Key Factors to Consider When Selecting High-Pressure Valves
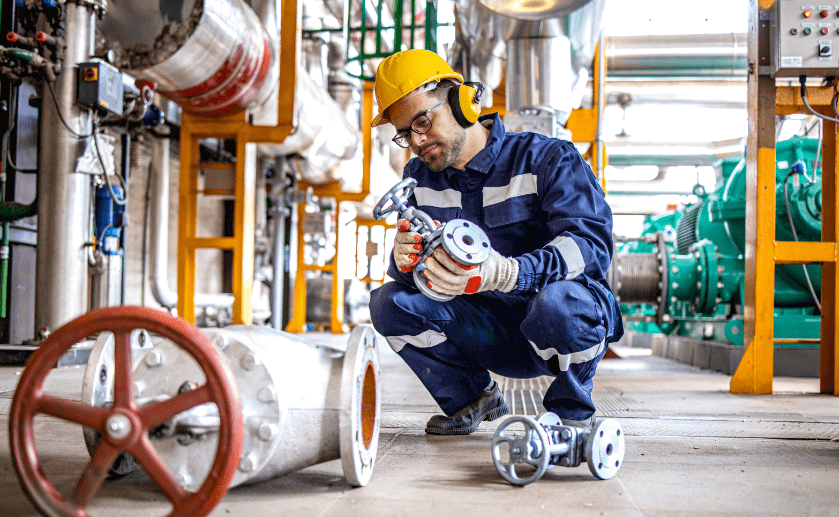
Ever wonder how precise fluid flow management occurs at the core of industrial safety? Particularly in high-pressure situations, valves hold the solution. However, how do you deal with the difficulties of choosing the appropriate valve to guarantee efficiency and safety? You must look for pressure ratings, materials type, valve types, efficiency, and process integrity. This article will touch upon these essential factors to help you learn how to choose high-pressure industrial valves that ensure optimal performance without inviting potential risks.
Different Factors to Consider in High-Pressure Valves
1. Pressure Rating
You must know the ideal pressure the valve needs for a specific application to make the correct selection. High-pressure valves are rated in pounds per square inch (psi) or bar. The value indicates the maximum pressure the valve can withstand safely.
If you underestimate the pressure and the valve is exposed to more pressure than its maximum rating, it can lead to catastrophic failures. Valve failure may cause severe damage, injury, and environmental hazards.
Besides the application pressure requirement, you must consider additional factors like pressure surges that might occur during system operation to determine the pressure rating and choose the valve accordingly.
2. Material Compatibility
High-pressure valves are used to control the fluid pressure. In this regard, the valve material should be compatible with the fluids it will handle. Without chemical compatibility, the fluid may corrode or degrade the valve body and internal components with constant exposure.
Generally, experts consider factors like acidity, alkalinity, and corrosive elements in the fluid to determine the ideal material type for the valve body and o-rings.
High-pressure valves are usually made of forged steel and stainless steel. For extreme environments, such as marine conditions, high-pressure valves are made of bronze.
3. Valve Type
Here is a quick guide to help you understand different types of high-pressure valves and their function within the system.
- Gate valves: Ideal for complete opening or closing the flow to offer minimal pressure drop
- Globe valves: Well-suited for throttling applications to attain precise flow regulation through a screw mechanism
- Ball valves: Provide quick on/off operation with a rotating ball element, suitable for various pressures and fluids
- Check valves: Allow one-way flow to prevent backward flow of the fluid in the system
- Pressure relief valves: Protect the system by automatically releasing excess pressure that exceeds the preset limit
4. Performance Requirements
- Beyond the basic function, several performance factors must be considered during valve selection. Here are some important ones:
- Flow rate: The valve should be able to handle the set volume of fluid without any hassle
- Cycle life: represents the frequency of operation (opening/closing cycles) and directly influences valve durability
- Leakage rate: valves with minimal leakage rate are ideal for critical applications
- Temperature: the valve material should be able to withstand the operating temperature range of the fluid
5. Additional Considerations
If you are operating valves in harsh environments like extreme temperatures, high humidity, or dust, consider valves with weatherproofing or special coatings.
Also, as per safety rules in the industry, high-pressure valves must undergo periodic maintenance. However, while performing maintenance, workers must be equipped with the necessary safety tools and equipment as per the requirements of industrial work safety.
Looking for a qualified high-pressure valve manufacturer and safety equipment supplier?
Partner with Moglix Solutions! Visit our website to learn more.