Building Flexible Supply Chains in Manufacturing: Lessons from the Covid19 Pandemic
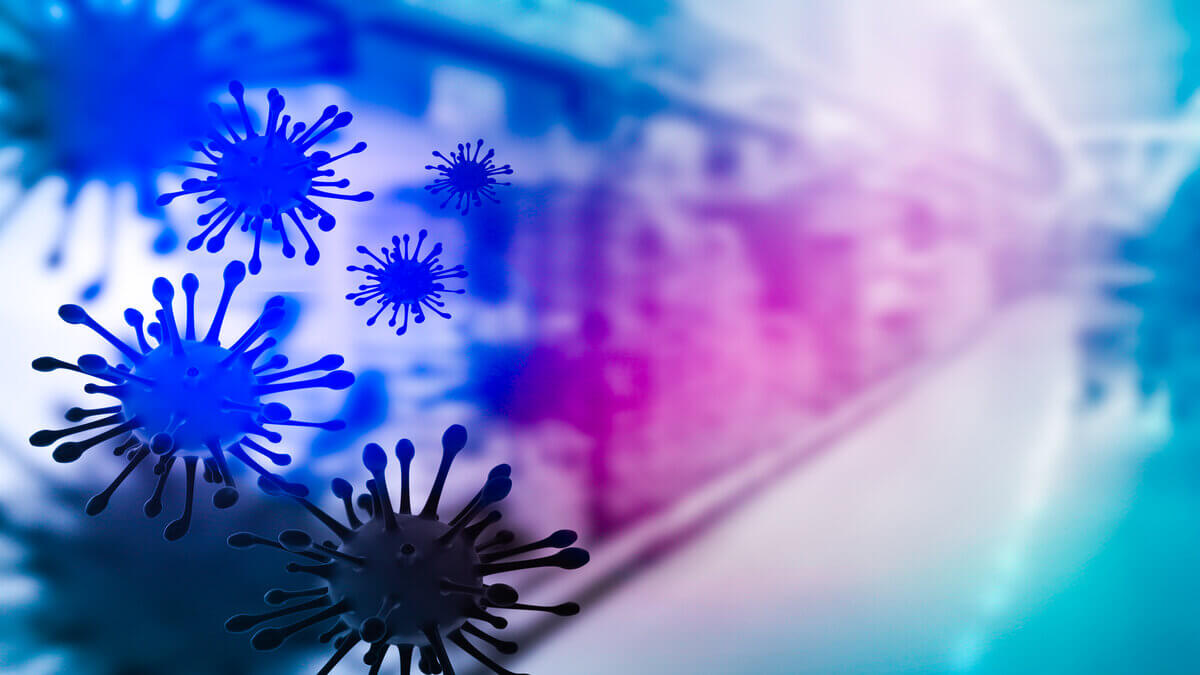
As countries continue to be affected by the disruptions caused by the transmission of the Coronavirus pandemic, enterprises in the manufacturing sector are becoming increasingly wary of what the future of their procurement should look like. While the transient setbacks to a large number of suppliers are nudging supply chain leaders in the manufacturing sector towards exploring local sourcing options, fact remains that global procurement offers the best supply chain risk mitigation outcomes and is therefore likely to not only stay but grow once the manufacturing sector looks to recover and rebuild.
The Costs of Supply Chain Disruption on the Community and Businesses –
As governments across countries issue orders for lockdowns and look to freeze the mobility of multimodal logistics, supply chains across the globe are coming to a grinding halt. For many industry verticals like FMCG, pharmaceuticals, chemicals and life sciences that manufacture essential goods and are thus still in operation, the capability of enterprises to withstand the disruptive supply-side shocks also determines the potential risks of entitlement failures what with communities of people being dependent on uninterrupted supplies of PPE, masks, sanitizers, soaps, medicines, shelf-stock food items, groceries, and other edible items. The Coronavirus pandemic presents them with multifold challenges of procuring:
- MRO items to keep their operations up and running
- effective packaging to roll-out products into the market
- warehousing to maintain sufficient inventory
- logistics to ensure fast last mile delivery
The Contemporary Scope of Local Sourcing and the Promise of Global Procurement –
The supply chain challenges facing enterprises in the manufacturing sector may nudge them towards searching for new suppliers with local footprint and in proximity to the points of manufacturing, new logistics service providers and even new sub-contractors with industrial-scale capabilities for agile manufacturing to meet the demand gap. However global procurement offers enterprises unparalleled advantages of supply chain de-risking that are beyond the scope of local sourcing.
Success Stories of Enterprises Using Global Procurement to Overcome Supply Chain Disruptions –
As arguments for greater localization of supply chains and procurement networks begin to gain traction, here are a few lessons from success stories of enterprises that have leveraged global procurement to navigate supply chain disruptions.
Intelligent Product Design Can Lend Greater Flexibility to the Supply Chain
Back in the first decade of the new millennium, Nokia was a leader in mobile handset manufacturing with the demand for its products at its peak. The Finnish mobile company had manufacturing facilities across countries in the world. In the year 2000, a mishap destroyed an important chip manufacturing facility located in Albuquerque that supplied Nokia. Despite the mishap, the impact on the manufacturing capabilities of Nokia was by and far limited. Nokia had designed the chips from the ground up such that it was possible for the enterprise to swiftly move its production to the Netherlands and Singapore.
Lesson #1: If products are designed intelligently from the ground up with an eye on scaling up manufacturing across multiple locations it offers an enterprise greater insulation from disruptive shocks to their manufacturing and operations and consequently to their downstream supply chain and distribution channels.
Contingency Logistics Planning Can Help Enterprises with Downstream Distribution
The cotton shirt manufacturer, Esquel is a vendor for major international labels like Hugo Boss and Nike. The enterprise has manufacturing facilities in Vietnam and routinely uses logistics routes from China to procure fabrics for its manufacturing units in its home country, Vietnam. However,the enterprise had invested heavily in forging partnerships with logistics service providers with a diverse portfolio of supply chain capabilities that could, if required, divert from the regular trade route through Hong Kong and on to Vietnam. This contingency planning for alternative logistics proved critical when eventually Esquel did face the challenge.
Lesson #2: Agile companies that are proactive and prepared for the turbulences downstream face a relatively lesser risk. It may take longer and cost more to ship supplies through a second-best route, but given the stakes of imminent disruption, even a sub-optimal choice is better than having no choice at all.
Access to Multiple Avenues of Connectivity Can Create Market Opportunities
Take the case of Ethiopia. Until a few years ago Ethiopia was a landlocked country with very limited options for first and last-mile connectivity to long-distance logistics infrastructure for the mid-mile leg of the supply chain. This had the effect of inhibiting the growth of the textile industry. Over the years there have been massive investments in new highways and a railway project that provides connectivity to the nearest major port and a multitude of industrial parks located in its neighbor Djibouti. Today Ethiopia is the home to several global manufacturers in the clothing and textile industry that have set shop in the country and operate production units.
Lesson #3: Suppliers with access to global connectivity are better positioned to hit the ground running in times of disruptive shocks to the supply chain to feed supplies to large scale enterprises that operate a truly global and multi-plant manufacturing network.
Looking Ahead: Global Procurement Shall Be Inclusive, Collaborative and Digital
While the temptations of the localized supply chain and sourcing strategy are palpable, there are enterprises that have been leveraging collaborative supplier ecosystems to good effect prior to the onset of the Covid-19 pandemic. For instance, an American multi brand retail heavyweight operates a procurement ecosystem consisting of 100 suppliers through a dedicated project that aims to improve the operational environment at their manufacturing units and bring greater visibility into its supplier collaboration. The internal consulting team at the enterprise is entrusted with responsibility to meticulously map the capacities and capabilities of each supplier. Thereafter the team recommends a customized supplier collaboration program that aligns with the concerned supplier’s business model. Interestingly the enterprise extends its supplier collaboration beyond the timelines of the project. Through greater repetitiveness and economies of flow, the supplier ecosystem when managed through a single window, improves over time and develops a greater immunity to supply side shocks.
In the face of the takeaways evidenced by the above mentioned business cases there are some lessons for enterprises in the manufacturing sector to draw inspiration from. Global procurement networks offer a reliable risk mitigation strategy. It makes enormous good sense to assert the same by premising one’s conclusions on the following paradigm:
- First, it is apparent by now that the Coronavirus pandemic leverages a time interval to spread from the epicenter to the rest of the world. As manufacturing units of suppliers and large scale multi-plant enterprises in the epicenter crawl back to normalcy, they are now in a position to provide supplies to enterprises in the rest of the world.
- Second, this time lag in the spread of the pandemic and the consequent economic lockdowns across countries creates opportunities for: arbitrage (procurement from vendors across geographies) and speculation (distribution and sales across time horizons through brand partnerships).
- Third, diversified supplier ecosystems provide greater flexibility of choice to large scale enterprises for procurement by providing diverse options for logistics, warehousing and procurement of relevant products that comply with specifications, quality parameters and costs.
With global procurement, enterprises in the manufacturing sector can actually have minimum exposure to the risks associated with supply chain disruptions like the ones caused by the Covid19 pandemic.