Complete Guide to Sustainability in Procurement
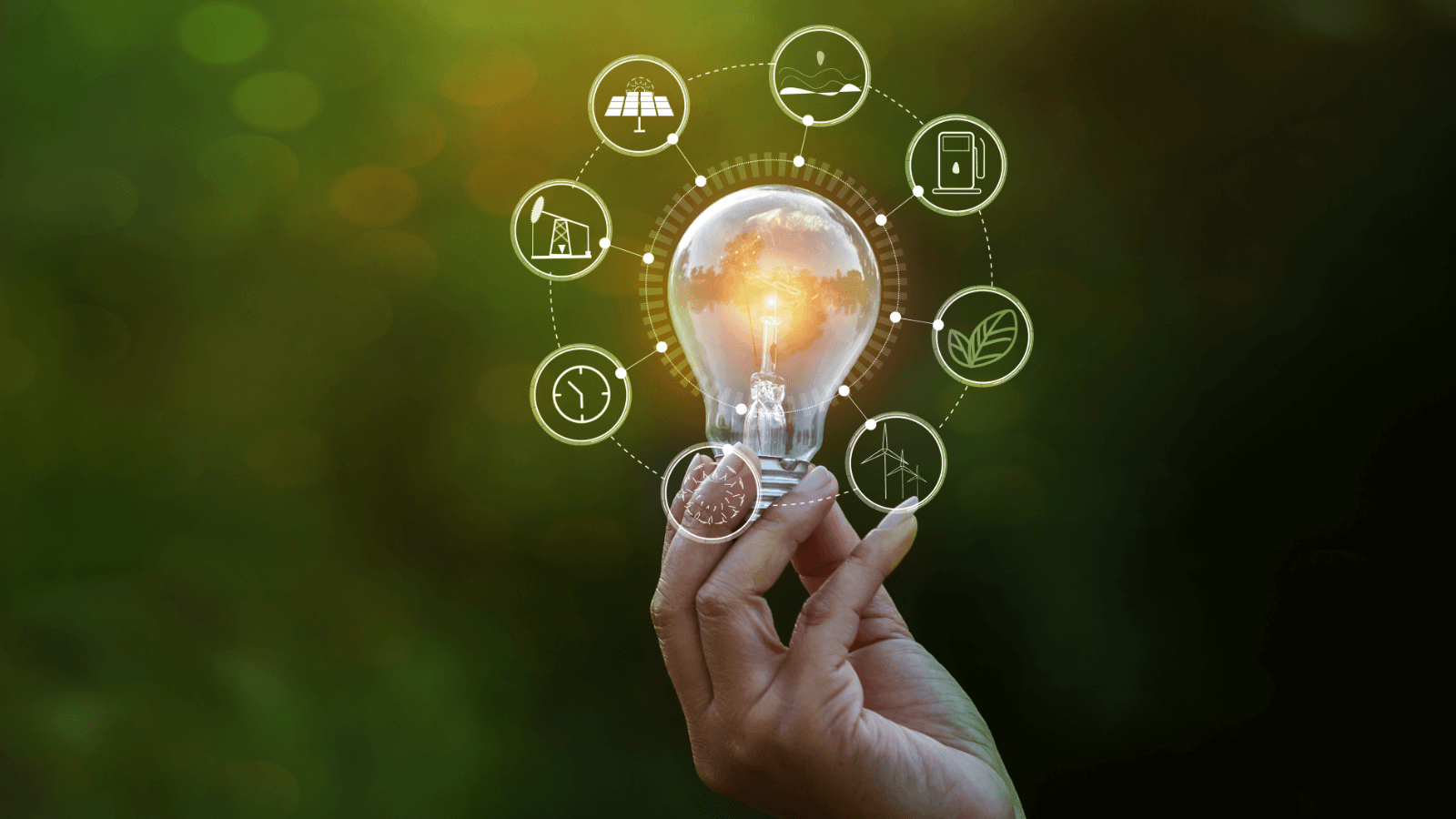
Complete Guide to Sustainability in Procurement
As per a study conducted by Mckinsey, only 20% of the CPOs surveyed said their companies used sustainability as a key criterion to make sourcing decisions. This is far from encouraging because sustainability is the future. Most industry leaders across the globe make the shift towards future-proofing their operations with sustainability at the core. Additionally, an increasing number of organizations are also driving their efforts toward tackling Environment, Social, and Governance (ESG) issues.
Against the backdrop of these developments, sustainability is the way forward for all facets of supply chain management, including procurement. Sustainable practices are crucial for procurement leaders who want to align their strategies with their organization’s overall principles.
With ‘sustainability’ being the buzzword here, let’s understand how MRO procurement can be transformed to accommodate this necessary principle.
Upgrade to Sustainable Procurement with 3 Simple Steps
Procurement is one of the most important functions in an organization’s supply chain. To implement end-to-end sustainability in your organization’s procurement function, it is pivotal to assess the status quo. Furthermore, you must detect the missing links and devise a comprehensive strategy to address these issues.
Here are the steps that you can adopt for a sustainable approach to all aspects of procurement, including MRO categories.
1. Take stock and ascertain the status quo/weigh up and mark the status quo: The first step is assessing where your supply chain stands and ascertaining its ESG impact. Once you have established the status quo, you must identify the elements of the supply chain which can be optimized. You may be faced with several bottlenecks in the process, for instance, the challenges in MRO procurement.
2. Develop a core strategy and plans to implement it: Having established the areas of improvement in the supply chain function, you must move on to the next step. Develop a strategy to incorporate sustainable practices and processes in procurement. This strategy should encompass all the elements of procurement, ranging from supplier selection to data management and visibility.
3. Drive a phased implementation of the sustainable procurement strategy: Implement an organization-wide sustainable approach to procurement in a phased manner, and make course corrections wherever necessary. It is critical to monitor every step of the transition and compare actual results with the planned ones. Subsequently, you must ensure that the necessary rectifications are implemented in a timely manner.
Switch To Sustainable Procurement Now!
Driving a shift from legacy systems in procurement to sustainable practices is a comprehensive undertaking. Therefore, assistance from experts can help streamline the transition. At Moglix, we can help you streamline your procurement function, including MRO procurement. Download our exclusive e-book to get your hands on an exclusive guide to help you nail the procurement game!
Are you looking to transform your procurement function? Send us your business queries at info@moglixbusiness.com.
Digitalization is the next frontier for product procurement
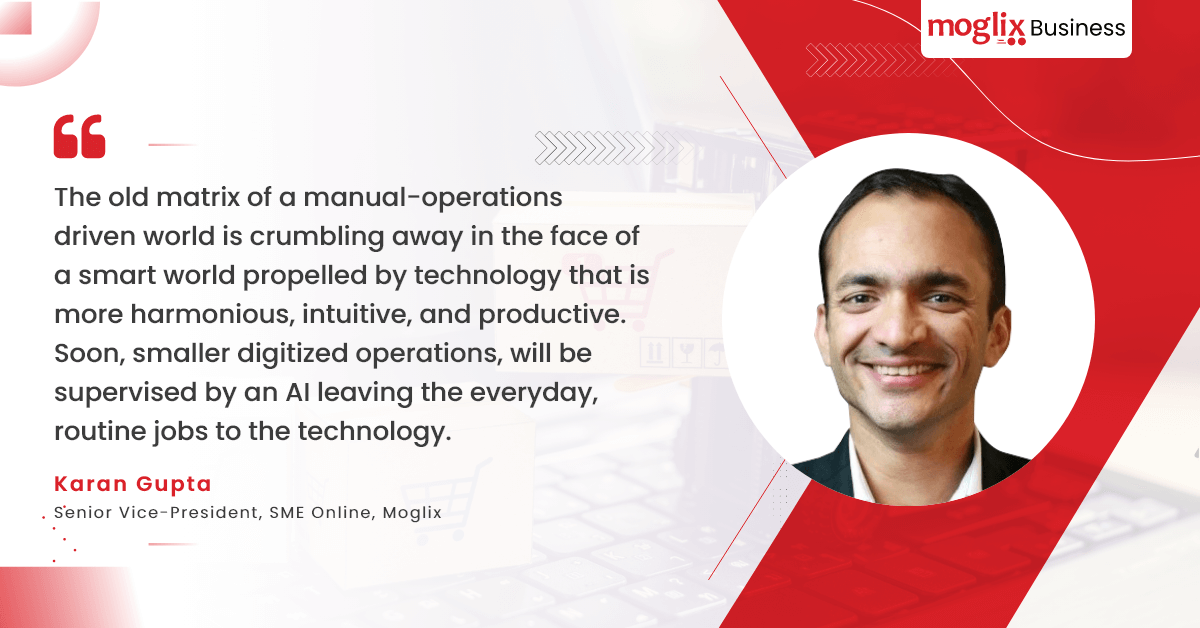
Digitalization is the next frontier for product procurement
A silent revolution is underfoot in India, apparent in India’s expanding scope of Digitalization of MSMEs. Be it a mom-and-pop store, a hole-in-the-wall shop, or a mid-sized firm that runs factories and employs hundreds of workers, more and more business entities are starting to realize that running an agile business without embracing the new digital paradigm is impossible.
The Digitalization endeavor underway in the country in varied sectors like agriculture, education, labor, logistics, energy, financial services, and many more are likely to create economic value of anywhere between $10 to $150 billion by 2025.
“Digitization for a firm should include, within its scope, numerous operations like the purchase of goods and services, vendor shortlisting, purchase agreements, inventory management, monitoring of cash cycles,”
adds Karan
Beware of committing the 5 Deadly Sins of Procurement
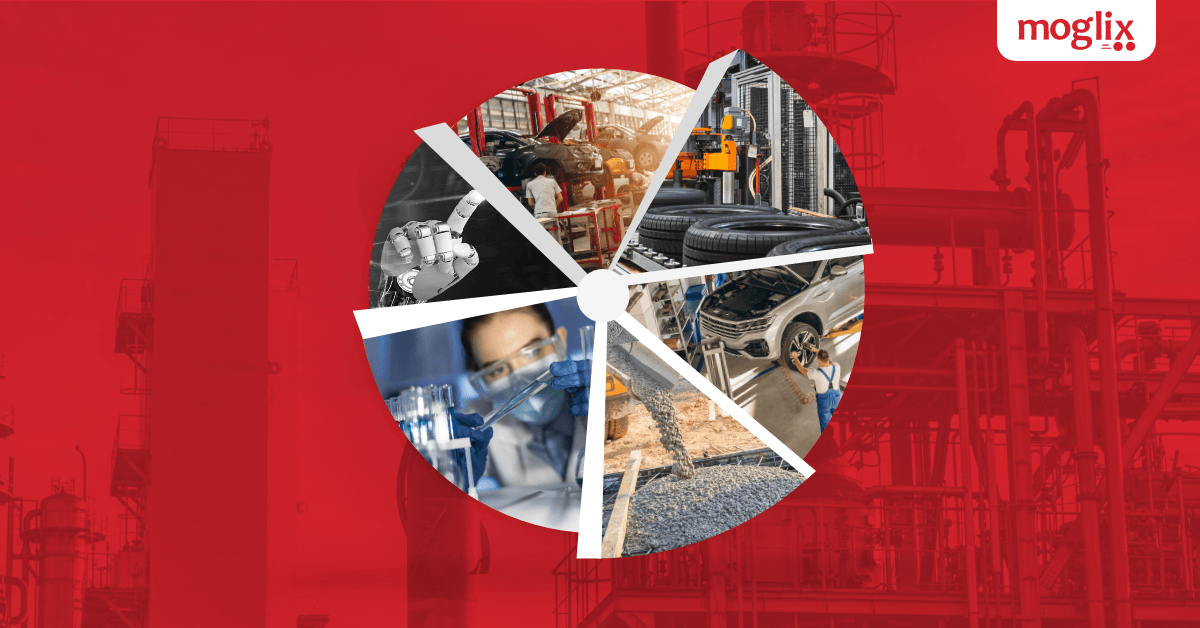
Beware of committing the 5 Deadly Sins of Procurement
Did you know that over 60% of enterprises rely on manual MRO procurement? But just because it’s prevalent, it doesn’t mean it’s the best strategy. If your organization is also yet to automate and upgrade its procurement process, here are two questions for you:
- Are you struggling to minimize expenses and keep track of costs?
- And are you piling inventory or facing material shortages?
It’s highly likely that you may have answered yes to either of these questions. Unfortunately, such gaps in the procurement process can cause consequential disruptions to your business operations.
Effective management of procurement, especially indirect procurement like MRO (Maintenance, Repair, and Operations), can considerably reduce unnecessary costs. However, curtailing costs alone is not enough. If the COVID-19 pandemic has taught us anything, it is that procurement dynamics are changing as rapidly as technology. Today, procurement spans across departments in companies — from finance to operations — advocating the need for a sound procurement strategy.
So, this Dussehra may be the perfect time for your organization to identify and steer clear of the fundamental errors in the procurement process. After all, the festival is all about the triumph of good over evil, and what better time than now to draw up a plan and fight the cardinal sins of MRO procurement?
5 Sins of Procurement
1. Getting your Sourcing wrong? Think Again
Indulging in any procurement activity without a robust sourcing strategy is calling trouble. From picking out the sellers, negotiating contracts, and buying the materials, vital sourcing channels and effective supply chain management are necessary. Many times there is a spike in demand for goods. You might need to procure from global networks to ensure timely delivery of the product. But, global markets are susceptible to volatility in the currency exchange market, time constraints, and import limitations.
You can mitigate supply risks by diversifying the sourcing channels and selecting the most suitable products and services you require to run the business.
2. Manual Processes are so last decade. What You can do instead?
Living in a digital world and relying on manual processes is outdated and inefficient. Doing things the old way can be comforting but waste time and money. One of the significant challenges in MRO procurement stems from investing time in manual tasks. They make procurement cycles lengthy and lead to increased operational costs.
By digitizing the procurement process, you can safeguard yourself from task burnout and working with poor-quality data. The advent of mobile apps and catalog-based buying ensures you undergo smooth procuring.
3. Streamlined Supplier Base
You might have a business where there is a need for specialized demands and unique materials. Often these necessities are met with a fragmented supplier pool and a decentralized procurement network. Such networks pose significant risks in carefully monitoring the procurement process and lead to massive costs, specifically in MRO categories. Additionally, a decentralized system leaves room for errors because individual departments/stakeholders purchase materials separately. It also results in poor management of data, thus suboptimal business analysis.
To reduce cost, waste, and risks associated with multiple supplier bases, you should opt for supplier consolidation and standardized pricing to beat the latent costs of the procurement: which will allow you with greater buying power and higher long-term returns.
4. Inadequate Analysis of Internal Needs
Faulty decisions always arise when you are uncertain about the company’s requirements and goals. Today, data is the world’s most critical resource, and its improper conduct will lead to inaccurate business forecasting. It paves the way for piling inventories because you cannot gauge the market demand and estimate necessary sales. It results in short budgeting and inferior overall outcomes.
Safeguard your business from the misery of inventory pile-up by strategic optimization. Avail of the benefits of vendor-managed inventory and enjoy the perks of an entirely data-driven process and demand-supply optimization. Also, with the help of an MRO aggregator, you can automate the procurement process and indulge in cost savings.
5. Shoddy Inspection in Contract Agreements
The biggest obstacle to the seamless procurement flow is the lags caused due to breaches in service and contract agreements. SLA breaches can result in delayed delivery of goods or subpar service performance. Moreover, seeking redressal from vendors becomes difficult if you do not follow proper contract management practices.
To avoid such violations, look at the finer points of the contract. Inspect the supplier proposal to keep away from making the wrong decisions.
Get Cracking with the proper steps
Managing MRO in procurement can get overwhelming if not tackled correctly. You can reimagine your procurement process with guided assistance from experts. Moglix, with its digital solution, can assess the pain points of your procurement process and elevate it to a new digital paradigm. Download this exclusive e-book, as it can be a helpful ally in your journey to ease the hassles of procurement.
Looking forward to transforming your procurement? Just send your business query to info@moglixbusiness.com.
Decoding Moglix’s Success and Acquisition Strategy
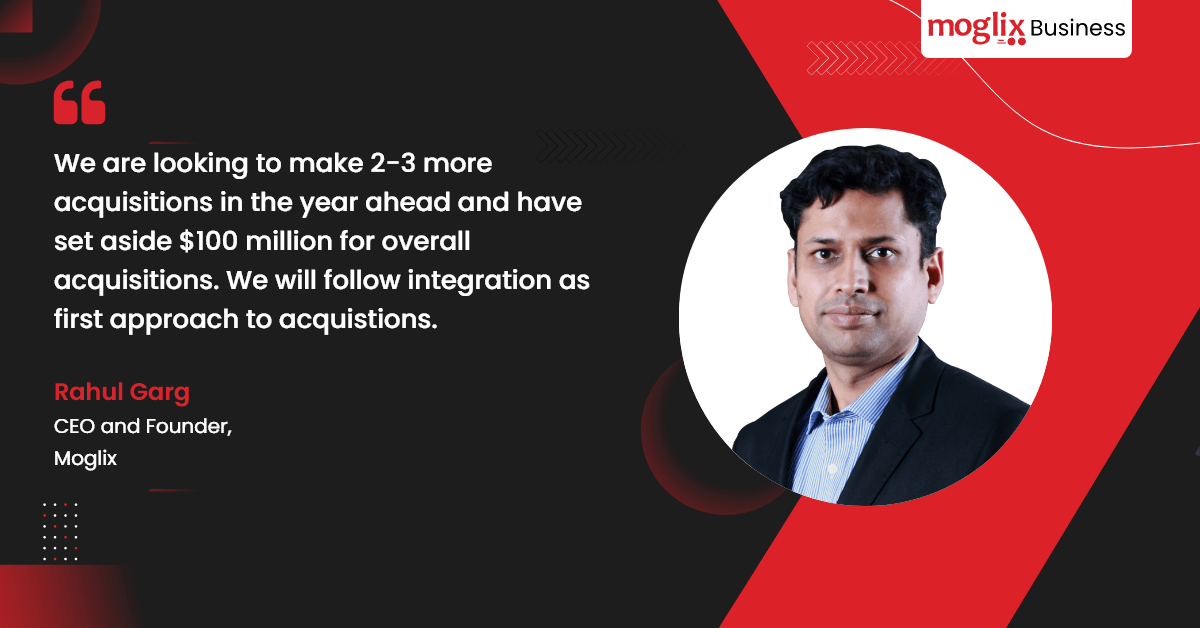
Decoding Moglix’s Success and Acquisition Strategy
In the recent interaction with Rahul Garg, Mint covers Industrial goods marketplace Moglix, that counts Sequoia Capital, Tiger Global and Accel Partners among its investors. The company has earmarked $100 million (Rs 814 crore) as part of its strategy to acquire up to three companies in the next 12 months.
Moglix launched in February 2021 the digital supply chain financing platform Credlix, which acquired trade financing focused fintech startup NuPhi for an undisclosed amount in November. Last year, Moglix also bought machinery marketplace Vendaxo.
“In terms of our global expansion plans, we have entered the UAE market last year and we are looking to foray into two more emerging markets. We are also looking deeper into Indian micro markets, which comprises energy, electric vehicles, hydrogen and solar verticals,”
adds Rahul Garg
Why popular e-marketplaces are a strict no go when it comes to corporate gifting?
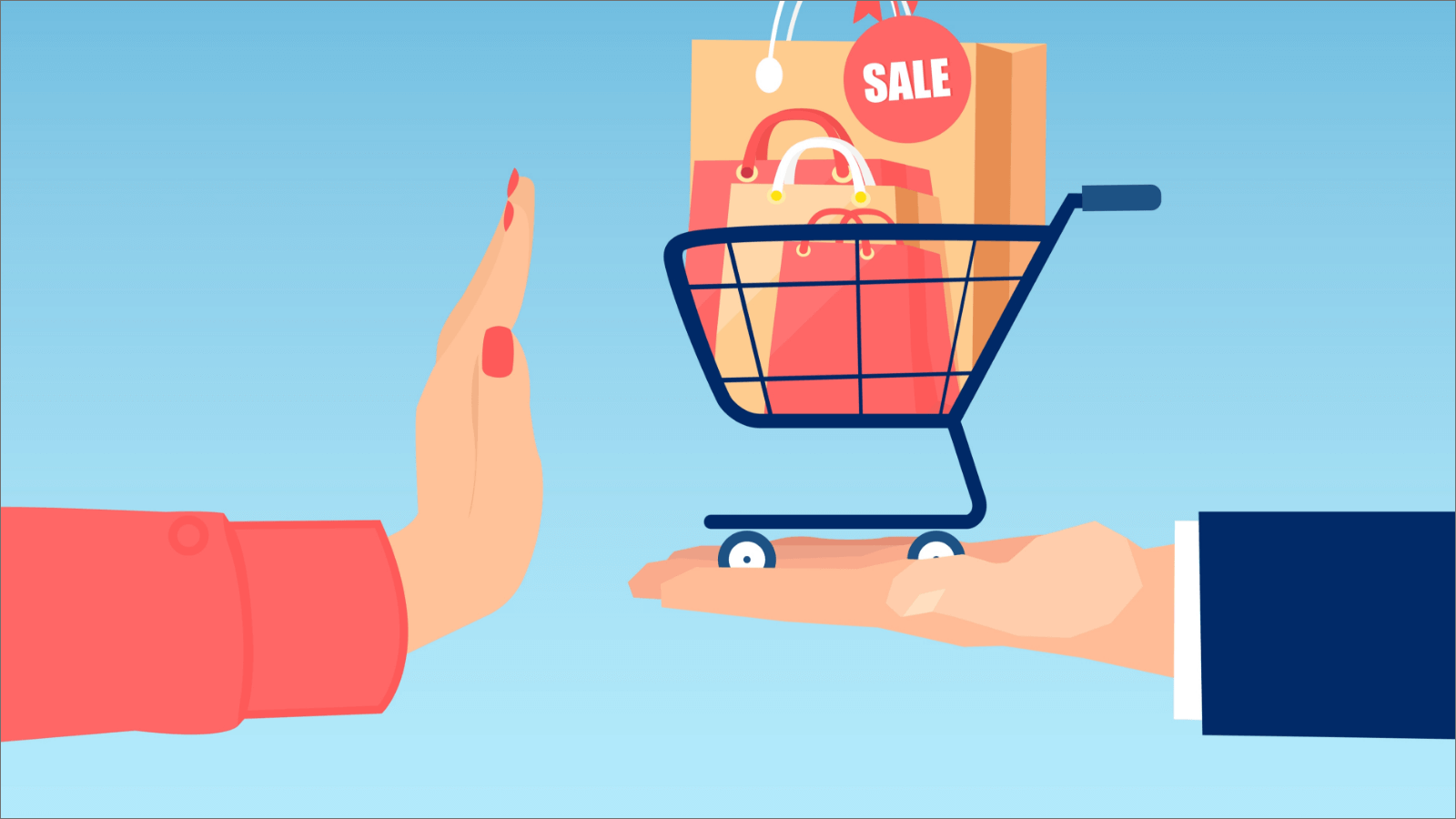
Why popular e-marketplaces are a strict no go when it comes to corporate gifting?
How often have you heard (or used) the phrase: “I’ll just buy it online”?
Let’s face it. eCommerce platforms have a robust market presence. They’re the go-to destinations for most people who are shopping online, particularly for gifts. As one global survey revealed, around 42% of people prefer to buy most (or all) of their holiday gifts on one of these platforms.
Often confused, hence seldom understood is the fact that marketplaces lack the sensitivity when it comes to corporate gifting. Shopping for corporate gifts on these marketplaces defeats the objective of corporate gifting. This festive gifting season, hence, it is a good time to reinvent corporate gifting and look beyond these marketplaces for your employee,customer, and other stakeholder gifts.
One of the key reasons to give bespoke portals a chance this year is that they offer greater freedom to personalize the gifts you purchase. And personalization is one of the hottest gifting trends at the moment. Even adding small details like names, designations, and achievements can significantly elevate the quality of a gift.
Customized gifts like these make receivers feel more valued and included in the corporate family. Unfortunately, on larger, bulk-order marketplaces, you cannot choose curated gifts or add a personal touch to every gift.
Another reason to steer clear of universal online stores is their vetting process. Leading eCommerce marketplaces are generally not particularly picky about the sellers they enlist on their platforms. So, you may have to navigate various issues like inaccurate or insufficient product information, failure to meet delivery deadlines, or a lack of standardized customer service.
Additionally, when you look beyond such generic marketplaces to pick a portal that specializes in corporate gifting, you get the advantage of building a relationship with the latter. You can capitalize on this partnership to build a robust and dynamic corporate gifting program that could quickly become a unique value proposition for your company. This may not be possible when you choose large, consolidated eCommerce portals.
Want to give your corporate gifting game an upgrade this year?
If you answered yes to that question, the Moglix Big Bonanza Festival is just what you’re looking for. Its unique and customized corporate gifting catalog includes over 100 brands across 50+ product categories, and you’re sure to find the perfect corporate gift to let your employees, customers, dealers, distributors and suppliers know just how much they are valued.
You can also take advantage of the massive bulk deals and discounts on the products listed for sale. So, no matter what your corporate gift budget is, India’s biggest corporate gifting festival from Moglix is bound to have something for you.
Know more about how to delight your employees and business associates through the Big Bonanza Festival this year.
Corporate Gifting Made Easy – 5 unmissable corporate gifting ideas
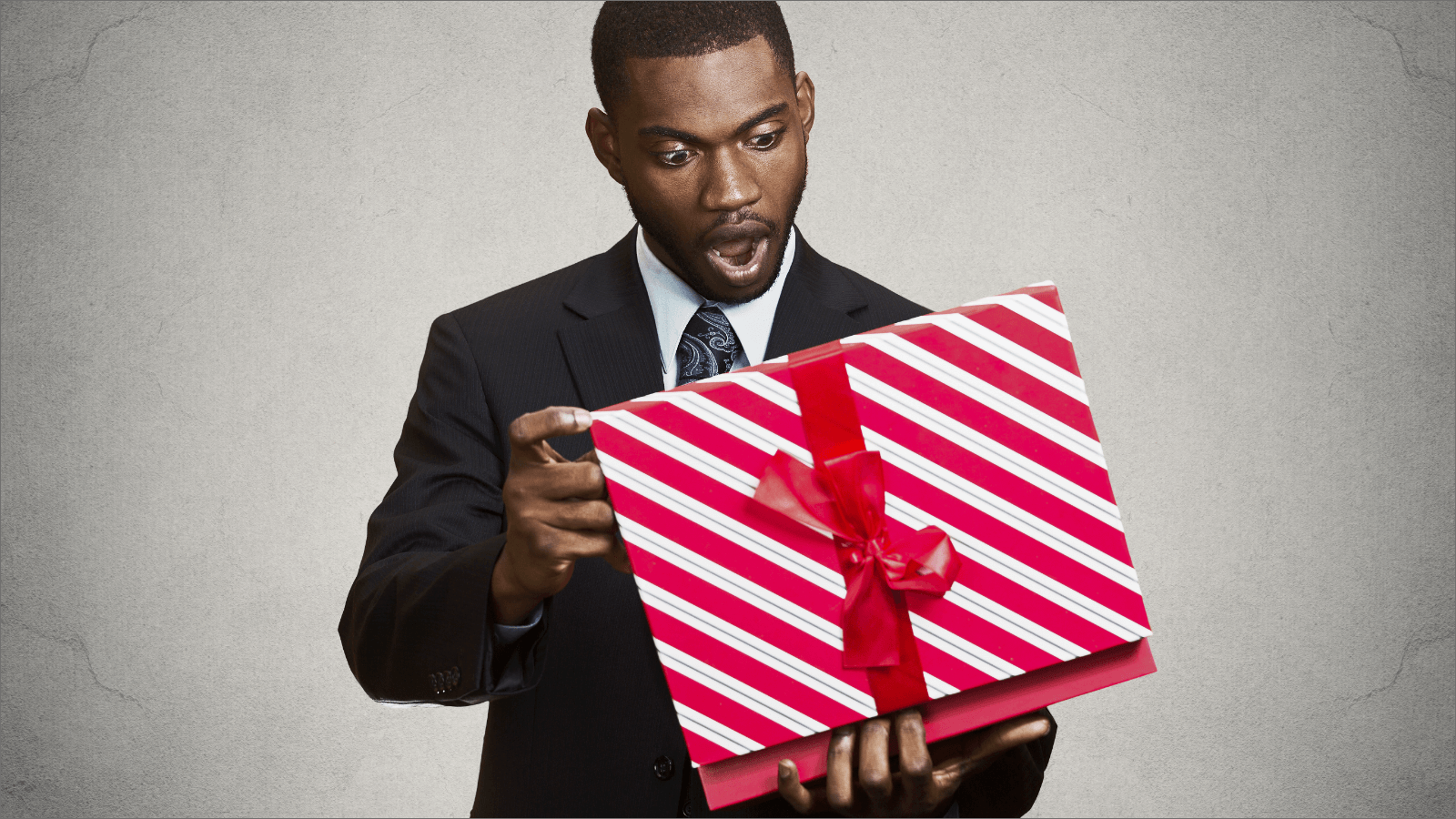
Corporate Gifting Made Easy – 5 unmissable corporate gifting ideas
Back in the day, corporate gifts in India may have been limited to a classy gold watch presented to retiring employees. But in the years since, gift-giving has become a more integral part of corporate culture in the country. In fact, the corporate gifting market in India, now worth Rs. 12,000 crores, is estimated to be growing at over 200% annually.
This is not surprising because the gifting season in India’s offices comes around every year (or sometimes even twice a year!). Gifting trends, however, change from one year to the next.
So, if you want to go the extra mile for your employees, customers, vendors, and other stakeholders this festive season while still keeping pace with the times, here are 5 trending corporate gifting ideas across different budgets.
1. Something that’s sustainable and eco-friendly
With businesses and individuals increasingly embracing sustainability, eco-friendly products will undoubtedly be a hit. This year, you can adopt a sustainable theme and choose gifts that contribute to the betterment of the environment, like reusable products, recycled luxury goods, or even organic options for regular products.
2. Something for the home
You could also get the recipients something for their home, like charming home decor items. If your corporate gift budget allows it, you can even consider getting home appliances this season. Alternatively, if your company follows a hybrid work culture, your employees and other stakeholders will certainly appreciate gifts that will be useful in a home office.
3. Something that’s personalized
Customized gifts never go out of style. Adding little details to a gift, like an employee’s or customer’s name, can give a heartfelt touch to the gesture of corporate gifting. It also boosts their morale and trust more than a generic gift ever could. You can customize many regular products like stationery, coffee mugs, photo frames, and more.
4. More gift to you
If personalized or curated gifts are not what you’re considering this year, why not give the recipients more flexibility with a digital gift card? Each individual can redeem their gift cards at the relevant online marketplaces to purchase products or services that they actually want. This kind of flexibility is a gift in itself, isn’t it?
5. Some cool, new tech gifts
You can never go wrong when you choose a tech-based gift. The options here are practically endless. Depending on the budget available, you can opt for accessories like headphones, power banks, smartwatches, and other wearables, or even electric grooming products. These may not be your average corporate gifts, but your employees, customers, and other patrons will certainly appreciate them.
Want to crack the corporate gifting code this season?
If you answered yes to that, you’ll love the Moglix Big Bonanza Festival, India’s biggest corporate gifting festival — where you can find a wide range of gifting options, all available at attractive deals and discounts. Visit our website to know more.
Reengineering the Automotive Supply chain
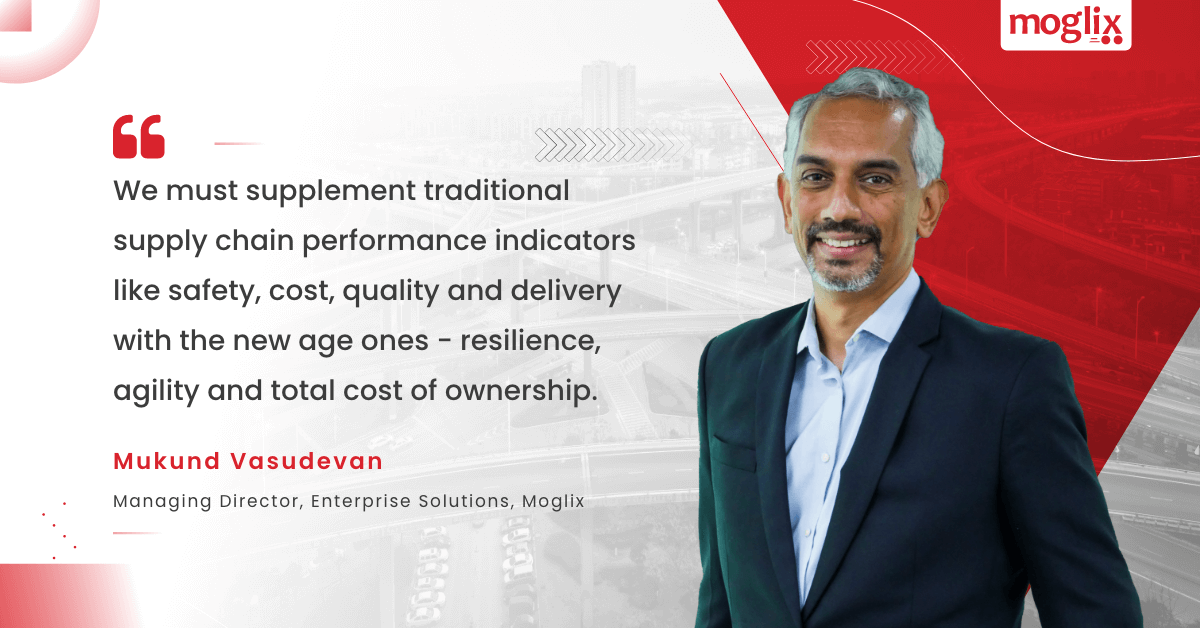
Reengineering the Automotive Supply chain
In 1982, Maruti Udyog and Suzuki signed a historical joint venture which changed the landscape of the Indian automobile sector forever. Nearly four decades later, in 2019, India is set to become the 4th largest automobile market in the world. It produces about 4.5 million vehicles annually (80% passenger and 20% commercial). The industry employs more than three crore people and contributes more than 7% to the overall GDP of India.
Cut to 2022, the industry is recovering from a torrid two-year period of material shortages, flagging customer demand and underutilized production capacity due to Covid. According to SIAM, 2021 was the worst performing year for Indian automobile sales in a decade, with only 17.51 million units sold.
Mentorship Series on `Excelling Business Operations`
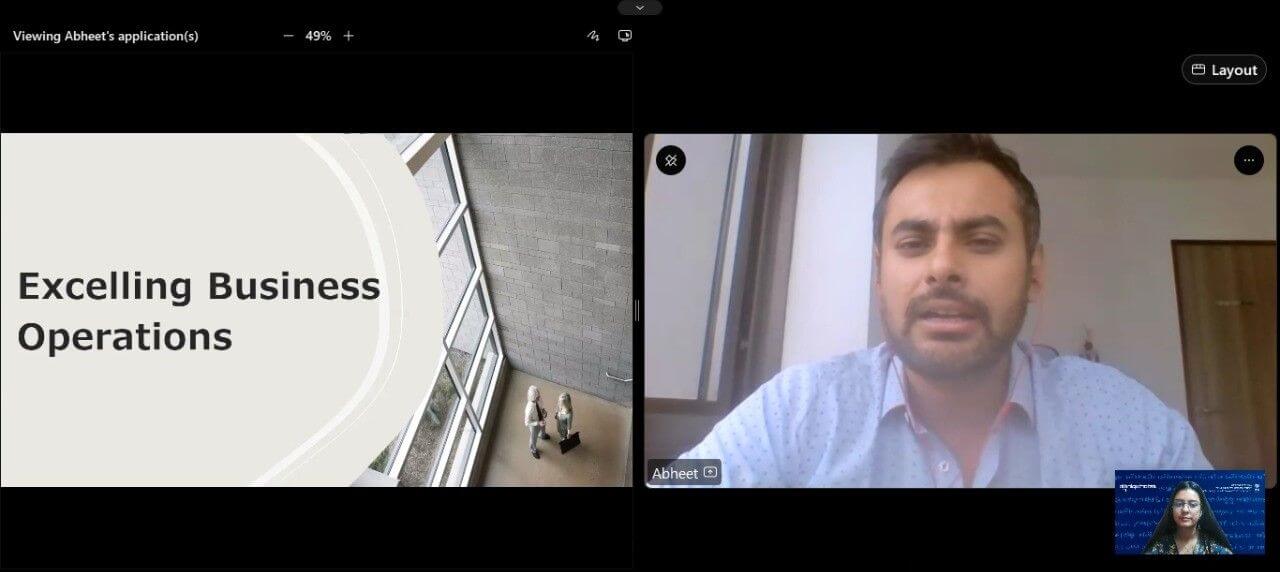
Mentorship Series on `Excelling Business Operations`
Date : August 17, 2022
Organizer: Shanghai Cooperation Organization
About the Event: Mr. Abheet Dwivedi, Senior Director, Moglix, recently delivered a talk on ‘Excelling Business Operations’ at an event organized by the Shanghai Cooperation Organization as part of its Mentorship Series.
India – A beacon of light in the gloomy world of economic turmoil

India – A beacon of light in the gloomy world of economic turmoil
On the occasion of 76th Independence day, Rahul Garg talks about India’s unprecedented growth.
On her diamond jubilee of Independence, India is setting the pace for science, technology, manufacturing and a collective rise in the quality of living for the world to follow. When we won our independence in 1947, the share of national investment in science and technology was 0.1 per cent of the GDP. After a fractious partition and centuries of a colonial hangover, we immersed ourselves into a mode of nation-building that can serve as an example for any young nation todav.
Digital nirvana enabled by startups
As more quintessential Indian consumers shift to a digitally native approach, startups are fulfilling this transformation by addressing the consumer experience gap. The B2B and D2C category provides a secondary business substrate to a new generation of creators with unlimited reach. Startups are at the heart of India’s service-oriented economy’s transformation into a product-led behemoth.
Cohesion: Alumni Connect Series

Cohesion: Alumni Connect Series
Date : August 06, 2022
Organizer: Indian Institute of Management, Calcutta
About the Event: Mr. Avinash Pandey, Director-Packaging, Moglix delivered a talk on the “Emerging Trends in Packaging & B2B Commerce” at ‘Cohesion: Alumni Connect Series’ organized for PGPEX VLM- IIM Calcutta, IIT Kanpur & IIT Madras 16th batch.