From Welded Woes to Seamless Superpowers: Unveiling Industrial Pipe Secrets
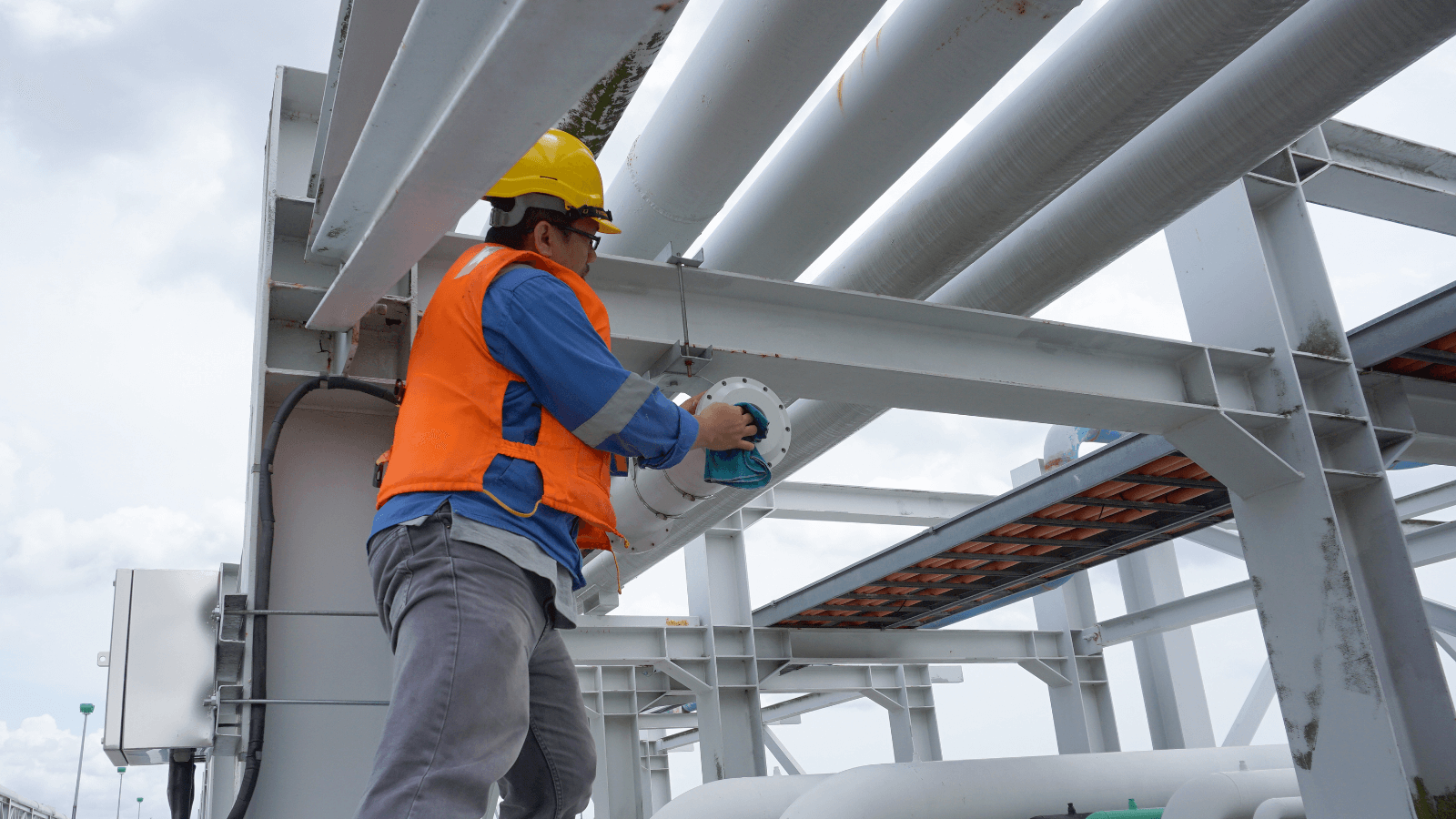
From Welded Woes to Seamless Superpowers: Unveiling Industrial Pipe Secrets
Pipes are the unsung heroes of countless industries, providing a vital conduit for the transportation of fluids and gases. Among the diverse array of pipe options available, seamless pipes emerge as true champions, boasting exceptional strength, unwavering reliability, and peak performance. This blog will enlighten you by unraveling the key differences between seamless and welded pipes while exploring the fascinating realm of materials used in seamless pipe manufacturing.
Seamless pipe – What is it?
A seamless industrial pipe is a type of pipe that is manufactured without any welded seams along its length. It is crafted from a solid cylindrical billet of metal, which is heated and pierced to create a hollow tube. The billet is then elongated and rolled over a mandrel to reduce its diameter and increase its length, resulting in a seamless tube. Seamless industrial pipes are known for their superior strength, reliability, and performance compared to welded pipes.
Understanding Key Differences – Seamless and Welded Pipes
Seamless Pipes:
- Crafted without welded seams along their length, ensuring high structural integrity and reliability.
- By virtue of its design it is resistant to failure, especially under high pressure conditions.
- Smoother internal surfaces, reduces frictional resistance and enabling efficient flow.
- Can withstand pressures up to 20% higher than welded pipes.
Welded Pipes:
- Created by joining two separate pieces, resulting in welded seams that may create potential weak points.
- more susceptible to corrosion, especially in harsh environments.
- Cheaper to produce, but their strength and pressure resistance are comparatively lower than seamless pipes.
- Higher risk of failure under pressure compared to seamless pipes, making them less suitable for critical applications.
Materials Used in Seamless Pipes and Their Applications
Carbon Steel:
- Carbon steel seamless pipes offer excellent strength and durability, making them suitable for industries such as oil and gas, construction, and infrastructure.
- These pipes exhibit exceptional resistance to mechanical stress and corrosion, ensuring long-lasting performance.
- Carbon steel seamless pipes dominate the market, accounting for approximately 70% of the total seamless pipe production.
Stainless Steel:
- Stainless steel seamless pipes are known for their superior corrosion resistance, making them ideal for applications involving aggressive fluids or corrosive environments.
- They are widely used in industries like petrochemicals, pharmaceuticals, and food processing.
- Stainless steel seamless pipes constitute a significant portion of the seamless pipe market, with an estimated market share of around 20%.
Alloy Steel:
- Alloy steel seamless pipes combine the strength of carbon steel with additional alloying elements to provide enhanced mechanical properties, including high temperature and pressure resistance.
- These pipes find applications in industries such as power generation, aerospace, and automotive.
- The global demand for alloy steel seamless pipes is projected to grow at a CAGR of around 7% from 2021 to 2026, according to market studies.
Right Seamless Pipe for Your Project
- Consider the type of fluid or gas being transported: Different fluids and gases have varying chemical properties that require specific pipe materials and corrosion resistance.
- Assess temperature and pressure requirements: Determine the maximum temperature and pressure conditions the pipe will be subjected to, ensuring the selected seamless pipe can withstand them.
- Evaluate corrosion resistance: Analyze the environmental conditions and potential corrosion factors to choose a suitable material that can withstand corrosion and maintain longevity.
- Consult industry standards and seek expert advice: Adhere to recognized standards such as ASTM and API, and consult experts to ensure compliance and receive guidance on selecting the right seamless pipe for your project.
Seamless pipes offer remarkable advantages over welded pipes, including superior strength, pressure resistance, and smoother flow. The selection of the right material, such as carbon steel, stainless steel, or alloy steel, plays a pivotal role in achieving optimal performance and durability. By understanding the key differences and material options, you can make informed choices that meet the specific requirements of your projects. At Moglix, our inhouse, experienced industry consultants and piping experts work with customer procurement teams to understand their requirement and suggest objective, brand agnostics solutions that would put procurement teams challenges at the core. At Moglix you will find the most comprehensive range of certified seamless pipes, from all brands and all budgets. Know More
Cracking the Code to Intelligent Supply Chains
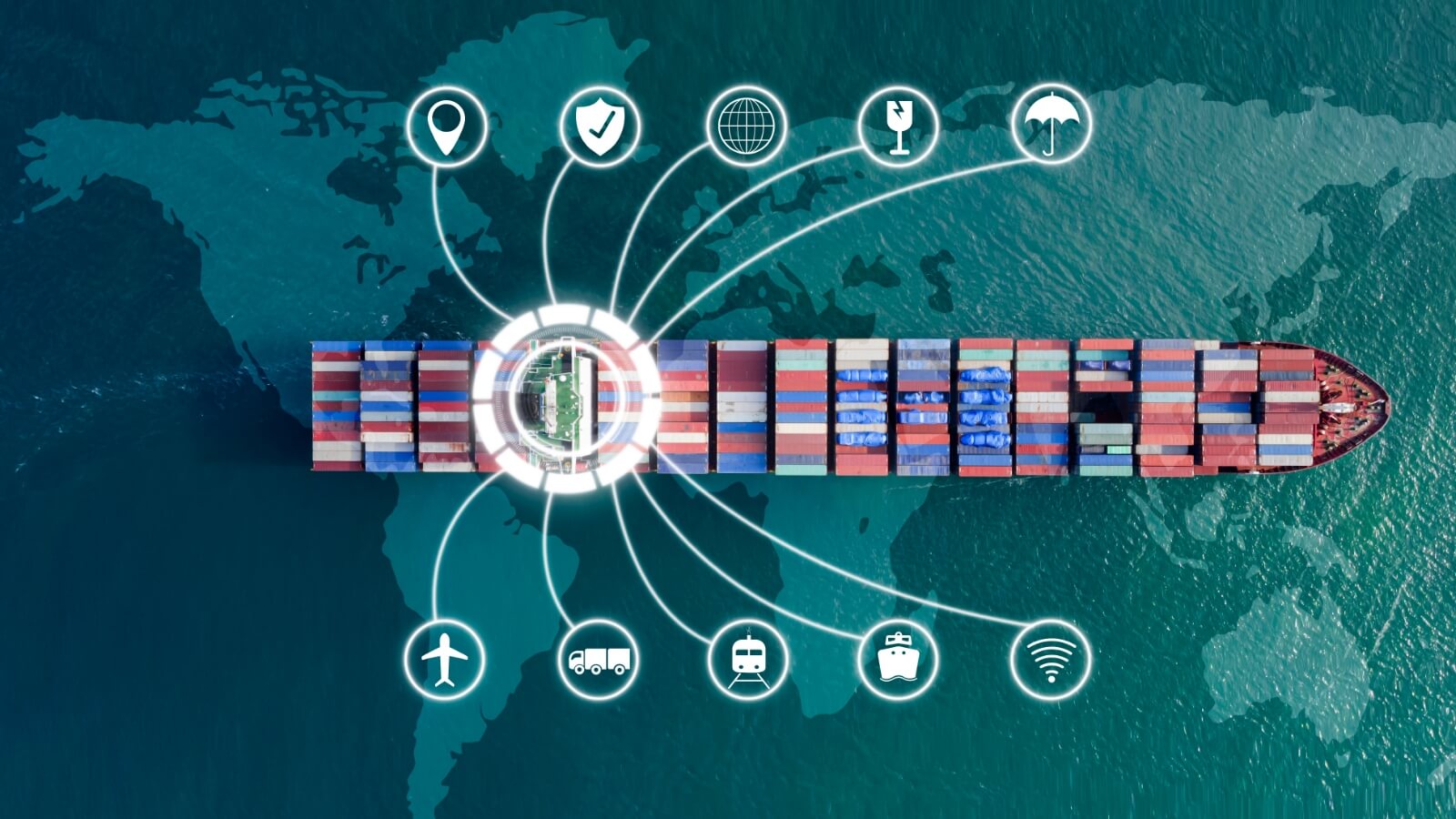
Cracking the Code to Intelligent Supply Chains
Many businesses struggle to optimize their supply chain management; hence, they risk falling behind competitors who can save money and streamline operations through the use of intelligent supply chains.
To stay competitive, businesses need to use new technology for smarter supply chain management. According to McKinsey(1), early adopters of AI-enabled supply-chain management have seen improvements of 15% in logistics costs, 35% in inventory levels, and 65% in service levels compared to slower-moving competitors. However, there is still a significant gap in adopting intelligent supply chains.
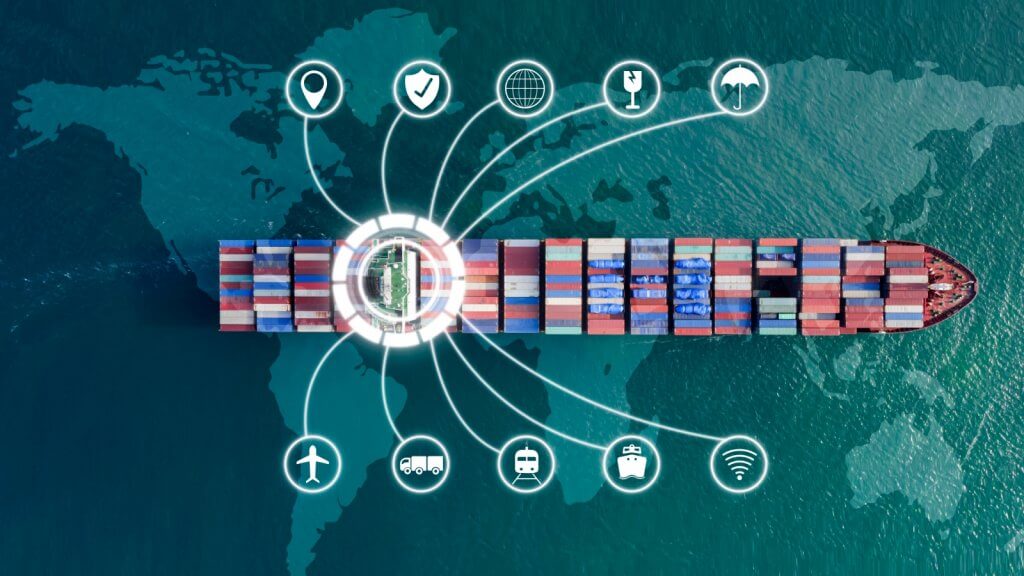
The Art of Smart: Understanding Supply Chain Intelligence
First, let us understand supply chain intelligence.
Supply chain intelligence involves collecting and analyzing data to gain insights into performance. By using technologies like IoT, AI, and machine learning, businesses can monitor and track operations, identify inefficiencies, and improve supply chain management.
Now, let’s explore some trends in supply chain management and how brands can leverage an intelligent supply chain system to achieve commercial and brand success.
Trimming the Fat: Reduce Excess Inventory
Excess inventory can lead to increased storage costs and a decreased return on investment. By using the predictive analytical capabilities of an intelligent supply chain system, organisations can accurately forecast demand and adjust their inventory. This allows businesses to reduce inventory costs by optimising their stock levels, minimising waste and freeing up working capital.
Keeping It Running: Optimise MRO
- Intelligent supply chain systems can help optimise Maintenance, repair, and operations (MRO) by providing real-time data on equipment and maintenance needs.
- Purpose-built technology can track the performance of equipment and predict when maintenance is necessary, reducing downtime and extending the life of machinery.
Supplier Synergy: Improve Supplier Management
- Supply chain intelligence can also help organisations manage their suppliers more effectively.
- Businesses can identify high-performing suppliers and cultivate stronger relationships by analysing supplier performance data.
- Additionally, supply chain intelligence can help organisations identify potential risks in their supply chain, such as supplier disruptions or quality issues.
The Safety Net: Mitigate Risks
- Intelligent supply chains can also help organisations mitigate risks associated with their supply chains.
- By monitoring operations in real-time and analysing historical data, businesses can identify potential risks and take steps to prevent them from occurring.
- For example, supply chain intelligence can help organisations identify suppliers in regions prone to natural disasters and take steps to ensure the continuity of supply.
Join the Revolution: Transforming Your Supply Chain with Intelligence
As supply chain intelligence continues to evolve, it will become increasingly essential for businesses to stay competitive in today’s marketplace. Plug-and-play technology is also making it easier for companies to implement supply chain intelligence solutions without extensive customisation or complex integrations.
In today’s fast-paced business world, supply chain intelligence is no longer a “nice to have” – it’s a must-have for achieving cost savings in procurement. At Moglix, we offer cutting-edge solutions to help you make sense of your data and optimise your supply chain. Download this case study to discover how we helped an automotive OEM unlock a 2% cost savings in procurement.
Contact us to learn more about how we can help you gain a competitive edge.
Additional Reading:
From Bottlenecks to Breakthroughs: How Digitization Can Solve Pharma’s Supply Chain Woes
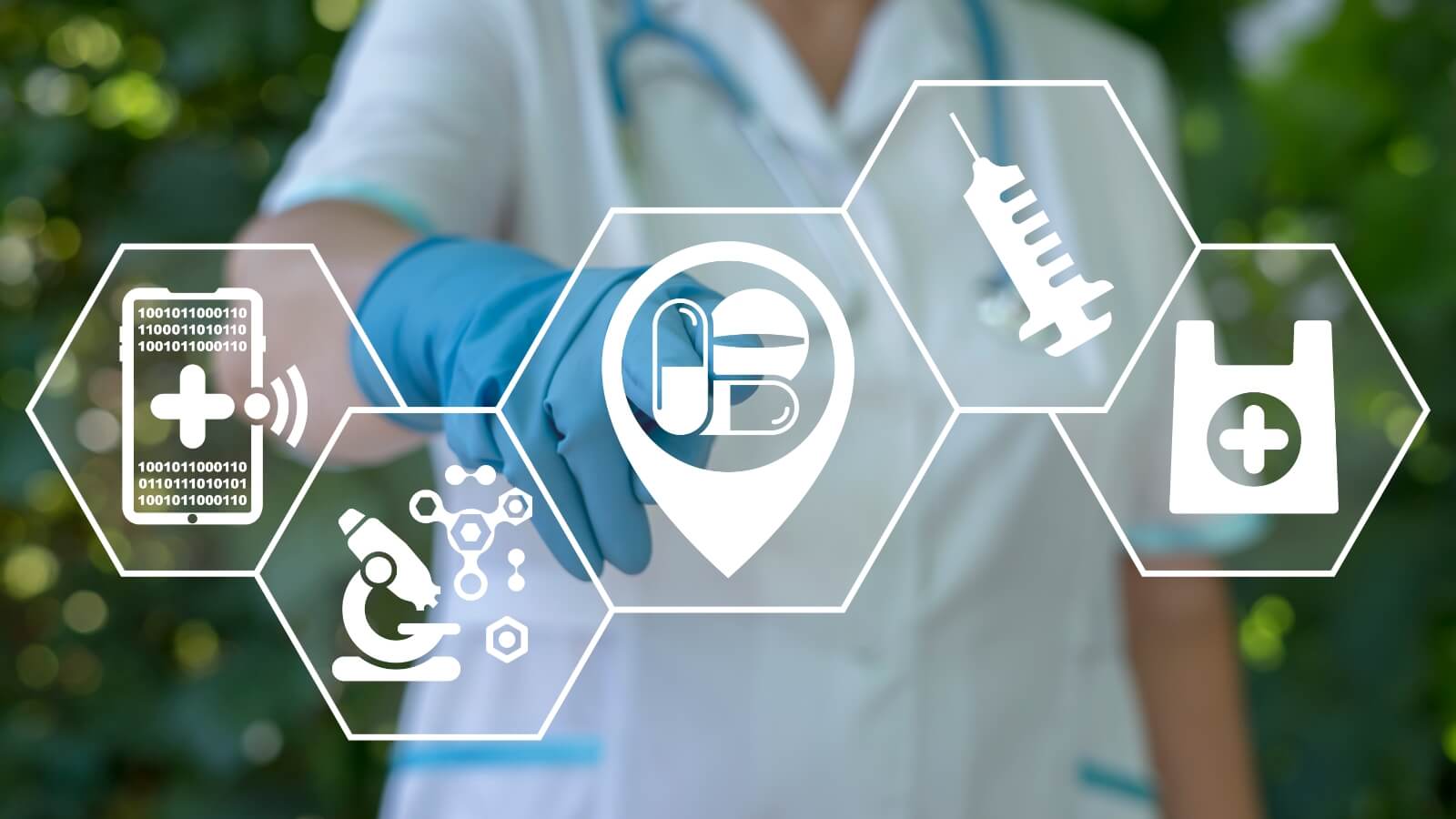
From Bottlenecks to Breakthroughs: How Digitization Can Solve Pharma’s Supply Chain Woes
The pandemic revealed weaknesses in traditional pharmaceutical supply chains, causing procurement challenges and reduced profits due to labor shortages, geopolitical tensions, and regulatory changes. In fact, a McKinsey study(1) found that over a 10-year period, supply chain disruptions pose a significant risk to pharmaceutical companies, potentially resulting in a 25% loss of earnings.
To address these challenges, leading pharmaceutical companies have realized that the traditional ways of supply chain management and procurement are insufficient to tackle today’s challenges, prompting a shift toward digital transformation.
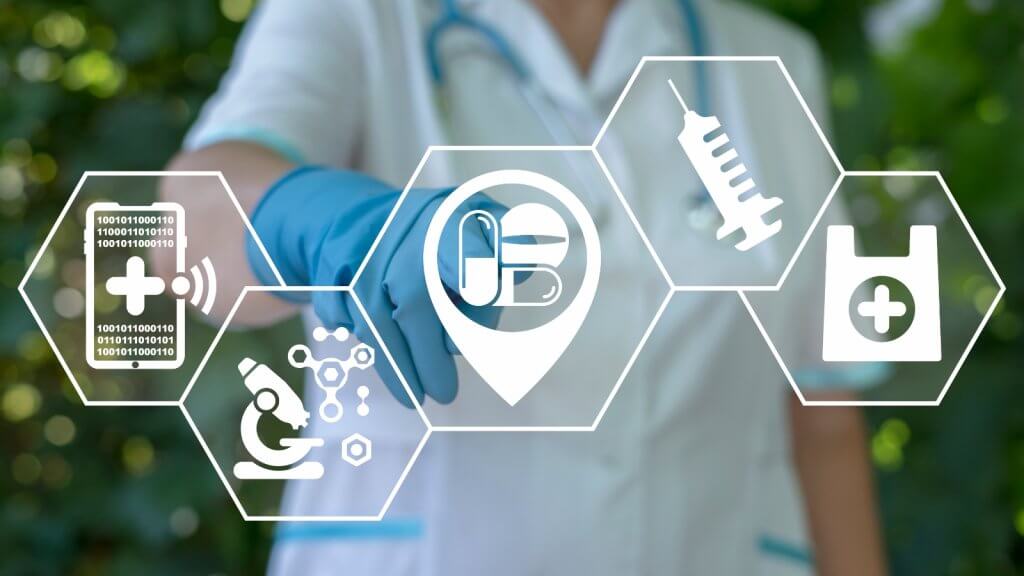
Pharma Industry’s Current Struggles with Supply Chain
Let us first look at some of the current challenges that companies need to address to improve supply chain resilience and reduce disruptions:
- Cold Chain Losses: Maintaining specific temperature parameters is crucial for preserving the quality of medicines and drug products during the supply chain process. According to the IQVIA Institute for Human Data Science(2), the pharmaceutical industry loses approximately $35 billion annually due to temperature-controlled cold chain logistics failures.
- ‘Offshoring’: Offshoring of production and sourcing can create several challenges, including quality control issues, geopolitical risks, longer lead times, and increased transportation costs. As a result, many pharma companies are considering ‘nearshoring’ to improve supply chain resilience.
- API and Raw Material Costs: Active Pharmaceutical Ingredients and raw material costs account for a major chunk of pharmaceutical manufacturing costs. Cost fluctuations and shortages of these materials significantly disrupt the supply chain and increase production costs.
- Lack of Visibility: Limited real-time data access and visibility into critical KPIs hampers pharma supply chain performance.
Digitization: The Prescription for the Pharma Industry’s Supply Chain Headaches
As companies look for solutions to overcome supply chain challenges, many are turning to digital transformation. In 2023, Pharmaceutical companies will use digital supply chain tech more in 2023 to gain the following benefits.:
- Digitization helps track products in real-time to identify and address supply chain disruptions.
- It also ensures transparency and accountability in the supply chain.
- Digitization automates inventory management, preventing the risk of stockouts or overstocks.
The Digital Frontier: Revolutionizing the Pharma Industry’s Supply Chain
Digital technologies have been a transformative force in the pharmaceutical industry, revolutionizing supply chains by improving collaboration, integration, and efficiency. These advancements have helped companies reduce costs and enhance patient outcomes, making it essential for pharmaceutical firms to adopt these solutions.
At Moglix, we provide innovative solutions for improving the efficiency of supply chains. Discover how we helped a leading vaccine manufacturer implement just-in-time delivery to 16 plants across India. By doing so, the manufacturer was able to unlock working capital and reduce inventory carrying costs, leading to significant cost savings.
Contact us to know more about our approach and how we can support your digital transformation strategy.
Additional Reading:
Reimagining Procurement with Digital Transformation in FY 2024
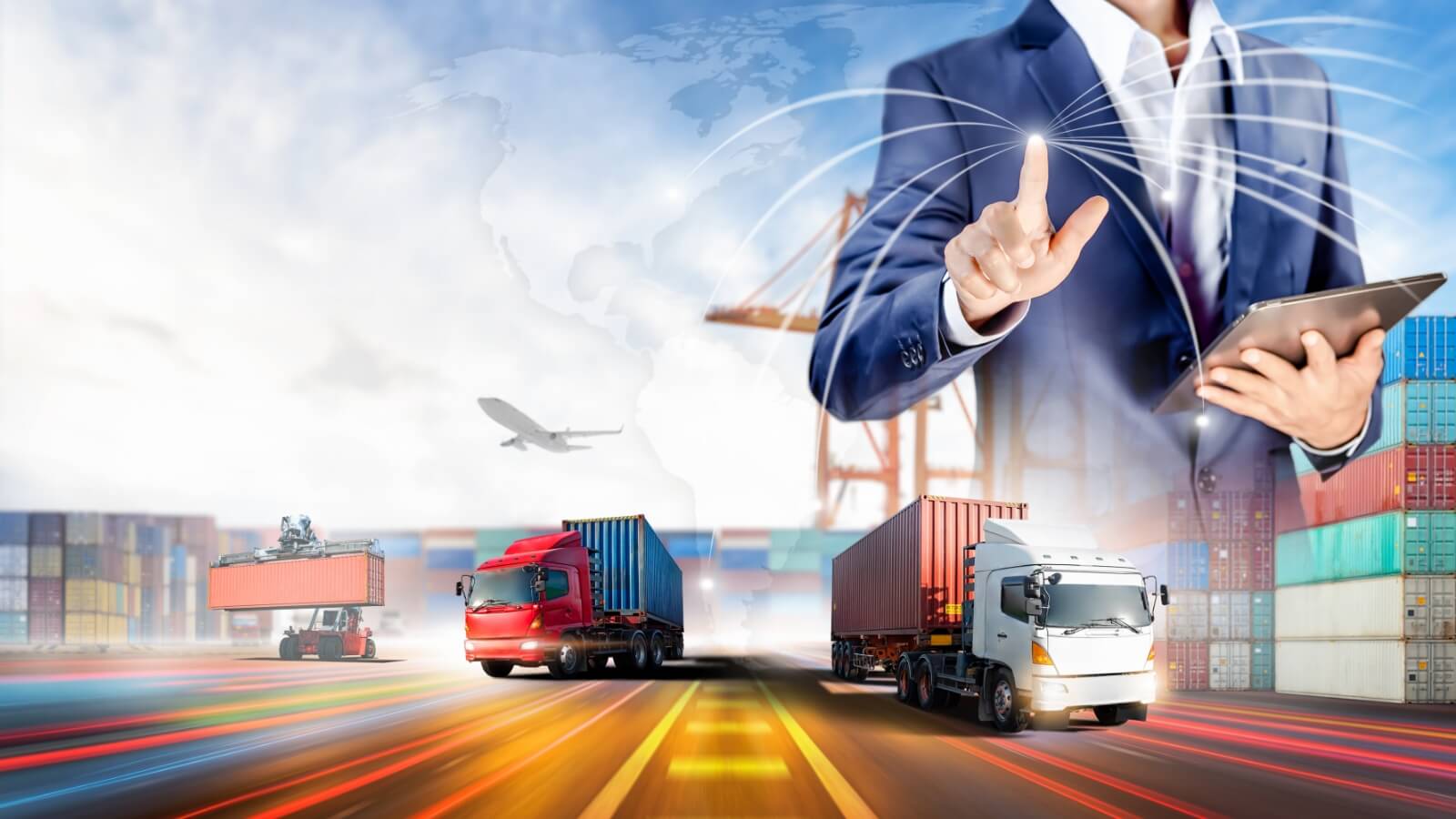
Reimagining Procurement with Digital Transformation in FY 2024
The COVID-19 pandemic, long-standing skilled labour shortages, and recent geopolitical developments have disrupted the global supply chain. As a result, companies are adopting various strategies to overcome these challenges. A recent McKinsey report(1) found that 67% of businesses have adopted digital tools for end-to-end supply chain visibility, making them twice as likely to avoid disruptions caused by early 2022 supply chain disruptions. Therefore, the digitisation of procurement is emerging as the most effective one for building resilient supply chains.
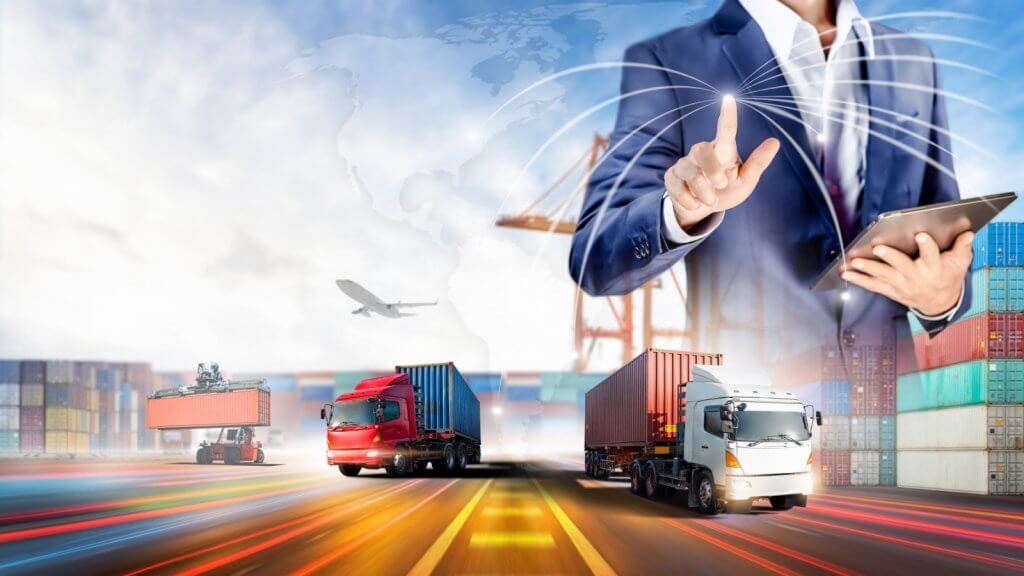
While more than 60% of companies have fully embraced digital transformation in procurement, others still face significant challenges in adopting and implementing digital tools. This digital divide is a significant issue that needs to be addressed in procurement functions. Let us take a closer look.
The Digital Divide: Analysing the Need-Gap in Procurement
Access to critical decision-support information such as production statuses, inventory levels, capacities, forecasts, KPIs, and more can be delayed when data is siloed and disconnected in procurement functions. Procurement functions still face challenges such as:
- Fragmented and outdated processes
- Poor data management
- Inefficient supplier management
- Lack of visibility into spend data
To overcome these barriers, procurement teams need to be more agile, efficient, and responsive to changes in the market by embracing digital transformation.
From Paper to Pixels: The Benefits of Digitising Your Procurement
Let us look at some of the beneficial impacts of digital transformation on procurement:
Automating Procurement Processes
- Digitisation can help eliminate the manual, time-consuming tasks that procurement teams have daily, such as supplier onboarding, contract management, and purchase order processing.
- Automation can help reduce errors, increase speed, and free procurement professionals’ time to focus on more strategic tasks.
Improving Data Management
- Digital transformation can help improve data management by providing real-time visibility into spend data. This visibility can help procurement teams identify trends, reduce costs, and negotiate better contracts with suppliers.
- By leveraging big data analytics and AI, procurement teams can gain insights into supplier performance, risk management, and compliance, enabling them to make data-driven decisions.
Enabling Efficient Supplier Management
Digitisation can help procurement teams manage supplier relationships more effectively by providing real-time insights into supplier performance, risk management, and compliance. This can help procurement teams optimise their supplier base, improve supplier performance, and reduce supplier risk.
The Future of Procurement is Digital: Join the Journey in FY 2024
The rise of digital transformation has elevated procurement from a tactical function to a strategic one, empowering procurement teams to generate value for their organisations. By leveraging technology, professionals can effectively tackle bottlenecks in the procurement process.
At Moglix, our tailored digital solutions are designed to streamline the entire procurement cycle. Download this case study to discover how we helped a major chemical company overcome supplier fragmentation, limited MRO purchase visibility, and procurement price variation challenges. Our solutions delivered an 85% reduction in processing of transactions, POs, and invoices and a 5% savings in procurement costs.
Contact us today to learn how we can help you digitally transform your procurement strategy.
Additional Reading:
Safety Frontline-A guide to choosing right gumboots for your industry
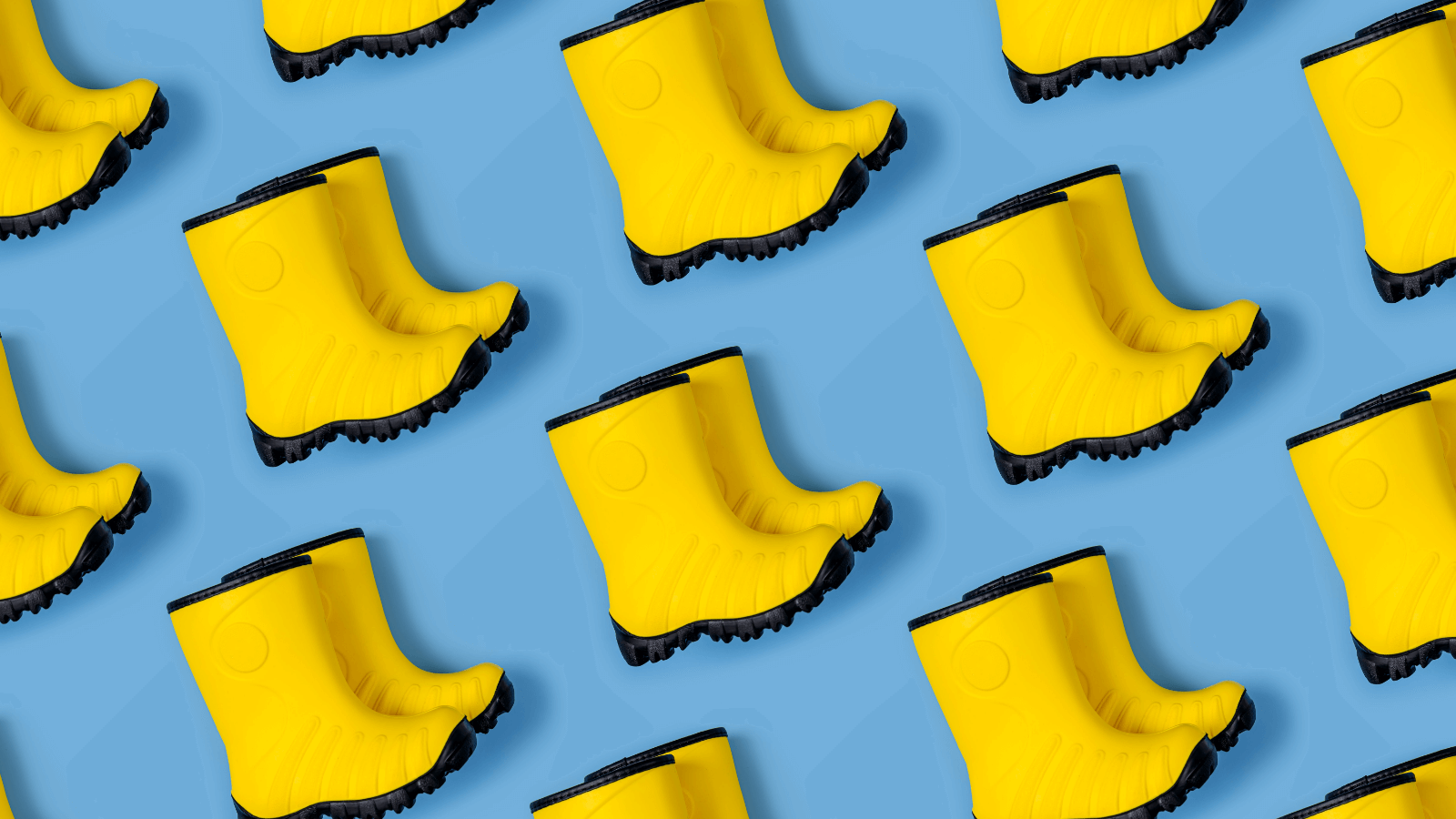
Safety Frontline-A guide to choosing right gumboots for your industry
Choosing the right gumboots for your job or industry is crucial to ensure proper protection and safety. With so many types of gumboots available, it can be overwhelming to know which one is suitable for your specific needs. Whether you work in construction, agriculture, or food processing ensuring you select the right gumboots for your job in a critical as the job itself.
We have created a industry specific safety gumboots guide which details, features you shouldn’t miss including in your safety gumboots as per the industry you operate in.
Food Processing
In the food processing industry, gumboots are essential to maintain a clean and hygienic work environment. Workers are often exposed to slippery floors, wet conditions, and various food-related substances, such as fats and oils. Therefore, gumboots should have slip-resistant soles, steel toes for impact protection, and chemical-resistant materials that are easy to clean and sanitize.
Mining
Mining is a hazardous industry that requires gumboots that can withstand harsh conditions and protect against various hazards, such as falling objects and chemical exposure. Gumboots for mining should have reinforced steel toes and shanks for impact protection, slip-resistant soles for traction, and chemical resistance to protect against hazardous materials.
Construction
Construction workers are often exposed to various hazards, such as falling objects, sharp objects, and uneven surfaces. Gumboots for construction should have steel toes for impact protection, slip-resistant soles for traction, and good ankle support for stability on uneven terrain.
Agriculture
Agriculture workers often work in muddy or wet conditions and are exposed to various hazards, such as animal waste and sharp objects. Gumboots for agriculture should be comfortable, waterproof, and have good traction to prevent slips and falls.
Chemical Manufacturing
Chemical manufacturing involves exposure to various hazardous chemicals that can cause burns and other health problems. Gumboots for chemical manufacturing should be made from chemical-resistant materials, such as neoprene or other synthetic materials, and have slip-resistant soles for traction.
Fishing
Fishing involves exposure to cold water and slippery surfaces. Gumboots for fishing should have good traction and waterproofing, as well as insulation for cold water.
Cleaning Services
Cleaning services workers are often exposed to wet and slippery surfaces and various cleaning chemicals. Gumboots for cleaning services should have slip-resistant soles, easy-to-clean surfaces, and chemical resistance to protect against exposure to cleaning chemicals.
Plumbing
Plumbers often work in wet and slippery conditions and are exposed to various chemicals and sharp objects. Gumboots for plumbing should have steel toes for impact protection, slip-resistant soles for traction, and chemical resistance to protect against exposure to hazardous materials.
Oil and Gas
Oil and gas workers are often exposed to various hazardous chemicals and conditions, such as extreme temperatures and slippery surfaces. Gumboots for oil and gas should be made from chemical-resistant materials, have good traction and insulation, and be slip-resistant for added safety.
Healthcare
In healthcare, gumboots are essential to protect against exposure to hazardous substances, such as blood and other bodily fluids. Gumboots for healthcare should have slip-resistant soles, chemical resistance, and anti-static properties to prevent the buildup of static electricity.
Choosing the right gumboots for your specific industry and application is essential to protect you at your workplace, and look for gumboots that have the appropriate features, such as slip-resistant soles, steel toes, chemical resistance, and insulation.At Moglix you have access to the widest range of industry and application specific safety gumboots from from best in class brands all in one place. Check our range
Gumboot Guide
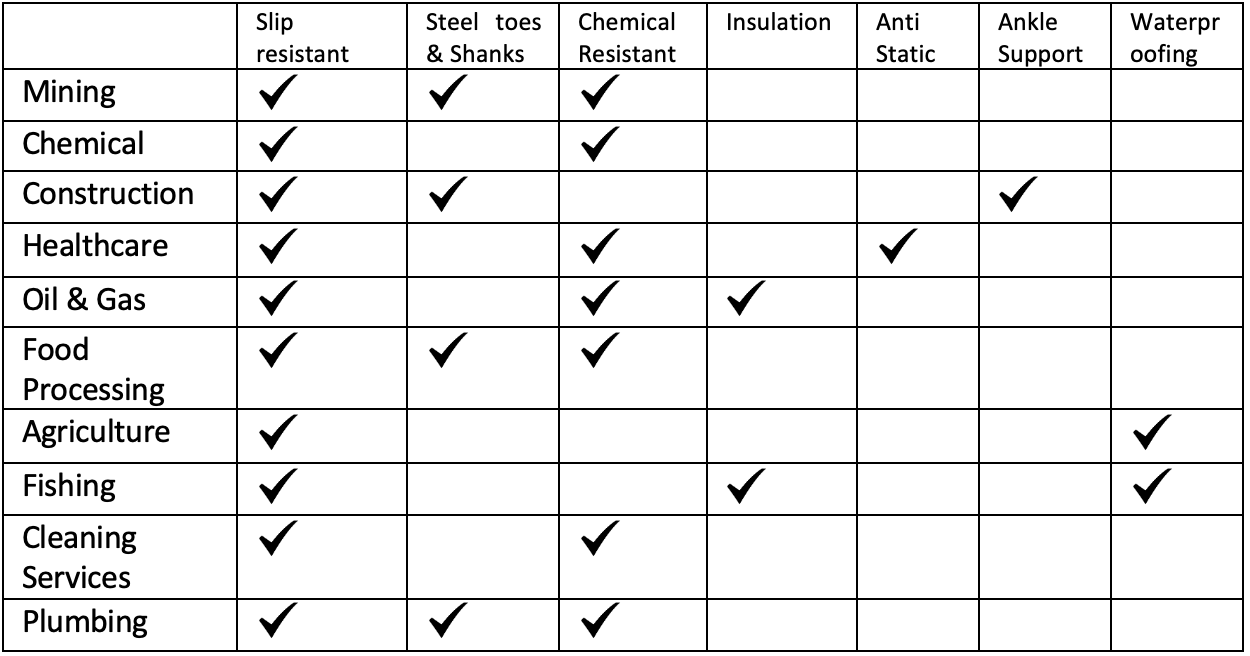
Please Note: This guide is an indicative guide, eventually gumboot material, features and application will depend on your eventual use
Evolution of Safety Gumboots in Workplace Safety: A Comprehensive Guide
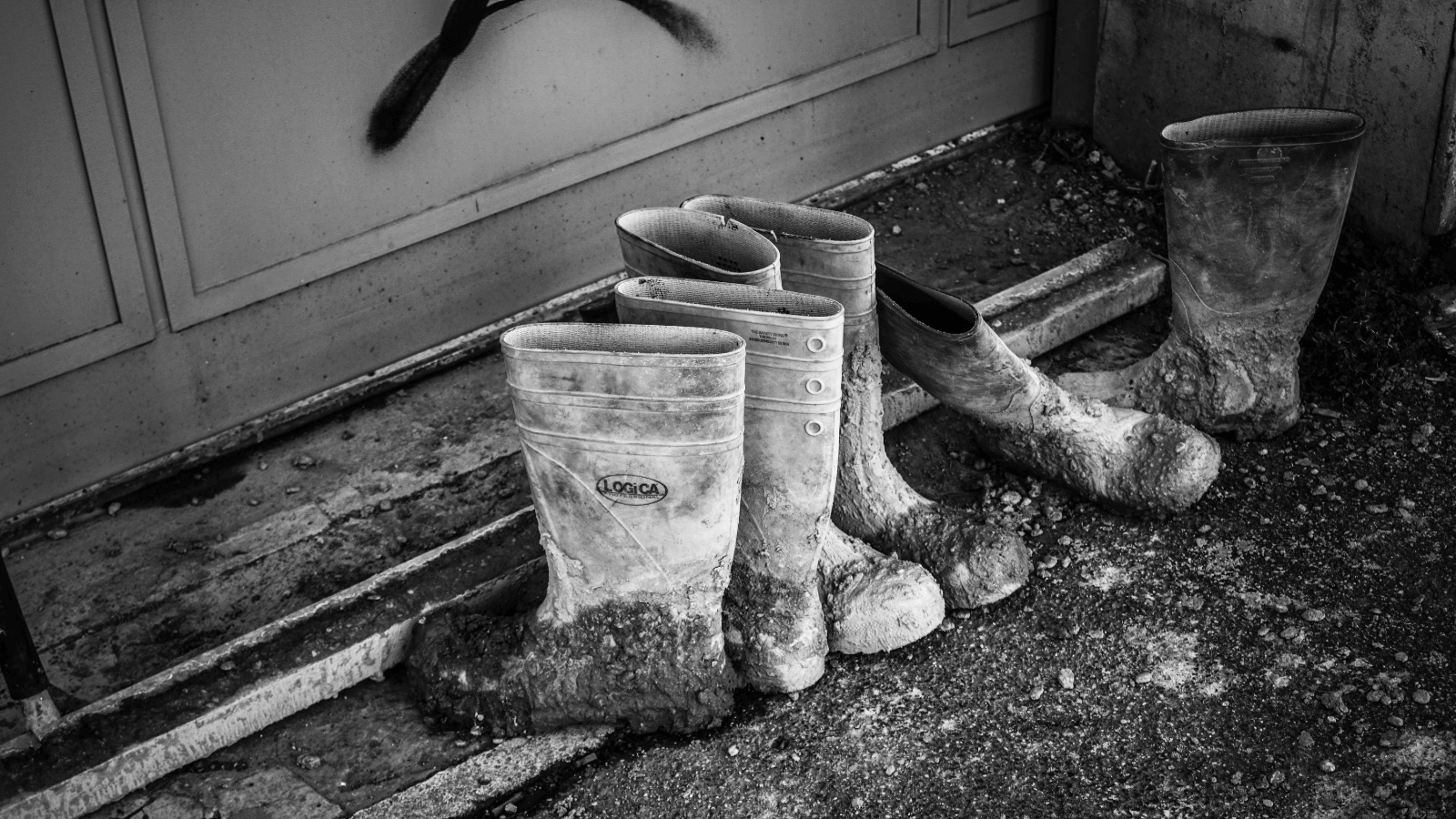
Evolution of Safety Gumboots in Workplace Safety: A Comprehensive Guide
Also known as wellies, rubber boots, rain boots, muck boots and many more depending upon the country you are in, Gumboots have been around since the early 19th century. Originally designed for farmers to protect their feet from mud and water, gumboots have evolved over time to become an essential part of personal protective equipment (PPE) in various industries.
Origins of the Gumboots
Gumboots were first invented in Europe for farmers working in wet and muddy conditions. The first gumboots were made of leather, but this material was heavy and didn’t provide adequate protection against water. In the mid-19th century, Charles Goodyear invented vulcanized rubber, which revolutionized the gumboot industry. Rubber gumboots were much lighter and more durable than leather gumboots, and they quickly became popular among farmers and other outdoor workers.
Industrial Revolution
During the Industrial Revolution, gumboots became popular in factories, mines, and other industrial workplaces. Workers needed footwear that could protect their feet from falling objects, chemicals, and other hazards. Rubber gumboots were a perfect fit for these requirements, and they quickly became an essential part of PPE in various industries.
Rubber Technology
The invention of vulcanized rubber paved the way for various innovations in gumboot design and manufacturing. Rubber gumboots could now be produced in different sizes, shapes, and colors. They also became more comfortable to wear, thanks to the development of rubber cushioning and insoles.
World War I and II
During World War I and II, gumboots became crucial for soldiers in the trenches. They protected soldiers’ feet from wet and muddy conditions, as well as from diseases like trench foot. The demand for gumboots during these wars led to significant innovations in gumboot design and manufacturing. For instance, manufacturers started using lighter and more flexible materials to make gumboots that were more comfortable to wear for long periods.
Modern Safety Standards
In the 20th century, safety gumboots became subject to strict safety standards and regulations. These standards were developed to ensure that gumboots provided adequate protection against various hazards in the workplace. Today, safety gumboots are tested for slip resistance, impact resistance, and other safety features before they can be sold to the public. According to a report by Zion Market Research, the global safety footwear market was valued at $6.8 billion in 2020 and is expected to reach $9.8 billion by 2028, growing at a CAGR of 4.8% during the forecast period.
Materials Innovation
In recent years, materials such as neoprene, PVC, and polyurethane have been used in the production of safety gumboots. These materials offer superior resistance to chemicals, oils, and other hazards, making them ideal for use in industries like construction, mining, and agriculture. According to a report by Allied Market Research, the global safety footwear market is expected to witness significant growth due to the increasing demand for lightweight, comfortable, and durable safety footwear.
Global Industry
Today, safety gumboots are produced and used all over the world. Different cultures and industries have influenced the design and development of safety gumboots in different parts of the world. For instance, gumboots used in the agriculture industry in India are designed to be comfortable and breathable, while those used in the mining industry in South Africa are designed to be durable and slip-resistant.
Road ahead
We can expect to see continued innovation in the design and materials used to make gumboots. One promising trend is the growing use of sustainable and eco-friendly materials, which can reduce the environmental impact of these essential safety tools. At the same time, advances in 3D printing technology could allow for greater customization and personalization of gumboots, improving their fit and comfort.
The evolution of gumboots reflects a broader trend in workplace safety, which is a growing recognition of the importance of protecting workers from hazards and providing them with the tools they need to do their jobs safely and effectively. As technology and materials continue to advance, we can expect gumboots to remain a critical part of workplace safety for many years to come. At Moglix you have access to the widest range of industry and application specific safety gumboots from from best in class brands all in one place. Check our range
Overheating of Switchgear Components and How to Mitigate It
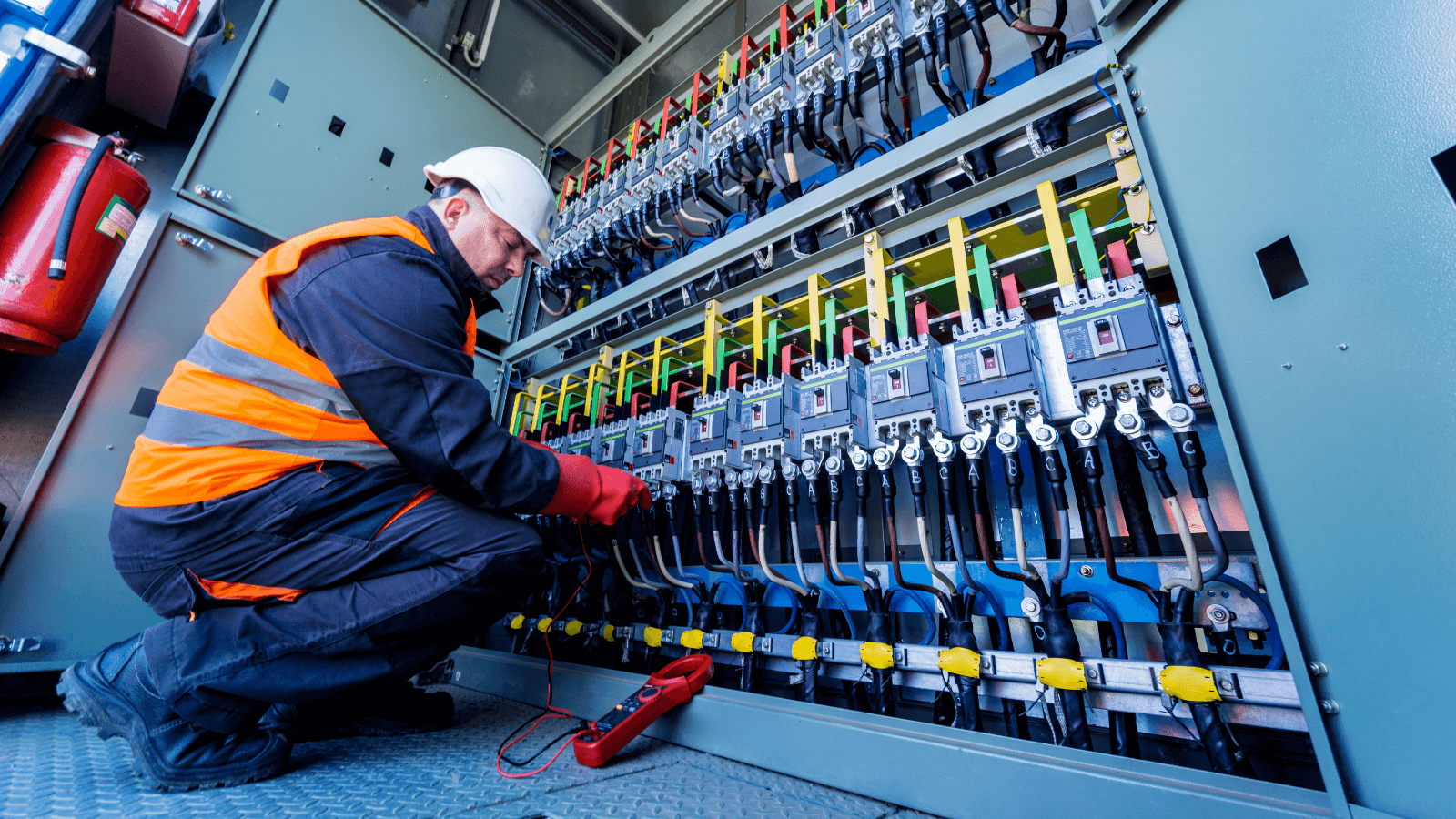
Overheating of Switchgear Components and How to Mitigate It
Switchgear components are essential for the safe and reliable operation of power distribution systems. However, like any electrical equipment, they can be susceptible to overheating. This not only leads to equipment failure and downtime but also poses safety hazards. Therefore, it’s crucial to maintain proper temperature control for switchgear components. Lets understand common causes of switchgear overheating and some practical tips and advanced solutions for mitigating it.
Common Causes of Switchgear Overheating
Overheating of switchgear components can occur due to various reasons, including:
Overloaded circuits: When the electrical load on a switchgear component exceeds its rated capacity, it generates excess heat, leading to overheating.
Poor ventilation: Switchgear components require adequate ventilation to dissipate the heat they generate. Poor ventilation can cause the heat to build up, resulting in overheating.
High ambient temperatures: When the ambient temperature exceeds the switchgear component’s rated temperature, it can lead to overheating.
Inadequate maintenance: Dirty and corroded contacts, worn-out insulation, and loose connections can all cause increased resistance and heat generation, leading to overheating.
Best Practices for Mitigating Switchgear Overheating
To mitigate switchgear overheating, the following best practices should be followed:
Regular inspection and maintenance: Switchgear components should be inspected and maintained regularly to detect any signs of overheating early on.
Proper ventilation: Adequate ventilation is crucial to dissipate the heat generated by switchgear components. The ventilation system should be designed and installed to meet the switchgear manufacturer’s recommendations.
Thermal imaging: Thermal imaging can be used to detect hot spots in switchgear components, enabling early detection and mitigation of overheating.
Load management: Electrical loads should be managed to ensure that they don’t exceed the switchgear component’s rated capacity.
Advanced Solutions for Switchgear Temperature Control
In addition to the best practices mentioned above, the following advanced solutions can be used for switchgear temperature control:
Active cooling systems: Active cooling systems, such as air conditioning and liquid cooling, can be used to cool switchgear components and maintain their temperature within the rated range.
Intelligent temperature monitoring: Intelligent temperature monitoring systems can be used to continuously monitor switchgear components’ temperature and adjust the cooling system as required.
Automated load shedding: Automated load shedding systems can be used to shed excess electrical loads automatically, preventing switchgear components from overheating.
Use Cases
To illustrate the practical applications of the solutions discussed above, let’s look at a few use cases:
- A switchgear component at a manufacturing plant was consistently overheating due to high ambient temperatures. To mitigate this, the plant installed an active cooling system that maintained the component’s temperature within the rated range.
- A thermal imaging survey detected hot spots in a switchgear component at a data center. The hot spots were caused by overloaded circuits. To prevent overheating, the data center implemented load shedding, shedding excess loads automatically to keep the switchgear component within its rated capacity.
Moving Forward
As technology advances, new solutions and innovations for switchgear temperature control are emerging. These include:
Advanced sensors: Advanced sensors can provide more accurate temperature readings, enabling better temperature control and more efficient cooling.
Artificial intelligence: Artificial intelligence can be used to predict when switchgear components are likely to overheat, enabling proactive mitigation.
Renewable energy sources: As more renewable energy sources, such as solar and wind, are integrated into power distribution systems, switchgear temperature control will become even more critical to ensure safe and reliable operation.
Overheating of switchgear components can lead to equipment failure, downtime, and safety hazards. Hence it’s important to identify the common causes of overheating and implement best practices. For all your switchgear supplies you can get in touch with us. Moglix, has the most comprehensive range of switchgear supplies and our pan india network of partners and warehouses ensure no place is remote for us to reach. Know more.
How to Prevent Workplace Electrical Fires: Root Causes and Actionable Strategies
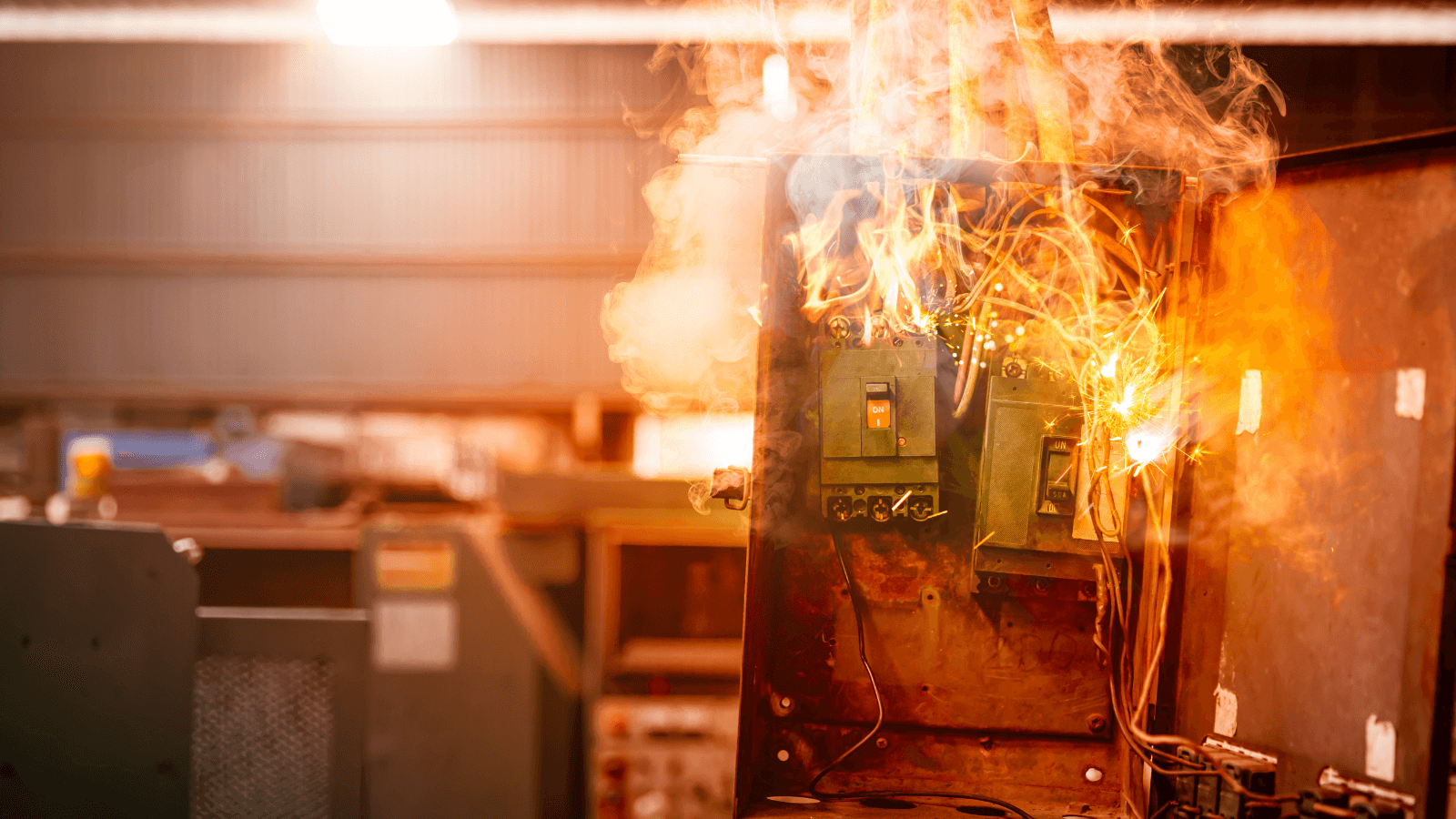
How to Prevent Workplace Electrical Fires: Root Causes and Actionable Strategies
Electrical fires are a common and devastating occurrence in the workplace. A study by the National Crime Records Bureau reveals that workplace electrical fires claimed the lives of 1,808 individuals in 2021 alone, equating to nearly five fatalities per day. However, as with many catastrophic events, the true cost extends beyond mere figures. Lives are forever changed, families grapple with loss, and businesses may never fully recover.
Understanding the causes of workplace electrical hazards and taking proactive measures to mitigate the risks can make all the difference. This blog delves into the causes and costs of workplace electrical fires and explores actionable strategies for businesses to prioritize workplace safety.
Connecting the Dots: Causes of Workplace Electrical Fires
Workplace electrical fires are often caused by faulty electrical equipment, poor electrical installation, improper grounding, overhead power lines, and misuse of electrical equipment. These factors can lead to electrical arcing, igniting nearby flammable materials, and causing a fire. Other common causes of workplace electrical hazards include overloaded circuits, exposed electrical wiring, and improper use of extension cords.
Fanning the Flames: How Workplace Electrical Fires Impact the Bottom Line
The financial cost of workplace electrical fires can be substantial. Beyond the apparent property damage, businesses may also experience a domino effect of losses, from decreased productivity and business interruption to increased insurance premiums. The cost of fire damage restoration and replacement of damaged equipment can quickly add up, and some businesses may not be able to recover from the financial impact of an electrical fire.
Recent studies show that workplace fires account for a staggering USD 328 billion in annual costs in the US alone, with 22% of these fires resulting from electrical sources. With such high stakes, companies must engage in business continuity planning to safeguard their financial health and long-term viability.
Shock-Proof Your Business: Best Practices for Preventing Workplace Electrical Fires
Businesses must prioritize electrical safety to mitigate the risk of workplace electrical fires. This can be achieved by implementing proper electrical installation and maintenance procedures, employee training programs, and regular equipment inspections. Here are some steps that businesses can take to minimize the risk of workplace electrical fires:
Conduct regular electrical safety inspections: Regular inspections of electrical equipment and wiring can help identify potential hazards before they result in a fire and enable electric fire prevention.
Develop an electrical safety program: A comprehensive electrical safety program can provide employees with the knowledge and tools they need to use electrical equipment safely.
Provide regular training: Ongoing training can help employees stay informed about the latest electrical safety practices and guidelines.
Invest in Quality electrical supplies – Invest in high quality electrical supplies like switchgears, wires and cables etc. Best would be to source it from a one stop solution provider like Moglix so that you have access the comprehensive product range from bets in class brands
Ensure proper installation and maintenance: Proper installation and maintenance of electrical equipment can help prevent electrical fires caused limited product understanding. Moglix has on roll electrical experts that can guide through procurement, installation and maintenance cycles.
Promote a culture of workplace safety: Encourage employees to prioritize safety and report any potential hazards immediately.
OSHA Compliance: Ensuring compliance with Occupational Safety and Health Administration standards can also help in fire risk management.
Wiring a Safer Future
Mitigating the risks of workplace electrical fires requires a comprehensive approach that prioritizes electrical safety through regular inspections, employee safety training, and proper equipment installation and maintenance. By taking these steps, businesses can create a safer work environment for their employees and minimize the risks and costs associated with electrical hazards. At Moglix, we are committed to the cause of employee safety in the workplace. Contact us today to explore supplies and solutions that keep your workplace safe from fire related accidents
Why We Need to Rethink PPE for Women in Industry?
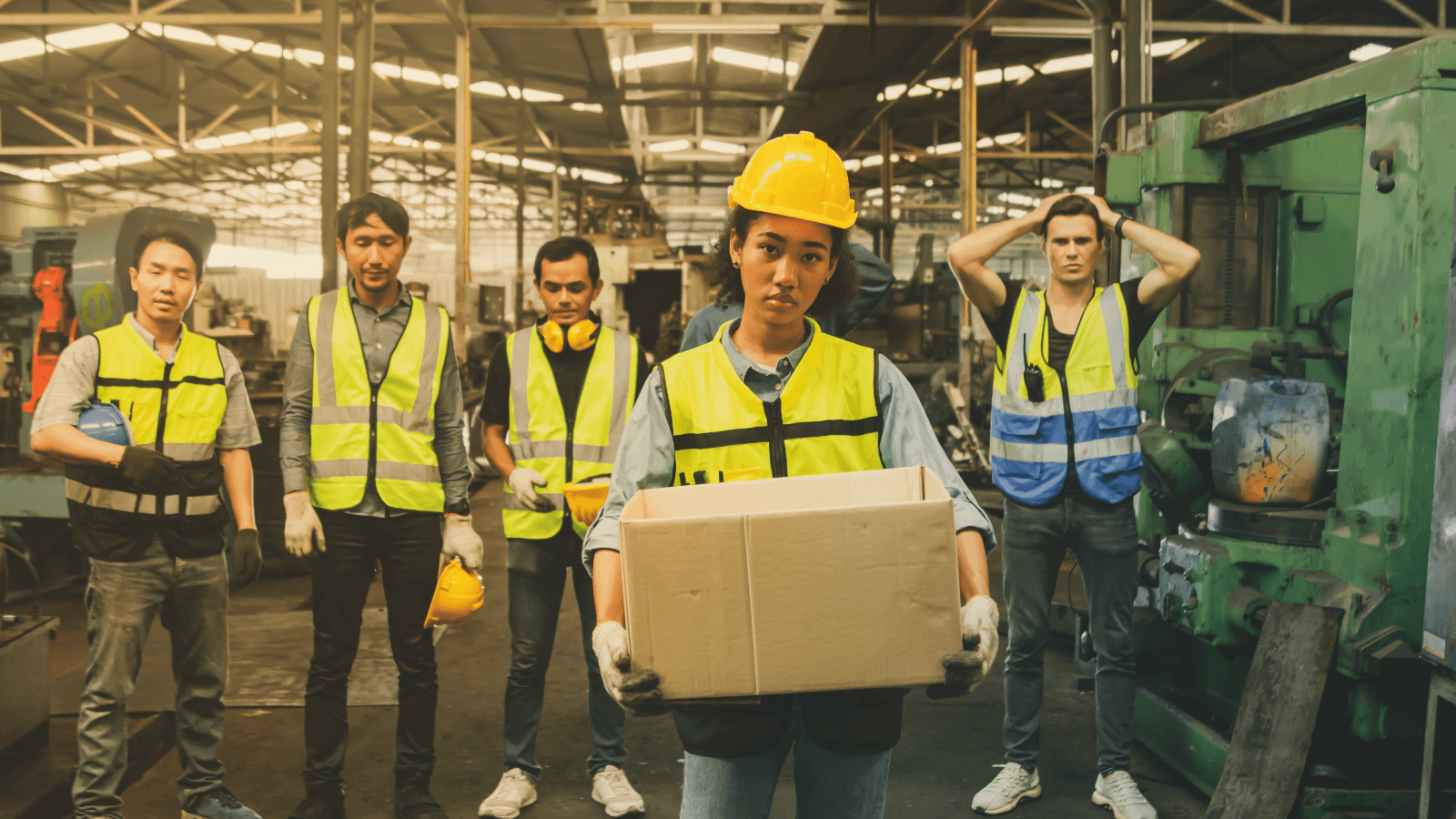
Why We Need to Rethink PPE for Women in Industry?
When we think of personal protective equipment (PPE) in the industrial sector, we will likely picture a bulky suit and helmet on a male worker. However, this image fails to acknowledge the millions of women working in industries that require PPE. Women face unique challenges in the workplace, including ill-fitting PPE and inadequate safety gear, which can expose them to dangerous working conditions.
Despite the pressing need for gender-specific PPE, a recent Women in Global Health study(1) reveals that about three-quarters of the women surveyed experienced problems with PPE fit, and a mere 14% reported using exclusively fit-tested PPE. This alarming finding is a cause for concern as poorly fitting PPE can lead to reduced productivity, injuries, and in severe cases, fatalities. The fact that women face such challenges in obtaining appropriate PPE should be treated as a critical issue that requires our immediate attention to ensure women’s safety at manufacturing facilities.
One Size Does Not Fit All: The Gender Gap in PPE Procurement
The lack of awareness within some organizations of women’s unique PPE needs and female-friendly safety equipment is a primary challenge women face. The all too common “one size fits all” strategy is often employed in PPE procurement, leading to employers neglecting the purchase of PPE designed for women and displaying indifference towards their safety.
Additionally, the male-dominated construction industry culture presents another significant barrier to women’s access to adequately fitting PPE. Women are frequently expected to make do with PPE designed for men, modify their gear, or purchase their PPE outright. This culture of indifference must be challenged, and solutions must be sought to provide female worker safety in the manufacturing sector.
Procuring for Diversity: The Importance of Gender-Specific PPE
The importance of addressing PPE challenges for women cannot be overstated. In many industries, women are exposed to the same risks as men, including exposure to chemicals, heat, and electrical hazards. Without adequate protection, women are at risk of injury or even death. To be effective, the safety-oriented design and production of PPE must cater to the distinct requirements of every gender.
In addition to the moral imperative of ensuring women’s safety, there are practical reasons to address PPE challenges for women. When workers feel safe and protected, they are more likely to be productive and engaged in their work, leading to a more positive and efficient work environment.
Empowering Women with Innovative PPE Solutions: Join the Revolution
Unfortunately, many women still face unique challenges regarding selecting and using PPE in the workplace. To bridge this gap, employers must engage women in the PPE selection process and thoroughly assess their needs.
Thankfully, some manufacturers have recognized the need for gender-specific PPE and are leading the charge toward innovation in this area. Women’s PPE is now being designed to fit the female body shape, with adjustments made for height, waist size, and shoulder width differences. The use of softer materials and more flexible fabrics not only improves comfort and range of motion but also promotes safety.
Moreover, In order increase adoption women’s PPE is now being made more practical and appealing, with various colors, patterns, and form-fitting designs. This is a welcome change as it encourages women to wear their PPE more often, improving safety and reducing the risk of workplace accidents.
At Moglix, you have access to the most comprehensive range of safety supplies and solutions. You can find a range of PPE solutions specifically designed for women at workplace. Contact us today and partner with us to build a safer environment for women.
[Supply Chain Central] Is your business ready for FY23?
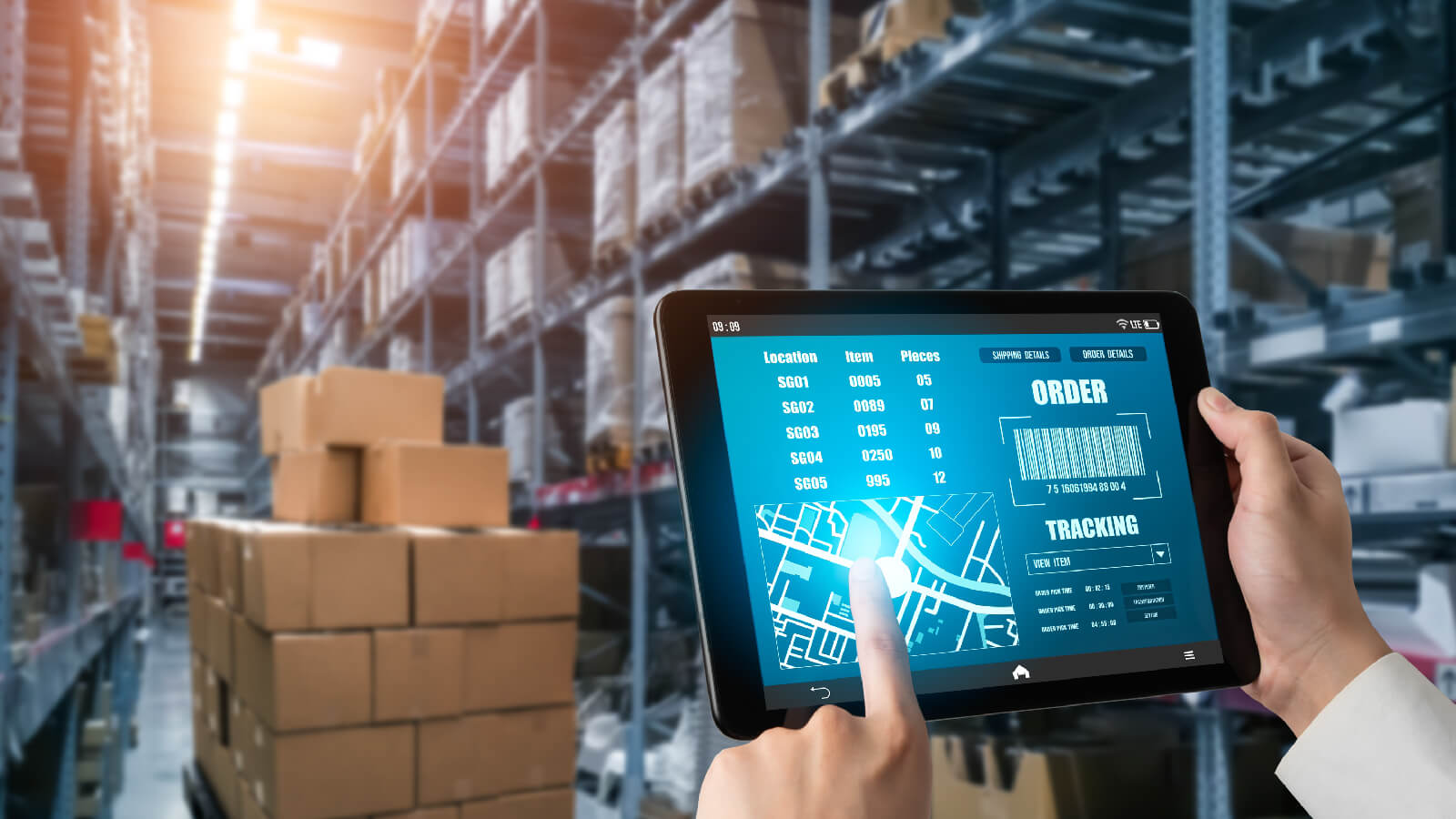
[Supply Chain Central] Is your business ready for FY23?
The year 2023 has arrived, and with it, a new era of supply chain management trends. Businesses must be ready to adapt to these changes to remain competitive in the global market.
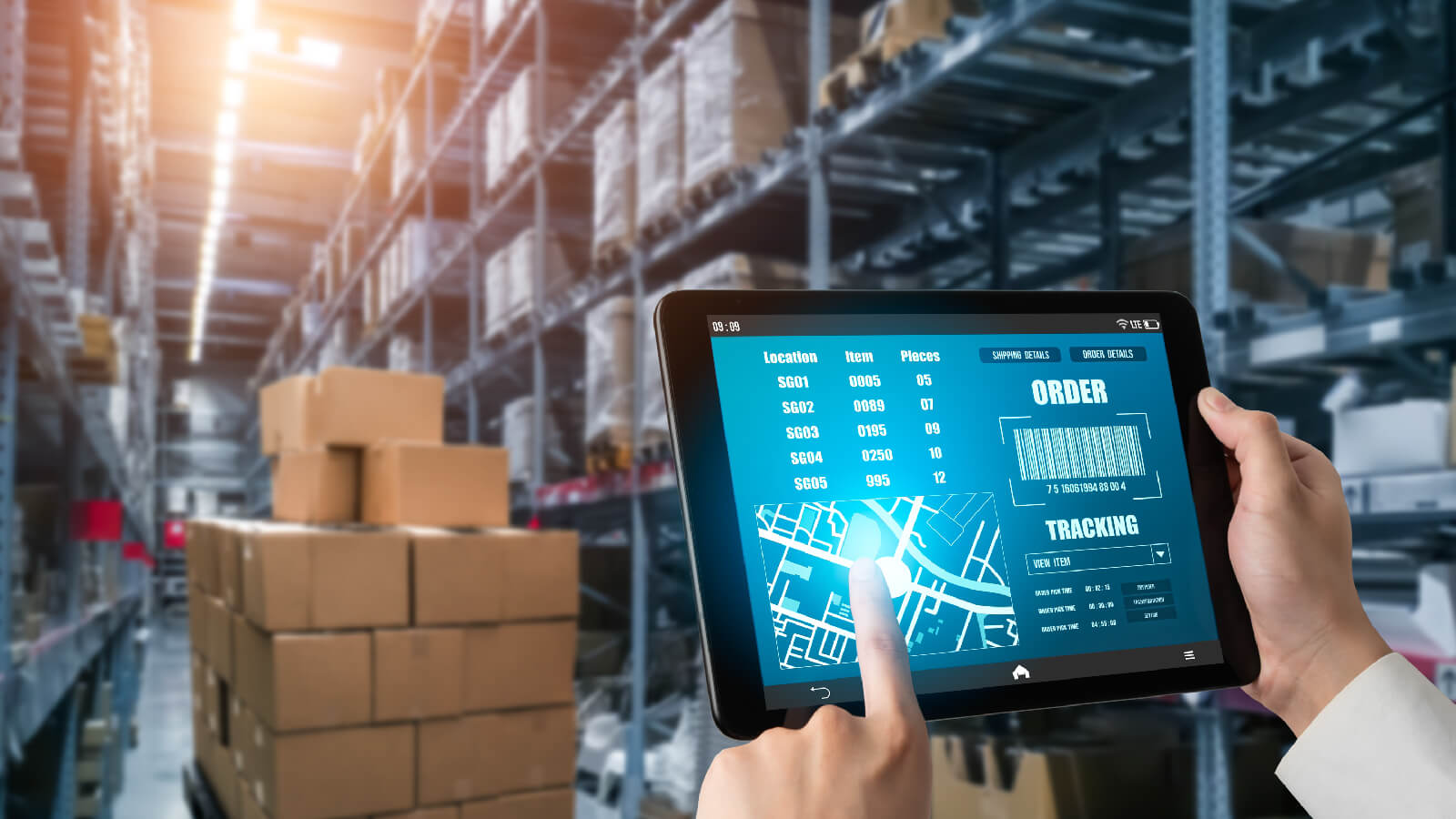
As we continue to recover from the pandemic, the supply chain has become even more critical, and many organizations are investing time and resources in supply chain management to mitigate the disruptions of early 2022.
Notably, a recent McKinsey report highlights that 67%(1) of respondents have adopted digital tools for end-to-end supply chain visibility.
This article discusses some key supply chain management trends to watch for in 2023.
Digital Revolution of Supply Chains: The Future is Now
The shift toward digitization may be the most significant trend in supply chain management in 2023. As the world becomes more connected, companies will embrace digitization on a large scale to stay ahead of the competition.
Digitization of supply chains requires implementing the internet of things (IoT), cloud-based networks, artificial intelligence, and machine learning. These digital tools help businesses to track, monitor and analyze every aspect of the supply chain management process.
By adopting these tools, companies can streamline their supply chains, develop new revenue streams, and tap into new markets.
Green is the New Gold: Prioritizing Sustainable Supply Chains
With the rising global emphasis on environmental sustainability, businesses will prioritize sustainable supply chains. Investors, including private equity firms and venture capitalists, are increasingly opting for sustainable organizations in their portfolios.
Thus, companies will look to demonstrate a commitment to sustainability to gain a competitive edge in funding and attracting investors.
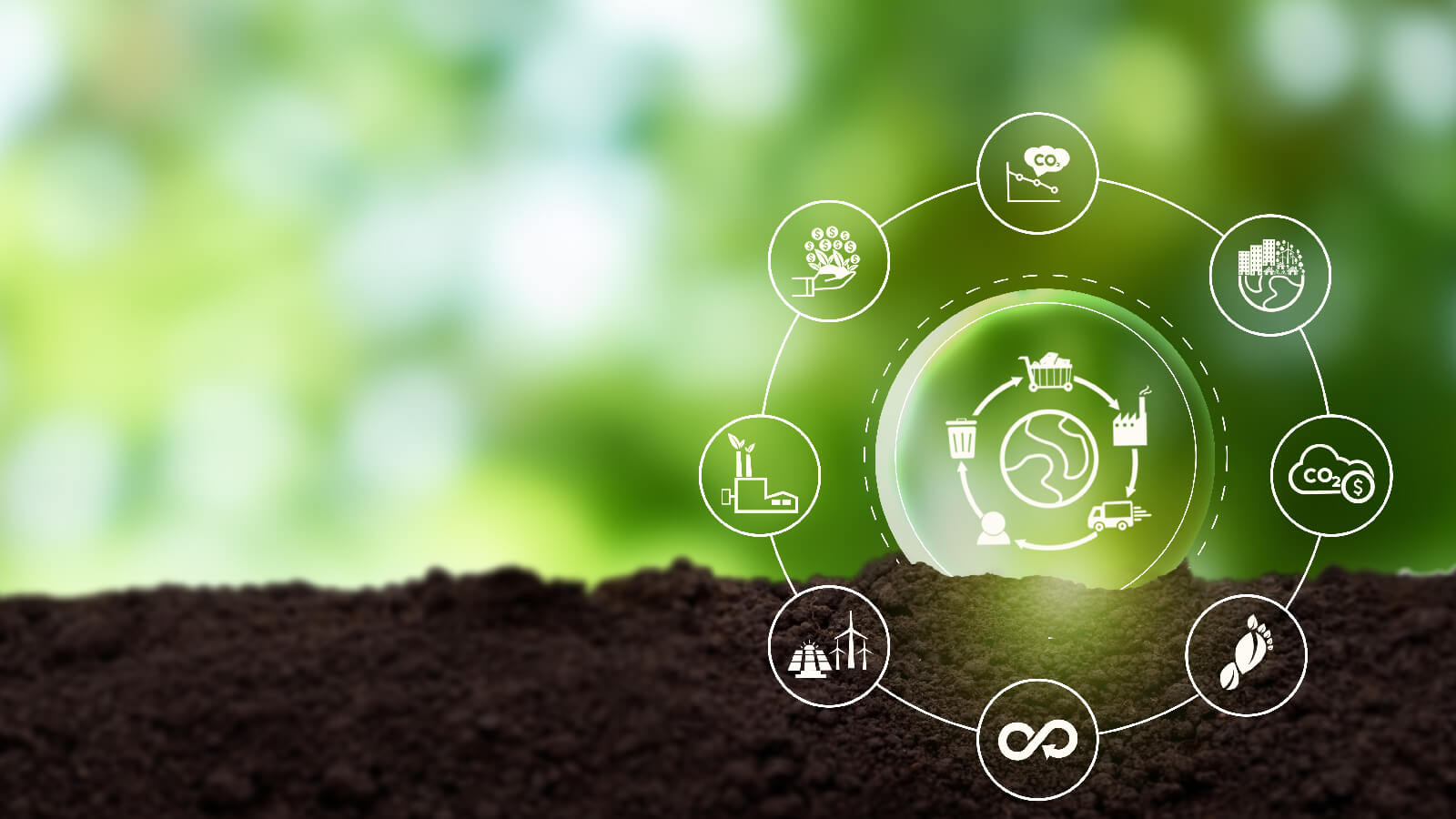
To achieve sustainable supply chain operations, businesses will adopt green logistics practices that are environment-friendly. This can include investing in energy-efficient technologies and utilizing sustainable packaging materials.
Environment, Social, and Governance (ESG) focused procurement decisions will also gain momentum for implementing sustainable supply chain management processes.
Don’t Fall Behind: How Partnerships are Changing the Supply Chain Landscape
Don’t miss out on the opportunity to stay ahead of the competition by harnessing the power of supply chain integrations. The year 2023 is expected to witness a proliferation of supply chain components due to many companies pursuing cost reduction and enhanced customer service.
As a result, companies that fail to integrate with third-party service providers risk falling behind.
In 2023, integration with third-party service providers will become common for reducing overall freight expenses and optimizing the supply chain.
Moreover, companies will seek partnerships with other enterprises that leverage digital solutions to improve delivery estimation accuracy and minimize administrative work. This would further enhance the overall efficiency of supply chain management.
Future-proofing Your Supply Chain: Building Risk and Resilience
In today’s complex and unpredictable business environment, managing supply chain risks and building resilience has become a critical priority for companies. These risks can emerge in various forms, from natural disasters that disrupt the flow of goods to cyber-attacks that jeopardize sensitive data.
To address these risks, companies will embrace an array of strategies including the following:
- Supplier diversification– Companies will adopt strategies to mitigate the risks of overreliance on a single supplier. Supplier diversification will become a key priority as companies seek to avoid the impact of supply chain disruptions.
- Localizing production and transportation– Businesses will seek to reduce the distance between the manufacturing plant and end customers and transport goods through local channels, such as short-haul trucking or rail transport.
- Forging non-traditional partnerships– Companies will seek to expand their network of partners to tap into new sources of innovation, secure access to specialized talent, and access new markets.
A robust supply chain design will be adopted to enable quick recovery from adverse events, provide superior customer service, and increase the market share.
Big Data, Big Benefits: Leveraging Big Data and Analytics
Big data and advanced analytics will power the future of the global supply chain. The ability to collect and analyze vast amounts of data will provide greater visibility, synchronized planning and execution, data-driven decision-making, and profitability.
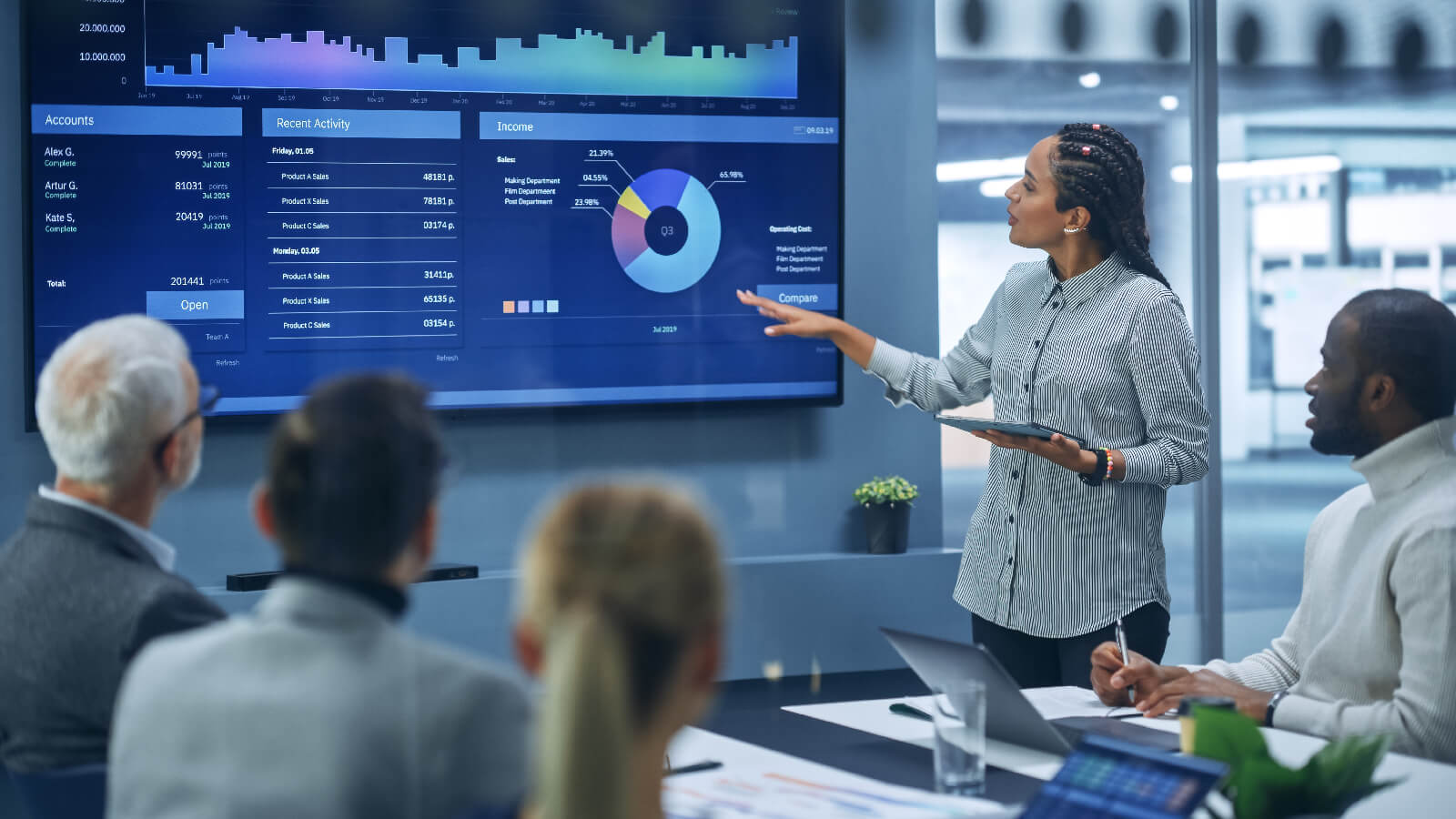
By leveraging these technologies, companies can optimize their supply chains, improve delivery times, and enhance the overall customer experience by identifying patterns and trends. Implementing algorithms and robotics will further drive efficiency and productivity, making big data and analytics the cornerstone of future-proof supply chain operations.
Cybersecurity for the Win: Protecting Your Supply Chain from Modern Threats
As businesses continue to expand their digital footprint, the threat of cybercrime becomes more prevalent. The supply chain, in particular, is increasingly vulnerable to attacks from cybercriminals seeking to gain access to sensitive data.
To safeguard against these threats, companies are adopting a proactive approach to cybersecurity. This includes investing in anti-hacking systems, implementing firewalls, providing employee training, and building stronger relationships with supply chain partners.
Through collaboration and coordinated efforts, businesses are protecting their assets and people from cyber threats, ensuring the resilience of their supply chains.
Reshaping the Map: The Rise of Domestic Self-Sufficiency
Geopolitical tensions have promoted domestic self-sufficiency in material supply and manufacturing.
As nations grow more skeptical of cooperation and interdependence, governments seek to secure the supply chain. They’re exploring domestic production capabilities and ‘friend-shoring’ relationships with like-minded and geographically proximate countries.
This approach provides a more secure supply of goods and mitigates the risk of material unavailability or supply chain disruption due to geopolitical tensions. Thus companies may have to restructure their supply chains in 2023.
Capitalizing on Supply Chain Management Trends 2023
The trends in supply change management in 2023 will transform how businesses operate. At Moglix, we are well-equipped to help companies to navigate these changes, capitalize on opportunities and stay ahead of the curve.
We understand the challenges businesses may face as they seek to adapt to these changes in the supply chain landscape. Contact us to learn more about how we can help your business optimize its supply chain management strategy.