The PPE Shortage of 2020: 4 Insights for Your Supply Chain
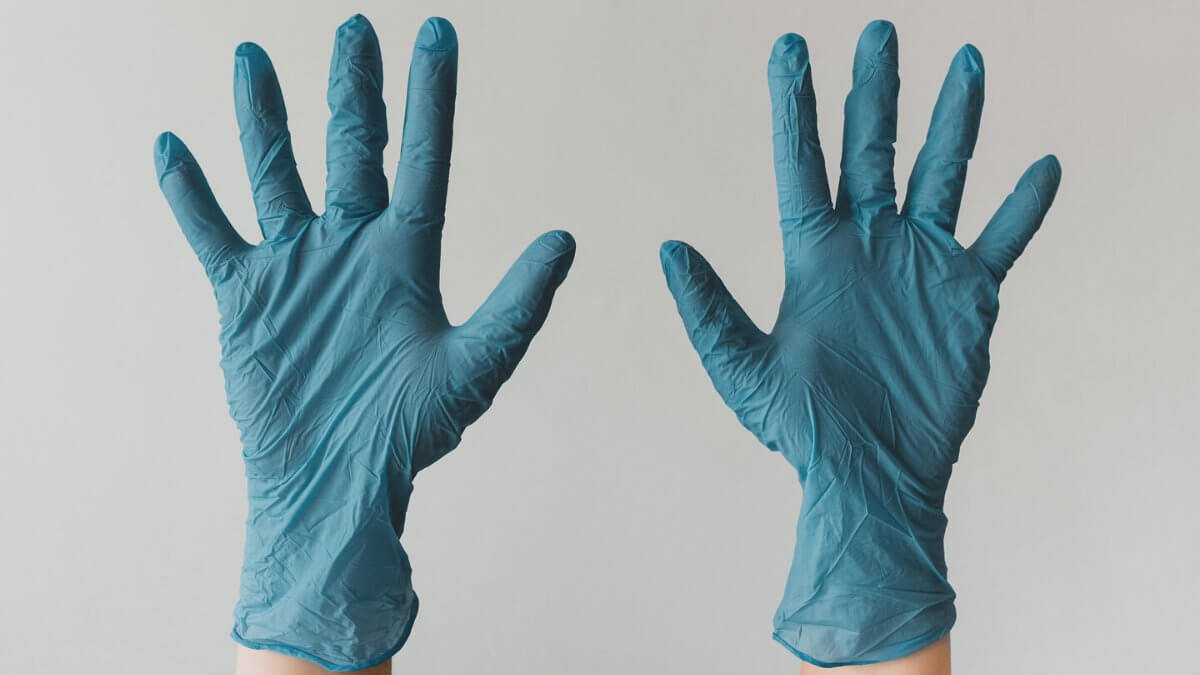
A recent press release published by the Department of Health and Social Care in the UK on 25 June suggested that about 2 billion PPE items were delivered to the frontline workers since the start of the pandemic. This outcome, the release said, was a collaborative effort of the government, NHS, industry bodies and the armed forces, to massively scale-up distribution networks. In the last two months, this news has come as a welcome relief to everyone, especially, frontline workers. What the government says it has achieved is no small feat.
However, some reports such as the British Medical Association suggest that about 1 in every 2 frontline UK doctors surveyed had to source their own PPE. Even Italy, which has one of the best public health systems in the world, was dependent on imports and donations of protective equipment and they didn’t have enough to fight the pandemic.
Could many of these have been prevented if they had access to effective and adequate PPE? The answer is a resounding yes. However, our unpreparedness to handle the PPE demand was largely due to the global nature of the crisis. In a scenario where a particular country or a continent were only affected, the rest of the world could have replenished the PPE demand. The global nature of this crisis has accentuated this shortage of PPE around the world. This does not mean that there are gaps in all global supply chains. Even before coronavirus struck, global trade volumes were falling for the first time since the 2008-2009 financial crisis.
In fact, what the pandemic has really done is reinforced the focus on the importance of medical supplies and products in the supply chain. According to a report by WTO, trade in medical products (personal protective products, hospital and laboratory supplies, medicines and medical technology) which have been described as critical and in severe shortage during the COVID-19 crisis totaled about USD 597 billion in 2019, accounting for 1.7% of total world merchandise trade.
Read: COVID19: The Three Phases of Recovery in Manufacturing
Today in the aftermath of the pandemic, it is now estimated that the global personal protective equipment (PPE) market, which was valued at USD 52.7 billion in 2019, is expected to reach USD 92.5 billion by 2025. A number of countries and companies, including us, have repurposed their supply chains to meet demands of masks, sanitizers and medical equipment locally and globally.
To ensure this demand continues to be met, organizations need to invest in increasing visibility and customise the operability of their supply chains if they intend to meet the complex demand patterns across countries and companies alike. These are a few lessons that we have learned from the disruption caused by the coronavirus. These practices will go a long way into exemplifying supply chains of the future.
Listen: How We are Enabling UK Businesses to Get Back to Work.
1) Adapt and learn
The modern supply chain is long and complex with multiple links. Therefore, it is important to establish accurate and timely communication between the suppliers and end-consumers. To ensure that it happens, and that the transfer of information doesn’t get lost in translation, there needs to be open communication between countries where the disruption of one supply chain can be overcome by another in the future. Localisation of supply chains is one thing, but tighter supply networks could also lend better enforcement of supplier standards and improve product quality. Take for instance, Since the 2011 disaster in Japan, global auto suppliers have changed the way they produce and source the auto parts required to assemble a single car, including raising stocks, diversifying production and creating alternative manufacturing capabilities.
2) Keep your customers close, keep your suppliers closer
Let’s consider the example of the NHS. The Category Tower Service Providers (CTSPs), which are responsible for approving the companies that appear on the Secretary of State for Health and Social Care (SCCL) catalogue, are not required to diversify the supplier base for the products in their “category tower”. This is done so, in part, to create an oligopoly or limit the competition. However, in the current circumstances like these, the NHS has the opportunity to expand the SCCL catalogue so that procurement of scarce goods in bulk can take place. This means that more suppliers will have the opportunity to enter the category tower and increase reliability of supply during disruptions.
3) Increase visibility across the supply chain
The modern supply chain is long and complex, but it doesn’t have to be opaque. Investing in increasing visibility across the supply chain will enable executives to make decisions in real-time, conducting an end-to-end risk assessment, identifying potential problem areas, and devising crisis management strategies. Visibility across the supply chain is also critical for making decisions around how to restart lines, prioritize products, and manage relationships with suppliers. A large networking solutions company provides data on changes in supply and demand to partners continuously so they can respond quickly with the help of an technology platform, to connect suppliers and the company. This allows all the firms to have the same demand and supply data at the same time, and keep track of changes in supply or demand immediately.
4) Invest in monitoring tools and analytics
The companies that have responded well to the crisis are ones that took a digital-first approach. They invested in monitoring tools and analytics to forecast the changing demand patterns using market, economic, and social media indicators at the beginning of the pandemic and adjusted their operations appropriately to avoid overstocks and stockouts.
The coronavirus pandemic has given us a lot of food for thought. If nothing else, it has proved that our supply chains need to be more resilient to such unplanned disruptions. Business leaders need to get together to discuss all the possible “what-if” scenarios and the plan of action for the same. The one thing that will aid them in making these decisions? Investing in making their supply chains more transparent and technology-driven.
Moglix has extensive experience in streamlining the supply chains of some of the biggest companies in the world. Our range of solutions including Optimize MRO, Digitize procurement, Simplify packaging, SaaS, and now PPE has helped us in supporting businesses to handle this unprecedented crisis.