The Ultimate list of Safety Tools for Industrial Workplace
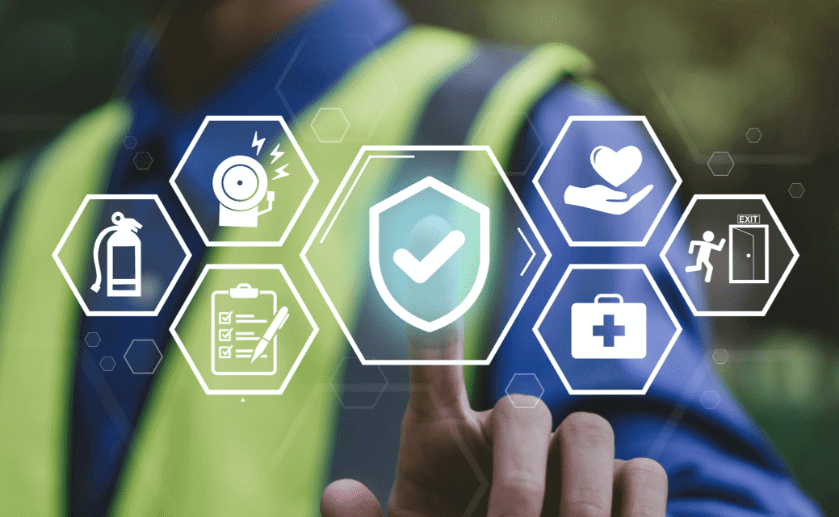
The Ultimate list of Safety Tools for Industrial Workplace
OSHA reports that while 12%–14% of occupational injuries resulting in total disability are brought on by workers not wearing the proper PPE, the correct use of PPE can prevent 37.6% of occupational injuries and diseases. PPE use, for all its importance, can occasionally cause discomfort because of problems with movement, visibility, breathability, or sweating—all of which require careful thought to guarantee compliance and efficacy.
With an emphasis on those used in industrial environments, this blog seeks to define what safety tools and equipment actually are. Safety tools and equipment are a wide category of equipment made to shield you from different risks. Among these are, but are not restricted to, gloves, eye protection, helmets, highly visible clothing, and respiratory protection. Every item is designed to reduce particular hazards connected to working conditions, so guaranteeing your health and safety in a variety of settings.
Industrial safety equipment refers to the specific instruments and equipment used in production and manufacturing settings to control risks and avoid accidents. This group includes, beyond personal equipment, fire extinguishers, safety signs, emergency stop buttons, and spill or hazardous material containment systems.
You will have a better idea of the top safety equipment that every industrial workplace should have and how to outfit your settings to improve safety and meet legal requirements. This information encourages not only a safer workplace but also a safety-first culture in all sectors.
Hard Hats
Safety officers frequently prioritize hard hats as a critical personal protective equipment (PPE) item in industrial environments. The reason for this prioritization is the critical function that hard hats fulfill in safeguarding employees’ heads against potential harm caused by electrical shocks or falling objects. The diverse range of hazards present in such settings renders hard hats an essential instrument of protection due to their comprehensive nature.
Safety officers highly recommend Hard hats due to their substantial capacity to mitigate the likelihood of severe injuries in hazardous environments, including construction sites, areas where workers may encounter falling debris, and vicinity to overhead hazards such as exposed shelves or energized conductors. Specialized designs, such as hard hats with light attachments for miners, reflective stripes for night work, face shields for welders, and earmuff attachments for hearing protection, are available to meet the specific requirements of various work environments. Every individual feature has been meticulously crafted to tackle specific safety concerns, thereby guaranteeing comprehensive protection for the wearer.
Adherence to the ANSI Z89.1 standard is an absolute requirement for hard hats. It ensures the presence of a resilient suspension system capable of effectively dampening and dissipating impacts while preserving a secure distance between the head and the hat shell.
Types
- Type 1 helmets: Top impact protection.
- Type 2 helmets: Top and side impact protection.
Classes of Hard Hats
- Class E: Non-conductive, protects against high-voltage shocks up to 20,000 volts.
- Class G: General use, limited voltage protection up to 2,200 volts.
- Class C: Offers comfort and impact protection but no electrical resistance.
Maintain hard hats by cleaning them with hot water and detergent, and regularly check for damage. Adjust the straps for a secure fit and add liners or sweatbands for comfort.
Also Read: Things to Consider While Choosing Safety Helmets
First Aid Kit
Around half of the employees have admitted that their companies did not provide them with a first aid kit. For this reason, the first aid kit is frequently praised as the best option among industrial safety equipment. This preference mostly results from compliance, according to ANSI/ISEA Z308.1-2021 standards.
A first aid kit usually includes bandages, gauze pads, and resuscitation supplies. These supplies are essential for meeting urgent medical needs during work-related accidents or unexpected illnesses.
A first aid kit also shows that you are prepared and follow the law. The uniform components of this kit show a dedication to following safety procedures and the health and safety of employees.
Fire Extinguishers
Fire extinguishers are essential industrial safety equipment for early fire suppression. They enable employees to extinguish fires before they grow larger and more dangerous. Fire extinguishers are readily available in factories. It reduces the risks of injury (major burns), fatality, and property destruction.
Furthermore, they assist in ensuring compliance with workplace safety regulations. There are different types of fires. Each needs a different kind of extinguisher. OSHA and NFPA say:
- Class A: For wood, paper, and cloth fires.
- Class B: For liquids and gases that can burn.
- Class C: For electrical fires.
- Class D: For metals that can catch fire.
- Class K: For fires from cooking oils and fats.
If a workplace doesn’t follow these rules, it can be fined—and the fines can be very high. It can also face criminal charges.
Safety officers prioritize emergency preparedness, recognizing extinguishers’ pivotal role in risk management. Advancements in fire protection equipment, addressing risks like lithium-ion battery fires, demand vigilance in compliance. Updated guidelines ensure optimal fire safety coverage in small premises, emphasizing spatial considerations and risk profiles. Safety officers, informed by evolving regulations, play a crucial role in protecting lives and property from the persistent threat of fire.
Safety Signage
Industrial safety signs communicate vital information to prevent injuries and manage risks. These signs usually display maintenance, operating, and safety instructions. They may include detailed instructions for shutting down equipment, basic operating procedures, or chemical exposure warnings. These signs are often required to protect workers and help companies avoid liability.
Industrial safety signs help prevent injuries and comply with safety regulations. Emergency signs guide people to exits and locate emergency equipment.
Danger, warning, and caution signs indicate different levels of industrial safety hazards. Other types include biological hazards, notices, and general safety signs. Luminescent materials can improve sign visibility.
Regulations from OSHA, ANSI, and military standards dictate the specifics of safety signage, including colour codes, symbols, and placement. Compliance with these standards ensures that signs are effective and protective.
Given the critical role that industrial safety signs and equipment play in maintaining safety and compliance in the workplace, it is advisable for companies to continuously evaluate and update their safety protocols. Learning from OSHA’s insights on the significant reduction in occupational injuries through proper use of Personal Protective Equipment (PPE), industries should focus on not only providing the necessary equipment but also ensuring it is comfortable and practical for continuous use.
For industries looking to enhance their safety measures, consulting with experts such as those at Moglix can be a strategic move. Moglix, with its expertise in industrial products, can offer guidance on the latest safety tools and equipment that meet current regulations and standards. By collaborating with safety experts, companies can ensure they select the most effective equipment and signage, tailored to their specific operational needs.
From Manual to Magical: The P2P Automation Guide
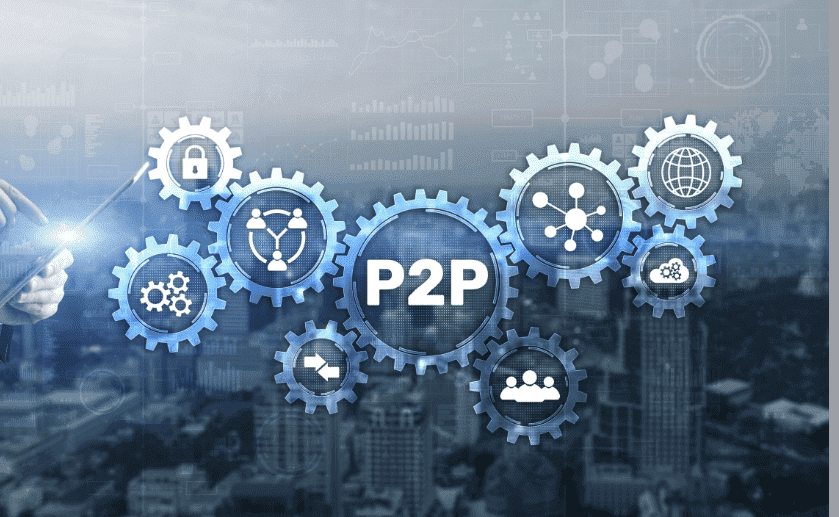
From Manual to Magical: The P2P Automation Guide
Do you know that 80% of organisations still use manual tools to manage their P2P cycle? That said, most procurement leaders will try to automate procurement in the future.
Usually, organisations integrate their P2P (procure-to-pay) process with their ERP or accounting software. However, this is not beneficial in the long run.
Let’s see how automation can easily help overcome most P2P process challenges.
Challenges With the Manual P2P Process
The traditional P2P processes often rely on manual tasks and paper-based systems. That’s why the manual process is prone to several inefficiencies, such as:
- Slow Workflows
Manually processing requisition approval or generating purchase orders takes a lot of time. Additionally, manually processing invoices or payment authorisation calls for slow procurement processing.
- Errors in Data Entry
Manual procurement involves manual data entry across multiple systems. Imagine filling out a paper for requisition and getting it routed for approvals through various desks. That increases the chances of human errors. These error rates can range up to 5% and may eventually lead to process delays and discrepancies.
- Lack of Visibility
A centralised system makes tracking order progress, approvals, and payments across the supply chain easier. Companies face process delays in the entire supply chainHowever if not managed properly, companies can avoid process delays throughout the supply chain if managed properly. However, if managed properly, companies can avoid process delays throughout the supply chain.
- Limited Control and Compliance
If a procure-to-pay process takes a manual route, companies can no longer track their spending limits or compliance with company policies. For instance, without automated controls, the management may hardly track department spending or prevent maverick buying.
Also Read: How Does P2P Automation Surpass Traditional Barriers?
P2P Automation: How to Transform the Procurement Cycle?
An ideal P2P automation software automates the entire procure-to-pay cycle. The software carries out many repetitive tasks to save manual time.
In this regard, let’s look at some USPs of an ideal procure-to-pay software.
- Automated Requisitions and Approvals
Your employees can electronically submit requisitions, specify details, and request approvals through predefined workflows. The automation frees your management from tedious paperwork and speeds up approval.
- Streamlined Purchase Order Generation:
Once approved, requisitions automatically convert into purchase orders. Since no manual data entry is involved, you can rest assured of high order accuracy.
- Efficient Invoice Processing:
P2P software can automatically analyse invoice information and match it with purchase orders and receipts to flag discrepancies.
- Improved Payment Processing:
Thanks to the automated workflows, all invoices are processed promptly for approval and payments as per the pre-defined payment terms.
Also Read: Streamlining Procurement: The Power of P2P Automation
Benefits of P2P Automation
Correctly implementing P2P automation offers numerous advantages, such as:
- Reduced costs
Automation takes care of many manual procurements and payment tasks, saving you on manual labour costs. It also minimises errors, leading to cost savings from duplicate orders or incorrect payments.
- Improved Accuracy
Automated data entry eliminates human errors and ensures consistency throughout the P2P process.
- Increased Compliance
P2P software sets pre-defined rules and approval workflows so that the process, by default, adheres to company policies and regulations.
Also Read: P2P Automation: The Backbone of Resilient Businesses
How to Implement P2P Automation?
Under the right strategy, P2P automation is a high-return investment. Here is how you should get started.
- Analyse your current P2P process:
Identify which areas of your P2P process need improvement, and learn the challenges posing delays or inefficiencies.
- State Automating Goals
Determine what you aim to achieve with P2P automation, such as faster approvals, improved data accuracy, or better spend visibility.
- Evaluate P2P Software Solutions
Research and compare P2P software options to find one that fits your needs and budget.
- Develop a Phased Implementation Plan
Now, you are all set to automate key areas of the P2P process. Start slow and gradually scale up as your team becomes comfortable with the new systems.
Automating the P2P process helps you reduce processing costs, minimizes human errors, improves data accuracy, and enables you to adhere to company policies and regulations. However, you need to carry out the automation with the help of an expert to save yourself from costly mistakes and redos.
Are you seeking a robust P2P automation solution to increase procurement efficiency?
Partner with Moglix Business! Visit our website for advanced P2P automation solutions.
Future Proofing Supply chains: 3 most impactful sustainability trends
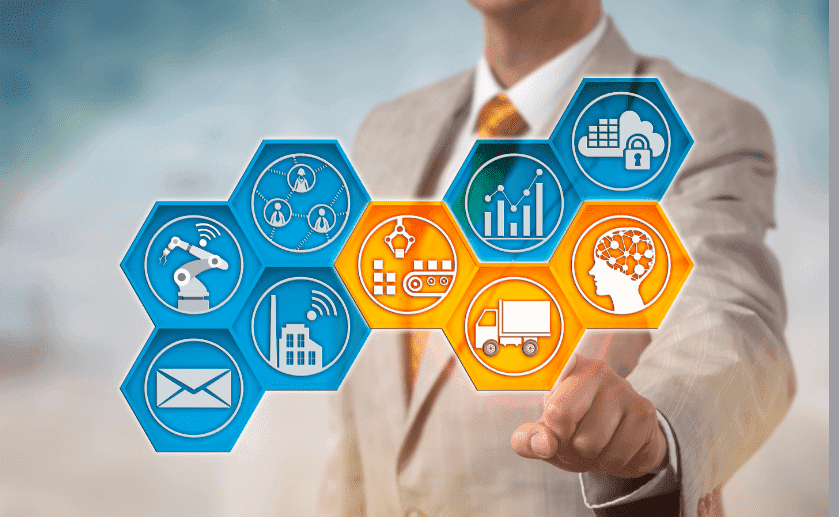
Future Proofing Supply chains: 3 most impactful sustainability trends
Introduction
With sustainability at its heart, supply chain operations management has a greater influence than ever in the quickly changing global commerce scene. The recently passed EU Supply Chain Law best shows significant legislative changes pushing businesses toward more sustainable practices. This directive challenges businesses, but it also offers a chance to reimagine their environmental impact by affecting everything from procurement to logistics.
The results from Earth Day 2024 also throw light on the real difficulties and expenses logistics professionals encounter when trying to improve supply chain sustainability. With supply chain activities accounting for almost 80% of a company’s emissions, this knowledge is essential for businesses trying to lessen their environmental impact.
Leaders must be aware of and able to adjust to these sustainability trends in supply chain operations management as industries develop. In a world of limited resources, this guarantees long-term viability and competitive advantage and encourages adherence to new laws.
This blog will talk about new ideas and actions that are meant to help the environment and encourage people to be responsible.
GenAI in Supply Chain: Leading the Charge in 2024 Trends
Did you know that 72% of businesses intend to spend more money incorporating generative artificial intelligence into their daily operations? Application of this cutting-edge technology has several benefits, especially in the supply chain operations industry. One of the main trends for 2024 will be covered in this part: demand forecasting.
The start of the COVID-19 pandemic brought to light how urgently agile demand forecasting is needed because consumer spending shifted dramatically from services to goods, creating very unpredictable supply chain dynamics. These days, companies are using generative AI models to better predict and to adjust to such shifts in demand?
By simulating possible supply-and-demand situations, these models examine past sales data, market trends, and a host of other variables, greatly improving forecast accuracy. Through monitoring these demand trends, businesses can reduce interruptions and avoid inventory problems, guaranteeing a more dependable and seamless supply chain.
The Rise of AI-Enabled Low and No-Touch Planning
As we look towards 2024, a significant trend emerging in the supply chain operations sector is the shift towards low and no-touch planning processes enabled by AI technology.
Low-touch planning increases revenue, cost, and asset gross margins by 1 to 3 percent and enhances predictability, increasing Return on Equity (ROE) by 2 to 4 percentage points.
Low-touch planning leverages AI-powered applications to automate complex aspects of both sales and operational planning as well as integrated business planning. Through the use of sophisticated analytics to handle complicated problems with little human involvement, this approach greatly reduces the manual labour required in the end-to-end planning process.
AI shines in big, unstructured dataset analysis, as well as pattern and anomaly detection that could indicate impending disruptions. By doing so, it can swiftly propose effective solutions.
The success of a no-touch supply chain operations planning model depends on robust analytics, transparent real-time tracking through apps or dashboards, and granular, reliable data. Standardized procedures must be applied supply chain-wide. This transition requires a cultural shift in organizations, as seasoned professionals may be hesitant to hand over core activities to digital tools.
To manage this transformation, McKinsey suggests a “two-speed IT architecture.” This method layers a dynamic, fast-paced test-and-learn environment over the existing technology infrastructure for rapid prototyping and iterative development.
This lets users quickly develop, test, and refine new methods before integrating them into the system. Once proven, these new solutions can be fully integrated into the primary technology stack, improving supply chain efficiency.
Also Read: AI in Procurement: Top Reasons It Will Change The Way We do Business
Supply Chain Management through Data Integration
Moving ahead in Supply chain operations management, data is often isolated in silos, complicating critical data access and sharing. The globalisation of supply chains introduces complexity, variability in demand, and product diversification. Companies struggle with demand forecasting, balancing inventory against customer demands, and maintaining low holding costs. Additionally, regulatory compliance adds further complexity.
According to a study, 81% of digital supply chain management managers believe that data analytics will be critical for cost reduction. The key to this lies in Data integration. It involves combining data from different sources into a single format. This makes the supply chain more visible and gives users access to important operational data in real-time.
This integration uses historical data, market trends, and customer feedback to make decisions, automate and streamline processes, and predict demand more accurately. It also makes it easier for suppliers to work together, helps with compliance and risk management, and lowers costs by making operations run more smoothly and bringing products to market faster.
Also Read: The Power of Data Analytics in Inventory Optimization
Efficiency Gains through Supplier Consolidation at a Leading Tyre Manufacturer
Established in 1977, a leading tyre manufacturer with seven plants across India and Europe faced significant supply chain challenges due to a fragmented supplier base of over 600 suppliers, none of which were mapped to its crucial plant locations in Vadodara, India. This led to inefficient workflows and excessive inventory-carrying spaces.
Moglix intervened to streamline the supply chain by implementing vendor-managed inventory and consolidating suppliers, reducing the supplier count from 600 to 415 and line items from 8000 to 6000. This strategic consolidation achieved a 3% reduction in effective landed costs and a rebate of 0.5 to 2% on turnover.
Further enhancements included reducing the PR to PO generation time from an average cycle to just 2 days and setting up a warehouse within 25 KM of the plants, which improved the On-Time In-Full (OTIF) delivery rate to 90%. This restructuring not only streamlined operations but also unlocked significant cost savings and operational efficiencies.
Towards Tomorrow
As businesses confront new sustainability mandates, they must adapt to survive in a resource-constrained world, for organisations keen on adapting to sustainability trends, working with seasoned experts like Moglix offers valuable lessons. Moglix’s expertise in streamlining complex supply chains provides a blueprint for companies to enhance efficiency while meeting regulatory standards. Engaging with such partners can help firms maintain a competitive edge in a resource-sensitive market, making Moglix a strategic choice for those aiming to lead in supply chain innovation and sustainability.
7 Must-Ask Questions while Selecting the Perfect Ball Valve
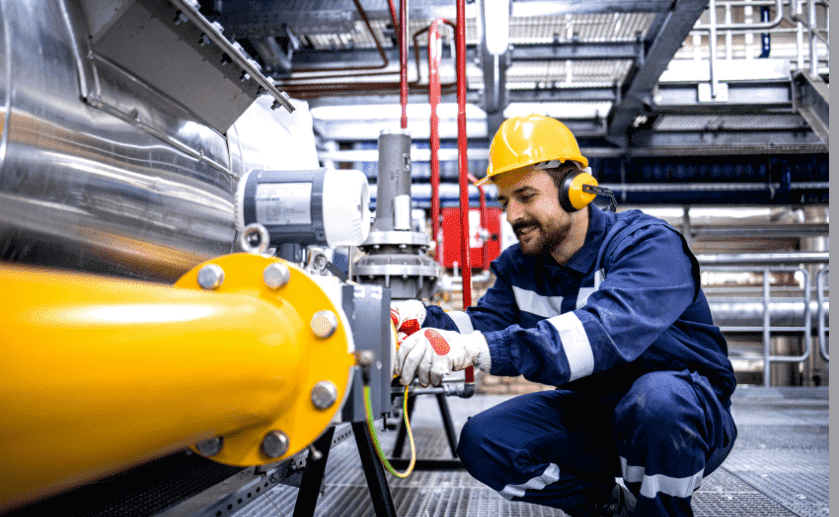
7 Must-Ask Questions while Selecting the Perfect Ball Valve
Industrial ball valves control the flow and ensure your industrial processes’ smooth operation and safety. They are highly durable, reliable, and easy to use. ̧
However, industries face challenges when selecting the optimal ball valve for their specific application. Let’s look at the key questions you should ask before choosing ball valves.
Also Read: Key Factors to Consider When Selecting High-Pressure Valves
Seven Essential Questions to Ask Before You Buy Industrial Ball Valves
1. What type of media will flow through the ball valve?
The nature of the fluid type (liquid, gas, or semi-solid) passing through the pipeline greatly influences the industrial valve selection. Different media have varying ike corrosive, abrasive, and viscosity. This analysis will guide engineers in selecting ball valves of ideal material to be compatible with the media to prevent leaks, damages, or malfunction properties, such as corrosive, abrasive, and viscosity. This analysis will guide engineers in selecting ball valves of the ideal material to be compatible with the media to prevent leaks, damages, or malfunctions.
2. What is the right actuation method for the ball valve?
How you actuate (close and open) valves will influence their efficiency. Therefore, it is vital to understand the various types of ball valve actuation.
There are different types of ball valve actuation, such as:
- Pneumatic ball valve: These valves use compressed air to open and close the ball. They are ideal for applications where large opening and closing forces are required.
- Electric ball valve: Such valves use an electric motor to open and close the ball and are highly useful where precise control is required.
- Hydraulic ball valve: Here, a pressurized hydraulic fluid opens and closes the ball where large forces are required.
- Manual ball valve: These valves are operated by a handle and are often used in low-pressure systems.
In this regard, you have to consider these things:
- Frequency of operation
- Energy availability and complexity
- Actuation operations
- Control and reliability
For instance, pneumatic actuators are needed for frequent and fast operations, whereas electric actuators are ideal for a reliable power supply. Similarly, hydraulic ball valves are best suited for high-pressure applications where frequent operations are needed, and manual ones are the ideal bet for low-pressure applications that require occasional manual control.
3. What are the maximum and minimum temp & pressure ratings of the fluid passing through the pipeline?
Ball valves also have temperature and pressure ratings. The minimum and maximum values indicate the temperature and pressure range of the working fluid that valves can handle.
Why is adhering to these values important?
- High-temperature variation can cause non-uniform expansion and contraction, leading to cracks.
- Minimum and maximum values indicate the valve’s temperature and pressure range.
- Excessive fluid pressure can break the seal and cause premature wear, leaks, and safety hazards.
The number of times you open and close the valve in a year is known as its annual cycle rating. Ball valves are rated for a specific number of cycles. Using a valve over its annual cycle rating may hamper its durability. If you use ball valves to understand their cycle requirements, they can work for tens of thousands of operations without any performance issues.
5. How are you going to use the ball valve?
Different ball valves are available on the market depending on the nature of their operation.
- Shut-off vs. flow direction control:
Standard ball valves can completely restrict the fluid flow. However, specialized ball valves are also available if you need directional control.
- Multi-directional flow (3-way ball valves):
Three-way ball valves offer even more control by splitting the flow from a single source to two destinations.
6. How do you choose the right material for the ball valve?
The media flowing through the valve should be compatible with the materials of the valve’s body and internal components (ball, seat). Incompatible materials can corrode or weaken the seal, leading to safety hazards or malfunctions. Consider stronger options like Monel, Inconel, or alloys containing molybdenum, chromium, or nickel for highly corrosive fluids.
7. What certifications should the valve have?
It’s imperative to select ball valves with the right certifications relevant to the fluid type and application within your facility. Depending on your application, your ball valve and its actuator might require certifications from:
- ANSI (American National Standards Institute): verifies pressure and temperature ratings for pipe flanges for safe operations within desired limits
- NEMA (National Electrical Manufacturers Association): sets design standards for electric ball valves for reliable performance
- NSF International: offers guidelines for selecting ball valves in food, beverage, and pharmaceutical production facilities to safeguard public health
Also Read: How to Choose the Right Valve for your Industrial Requirement?
Looking for an ideal supplier for high-quality industrial ball valves for your specific applications?
Partner with Moglix Business! Visit our online store for more industrial tools and equipment.
How innovative approaches can optimize procurement approaches?
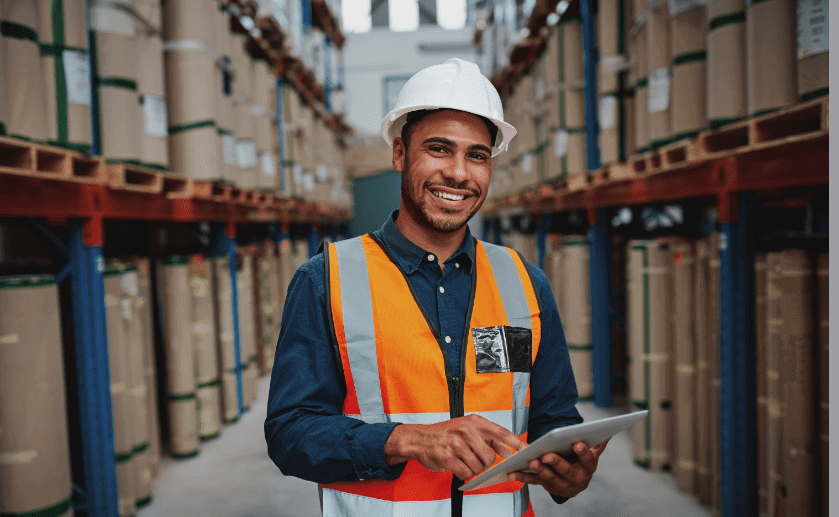
How innovative approaches can optimize procurement approaches?
In business, efficiency is everything. However, when it comes to procurement, where only 6% of companies agree to have full visibility of their supply chain, efficiency optimization matters even more. One of the studies revealed that procurement professionals spend one-third of their time handling manual mundane tasks. There are other performance bottlenecks that are affecting the process efficiency to a great extent. Let’s analyze top procurement challenges and learn some innovative ways to overcome them to improve efficiency with ease.
Traditional Procurement Challenges and Limitations
Traditional procurement methods typically rely on manual processes. Data may be siloed across departments, resulting in unwanted delays and performance inefficiencies.
As traditional procurement caters to a large number of average suppliers, businesses miss out on potential savings and innovation opportunities through strategic partnerships.
All these challenges can cause:
- Inflated costs due to reacting sourcing
- Lengthy approval cycles
- Missed opportunities for volume discounts
Operating with such slow, expensive procurement processes for a prolonged period can push a business into a competitive disadvantage.
On the other hand, companies leveraging innovative procurement approaches are more likely to thrive, innovate, and shape their sourcing and procurement lifecycle.
Different Ways of Procurement Optimization for High-Efficiency
Spend Analytics
Spend analytics gives you a clear picture of where your money goes. It analyzes your historical purchasing data to identify hidden costs and areas with excessive spending. You also get valuable data on buying trends and supplier performance to negotiate with a stronger hand.
Spend analytics are also useful in categorizing purchases to identify opportunities for standardization that translates to efficiency. You can use ERP systems to collect data from various departments and visualize them with business intelligence tools to analyze spending patterns and uncover areas for consolidation.
Also Read: Real-Time Analytics: The Driving Force Behind Responsive Supply Chains
Supplier Consolidation
Strategically reducing the number of vendors is one of the most effective methods to optimize your business’ procurement efficiency. When you purchase from a few suppliers, you get the chance to leverage better pricing terms and discounts due to a higher volume of orders.
Additionally, fewer suppliers means fewer invoices and lower processing costs. As mentioned earlier, you can take the help of spend analytics to identify categories for consolidation. You can also leverage supplier relationship management systems to centralize suppliers and efficiently manage supplier relationships with consolidated vendors.
Reverse Auction
Reverse auctions are undeniably innovative procurement strategies to drive prices down. Here, the traditional roles of suppliers and buyers are reversed. Unlike the traditional process, the buyer posts a request for a specific commodity or service. Then potential suppliers submit competitive bids in real time.
The winner is generally the supplier willing to do the job or provide service at low costs. There are dedicated reverse auction platforms where businesses can define their needs and manage the bidding process online. You can also integrate reverse auction platforms with your existing procurement systems for a smooth data exchange and task automation for easy management of the entire procurement cycle. Moglix utilized all of the tips shared above and a few more to increase the working hour efficiency of a leading cement manufacturer by 20% which was challenged by a fragmented supplier base, and non-standardization in pricing.
How to Optimize Indirect Procurement?
What is indirect procurement?
Indirect procurement involves purchasing goods or services that are not directly related to a business’s core production. This could include office supplies, facility management, travel expenses, and marketing services. As indirect procurement accounts for up to 80% of a company’s total purchases, it is imperative to optimize it with innovative strategies.
Here are some innovative methods to optimize indirect procurement:
- Use big data and spending analysis to identify hidden patterns and potential cost savings
- Implement a category management system to manage specific categories and identify innovative sourcing solutions
- Leverage cloud-based e-procurement platforms to automate workflows, streamline operations, and reduce administrative burdens
- Use online marketplaces dedicated to specific indirect procurement categories to access a large pool of vendors with low-price bids
Also Read: Digital Transformation in Procurement: The Current Trends and Future Directions
Nowadays procurement optimization requires modern technologies and approaches to address challenges emerging out of growing competition in the market. However, thoughtful implementation of these strategies is imperative to achieve significant procurement optimization that reflects recurring profit to the organization.
Are you looking to optimize your procurement through innovative methods? Leverage Moglix Procurement Solutions today!
FAQs
How to optimize product procurement?
An ideal product procurement optimization strategy should focus on acquiring the right products, at the right price, and at the right time. In this regard, businesses can use spend analysis and supplier consolidation to identify areas of cost reduction and make consolidated purchases for maximum discounts. They can also utilize an e-procurement process to automate routine tasks to save time and reduce operational costs.
What are the 4 stages of procurement?
The four stages of procurement are as follows:
Stage 1: identify goods/service requirements and outline the budget and specifications
Stage 2: find qualified vendors and select the best supplier through various methods
Stage 3: negotiate contracts, issue purchase orders, receive/ inspect goods or services, and manage supplier performance
Stage 4: release supplier payments and evaluate the procurement process for potential improvements
Mitigating Workplace Hazards With PPE
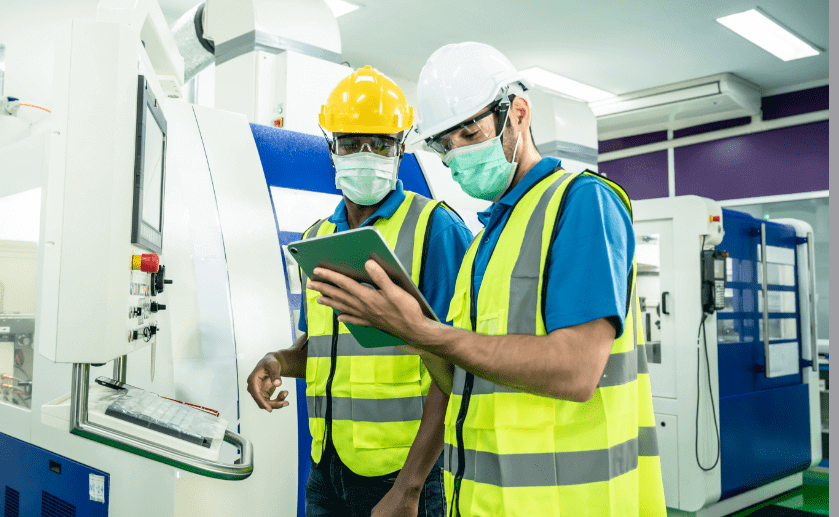
Mitigating Workplace Hazards With PPE
On the Birmingham High Speed 2 (HS2) rail link site, for instance, a contractor had a fatal accident. Although emergency services, such as Midlands Air Ambulance, were called, it was discovered that the contractor might not have been wearing enough personal protective equipment, which probably made the situation worse. The possible results of ignoring safety equipment in dangerous work situations are brought home by this incident.
Data from the International Labour Organisation (ILO) that indicates that around 2.3 million people die annually from diseases or accidents connected to their jobs highlights the significance of Personal Protective Equipment statistically even more. With almost 6,000 deaths per day, this emphasizes how urgently thorough safety precautions and equipment are needed.
This blog will discuss the many kinds of PPE available, outlining their particular applications and the laws that control their use. We’ll also discuss the role employers play in providing workers with the right Personal Protective Equipment to reduce risks at work and guarantee their safety. Business owners and safety officials will gain insightful knowledge on how to implement and maintain efficient safety protocols for employees.
Head Protection
Hard hats are the most often worn head protection. They shield against electrical hazards, impacts, and falling objects. They are available as Type II (top and lateral impact protection) and Type I (top-of-head impact protection). Safety standards, including OSHA and ANSI Z89.1, control the impact resistance and electrical insulating properties of hard hats.
Bump caps are lightweight head protection suitable for areas with low overhead hazards. They offer protection against minor bumps, scrapes, and lacerations. Bump caps are not designed to replace hard hats where significant impact hazards exist and may not meet all the same formal safety standards.
There are also specialized helmets for diverse tasks. These include:
- Welding helmets
- Firefighting helmets
- Electrical helmets
Key considerations
Always use head PPE that meets industry and workplace safety standards. ANSI and OSHA specifications require rigorous testing and performance to ensure Personal Protective Equipment provides adequate protection. Proper fit and regular inspections are key to keeping head PPE working properly.
Also Read: Things to Consider While Choosing Safety Helmets
Importance of Respiratory Protective Equipment in Industrial Settings
When a study was conducted way back in 2020 by Global Action Plan and Zehnder Clean Air Solutions in the UK, they found out that 440,000 workers are exposed to harmful air conditions. It is a matter of time before a similar kind of study is witnessed in the USA too. However, the solution lies in the Respiratory protective equipment (RPE). The reason is simple, it can be worn by anyone, it protects the user against all harmful gasses and particulate matter and it is cost effective. Whenever you consider RPE for your work, you can look for:
Air-Purifying Respirators (APRs)
When you look for APRs you will find two common types. Both of them consist of filters or cartridges but their utilities are different. Let’s understand:
- Disposable filtering facepieces (N95, etc.): We witnessed their importance during the pandemic. They block particulate matter (dust and some airborne pathogens) from entering the air.
- Half-mask or full-face respirators: This kind of RPE provides higher protection levels and uses replaceable cartridges for filtering glasses, vapours, or particulates.
Atmosphere-Supplying Respirators (ASRs)
ASRs supply clean air from an independent source. Types include:
- Supplied Air Respirators (SARs): Workers who enter into Confined spaces (tanks or tunnels) with dangerously low oxygen levels or highly toxic contaminants need it. There is a hose which supplies the clean air to the user via a hose.
- Self-Contained Breathing Apparatus (SCBA): This equipment is essential for reducing the inhalation of toxins.It enables breathable air in unbreathable environments, such as smoke in a building or toxic gas outbreaks.
Also Read: 5 Trends Driving the Safety Equipment Industry
Compliance and Standards
As a safety officer, selecting Respiratory Protective Equipment (RPE) requires adherence to key compliances. First, accurately identify workplace hazards to ensure the chosen RPE provides adequate protection. Second, select RPE that suits the wearer, task, and environment, taking into account fit and comfort. Third, ensure all RPE meets legal standards, such as CE marking and specific regulations set by OSHA or local authorities. Finally, consult with employees and safety representatives to ensure the RPE meets their needs and job demands, fostering a collaborative approach to safety.
Face and Eye Protection
Thousands of workers sustain serious eye injuries annually; some even lose their sight. These injuries can be avoided, claims the Occupational Safety and Health Administration (OSHA), with appropriately chosen and worn eye and face protection.
Understanding Workplace Hazards
- Impact Hazards: Most eye injuries result from tiny particles like metal slivers or wood chips hitting or scraping the eye. Serious injury can result from these being blown by the wind or thrown from tools.
- Chemical and thermal burns are common in settings using industrial chemicals or cleaning products. One hospital study conducted by the National Institute for Occupational Safety and Health (NIOSH), for example, reported that workers had eye burns from a cleaning solution containing acetic acid, peracetic acid, and hydrogen peroxide.
Also Read: How India is Tackling Workplace Hazards Head-On?
Selecting the Right Protective Gear
- Impact and Particle Protection: To guard against flying particles, wear goggles or side shields on ANSI-approved safety glasses.
- Chemical Burns: When handling hazardous chemicals or cleaning products, wear goggles or face shields to avoid splashes that can damage your eyes.
- Thermal burns in welding: OSHA mandates that welders wear helmets with properly shaded lenses to guard against sparks and high heat (OSHA Standard §1910.252(b)(2)).
- Laser Exposure: For jobs involving lasers, it is imperative to wear laser safety goggles that block the particular wavelength, following safety regulations such as §1926.102(c)(2)(i), which outlines the optical density required for protection.
Employers are responsible for ensuring that all employees can access and use the proper kind and quality of protective eyewear. This includes providing equipment to employees at no cost and covering prescription glasses when required.
Prospective Insights
As a Business owner or safety officer,, you face daily challenges in protecting workers from preventable injuries. The recent HS2 site incident and International Labour Organisation data underscore the vital role of Personal Protective Equipment (PPE) in safeguarding employees. Compliance with safety regulations and proper Personal Protective Equipment use are crucial in mitigating risks. Each workplace has unique hazards that demand tailored safety measures. To enhance your safety protocols effectively, consider hiring a consultant such as Moglix who can help you learn more by providing specialized insights and strategies tailored to your specific needs.
How Segmenting Suppliers can boost your profits
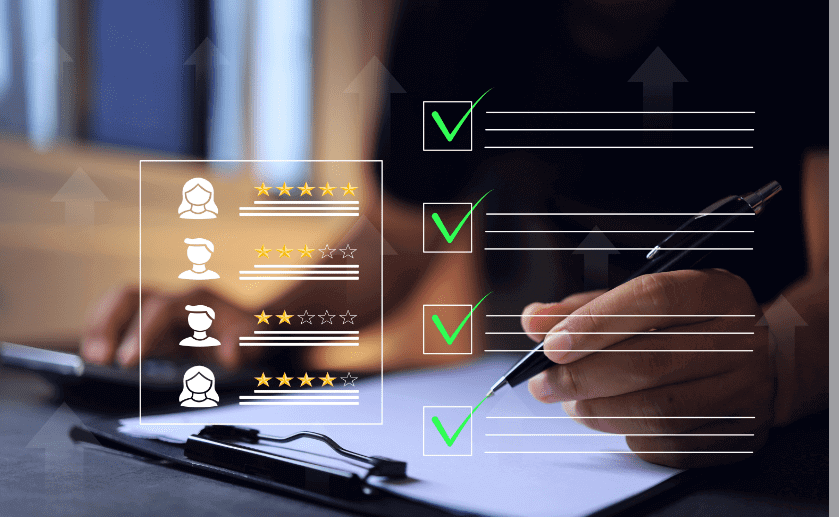
How Segmenting Suppliers can boost your profits
Vendor management improves how vendors affect the business. It centres on working together, following rules, and making payments efficiently. It decreases risks such as fraud. It simplifies supply problems using tactics like grouping suppliers.
Segmentation categorizes vendors based on spending volume and risk. It enhances targeted management. Vendor consolidationreduces vendor numbers, streamlines processes, and cuts costs. This blog explores how these strategies improve supplier management and business efficiency.
Understanding Supplier Segmentation
Supplier segmentation is one of the fundamentals of supplier relationship management (SRM). It categorizes suppliers based on specific criteria, enabling the efficient allocation of resources.
Benefits
Success in vendor management depends on having a well-designed supplier segmentation model. Other supplier segmentation model benefits are:
- Focuses on key suppliers driving the most value.
- Allows tailored management approaches.
- Realizes efficiency gains in procurement, inventory, and supply chain finance.
Also Read: Mastering the Art of Supplier Relationship Management (SRM)
Critical Factors for Segmenting Suppliers:
Strategic suppliers typically represent about 10% – 15% of the total number of suppliers in a database. The Kraljic matrix is used in procurement and supply chain management to categorize goods and services based on supply risk and profit impact. This classification, derived from the Kraljic matrix, can be further refined to create detailed sub-groups within each quadrant, enhancing the precision of supplier management.
Statistics and Key Factors for Segmenting Suppliers:
- Spend, Value, and Strategic Importance: Suppliers are categorized based on spending volume and business importance.
- Risk and Performance: Suppliers should also be assessed regarding potential supply disruption or financial instability.
- Complexity of Products/Services, Innovation, and Improvement: Suppliers are segmented based on their required specialized management strategies for complex products/services.
- Geographic Location and Business Unit Interaction: Suppliers’ segmentation is determined by the impact of their global or regional presence on logistics and market reach .
Also Read: How Businesses Can Drive Efficiency Through Vendor Consolidation?
The Way Forward
Supplier segmentation can elevate a business’s potential to the next level. Here is a case: Moglix implemented a vendor management system for a leading tyre manufacturer with operations across India and Europe, dealing with over 600 suppliers and 8000+ line items.
This system addressed challenges like fragmented suppliers, sourcing inefficiencies, and delayed deliveries by improving supply chain visibility and efficiency. The solution resulted in a 3% savings on the total cost of ownership, optimizing the manufacturer’s working capital, real estate, and resource bandwidth.
Suppose an organization is dealing with supply chain issues. In that case, it can seek expert consultation in the industry who can provide real-time insights, understand its core issues, and enhance its vendor management capabilities. For this, it can connect with Moglix for a consultation.
Stay Safe, Get Gear: Your Guide to Industrial Safety Equipements
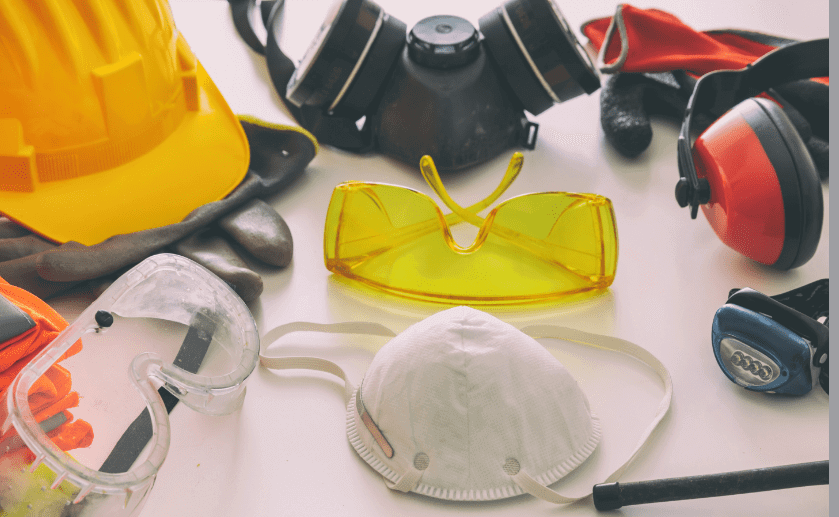
Stay Safe, Get Gear: Your Guide to Industrial Safety Equipements
Safety equipment in industries prevents fatal calamities. According to government data, three workers in Indian Factories perish daily on average due to fundamental safety precautions not being followed.
The organisation’s procurement and safety officers are in charge of choosing safety gear. This blog will guide you in choosing industrial safety gear such as safety shoes, helmets, face protection, and gloves.
Guide to Selecting Industrial Safety Equipment
Here is the breakthrough of the factors to consider before buying any safety equipment from suppliers:
For Safety Shoes
Safety Shoes are made to protect workers on the job. Before choosing your Safety shoes, you must:
- Identify specific dangers in your workplace, such as the risk of falling objects, electrical hazards, or exposure to chemicals.
- Ensure the footwear meets industry safety standards and regulations, such as ASTM F-2412-2005 or ANSI Z41-1999.
- Select shoes that fit well and are comfortable for long periods. Comfortable footwear prevents foot fatigue, enhances worker productivity, and reduces the risk of injury.
- Choose shoes made from materials that offer protection against the specific hazards of your environment, such as leather for durability or rubber for electrical resistance. Durable materials ensure longevity and sustained protection for workers.
- Depending on the risks identified in your workplace, look for features like steel toe caps, slip-resistant soles, and puncture-resistant materials. These features provide additional protection against common workplace hazards, reducing the risk of injury.
- Quality and Brand Reputation: Opt for reputable brands known for high-quality and durable safety shoes. Choosing established brands ensures reliability and consistency in performance, providing peace of mind to workers and employers.
Also Read: An insiders Knowing Difference between Safety Shoes and Work Boots
For Helmet
Safety Helmets protect the workers from fatal injuries.
Purchasing considerations for safety helmets:
- Ensure the helmet meets international safety standards like ANSI/ISEA Z89.1, CSA Z94.1, or EN 397, guaranteeing rigorous testing for impact resistance and electrical insulation.
- Different types are designed for specific hazards, such as hard hats for falling objects and electrical hazards. Others may offer additional features like face shields or earmuffs.
- Helmets are usually made from materials like HDPE, ABS, or fibreglass. Consider durability, weight, comfort, and ventilation features.
- A properly fitting helmet is crucial. Look for adjustable suspension systems and chin straps for a secure fit. Comfort is vital for long-term wear.
- Depending on job requirements, helmets with integrated eye protection, reflective strips, or accessory slots for headlamps and hearing protection may be necessary.
- Regularly inspect helmets for damage or wear. Follow the manufacturer’s guidelines for cleaning and storage to maintain their protective effectiveness.
Also Read: Things to Consider While Choosing Safety Helmets
For Face Protection
Here are the most important points to consider for choosing face protection:
-
The
first and most crucial step is to identify the specific hazards
present in your work environment. Consider the following:
- Impact: Flying chips, debris, or other projectiles.
- Chemical Splash: Acids, bases, or other harsh chemicals.
- Heat: Sparks, molten metal, or extreme temperatures.
- Optical Radiation: Welding arcs, lasers, or intense UV light.
- Dust or Biological Hazards: Fine particles or infectious materials.
-
Once
you understand the hazards, choose the appropriate protection:
- Safety Glasses: Protect against moderate impact and small particles.
- Goggles: Offer a tight seal, protecting against chemical splashes, dust, and some impact.
- Face Shields: Provide full-face coverage against larger impacts, splashes, and some heat exposure. Worn in conjunction with safety glasses or goggles for optimal protection.
- Welding Helmets: Specialized protection with shaded lenses for welding and similar activities.
-
The
material of the face protection is essential for durability and
resistance:
- Polycarbonate: Offers excellent impact resistance and is common in most safety gear.
- Chemical Resistant Materials: Consult a compatibility chart against the specific chemicals in your workplace.
- Heat-resistant Materials: Look for specialized materials for high-temperature environments.
-
Proper
fit prevents gaps, ensuring protection. Adjustable straps help
customize the fit. Comfort is crucial, as uncomfortable PPE is less
likely to be worn correctly.
- Always ensure the face protection you choose adheres to relevant safety standards, such as ANSI Z87.1 (USA), EN 166 (Europe), or your country’s specific standards. Check for markings on the equipment.
Important Points to Remember:
- Eye protection is often specialized. What works for metal grinding might not be appropriate for chemical handling.
- Face shields are usually considered secondary protection and should be worn with safety glasses or goggles.
- Consult your company’s safety guidelines and resources for specific requirements in your work area.
For Safety Gloves
A Concerning Statistic: Hand injuries are shockingly common in industrial settings. The Bureau of Labor Statistics reports that hand injuries account for a significant portion of all workplace accidents.
Key Considerations for Choosing Industrial Safety Gloves
-
Just
like with face protection, start by identifying the specific
threats you’ll face:
- Look for gloves with cut-resistant materials like Kevlar or specialized metal mesh.
- Check chemical resistance charts provided by glove manufacturers to ensure the glove’s material is compatible with the chemicals you handle.
- Choose gloves with heat insulation or thermal lining for temperature extremes.
- If sharp objects are a risk, consider additional puncture resistance.
- Electricians need specialized insulating gloves with voltage ratings.
-
Glove
materials make all the difference:
- Leather: Durable and offers good cut and abrasion resistance.
- Nitrile, Neoprene, or PVC: Excellent chemical resistance (check compatibility charts).
- Kevlar: Supreme cut resistance.
- Specialty Materials: Consider aluminized gloves for heat and chainmail for extreme cut hazards, etc.
-
Ill-fitting
gloves are clumsy and increase risk. Too loose and they slip; too
tight and they restrict movement. Look for snug fits with
flexibility for your specific tasks.
- Don’t
sacrifice the ability to handle objects for the sake of protection.
Balance the required protection with the need for precision and
control. Consider thinner gloves with high cut resistance where
appropriate.
- Ensure
the gloves you choose meet the required safety standards for your
industry, such as ANSI/ISEA (USA) or EN (Europe). Look for markings
on the gloves indicating compliance.
Pro Tip: No single glove is perfect for everything. You might need multiple types for different tasks. Consult safety supply resources and your company’s guidelines to make the best decisions.
Also Read: 5 Trends Driving the Safety Equipment Industry
After exploring this guide, you’re now prepared to enhance workplace safety by selecting the right safety equipment. To refine your choices consider consulting with industrial experts such as Moglix on safety equipment and get the best guidance.
How purchase order systems can cut costs?
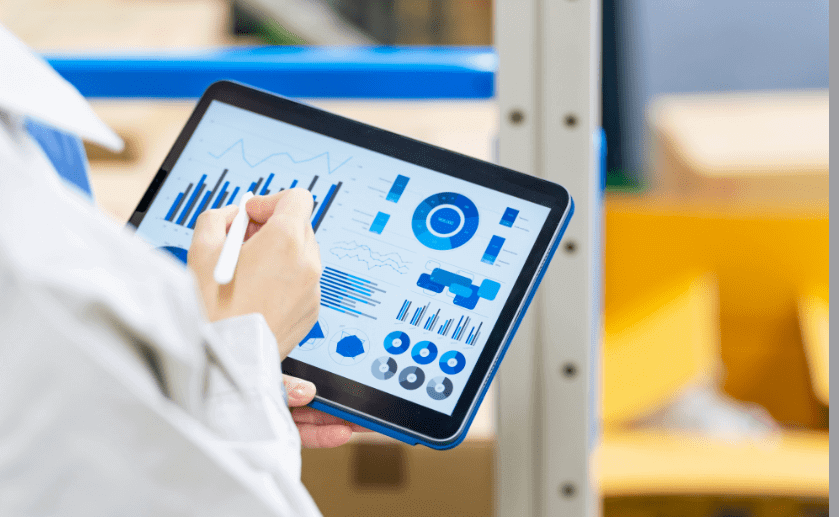
How purchase order systems can cut costs?
Businesses always aim to have full cost control and visibility over their procurement processes in real time. 79% of CPOs are prioritizing procurement cost savings in 2024 and years to come. When 10s or 100s of approvals are processed manually every week, tracking all PO and non-PO invoices with 100% accuracy becomes challenging.
This is where the need for purchase order systems becomes imperative. Let’s see how a Purchase order management system empowers businesses to gain greater control over spending, prevent costly overruns, and achieve significant cost savings.
Five Cost-Saving Benefits of Having a Robust Purchase Order Management Systems
Automated workflows
A procurement process involves many repetitive tasks. An ideal PO system can automate mundane manual tasks such as data entry, routing for approvals, and sending purchase orders, freeing up valuable man-hours for other strategic initiatives. An automated PO system can electronically route purchase orders to appropriate departments without requiring any paperwork.
Learn how Moglix reduced PR to PO time for a leading cement manufacturer company with a robust PO system for achieving 20% higher working hour efficiency.
However, for automated workflows to work effectively, businesses need to standardize data entry, approval processes, and communication protocols to avoid errors and delays. It is also imperative to integrate PO systems with existing ERP and accounting systems to ensure smooth data flow without any data silos.
Therefore, it is recommended to start by automating a few tasks and gradually expand as comfort levels increase.
Eliminating Manual Errors and Delays
PO systems come with a central platform for all purchase order communication. There is no need to communicate through lengthy email threads and scattered documents. Automated notifications keep everyone involved on the same page regarding order status updates, approvals, and any potential issues.
This streamlined communication minimizes misunderstandings and errors that can lead to order delays and additional costs. Some PO systems also allow real-time collaboration with suppliers to make informed sourcing decisions. This helps in better pricing negotiation and prevents unauthorized or unnecessary purchases.
Also Read: How Your Accounting Processes Is Being Undercut by Manual Processing?
Real-time Tracking of Purchase Orders
Advanced PO systems offer you real-time tracking capabilities. You can see where each order is in the process – from placement to delivery. As a result, you can identify potential delays or issues with orders early on.
This enables proactive intervention to minimize disruptions and prevent cost overruns. The real-time status of incoming materials also allows businesses to manage inventory better. They can easily avoid stockouts and unnecessary purchases, which leads to cost savings. If the status shows potential delays in order arrival, businesses can explore alternate vendors to save money on expensive rush orders.
Identifying Spending Patterns and Trends
PO systems are not just for streamlining workflows; they can also analyze your purchase order data to identify spending patterns and trends as well. This leads to cost savings. For instance, the analytics can highlight the areas of high spending, such as overused categories, unnecessary purchases, or potential vendor markups.
This analysis helps you develop targeted cost-reduction strategies. For instance, you can plan to negotiate better pricing with existing vendors or consolidate purchases with fewer suppliers. With historical spending data from purchase order management software, you can create more accurate budget forecasts and have tighter control to prevent unnecessary spending.
Ensuring Budgetary Compliance
Purchase order management software allows you to set spending limits for departments or categories. When purchase orders exceed these limits, the system would require additional approvals. This helps businesses prevent unauthorized or excessive spending.
Also, as you can track spending in real-time against the budget, it becomes easy to acknowledge how departments are utilizing the spending limits. As all purchase orders are managed from a centralized platform, there is no risk of duplicate or unauthorized purchases. Businesses can have better financial control and cut back on unnecessary expenses.
The Way Forward
Leveraging purchase order software offers huge cost-saving opportunities for CPOs. They feel empowered with real-time data to prevent departments from exceeding pre-defined budgets, identify opportunities for cost savings, and strengthen the company’s position during contract negotiations.
However, it is imperative to partner with an ideal procurement solution provider, like Moglix Business, to overcome the associated challenges with purchase order software implementation easily.
Ready to experience the cost-saving power of PO systems?
Explore procurement solutions from Moglix today!
A CPO’s Guide to Indirect Spend Management
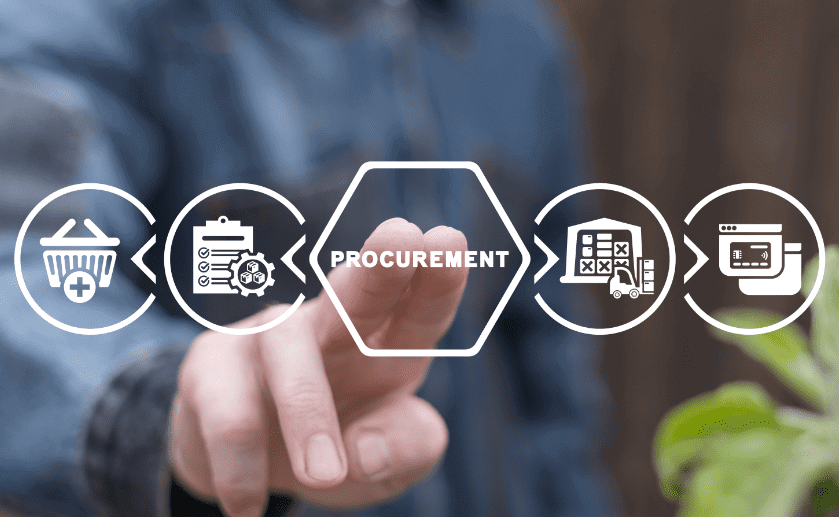
A CPO’s Guide to Indirect Spend Management
Did you know that indirect spend can devour a whopping 20% to 40% of a company’s overall financial budget? This highlights the importance of effective indirect spend management. For CPOs all over the world, spend optimization is a constant pursuit. While direct procurement often receives the maximum attention, indirect procurement should also be aware of the eagle’s eye. This blog will guide CPOs on indirect spend management by showing its impact on procurement strategy. Get ready for actionable insights and best practices to change your approach to indirect spend.
Understanding Indirect Spend
Indirect spend, or indirect procurement, refers to all indirect expenses in producing goods or services. This could include office supplies, marketing expenses, travel, utilities, professional services, and IT infrastructure. Unlike direct procurement, with fewer suppliers and high-value contracts, indirect procurement involves a more extensive, more fragmented supplier base with lower individual purchase values.
Importance of Indirect Spend Management
Cost Savings Potential: By optimizing indirect procurement, companies can reduce their costs by up to 25%.
Improved Visibility and Control: Due to its decentralized nature, indirect spending can go beyond control. Its effective management enhances visibility across the entire supply chain.
Enhanced Risk Management: A diversified supplier base can help you avoid the risk associated with sole dependency, as in direct procurement. Intel is the best example of a company that spends $300 million annually with diverse suppliers.
Challenges Faced by CPOs in Indirect Procurement
Let’s look at the challenges that indirect spend presents for CPOs.
Visibility and Data Accuracy: Due to the decentralized nature of indirect spend, CPOs need help to achieve complete visibility and maintain data accuracy across their supply chain.
Supplier Management: Indirect procurement involves a large and diverse supplier base. That makes it even more challenging for CPOs to build strong relationships, monitor performance, and negotiate effectively with each supplier.
Stakeholder Buy-In: Businesses need help monitoring stakeholder buy-in across various departments with the authority for indirect purchases. Unless you have implemented solid policies and procedures, it isn’t easy to streamline the process.
Limited Resources: Most businesses need a dedicated team to manage indirect spending. Also, they lack technology knowledge and do not know how to use automation to streamline processes. In that case, managing the indirect spend across the entire supply chain even gets more challenging.
Best Practices for Optimizing Indirect Spend Management
Here are some key strategies that CPOs can leverage to optimize indirect spend management:
Leveraging Technology: Nowadays, nearly 15%-40% of organizations are automating procurement through technologies for direct and indirect procurement cost savings. Using an ideal procurement software powered by AI and ML can automate tasks, centralize data collection, aid in spend analysis, and streamline approvals.
Category Management: CPOs can also group similar indirect spend categories and develop a strategic approach for each, according to a study by McKinsey & Company. This will help CPOs to quickly focus on negotiation, supplier consolidation, and volume discounts. You can also refer to this case study to learn how the e-catalog solution from Moglix has helped India’s second-largest tractor manufacturer save 85% of staff hours on procurement.
Vendor Management: Imagine working with a limited number of suppliers to manage your indirect expenses easily. Almost 70% of organizations are considering vendor consolidation by 2025 to negotiate favorable contracts, establish clear performance metrics, and identify cost-saving opportunities.
Spend Data Analysis: Big IT giants like Infosys are leveraging spend data analysis from both direct and indirect procurement to identify patterns, uncover savings opportunities, and inform category management strategies.
Are you looking for an ideal procurement software solution to manage your indirect procurement for substantial cost savings?
Partner with Moglix Solutions! Visit our website to learn more.