Valve Failure Analysis-Investigating Causes, Impacts, and Preventive Measures
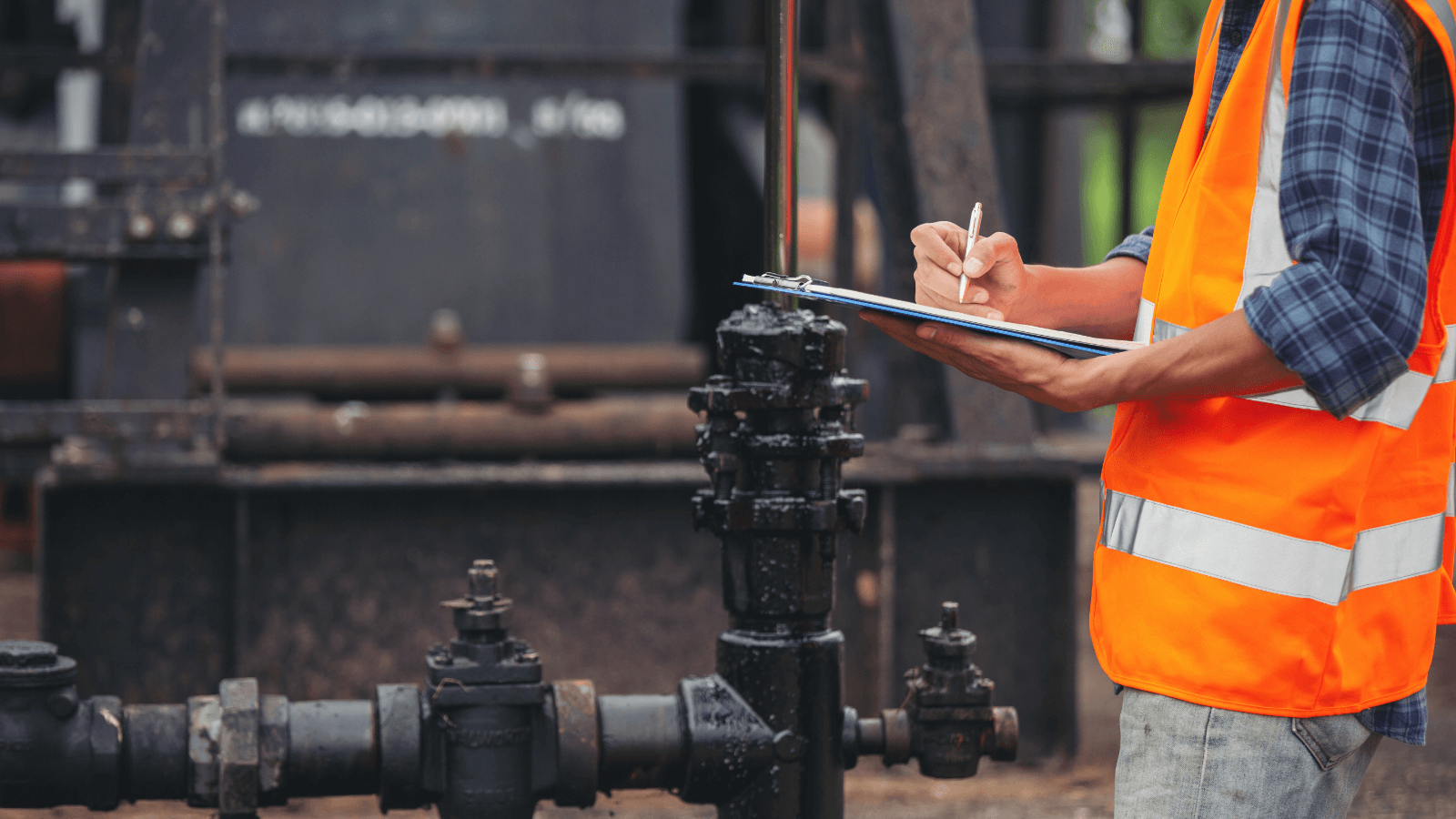
Valves are critical components in industrial processes, regulating the flow of fluids and ensuring efficient operations. However, valve failures can have severe consequences, ranging from safety hazards to production disruptions and financial losses. This blog deals with the causes and impacts of valve failures and explores preventive measures to minimize their occurrence.
Understanding Valve Failure
Valve failures come in various forms, including leakage, blockage, malfunctions, and structural failures. According to one industry report, approximately 40% of valve failures are attributed to internal leakage, while 25% result from corrosion and erosion. The most common causes of valve failure include wear and tear, corrosion, improper installation, operational errors, and fluid conditions. It is estimated that around 80% of valve failures occur due to insufficient maintenance and poor operating practices. Early detection and analysis of valve failures are crucial to prevent more severe incidents and mitigate their impacts.
Impacts of Valve Failures
The impacts of valve failures extend beyond immediate safety concerns. A study found that valve failures can result in an average production loss of $30,000 per hour. Moreover, environmental risks, increased maintenance costs, and reputational damage are additional consequences that industries face when dealing with valve failures.
Valve Failure Analysis Techniques
To identify the root causes of valve failures, comprehensive analysis techniques are employed. These include
- Visual Inspection – involves examining the failed valve to identify visible signs of damage, such as corrosion, erosion, mechanical deformation, or wear. This initial assessment helps in determining if the failure was due to external factors or internal issues.
- Non-destructive testing (NDT) – methods are crucial for evaluating the integrity of valves without causing further damage. Techniques like ultrasonic testing, magnetic particle inspection, and liquid penetrant testing are employed to detect defects, cracks, or flaws within the valve structure.
- Metallurgical analysis – involves examining the valve material under a microscope to identify any metallurgical abnormalities or inconsistencies that may have contributed to the failure. This analysis helps in understanding the valve’s material properties, including strength, composition, and heat treatment.
- Fluid analysis – is employed to evaluate the fluid characteristics and their impact on valve performance. It involves examining fluid samples for contaminants, acidity, viscosity, or any other factors that may have led to valve degradation or malfunction.
- Failure mode and effects analysis (FMEA) – is a systematic approach to identify potential failure modes and their effects on valve performance. It involves evaluating various failure scenarios, their severity, and the likelihood of occurrence. This analysis aids in determining preventive measures to mitigate future failures.
In addition to these techniques, data logging, computer-aided design (CAD) simulations, and expert consultations are also utilized to enhance valve failure analysis.
Valve failure analysis is a crucial process for investigating the causes, impacts, and preventive measures related to valve failures. By employing techniques such as visual inspection, non-destructive testing, and failure mode analysis, industries gain valuable insights to enhance operational efficiency and safety. Implementing targeted preventive measures based on these analyses enables organizations to minimize disruptions, optimize maintenance practices, and improve valve system longevity. Collaboration and knowledge-sharing among industry professionals further advance valve failure analysis practices. Investing in this process ensures reliable operations and long-term success in various industries.