MRO Management Strategies for Manufacturers to Drive Cost Savings
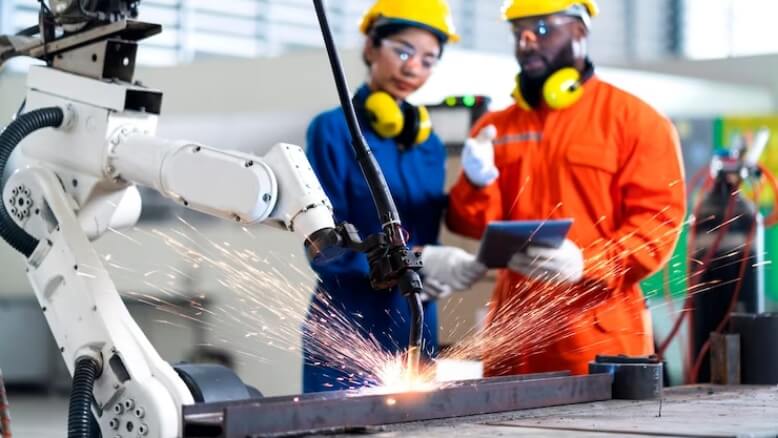
MRO Management Strategies for Manufacturers to Drive Cost Savings
With the majority of procurement initiatives targeted at streamlining direct costs, maintenance, repair, and operation (MRO) costs are often overlooked. 59% of procurement leaders have reported feeling pressured to reduce operational budgets, with another 40% stating the need to improve asset performance.1
This makes reducing unplanned downtime by ensuring all the right parts and equipment are readily available at any given time an absolute necessity. Adopting MRO management strategies can ensure manufacturers proactively deal with procurement risks instead of following reactive maintenance policies.
Top 3 Strategies to Optimize MRO Supply Chain
As manufacturers grapple with several procurement risks, including fragmented supplier base, low spare parts standardization, excessive inventory holding, low catalog usage, and high lead times, reducing indirect costs can feel daunting. Below, we outline the top three MRO procurement strategies that induce cost savings and improve operational efficiency.
Implement Spending Analytics
The global distribution of manufacturing plants paired with a large decentralized user and supplier base entails incurring millions of transactions, which hold massive scope for cost savings. Manufacturers can identify operational inefficiencies within their MRO procurement processes by thoroughly analyzing spending patterns.
Businesses must deploy techniques like ABC analysis to categorize MRO items based on their impact on production and cost to prioritize critical item purchases while reducing costs on lower-value items. To put this into perspective, procurement leaders spend almost 30%2 of their time making manual purchases.
Leveraging data-driven software tools, such as Moglix Solutions, can enable manufacturers to track their spending in real time, acquire actionable insights, and gain alternate product recommendations at better pricing, leading to substantial cost savings.
Introduce Process Transparency
Manufacturing’s MRO supply chain involves several procurement and inventory processes to ensure regular maintenance and replacement of assembly line machines, conveyor belts, and industrial motors. However, such multiple processes also imply multiple error possibilities. For instance, poor visibility into quality and compliance processes can raise procurement costs by 10%.3
Manufacturers must encourage cross-functional collaboration among operations, maintenance, and vendor teams by establishing clear communication channels and documenting detailed procedures for the proper management of MRO procurement processes. By ensuring thorough accessibility and transparency of procedures for all stakeholders, manufacturers can identify and remediate inefficiencies and quality slippage, promote accountability, and enable efficient decision-making, thus contributing to cost savings.
Establish Strong Supplier Relationships
Typically, manufacturers contract with hundreds of vendors to cater to unplanned and unanticipated stockouts and MRO purchases, which forces them to forgo the benefits of high-volume purchases. Hence, strategically consolidating your supplier base and collaborating with them can yield cost benefits. To illustrate, Moglix’s MRO procurement solutions help reduce the supplier base by 80%.4
Manufacturers must establish key performance metrics (KPIs), such as price competitiveness, quality standards, and delivery reliability, to evaluate supplier performance and prune their supplier tail end accordingly. Entering into long-term agreements facilitates better price negotiation and builds trust, which is necessary for cost optimization.
Augment Your MRO Management with Moglix’s Solutions
With Industry 4.0, powered by predictive data analytics, artificial intelligence, and the internet of things, becoming the new normal, harnessing data-driven insights has become intrinsic to streamlining MRO procurement processes. Using a centralized platform, like Moglix’s solutions, can empower manufacturing companies to better detect process deficiencies and maintenance needs, optimize workflows and resource allocation, enhance operational excellence, and gain complete visibility of their MRO supply chain.
To put this into perspective, Moglix helped cut operational costs by 5% for a major EPC company focused on civil and environmental infrastructural development. Faced with the numerous challenges of a fragmented vendor base, exponential inventory holding costs, and poor spending control, it sought to improve process efficiencies by aggregating its remote sites through Moglix’s solutions. Download the case study or get in touch to learn more.
How Technology is Transforming the Landscape of Procurement in Chemical Industry
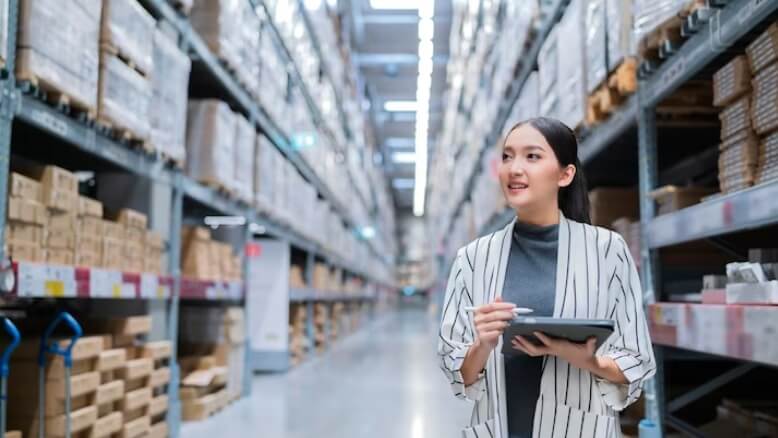
How Technology is Transforming the Landscape of Procurement in Chemical Industry
MRO procurement (maintenance, repair, and operations) in the chemical industry is not just about purchasing and managing industrial equipment at the lowest cost. It is also about ensuring compliance and sustainability, continuously improving and optimizing, creating value for stakeholders, and fostering innovation.
The chemical industry lacks severely behind the best-performing sectors, such as automotive, when it comes to optimizing the MRO procurement processes (McKinsey). This is worrying since the chemical industry relies heavily on MRO procurement, so much so that the purchasing costs in the industry are equivalent to 50–70% of sales revenues. Therefore, improving procurement processes can significantly impact the chemical companies’ bottomlines — as per a McKinsey analysis, sectors following procurement best practices have a 17% higher EBITDA.
One of the ways to achieve procurement excellence is by adopting modern tech solutions, such as procurement management systems. Such systems can transform the function from reactive and tactical to proactive and strategic. How? Continue reading to find out.
Tech-Driven Procurement in Chemical Industry
Procurement management systems transform the capabilities and culture of the function itself. It achieves this by giving you access to real-time data, tools to analyze it, a dashboard to present information in consumable chunks, and reports to present to the leadership teams:
Enabling you to improve the quality and efficiency of your communication and coordination between internal and external stakeholders.
- These platforms boast features such as real-time data sharing, end-to-end visibility for processes, in-context messaging, and uses AI to identify threats and do damage control.
- This can enhance the quality and promptness of communication, improve transparency, and foster value creation and innovation.
Helping you leverage big data and advanced analytics to tap into market trends, forecast demand, measure supplier performance, and track price fluctuations.
- It can help you monitor the availability and prices of commodities, negotiate from the point of power, and manage risks proactively.
- Spend analytics can also help you analyze spending patterns across suppliers, locations, and business units, giving you room to identify opportunities for cost reduction and consolidation.
Streamlining and automating transactional and tactical procurement activities such as ordering, invoicing, payments, and requisitioning.
- It can reduce manual work, save costs, save time, and increase accuracy.
- It can also help you track inventory levels, track shipments, and optimize logistics.
Conclusion
A robust digital procurement solution empowers chemical companies to make data-driven decisions, transform operations, and boost financial performance. One of the ways to do that is using Moglix’s vendor consolidation capabilities to simplify your procurement across multiple suppliers.
This case study shows how Moglix did this for a leading chemical manufacturer and helped them reduce cost, optimize inventory, and made the supply chain ecosystem more efficient and transparent. Learn more about how Moglix can help you, click here.
How Analytics Drives Efficiency in the Pharma Supply Chain
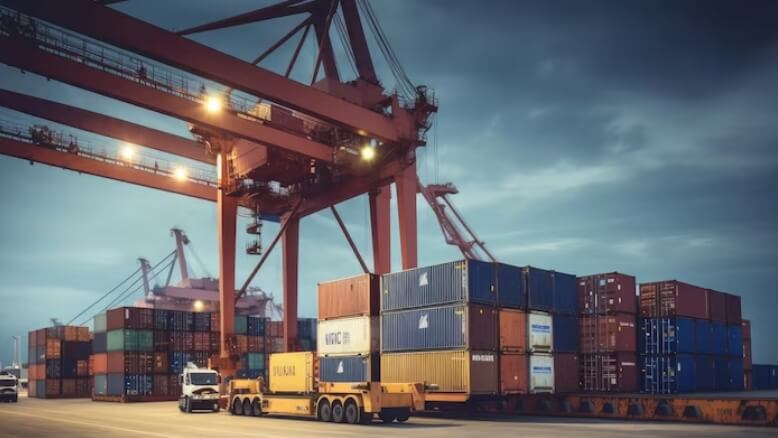
How Analytics Drives Efficiency in the Pharma Supply Chain
Supply chain disruptions in the pharma industry can cause a potential loss of 25% of EBITDA over ten years, notes a McKinsey report. EBITDA is a key indicator of a company’s overall financial performance, and losing it can be costly and avoidable. How? By using data analytics for MRO supply chain optimization.
Predictive modeling can help pharmacos predict product demand, optimize inventory, and reduce waste and costs. It can help them control and monitor product quality throughout the supply chain. Therefore, data analytics can offer significant value for MRO (maintenance, repair, and operations), supply chain optimization, and patient care.
In this blog, however, we’ll focus on how predictive modeling, or data analytics in general, could help pharmacos with MRO supply chain optimization and eventually minimize costs.
Keeping the MRO supply chain disruption-free
Another McKinsey report shows that a pharma company can achieve 15–30% operating efficiencies over five years by scaling the impact of advanced analytics. While this research focuses on the impact of predictive modeling on new medical therapies, here’s how it can also improve supply chain forecasting:
- Pharmacos can use data they generate and collect throughout their MRO supply chain to further optimize it by leveraging data analytics and digitizing their platforms. This could improve visibility, efficiency, and agility.
- You can streamline and secure the journey of medicines and equipment using data analytics, blockchain, and Internet of Things (IoT) sensors. So if a shipment is delayed, you can detect the problem and take corrective measures before the product reaches the end consumer.
- By anticipating and mitigating the impact of external factors, pharma companies can reduce the risk of disruptions and improve their resilience. For instance, using scenario analysis, you can evaluate the potential outcomes and impacts of different events on your MRO procurement processes.
While data analytics can help pharmacos by improving their supply chain’s visibility, agility, and resilience, what about mitigating the impact on MRO spending? This is where spend analytics come into the picture.
Minimizing Cost Using Spend Analytics
Spend analytics involves collecting, cleansing, classifying, and analyzing cost spending to reduce procurement costs, improve budgeting, and monitor compliance. It can help pharmacos in MRO procurement processes and supply chain optimization by:
- Identifying opportunities for savings by reducing waste or negotiating better prices or terms
- Improving accountability by tracking and measuring MRO spending across business units
- Enhancing supplier management by evaluating performance and benchmarking quality
- Supporting strategic decision-making using data-driven insights to evaluate return on investment and optimize cost-value trade-offs.
Conclusion
In the face of rising regulatory pressures, customer expectations, and costs, analytics is no longer just the source of competitive advantage for the pharma industry. However, success depends on building the right framework and capabilities.
One of the ways to do that is to leverage Moglix’s capabilities, just like this COVID-19 vaccine manufacturer did. Moglix enabled 16 of its plants for just-in-time delivery of MRO goods and replaced
the non-strategic vendor codes with a single point of contact. Click here to learn more about Moglix can make your MRO procurement efficient and financially sound.
Ideas for Building India’s National Infrastructure Pipeline in the Utilities Sector
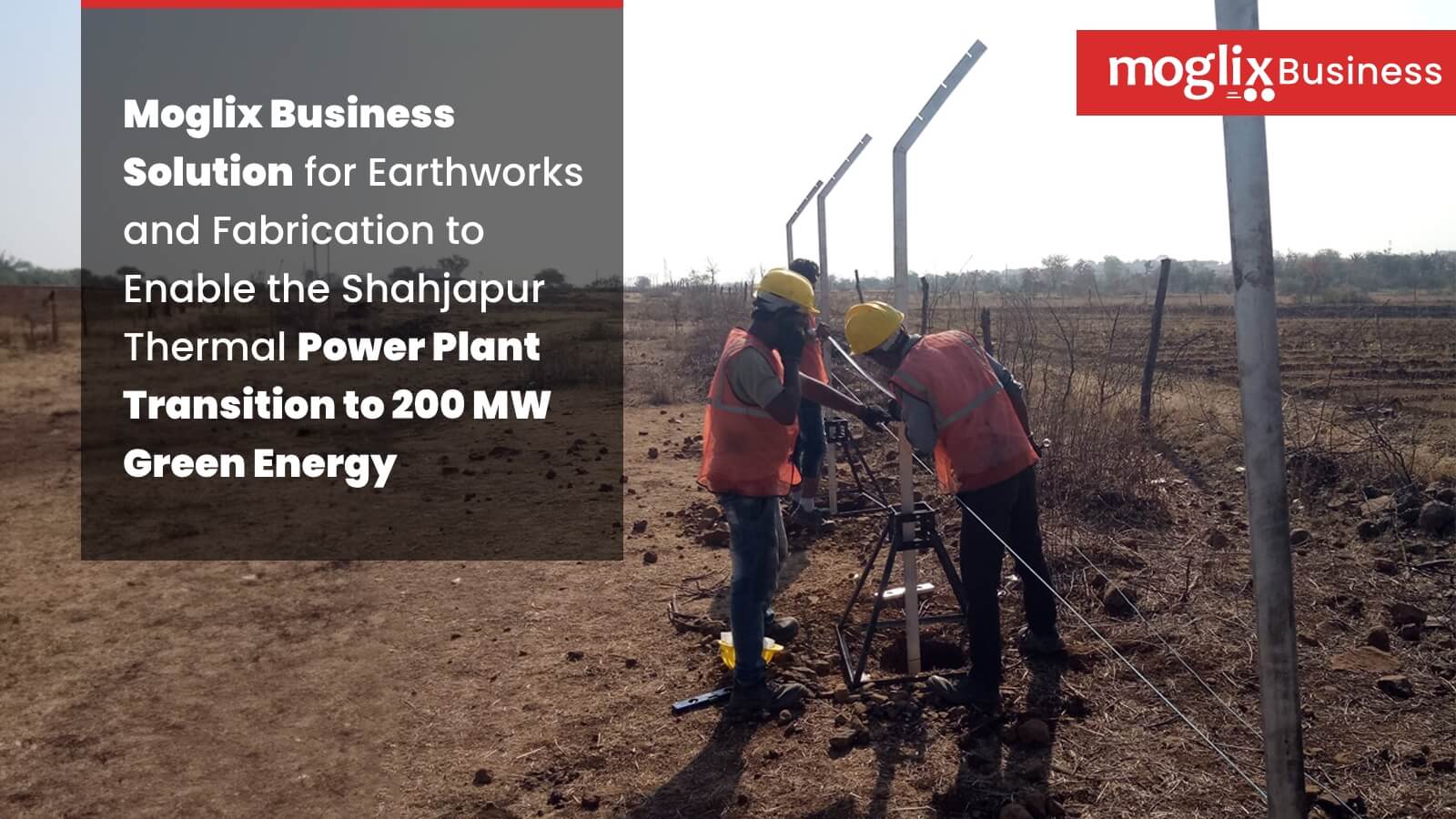
Ideas for Building India’s National Infrastructure Pipeline in the Utilities Sector
What Has Been the Progress in Building the Utilites Infrastructure in India till Now in 2023?
There are 4 sub-sectors of utilities across which India has experienced significant growth, namely: non-renewable energy, renewable energy, water resources, and waste management. India has an installed thermal power capacity of 230 GW, as of 2023 and is well on its way to transitioning towards net zero carbon emissions by 2070. With an installed solar PV capacity of 64 GW, India has become one of the world’s largest producers of solar power. Initiatives like the “One Sun One World One Grid” aim to establish a global interconnected solar grid. Here’s an insight on the opportunities available for building India’s utilities infrastructure and ideas on the supply chain that EPC companies will need.
What Are the Major Opportunities for EPC Infrastructure Companies in the Utilities Sector?
- Opportunities for EPC Infrastructure Companies in Non-Renewable Energy
In the non-renewable energy space, there are 20 projects worth INR 94185 crores under conceptualization. There are 20 non-renewable energy projects worth INR 35659 crores under development. Further, there are 39 projects worth INR 215000 crores which are under implementation.
- Opportunities for EPC Infrastructure Companies in Renewable Energy
In the renewable energy space, there are 17 projects worth INR 18305 crores under conceptualization in the National Infrastructure Pipeline. Further, there are 54 projects worth INR 1152000 crores under development and 73 projects worth INR 176000 crores under implementation.
- Opportunities for EPC Infrastructure Companies in Irrigation
The National Infrastructure Pipeline has 75 projects worth INR 267000 crores under conceptualization in the irrigation space. Further there are 100 projects worth INR 121000 crores under development and 319 projects worth INR 692000 crores under implementation.
- Opportunities for EPC Infrastructure Companies in Waste Management
There are 20 projects worth INR 23857 crores under conceptualization in the waste management space under the auspices of the National Infrastructure Pipeline. Moreover, there are 78 projects worth INR 325000 crores under development and 339 projects worth INR 455000 crores under implementation.
What Supply Chain Solutions Do EPC Infrastructure Companies Need to Leverage Opportunities in the Utilities Sector?
- Granular Approach Towards Custom Manufacturing and Fabrication
As we continue to build infrastructure assets for energy (renewable and non-renewable), irrigation, drinking water, and waste management, EPC infrastructure enterprises are demanding greater throughput of custom manufactured structures.
Typically, large custom manufactured structures are prone to risks of fitment issues. There are also issues of misalignment with specifications mentioned in the design & drawing that can adversely impact the quality of the infrastructure asset and user experience.
It is critical to bulk-break the requirement of a large-sized fabricated structure into small components. Bulk-breaking a project into smaller components offers several benefits. First, it allows for workload distribution among workshops. Second, it allows precision engineering with the existing set of resources. Third, a granular approach to custom manufacturing enables agile quality assurance and greater probability of course correction.
- Agile Procurement for Transmission & Distribution Projects
As India rushes to achieve its net zero emission milestones, the energy sector is poised for major changes. Independent power producers are already demanding faster execution of projects from subcontractors.
A significant consequence of the increase in demand for faster execution of energy projects is the need to fast-track procurement. Be it module mounting structures, balance of supplies, or construction raw materials like TMT steel bar, there is a need to cut slack across the supply chain journey.
Some of the ways to cut slack without compromising on quality and costs include the use of digital procurement solutions, fintech solutions for on-demand credit, and digital project management for fabrication. Business process reengineering methods like vendor consolidation, freight consolidation, and robotic process automation for non-strategic tasks.
- Credit Support and Payment Cycle Standardization for Suppliers
A significant barrier to the agile execution of infrastructure projects is the variability of payment cycles. The absence or lack of on-demand credit support for suppliers increases the turnaround time of order-to-delivery cycles.
One way to reduce the order-to-delivery cycle is to standardize the payment cycle and credit terms. Any deviation from the established timelines for accounts receivable should be mapped to on-demand credit support against a cost-of-credit.
The treasury in such cases may be the EPC project developer or the sub-contractor of the infrastructure project. Advantages of early payments to the EPC project developer or subcontractor include faster execution of purchase orders, fast-tracking of project execution, and incentives from government agencies for before-time completion.
Here’s a use case on how standardization of credit terms and working capital support can enable faster annual turnover growth of EPC project developers in the infrastructure sector in India.
- Pan- India Site Aggregation for Multi-Site Infrastructure Projects in the Operations Stages
Several infrastructure companies, especially in the utilities sub-sector organize their supplier bases on the conventional wisdom of ‘category expertise’. It leads infrastructure companies into relying on at least one supplier per category.
How does the category expertise led supplier selection and procurement affect infrastructure projects?
First, individual suppliers are responsible for the quality, cost, and on-time delivery of their respective categories only.
Corporate leaders of infrastructure companies are however accountable for completing one or more projects on time, not for completing one or more tasks on time.
Second, there are several tasks and resources in the supply chain that cross each other at multiple junctures in the operational stage of infrastructure projects. Individual suppliers are not accountable for mapping resource and task dependencies of an infrastructure company.
At any point in time, a large infrastructure company in the bracket of an annual turnover of INR 7000 crores or more, has not just one, but multiple projects going on at the same time.
Vendor consolidation at each project site makes one procurement partner accountable for the on-time completion of the entire project. Further, a pan-India site aggregation model for multiple infrastructure project sites puts the responsibility of the on-time completion of several projects on the shoulders of one procurement partner.
However, pan India site aggregation for multiple infrastructure projects can work only when the following thumb rules are satisfied.
First, the pan India procurement partner needs to have a very large-scale catalog of categories and SKUs.
Second, the procurement partner must have a digitally integrated supply chain ecosystem of several suppliers to enable fast allocation of resources, purchase orders, and logistics.
Third, the procurement partner must have a thorough understanding of the bill of quantities and an approved vendor list for each project.
Further, the procurement partner must be willing to sign on the dotted lines of SLAs as per the construction schedule and map the task and resource dependencies of suppliers as per the task and resource dependencies of the infrastructure company.
Here’s a successful use case of pan India site aggregation in the utilities sub-sector by a waste management EPC enterprise across 75 sites.
The Catalog for EPC Project Developers and Sub-Contractors That Are Building India’s Utilities Infrastructure
Moglix offers a comprehensive catalog of construction raw materials procurement, indirect procurement, and custom manufacturing solutions to EPC project developers and sub-contractors.
To know more about opportunities in the utilities sub-sector in India’s National Infrastructure Pipeline, download our e-book “Building India: The Infrastructure We Aspire for and the Supply Chain We Need, Second Edition.”
40 key Industrial Valve terms that you should know
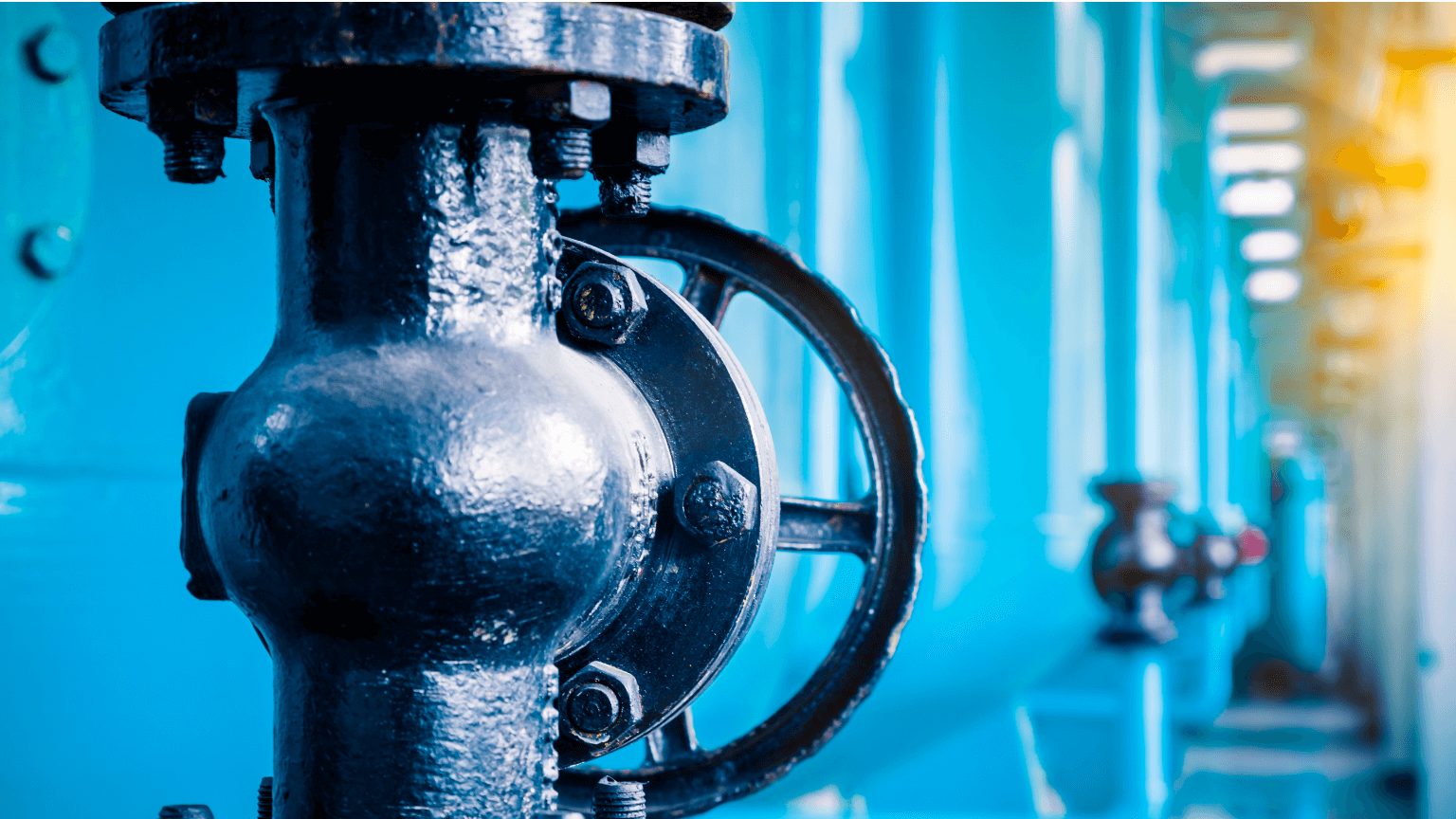
40 key Industrial Valve terms that you should know
Industrial valves are essential components in controlling the flow of fluids within various industries. Understanding the terminology associated with industrial valves is crucial for effectively communicating, selecting, and operating these vital devices. In this comprehensive guide, we will touch upon the key terminologies related to industrial valves, shedding light on their definitions and significance.
- Valve: A device used to control the flow of fluids (liquids, gases, or slurries) through a piping system by opening, closing, or partially obstructing the passage.
- Ball valve: A type of valve with a ball-shaped disc that rotates to control the flow.
- Gate valve: A valve with a flat or wedge-shaped gate that moves up or down to control the flow.
- Globe valve: A valve with a disc that moves linearly to control the flow, typically used for throttling applications.
- Butterfly valve: A valve with a rotating disc in the shape of a butterfly that controls the flow.
- Check valve: A valve that allows fluid flow in one direction and prevents backflow in the opposite direction.
- Smart valve: A valve equipped with sensors, actuators, and communication capabilities, allowing for remote monitoring, control, and integration into digital systems for enhanced performance and diagnostics.
- Actuator: A mechanism that operates the valve, converting an input signal into a physical motion to open or close the valve.
- Flow rate: The volume of fluid passing through a valve per unit of time, typically measured in gallons per minute (GPM) or cubic meters per hour (m³/h).
- Pressure drop: The decrease in pressure across a valve caused by flow resistance. It is the difference between the pressure upstream and downstream of the valve.
- Trim: The internal components of a valve that come into contact with the flowing fluid, including the disc, seat, stem, and other sealing elements.
- Bonnet: The top portion of a valve that houses the stem and packing, providing a protective enclosure and sealing against leaks.
- Seat: The sealing surface inside the valve where the disc comes into contact to provide shutoff and control the flow.
- Disc: The movable part of the valve that controls the flow by opening or closing against the seat.
- Body: The main casing or housing of the valve that contains the internal components and provides the inlet and outlet connections.
- Cv (Flow Coefficient): A numerical value representing the flow capacity of a valve, indicating the flow rate of water in gallons per minute (GPM) at a specified pressure drop across the valve.
- Stem: The elongated shaft that connects the actuator to the disc or other closure element, transmitting the motion to open or close the valve.
- Stem packing: The material used to seal the area around the stem where it passes through the valve bonnet, preventing leakage.
- Trim materials: The materials used for the internal components of the valve, such as the disc, seat, and stem, selected based on the fluid properties and operating conditions.
- Leakage class: A classification system that defines the allowable level of leakage through a closed valve, typically specified as per industry standards (e.g., API 598).
- Valve size: The nominal size of the valve, which refers to the diameter of the inlet/outlet connections or the internal flow passage.
- Valve positioner: A device used to precisely control the position of the valve actuator, ensuring accurate and reliable valve operation.
- Valve types: Different categories of valves based on their design and operation, such as gate valves, globe valves, ball valves, butterfly valves, plug valves, and check valves.
- Multi-turn valve: A valve that requires multiple rotations of the stem to fully open or close the valve, typically used for isolation or throttling applications.
- Quarter-turn valve: A valve that requires only a quarter turn of the stem to fully open or close the valve, commonly used for quick shut-off or on/off applications.
- Deadband: The range of control signal variation that does not produce any change in valve position or flow rate.
- Anti-cavitation: Measures taken to prevent or minimize the formation and damage caused by cavitation, which occurs when the pressure of a fluid drops below its vapor pressure and then rapidly rises.
- Fail-safe: A feature or mechanism in a valve that ensures it returns to a specified position (e.g., fully open or fully closed) in the event of power loss or actuator failure.
- Pressure rating: The maximum pressure that a valve can withstand without failure, typically expressed in pounds per square inch (psi) or bar.
- End connections: The type of connections at the valve’s inlet and outlet, such as threaded, flanged, welded, or socket-welded, which determine how the valve is connected to the piping system.
- Seat leakage: The amount of fluid that can pass through the closed valve, typically measured in drops per minute, and categorized into different classes based on acceptable leakage levels.
- Trim characteristic: The relationship between the valve position (e.g., stem travel) and the resulting flow rate, which can be linear, equal percentage, or modified equal percentage.
- Cavitation: The formation and collapse of vapor bubbles in a flowing liquid due to localized low-pressure zones, causing erosion and damage to valve components.
- Erosion: The gradual wear and removal of valve materials caused by the impact of high-velocity fluid flow, particularly in applications with abrasive or corrosive fluids.
- Fouling: The accumulation of unwanted deposits or substances on the internal surfaces of the valve, which can affect its performance and efficiency.
- Low flow trim: Additional components or modifications in the valve design to improve control accuracy and stability at low flow rates.
- Lockout/tagout: Safety procedures followed to isolate and lockout valves during maintenance or repair activities to prevent accidental operation and ensure the safety of personnel.
- Valve sizing: The process of determining the appropriate valve size based on the required flow rate, pressure drop, and other factors to achieve optimal system performance.
- Anti-static design: Measures taken to prevent the build-up of static electricity on the valve, reducing the risk of sparks in potentially hazardous environments.
- Blowdown: The process of reducing the pressure within a valve or piping system by allowing a controlled discharge of fluid, typically used to release pressure before maintenance or to prevent over-pressure situations
Familiarity with the terminologies related to industrial valves is vital for effective communication and understanding within the industry. By grasping these terms, professionals in the field can enhance their knowledge and make informed decisions when it comes to selecting, operating, and maintaining industrial valves. Like any industry industrial valves is also an evolving industry, terms mentioned here might change and evolve as and when innovations in this industries happen with respect to process, raw materials etc. Stay curious, explore further, and keep building your expertise in this critical field of fluid control.
At Moglix you have access to the most comprehensive range industrial valve solutions coupled with a team of industry experts who understand your requirement and customise and reverse engineer solutions that justify your requirements, budgets and timelines
Valve Failure Analysis-Investigating Causes, Impacts, and Preventive Measures
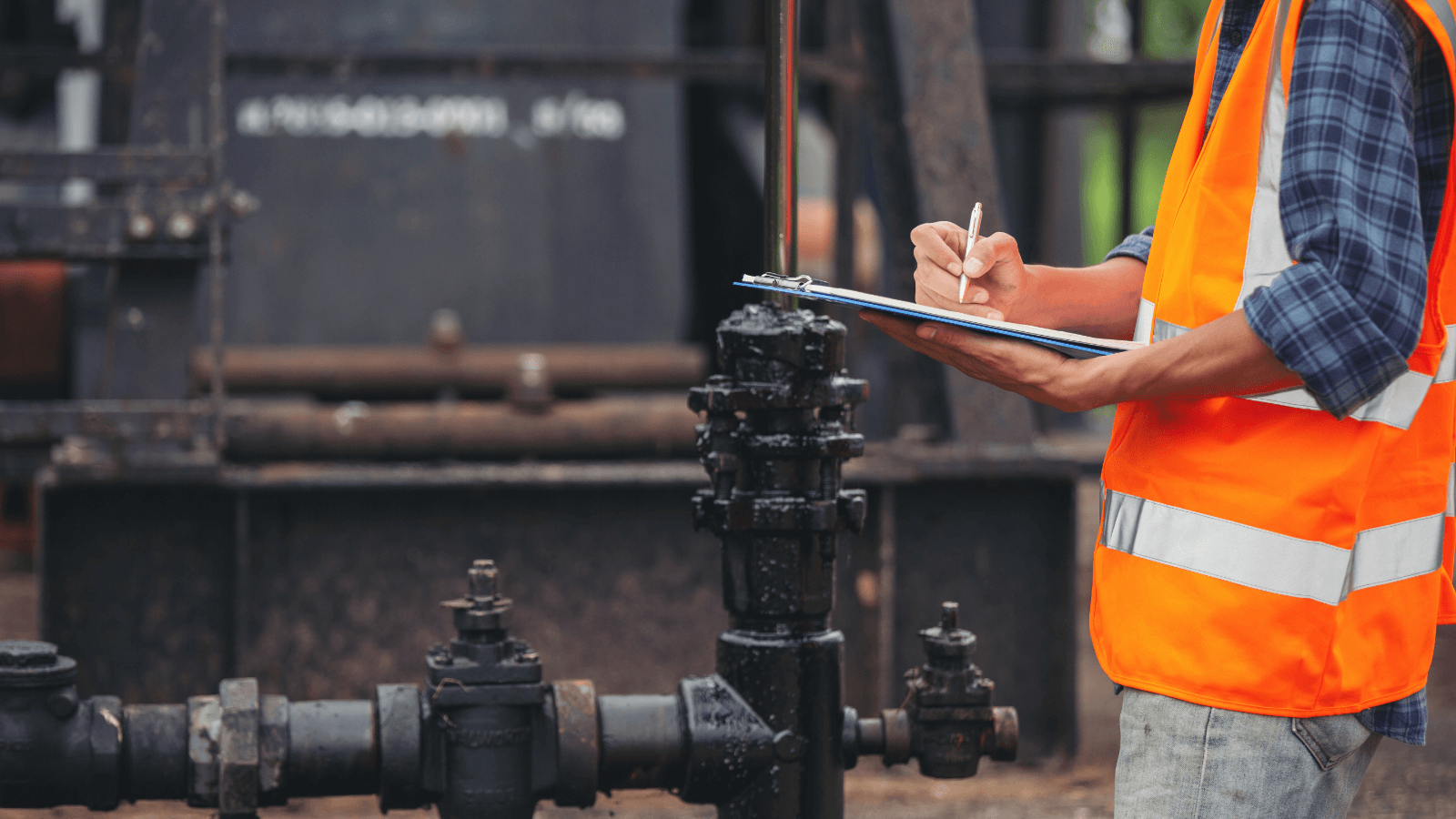
Valve Failure Analysis-Investigating Causes, Impacts, and Preventive Measures
Valves are critical components in industrial processes, regulating the flow of fluids and ensuring efficient operations. However, valve failures can have severe consequences, ranging from safety hazards to production disruptions and financial losses. This blog deals with the causes and impacts of valve failures and explores preventive measures to minimize their occurrence.
Understanding Valve Failure
Valve failures come in various forms, including leakage, blockage, malfunctions, and structural failures. According to one industry report, approximately 40% of valve failures are attributed to internal leakage, while 25% result from corrosion and erosion. The most common causes of valve failure include wear and tear, corrosion, improper installation, operational errors, and fluid conditions. It is estimated that around 80% of valve failures occur due to insufficient maintenance and poor operating practices. Early detection and analysis of valve failures are crucial to prevent more severe incidents and mitigate their impacts.
Impacts of Valve Failures
The impacts of valve failures extend beyond immediate safety concerns. A study found that valve failures can result in an average production loss of $30,000 per hour. Moreover, environmental risks, increased maintenance costs, and reputational damage are additional consequences that industries face when dealing with valve failures.
Valve Failure Analysis Techniques
To identify the root causes of valve failures, comprehensive analysis techniques are employed. These include
- Visual Inspection – involves examining the failed valve to identify visible signs of damage, such as corrosion, erosion, mechanical deformation, or wear. This initial assessment helps in determining if the failure was due to external factors or internal issues.
- Non-destructive testing (NDT) – methods are crucial for evaluating the integrity of valves without causing further damage. Techniques like ultrasonic testing, magnetic particle inspection, and liquid penetrant testing are employed to detect defects, cracks, or flaws within the valve structure.
- Metallurgical analysis – involves examining the valve material under a microscope to identify any metallurgical abnormalities or inconsistencies that may have contributed to the failure. This analysis helps in understanding the valve’s material properties, including strength, composition, and heat treatment.
- Fluid analysis – is employed to evaluate the fluid characteristics and their impact on valve performance. It involves examining fluid samples for contaminants, acidity, viscosity, or any other factors that may have led to valve degradation or malfunction.
- Failure mode and effects analysis (FMEA) – is a systematic approach to identify potential failure modes and their effects on valve performance. It involves evaluating various failure scenarios, their severity, and the likelihood of occurrence. This analysis aids in determining preventive measures to mitigate future failures.
In addition to these techniques, data logging, computer-aided design (CAD) simulations, and expert consultations are also utilized to enhance valve failure analysis.
Valve failure analysis is a crucial process for investigating the causes, impacts, and preventive measures related to valve failures. By employing techniques such as visual inspection, non-destructive testing, and failure mode analysis, industries gain valuable insights to enhance operational efficiency and safety. Implementing targeted preventive measures based on these analyses enables organizations to minimize disruptions, optimize maintenance practices, and improve valve system longevity. Collaboration and knowledge-sharing among industry professionals further advance valve failure analysis practices. Investing in this process ensures reliable operations and long-term success in various industries.
The Now and the Next of Building India’s Logistics and Transportation Sector Under the National Infrastructure Pipeline

The Now and the Next of Building India’s Logistics and Transportation Sector Under the National Infrastructure Pipeline
What Has Been the Progress in the Construction of Transport and Logistics Infrastructure in India till Now in 2023?
As of 2023, India has witnessed significant progress in the construction of transport and logistics infrastructure. The government has undertaken various initiatives to enhance connectivity and facilitate efficient movement of goods and people across the country.
Several notable developments have taken place recently. One of them is the construction of expressways, like the Delhi-Mumbai Expressway and the Chennai-Bengaluru Expressway. These expressways are built with the aim of decreasing travel time and to increase trade.
The expansion of the railway network, including dedicated freight corridors, has improved cargo transportation capabilities. Additionally, major ports have undergone expansion, enabling maritime trade.
The Bharatmala and Sagarmala projects have been implemented. This has increased the development of road and port infrastructure. This, in turn, has improved connectivity and stimulated economic growth.
What Are the Major Opportunities for EPC Infrastructure Companies in Transport and Logistics Systems Construction?
- Opportunities for EPC infrastructure companies in the construction of roads & bridges
There are 389 projects worth INR 382000 crores under conceptualization in the roads & bridges sub sector. There are 1210 projects worth INR 1128000 crores under development. Further there are 1580 projects worth INR 1478000 crores.
- Opportunities for EPC infrastructure companies in the construction of airports
In the airports and civil aviation sub-sector, there are 30 projects worth INR 37372 crores under conceptualization. Further, there are 13 projects worth INR 30709 crores under development and 70 projects worth INR 80781 crores under implementation.
- Opportunities for EPC infrastructure companies in the construction of ports & terminals
The ports & terminals sub-sector in India has 8 projects worth INR 3696 crores under conceptualization. There are 18 projects valued at INR 23651 crores in the ports & terminals sub-sector which are under development. Moreover, there are another 35 projects worth INR 19803 crores which are under implementation.
- Opportunities for EPC infrastructure companies in railways
The railway sub-sector has experienced several local manufacturing and sourcing projects in the last few years. These projects are in line with the Make in India policy initiative.
The most noteworthy accomplishment in Indian railways due to local manufacturing is the launch of the Vande Bharat express trains.
There are 69 projects worth INR 203000 crores under conceptualization and 96 projects worth INR 118603 crores under development. Further there are 74 projects of INR 1068000 crores under implementation.
- Opportunities for EPC infrastructure companies in building urban public transport systems
The public transport systems sub-sector in India has seen a massive spur in activity in recent years. The Government of India has set an ambitious goal. They plan to build 1000 kilometers of metro railway services across nine cities by 2030. This will revolutionize the way people travel in India.
There are 16 projects worth INR 15748 crores under conceptualization in the urban public transport systems sector. There are another 11 projects worth INR 67924 crores under development and 30 projects worth INR 416000 crores.
- Opportunities for EPC infrastructure companies in bulk material transportation systems
In recent times the Government of India has taken a slew of initiatives to build infrastructure for bulk material transportation. The most noteworthy projects in this sub-sector include the Eastern Dedicated Freight Corridor and the Western Dedicated Freight Corridor.
There are 80 projects in the bulk material transportation sub-sector worth INR 28394 crores currently being conceptualized. Additionally, 57 projects worth INR 89307 crores are in the process of development. Further there are 14 projects worth INR 17742 crores under implementation.
What Supply Chain Solutions Do EPC Infrastructure Companies Need to Leverage Opportunities in the Logistics & Transport Sector?
- Single Source of Truth for Collaboration Among All Stakeholders in the Supply Chain
EPC infrastructure projects in the logistics & transportation sub-sector have many moving parts. From conceptualization of the project to its commissioning, all stakeholders in the supply chain must rely on a single source of truth for material flow, work-in-progress, fund flow, and data flow.
These stakeholders include the EPC project developer, sub-contractor, raw materials and machinery supplier, and lender.
End-to-end digital transformation of the supply chain can enable stakeholders to identify congestion points, reasons behind the congestion, and take quick action to unclog bottleneck areas.
Here’s a use case on an award-winning digital procurement supply chain transformation from an EPC company which is part of a salt-to-sky conglomerate.
- Seamless Synchronization Across Logistics, Payment, and Delivery
Once all stakeholders in the supply chain are on the same page, the next step is to enable decision making and action. This calls for seamless synchronization among multiple processes in the procure-to-pay cycle.
These processes include the issue of purchase orders, requests for quote, onsite delivery of construction raw materials, consumables and MRO items, and finally, payments,
Procure-to-pay automation and integration can enable all stakeholders to make decisions, act fast, and execute the project as per the construction schedule.
- Agile Procurement of Construction Raw Materials and MRO Items as per the Bill of Quantities
40% of road projects face delays in project execution and construction, as per MoSPI reports. In 2023, the speed of national highway construction in India has improved to 24.14 KM per day. However, there is plenty of room for improvement.
A significant speed breaker in the logistics & transportation sector is the purchase requisition to purchase order (PR-to-PO) process. In some EPC infrastructure companies that still rely on manual processes, the PR-to-PO cycle time is 4 days.
Catalog-based buying can reduce the PR-to-PO cycle time for purchase of construction raw materials and MRO items to 3 minutes. What does that mean?
With catalog-based buying an EPC road developer can save 4 days. At the current rate of road construction, it can build an additional 96.56 KM.
For a road development project of 1 KM aggregate lead in the state of Uttar Pradesh, with greenfield alignment of 2 lanes +PS (BC, DBM, WMM & GSB), it can lead to additional revenue of INR 3.44 crores. Here’s a use-case on the agile procurement of steel TMT bars and AAC blocks with a turnaround time of 4 days.
- Alignment of Parts and Components as Per GAD/GFC Drawings
Another pain point faced by EPC infrastructure companies in the logistics & transportation sub-sector is the alignment of parts and components. There is very little margin for error in heavy, equipment, and general fabrication.
A solution that can serve EPC companies well is a digital project management solution. It allows users to track work-in-progress for fabrication requirements for roads, bridges, airports, tunnels, and ports.
It is important to lock the engineering and drawing and educate suppliers on the SLAs of a fabrication project from the word “go”.
A digital project management solution can enable EPC companies to monitor SLAs for quality metrics as per GAD/GFC drawings.
Here’s a use case on the alignment of parts as per GAD/GFC drawings for the fabrication of piers and pier cap shutterings from India’s first bullet train project on the Mumbai-Ahmedabad route.
- Agile Best Price Discovery for Procurement of Construction Raw Materials and MRO Items
It is impossible for EPC companies to do away with spot buying, especially for the purchase of construction raw materials.
Major reasons for spot buying include high inventory carrying costs and the balance sheet impact of a delta due to a sudden change in the cost of capital.
A solution that can enable ease of doing business for infrastructure project developers and subcontractors working on construction projects for roads, bridges, tunnels, airports, and ports is an RFQ automation tool.
An RFQ automation tool allows users to request quotes of multiple line items as per all attributes in the bill of quantities, at one go.
It is even better if the RFQ automation tool can give instant quotes to users. It saves significant time on the best price discovery.
Here’s a use-case on agile best price discovery of structural steel by a leading EPC road developer in India.
- Granular Manufacturing Processes for Quality Fabricated Structures
What happens when fabricators build a large structure at one go? While it may appear to save time and costs on paper, the ground reality is different.
It is always safer to bulk break a large heavy fabrication project into a sum of parts. Granular manufacturing allows fabricators better monitoring of fabricated structures and easier course correction. The probability and costs of re-work are lower.
Here’s a use-case on a granular approach to manufacturing of pre-engineered buildings from 150 years+ old civil construction company in India.
The Catalog for EPC Project Developers and Sub-Contractors That Are Building India’s Logistics & Transportation Infrastructure
Moglix offers a comprehensive catalog of construction raw materials procurement, indirect procurement, and custom manufacturing solutions to EPC project developers and sub-contractors.
To know more about opportunities in the logistics & transportation sub-sector in India’s National Infrastructure Pipeline, download our e-book “Building India: The Infrastructure We Aspire for and the Supply Chain We Need, Second Edition.”
PPE Chronicles: Ensuring Chemical Industry Safety Through PPE Effective Programs
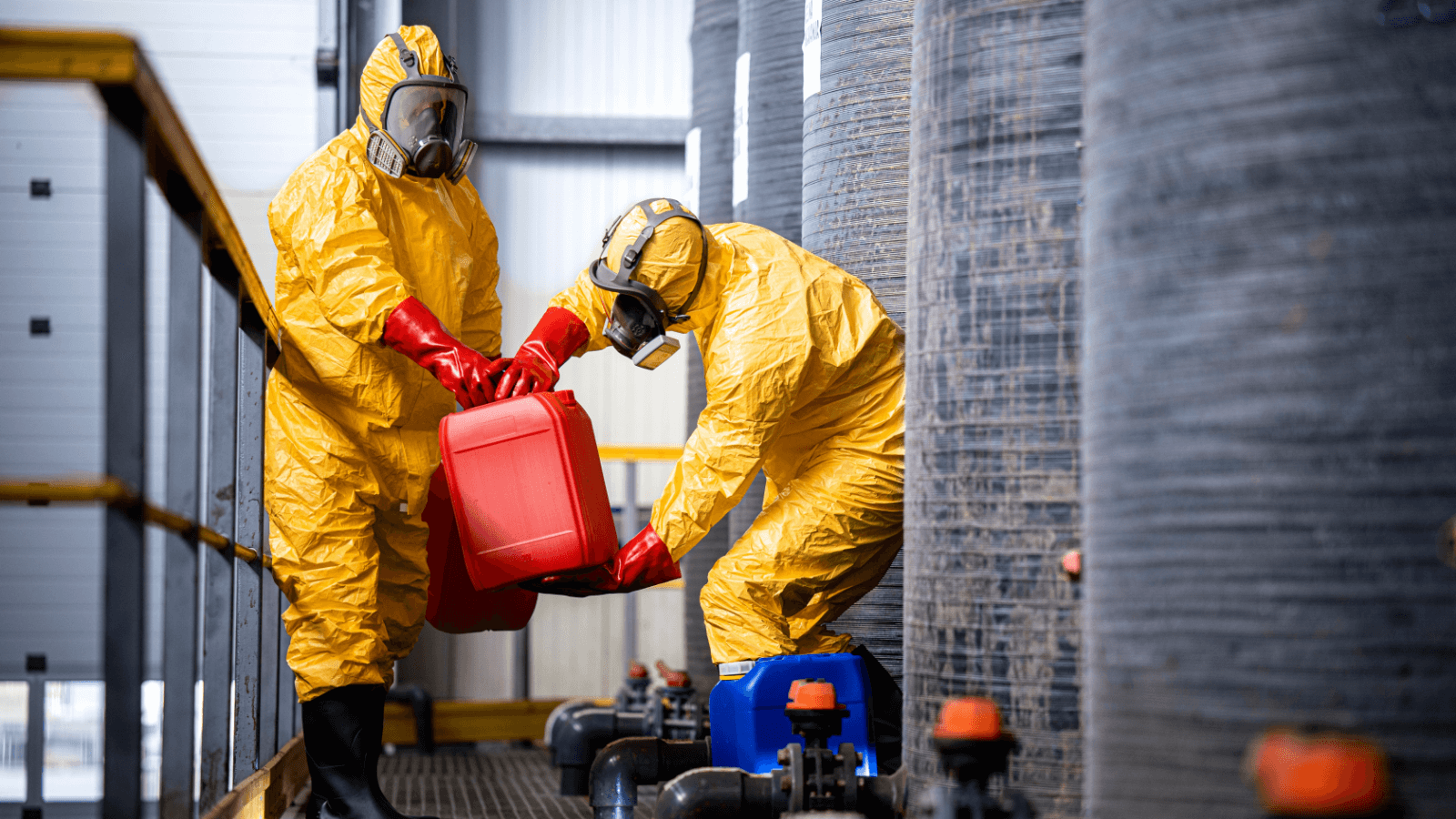
PPE Chronicles: Ensuring Chemical Industry Safety Through PPE Effective Programs
Worker safety is paramount in any industry, especially in the chemical industry. Personal Protective Equipment (PPE) plays a vital role in safeguarding workers from potential hazards and minimizing the risks associated with chemical exposures. However, it is crucial to evaluate the effectiveness of PPE programs to ensure optimal protection.
The Role of PPE in the Chemical Industry:
Chemical manufacturing and handling processes pose various hazards, including chemical spills, fumes, and corrosive substances. PPE acts as a critical line of defense, reducing the likelihood of injuries and long-term health effects. According to the Occupational Safety and Health Administration (OSHA), wearing appropriate PPE can reduce the risk of chemical-related injuries by 90%.
Understanding the Evaluation Process
Evaluating PPE programs involves analyzing several key elements. Incident analysis allows us to assess the effectiveness of PPE in mitigating or preventing accidents. Compliance tracking helps ensure that workers consistently adhere to PPE protocols, minimizing the chances of exposure. Gathering feedback from workers about their experiences with PPE provides valuable insights for improvement.
Assessing PPE Compliance and User Feedback:
Tracking and monitoring PPE compliance is crucial for evaluating program effectiveness. As per study companies with high compliance rates had significantly lower injury rates compared to those with poor compliance. Additionally, gathering feedback from workers through surveys and interviews helps identify areas for improvement, such as comfort, fit, and ease of use.
Analyzing Incidents and Accidents:
Examining past incidents and accidents helps us understand the role of PPE in preventing or mitigating injuries. Statistical data from the Chemical Safety Board showed that in 75% of chemical accidents resulting in severe injuries, the workers involved either did not wear PPE or wore inadequate protection. This highlights the critical importance of proper PPE usage in preventing accidents and reducing their severity.
Key Performance Indicators (KPIs) for Evaluation:
To measure the effectiveness of PPE programs, specific KPIs can be used. Incident rates, such as the number of chemical-related injuries or near misses, serve as valuable indicators. Conducting regular worker satisfaction surveys can provide insights into the perceived effectiveness and usability of PPE. These metrics help gauge the success of PPE programs and identify areas that require attention.
Continuous Improvement Strategies:
Continuous improvement is essential for enhancing PPE programs. Incorporating worker feedback, conducting regular training sessions, and staying updated on industry best practices are effective strategies. Initiatives like an annual PPE training program can significantly reduce PPE related incidents, demonstrating the value of ongoing improvement efforts.
Cost-Benefit Analysis:
Investing in PPE programs incurs costs, but the benefits outweigh them. According to the National Safety Council, the average cost of a chemical-related injury in the workplace is $40,000. Comparatively, the cost of providing appropriate PPE and implementing an effective program is significantly lower. By preventing accidents and reducing injuries, PPE programs result in long-term cost savings for companies.
Evaluating the effectiveness of PPE programs is vital to ensure the safety of workers in the chemical industry. Through incident analysis, compliance tracking, user feedback, and continuous improvement strategies, companies can optimize their PPE programs. By investing in worker safety and utilizing effective PPE, organizations can create safer working environments and prevent potentially devastating accidents. Also, it is an ongoing process, and staying proactive is key to protecting workers and minimizing risks in the chemical industry. At Moglix, you have access to the most comprehensive range of safety supplies and solutions. You can find a range of PPE solutions specifically designed for chemical industry. Contact us today and partner with us to build a safer environment.
Leveraging Technology for Streamlined Compliance Tracking in PPE Programs
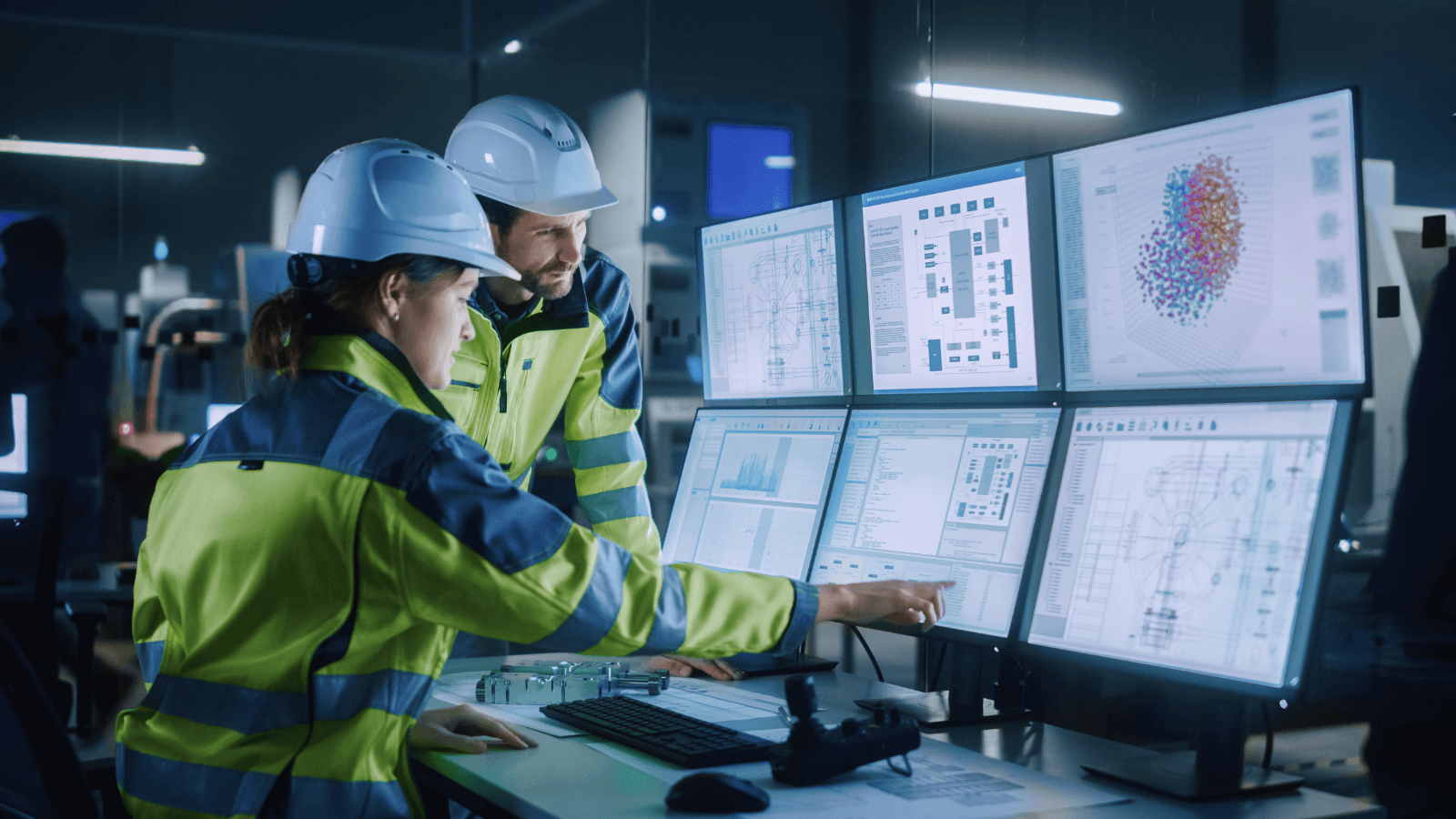
Leveraging Technology for Streamlined Compliance Tracking in PPE Programs
Personal protective equipment (PPE) is essential for protecting workers from hazards in the workplace. However, ensuring that PPE is used correctly and consistently can be a challenge. This is where compliance tracking comes in. Compliance tracking is the process of monitoring and documenting the use of PPE to ensure that it is being used correctly and consistently.
There are a number of ways to implement a compliance tracking system. One option is to use a paper-based system. This involves creating and maintaining paper records of PPE use. However, paper-based systems can be time-consuming and inefficient. They can also be difficult to maintain and keep up-to-date. When it comes to compliance tracking in PPE programs, leveraging technology can be a game-changer. By adopting the right tools and software, organizations can streamline their compliance efforts, improve accuracy, save time, and ensure a safer work environment.
Technology-based systems can automate many of the tasks involved in compliance tracking, such as data entry and reporting. This can save time and resources, and can help to ensure that compliance tracking is more accurate and efficient. There are a number of different technology-based compliance tracking systems available. When choosing a system, it is important to consider the specific needs of your organization. Some factors to consider include:
- The size of your organization
- The types of hazards your workers face
- The number of employees who need to use PPE
- Your budget
Why Automate?
Let’s understand various ways technology can be utilized to achieve streamlined compliance tracking in PPE programs.
Automated Data Collection and Reporting:
Technology allows for the automation of data collection processes, eliminating the need for manual recordkeeping. Organizations can use barcode scanning, RFID tags, or mobile apps to track PPE usage, inspections, and maintenance. This automated data collection enables real-time tracking and generates comprehensive reports that provide insights into compliance status, usage patterns, and potential areas for improvement.
Inventory Management Systems:
Managing PPE inventory can be a daunting task, especially for organizations with large-scale operations. Implementing an inventory management system can simplify this process. These systems use technology to track PPE stock levels, monitor expiration dates, and generate alerts for restocking. By ensuring an adequate supply of PPE at all times, organizations can maintain compliance and minimize the risk of employees working without proper protection.
Training and Certification Platforms:
Technology offers innovative solutions for delivering and tracking employee training and certifications related to PPE. Online training platforms enable employees to access relevant training modules at their convenience, ensuring consistent and standardized training across the organization. These platforms can also track and document employees’ progress, allowing employers to verify compliance with training requirements. At Moglix, we partner with organizations to provide safety solutions that go beyond just procurement of safety supplies. Our understanding of the entire value chain, allows us to focus on factors like Safety audits & End user training, that are often ignored, but important to create a safety culture within any organization.
Mobile Apps for Inspections and Audits:
Mobile applications are powerful tools for conducting inspections and audits related to PPE compliance. Inspectors can use mobile apps to complete checklists, capture photos of equipment and hazards, and record observations in real-time. This approach facilitates efficient data collection, reduces paperwork, and enables immediate corrective actions to address any non-compliance issues identified during inspections.
Integration with Environmental Health and Safety (EHS) Systems:
Integrating compliance tracking technology with existing Environmental Health and Safety (EHS) systems can further streamline PPE programs. By centralizing data and workflows, organizations can achieve a holistic view of safety compliance, including PPE requirements. This integration enables efficient data sharing, analysis, and reporting, leading to better decision-making and continuous improvement of PPE programs.
Incorporating technology into compliance tracking for PPE programs brings numerous benefits to organizations. It enhances data accuracy, saves time, improves efficiency, and ultimately contributes to a safer work environment. By leveraging automated data collection, inventory management systems, training platforms, mobile apps, and integration with EHS systems, organizations can streamline their compliance efforts, reduce risks, and ensure that employees are adequately protected through the proper use of personal protective equipment.
For Moglix safety is more than just safety products. It’s about working together, to analyze and understand all safety options and requirements needed to send your employees home safely. We assess your data and facility, to engineer out hazards, helping you define clear SOPs. We then train your employees through simulated VR training modules to enable easy understanding and acceptance.
Our engagement with you doesn’t stop at just training. Moglix works with safety consultants and safety auditors to help you design proactive and periodic audit plans. Be it electrical, fire, OSHA or wash audit, we have certified professionals who can help you with any type of audit. Safety Simplified
Seamless Excellence: Exploring the Seamless Pipe Manufacturing Process
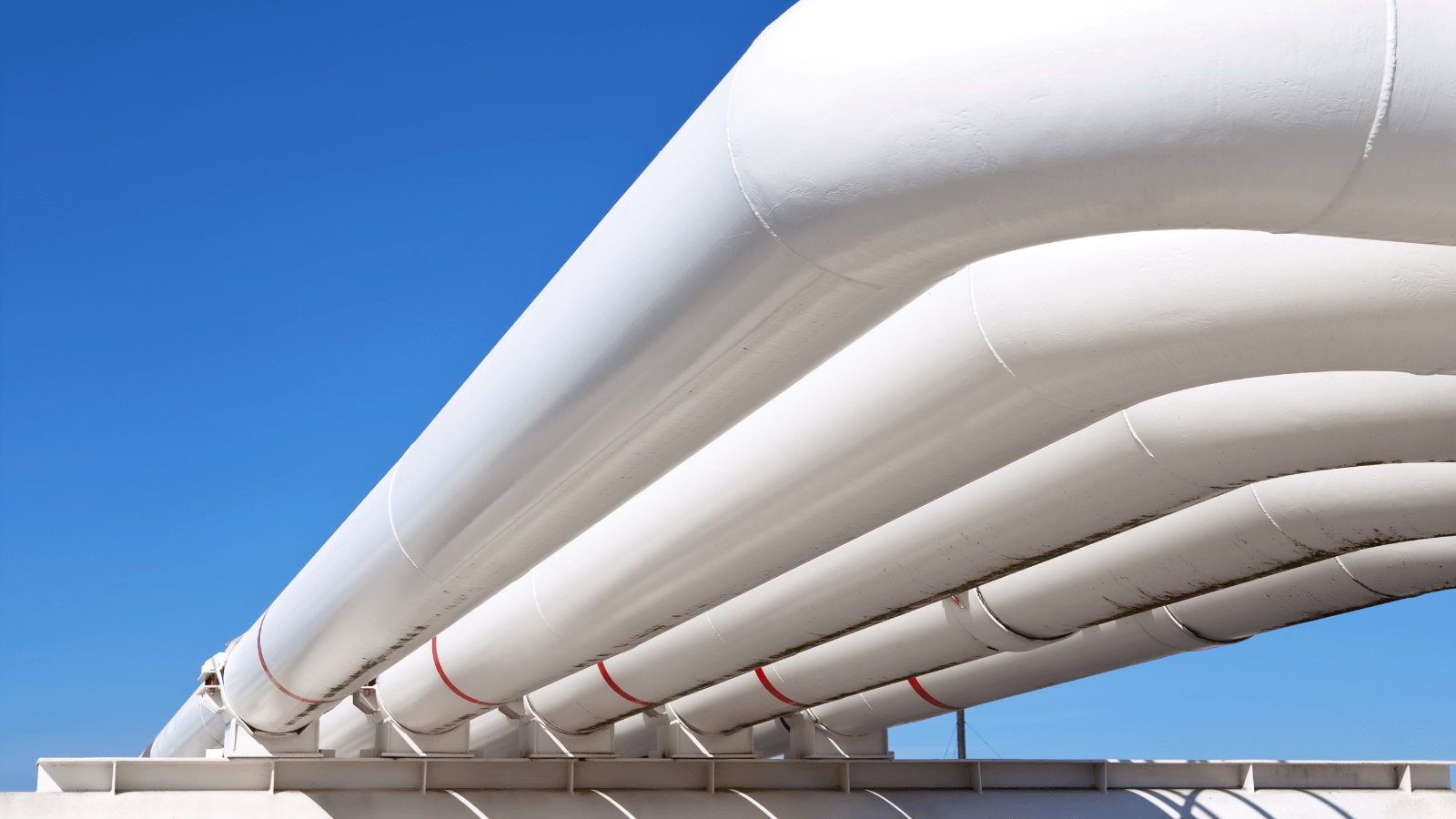
Seamless Excellence: Exploring the Seamless Pipe Manufacturing Process
According to a report by Grand View Research, the global seamless pipe market size is projected to reach USD 114.8 billion by 2028, with a compound annual growth rate (CAGR) of 3.6%. They are known for their superior performance and are free from welding seams, making them stronger and more resistant to pressure and corrosion. They play a crucial role in industries worldwide such as oil and gas, construction, and automotive, providing strength, durability, and reliability. Manufacturing seamless pipes is an intricate process that transforms molten metal into seamless excellence.
Seamless Manufacturing
The manufacturing process of seamless pipes usually involves the following steps:
- Raw Material Selection: High-quality steel billets or solid ingots are carefully chosen as the raw materials for seamless pipes. The selection process ensures that the material meets specific requirements for composition, purity, and structural integrity.
- Heating and Piercing: The selected raw material is heated to a high temperature using a furnace. Once heated, the material is pierced by a piercing mill or a rotary piercing machine to create a hollow cylindrical shape known as a shell.
- Shell Rolling: The pierced shell is then rolled by a mandrel mill or a plug mill. This process reduces the outer diameter and increases the length of the shell while maintaining a consistent wall thickness.
- Sizing: After rolling, the pipe is subjected to a sizing mill. This mill further reduces the diameter and refines the wall thickness to achieve the desired dimensions and tolerances.
- Heat Treatment: Heat treatment is often employed to enhance the mechanical properties and remove residual stresses from the pipe. This involves processes like normalizing, annealing, or quenching and tempering, depending on the specific requirements of the pipe.
- Straightening and Cutting: The pipe undergoes a straightening process to remove any residual curvature and ensure it has a straight and uniform shape. It is then cut to the desired length using either a flying saw or a cutting torch.
- Surface Treatment: The surface of the seamless pipe may be treated to improve corrosion resistance, appearance, or other specific requirements. This can involve processes such as pickling, passivation, or coating.
- Inspection and Testing: The finished seamless pipes undergo rigorous inspection and testing to ensure they meet the required quality standards. This can include visual inspection, dimensional checks, non-destructive testing, and mechanical property testing.
Marking and Packaging: The pipes are marked with relevant information, such as size, material, and heat number, for identification purposes. They are then carefully packaged for transportation, storage, and delivery to customers.
From the precise selection of raw materials to the rigorous quality control measures, the seamless pipe manufacturing process demands meticulous attention to detail. By understanding this process, we gain insights into the exceptional qualities and widespread applications of seamless pipes. As industries continue to rely on seamless excellence, their impact on safety, efficiency, and cost savings becomes increasingly evident. At Moglix, we have been working with organisation big and small to help them with industrial pipe procurement. We have the most comprehensive range of certified seamless pipes, from all brands which cater to all budgets. Know More