply for Enterprises? Procure PPE Items In Bulk?
The basic preventive measures mandate physical distancing of at least one meter at all times, use of masks, regular washing of hands for at least 20 seconds with hand sanitizers, and adherence to respiratory etiquette. The basic preventive measures apply to all people and are agnostic of commercial activity. However, this assumes importance from the standpoint of enterprises that operate in densely populated physical environments and have high exposure to a traffic of people such as retail, public transport, MSME, food, and beverages, pharma retail, repair, and maintenance services, MRO, healthcare, etc. Enterprises in these verticals should ideally invest in the bulk procurement of PPE items like alcohol-based hand sanitizers, N95 masks, coveralls for their employees. For enterprises operating in the downstream of the supply chain, it is important that they train their staff adequately in practicing zero-contact delivery to ensure the safety of themselves, their customers, and the community at large.
What are the Implications of the Preventive Measures for Offices? Is Digital Workflow the New Normal?
The new set of preventive measures for offices during Lockdown 4.0 requires enterprises operating from offices to restrict the entry of visitors apart from the organizational staff, avoid physical meetings and restrict the use of hard copy documents and files for official correspondence as much as possible. Given the need for social distancing, it is also important that enterprises make the point of common use in their infrastructure low-touch. For instance, no-touch equipment like doors, cloud installed human resource information systems for attendance in lieu of biometric machines, and automated office equipment are recommended. Beyond these, the standard measures for social distancing like regular screening of body temperature of all people entering the premises of the office using IR thermometers, soap dispensers, and sanitizer dispensers for regular sanitization are advised.
For enterprises, this translates into the requirements of designating the workplace infrastructure management team to map seating arrangements at the workplace for adherence to social distancing, creating daily rosters for the staff to attend to work and thus accordingly map the supplies of PPE items. In fact, it is advisable that data be maintained to proactively map PPE line items, volumes of each line item for a financial quarter, local PPE suppliers with credible records, procure the items in advance and further, create a separate PPE store with due diligence for safe storage, replenishment of inventories and disposal of used items as per instructions recommended by the MoHFW. Further, it is also advised that enterprises gradually move up the levels of digital workplace maturity by resorting to the use of online platforms for collaboration, sharing data on a “need to know basis” and digital workflows to make business processes low-touch. This applies especially to processes with external dependencies for the enterprise such as purchases, invoicing and payments, inventory management, track and trace of cargo and procurement, direct contract management, and supplier collaboration.
What Do the Measures to be Taken on the Occurrences of Cases Imply? Can Contact Tracing Reduce Risks?
While the guidelines of the MHA recommend measures for self-isolation and quarantine for both suspect and confirmed cases of COVID19, it calls for enterprises to be more agile in ensuring compliance with preventive measures. It makes good sense to suggest the reorganization of the workplace from the ground up and deployment of screening measures to control the sporadic transmission of the pandemic at the workplace. The use of the Arogya Setu app that facilitates contact tracing as recommended by the government can be a prima facie precursor to detecting and mitigating health risks and its spillover to business. This can especially be the case in business processes that entail mobility such as logistics, warehousing, inventory management, and supply chain.
What are the Implications of the Disinfection Procedures for Enterprises?
In the event of detection of COVID19 positive cases, the new guidelines for lockdown 4.0 mandate measures for thorough disinfection of the entire building premises before resuming work and close monitoring of the health of office staff with a low-risk exposure for the next 14 days. This implies that before resuming commercial activity, enterprises need to be ready with adequate stocks of surface cleaning agents, surface cleaning sprays, floor disinfectants, Lysol disinfectants, and disinfectant sprays to cope with any eventuality. The guidelines handbook mandates that disinfectants be used for regularly sanitizing: entrance gate of building and office, cafeteria and canteens, meeting room, conference halls, open areas, verandah, the entrance gate of sites, bunkers, portacabins, buildings, equipment and lifts, washrooms, toilets, sinks, water points, walls, and other surfaces. Further, it deems the sanitization of all vehicles, machinery entering the premises, and thermal screening for everyone entering and exiting the workplace as mandatory.
PPE Kits, Automation Software, and Digital Workflow: The Future of Workplaces in India
On a concluding note, the latest guidelines for lockdown 4.0 require enterprises to adapt to a new normal for the long term by securing the lives of its people and communities that are dependent on them. This can be enabled through agile collaboration between PPE suppliers and manufacturers on one hand and business enterprises that need them on the other for seamless procurement and distribution of PPE medical kits. Further, the requirement for social distancing calls for a new work culture in India that is driven by higher automation of programmable functions and greater penetration of technology into business processes especially in the ones that require teamwork, collaboration, and exposure to external environments beyond the control of enterprises. Paperless workplaces and workflows are here to stay.