The Role of Robotics in Modern Manufacturing
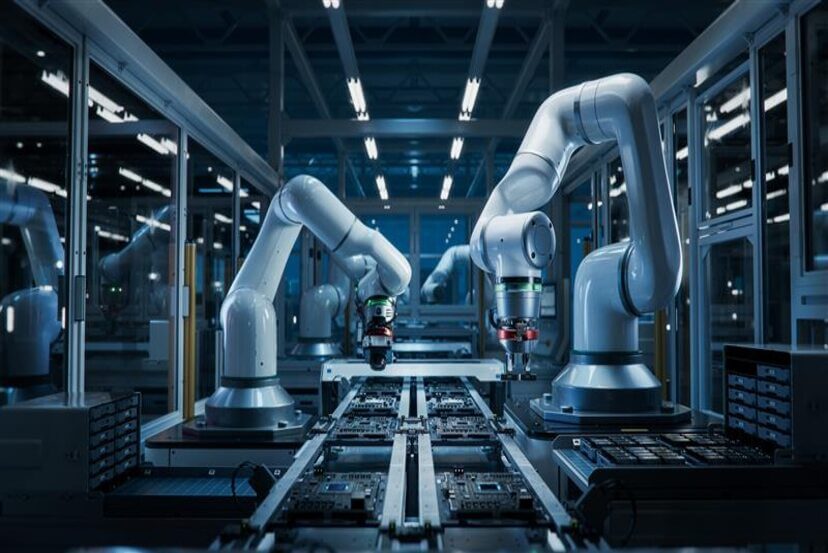
The Role of Robotics in Modern Manufacturing
Introduction: Robotics in Manufacturing is Reshaping the Industry
Manufacturing is changing quickly, with robotics leading this transformation. In various industries, companies are using industrial robots and automation to boost productivity, decrease errors, and solve labor shortages. In India, where the manufacturing sector is growing under initiatives like “Make in India,” robotics is playing a crucial role in modernizing production processes. As demand for high-quality, affordable, and scalable manufacturing grows, businesses see automation as a game-changer.
This blog explores how robotics in manufacturing is revolutionizing the industry in India, the benefits of automation, and the future of industrial robots in modern production.
How Robotics in Manufacturing is Transforming Production Processes
The use of robotics in manufacturing is transforming how goods are made. From automotive to electronics and pharmaceuticals, industries are using industrial robots to streamline operations. Key areas where robotics is making a difference include:
- Precision and Consistency: Robots perform tasks with extreme accuracy, ensuring high-quality production with minimal defects.
- Speed and Scalability: Automated systems can operate 24/7 without breaks, significantly increasing production capacity.
- Workplace Safety: By handling hazardous tasks, industrial robots reduce the risk of workplace injuries.
- Cost Efficiency: Although initially expensive, the long-term savings in labor costs and increased efficiency make automation a wise business decision.
These advancements highlight why manufacturers in India are investing in robotics in manufacturing to stay competitive in the global market.
Automation in Manufacturing: Addressing India’s Skilled Labor Shortage
India’s manufacturing sector is facing a shortage of skilled labor, impacting production efficiency. Automation in manufacturing is closing this gap by:
- Reducing Reliance on Manual Labor: Automated assembly lines and robotic arms take on repetitive tasks, freeing human workers for more complex duties.
- Upskilling the Workforce: Robotics is not replacing jobs but transforming them. Workers are learning to operate, program, and maintain industrial robots, which leads to better-paying and more specialized job options.
- Improving Work Conditions: Automation reduces physical strain and exposure to hazardous environments, improving overall working conditions in factories.
By implementing automation in manufacturing, Indian industries can overcome workforce challenges while improving operational efficiency.
Industrial Robots: Types and Applications in Manufacturing
Different manufacturing sectors use industrial robots in various ways. Some of the most commonly used robots include:
- Articulated Robots: These robots with multiple joints are commonly used in automotive assembly for welding and painting.
- SCARA Robots: Ideal for pick-and-place tasks, these robots are employed in electronics and pharmaceutical manufacturing
- Collaborative Robots (Cobots): Designed to work alongside human workers, cobots are increasingly being used in small and medium enterprises (SMEs) in India.
- AGVs (Automated Guided Vehicles): Used for material handling in warehouses and factories, improving logistics efficiency.
By adopting industrial robots, manufacturers in India are enhancing productivity, reducing waste, and ensuring consistent product quality.
The Future of Robotics in Manufacturing in India
With advancements in artificial intelligence (AI) and machine learning, the future of robotics in manufacturing looks promising in India. Emerging trends include:
- AI-Driven Automation: Smart robots with AI capabilities can learn and adapt to new tasks, making them more flexible and efficient.
- IoT-Enabled Robotics: Integration of robots with IoT (Internet of Things) allows real-time monitoring and predictive maintenance, reducing downtime.
- 3D Printing and Robotics: The combination of robotics and additive manufacturing is revolutionizing prototyping and custom production.
- Government Support and Investment: India’s push for “Industry 4.0” and initiatives like the Production Linked Incentive (PLI) scheme are driving investments in automation and robotics.
These trends indicate that robotics in manufacturing will continue to play a crucial role in India’s industrial growth.
Transform Your Business with Moglix for Robotics and Automation Solutions
The adoption of robotics in manufacturing is no longer a luxury but a necessity for businesses looking to enhance efficiency and remain competitive. As India moves towards becoming a global manufacturing powerhouse, automation and industrial robots will be key to driving productivity and innovation.
At Moglix, we provide cutting-edge automation and robotics solutions to help manufacturers optimize their production processes. Whether you are looking to integrate automation in manufacturing or explore the benefits of industrial robots, Moglix is your trusted partner for scalable and cost-effective solutions.
Contact Moglix today to discover automation solutions for your business and stay ahead in the manufacturing revolution!
Sustainable Manufacturing: Achieving Carbon Neutrality in Production
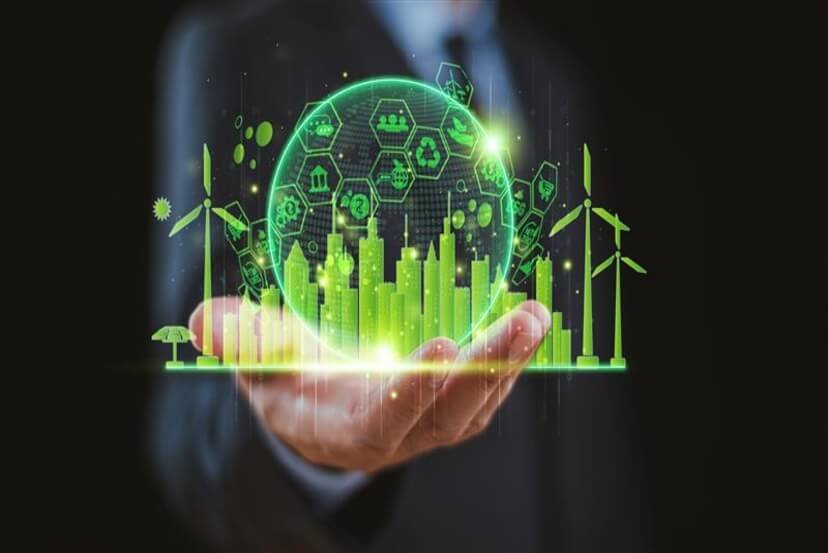
Sustainable Manufacturing: Achieving Carbon Neutrality in Production
Why Sustainable Manufacturing Matters
Sustainability is now a major focus for businesses globally, with the manufacturing sector playing a key role in this shift. Companies are now focusing on sustainable manufacturing to minimize their environmental impact, reduce carbon emissions, and ensure long-term resource efficiency. Reaching carbon neutrality in production has become essential for business, not just an ethical duty, due to stricter government regulations and consumer demand for eco-friendly products
In this blog, we explore key strategies that businesses can adopt to reduce their carbon footprint, implement eco-friendly production processes, and comply with sustainability standards to move towards carbon-neutral manufacturing.
How to Implement Sustainable Manufacturing Practices
To shift toward sustainable manufacturing, businesses need to incorporate green practices throughout the production process. This includes optimizing resource use, reducing waste, and adopting cleaner technologies. Here are some effective approaches:
- Energy Efficiency Measures: Switching to energy-efficient machinery, installing LED lighting, and enhancing production processes can greatly lower energy use.
- Renewable Energy Adoption: Shifting to solar, wind, or hydropower reduces reliance on fossil fuels and decreases overall emissions.
- Waste Reduction Programs: Implementing lean manufacturing principles, recycling materials, and minimizing waste can help businesses cut costs and reduce their environmental footprint.
- Water Conservation: Industries using large amounts of water should invest in recycling systems and water-efficient technologies.
By integrating these strategies into daily operations, companies can achieve eco-friendly production, enhance efficiency, and reduce costs.
Carbon Neutrality in Production: Steps to Achieve It
Achieving carbon neutrality in production means balancing the amount of carbon dioxide released into the atmosphere with an equivalent amount of carbon removal. Here’s how businesses can reach this goal:
1. Measure and Track Carbon Emissions
The first step is to understand the carbon footprint of manufacturing operations. Businesses should perform life cycle assessments (LCA) to monitor emissions from the extraction of raw materials to the disposal of products. Using smart sensors and sustainable manufacturing software can give real-time data on carbon output, aiding companies in making well-informed decisions.
2. Optimize Supply Chain for Sustainability
A major contributor to carbon emissions is the supply chain. Companies need to collaborate with suppliers who are dedicated to sustainability, including:
- Sourcing raw materials responsibly (e.g., using recycled or certified sustainable materials)
- Reducing transportation emissions by optimizing logistics and opting for local suppliers
- Implementing eco-friendly production techniques such as low-energy processing and biodegradable packaging
3. Invest in Low-Carbon Technologies
Technology plays a key role in reducing emissions. Companies should explore:
- Electrification of Processes: Switching from fossil fuel-based machinery to electric-powered alternatives
- Green Manufacturing Equipment: Using robotics and automation to enhance precision and minimize waste
- Carbon Capture and Storage (CCS): Capturing emissions from factories and storing them underground or using them in industrial processes
4. Adopt Circular Economy Principles
A circular economy approach minimizes waste and extends product life cycles. Key strategies include:
- Designing products for reuse, repair, or recycling
- Implementing take-back programs where customers return used products for refurbishment
- Utilizing biodegradable or recyclable materials to decrease landfill waste
By integrating these principles, manufacturers can ensure that resources are used efficiently and waste is minimized, aligning with sustainable manufacturing goals.
5. Offset Remaining Carbon Emissions
Despite the best sustainability practices, some emissions are inevitable. Businesses can achieve carbon neutrality in production by investing in carbon offset programs such as:
- Reforestation projects that absorb CO2
- Renewable energy credits (RECs) that support clean energy projects
- Community-based sustainability initiatives that promote environmental conservation
By taking responsibility for their carbon footprint, manufacturers can effectively neutralize their impact on the planet.
Compliance with Environmental Regulations
Governments and international bodies are enforcing stricter environmental laws to push industries toward eco-friendly production. Businesses must stay ahead of regulations such as:
- The Paris Agreement: Global commitment to reduce carbon emissions and limit global warming.
- ISO 14001: International standard for environmental management systems (EMS).
- Extended Producer Responsibility (EPR): Laws requiring manufacturers to take responsibility for product disposal and recycling.
- Carbon Tax Policies: Financial penalties on excessive carbon emissions to encourage cleaner practices.
Compliance not only prevents legal risks but also boosts a business’s reputation as a leader in sustainable manufacturing.
The Business Benefits of Sustainable Manufacturing
Beyond regulatory compliance, adopting sustainable manufacturing brings tangible benefits to businesses:
- Cost Savings: Reduced energy and material waste translate to lower operational expenses.
- Brand Reputation: Consumers prefer companies with strong environmental commitments, boosting customer loyalty.
- Competitive Advantage: Companies that prioritize carbon neutrality in production gain a market edge by aligning with global sustainability trends.
- Investor Confidence: Sustainability-driven businesses attract impact investors and funding opportunities.
Partner with Moglix for Sustainable Manufacturing Solutions
Transitioning to sustainable manufacturing is a journey that requires strategic planning, investment, and the right partnerships. At Moglix, we help businesses achieve carbon neutrality in production by providing sustainable procurement solutions, eco-friendly raw materials, and green technology support.
If your company is looking to embrace eco-friendly production, reduce carbon emissions, and stay ahead of sustainability regulations, partner with Moglix today. Together, we can build a cleaner, greener future for manufacturing.
Get in touch with Moglix now to explore sustainable manufacturing solutions!
Can India emerge as a Key Player in Global Manufacturing?
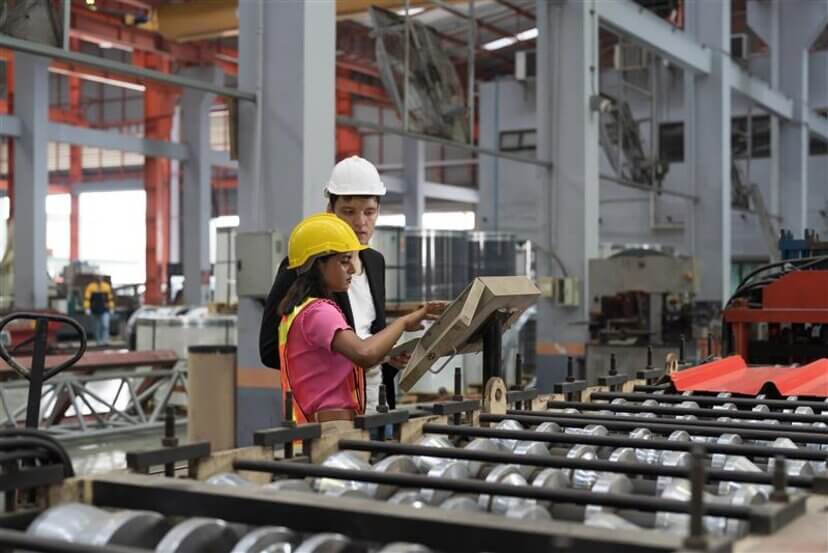
Can India emerge as a Key Player in Global Manufacturing?
In recent years, global supply chains have experienced major shifts, and India is now recognized as a key player in this transformation. Disruptions from events like the pandemic, geopolitical tensions, and trade conflicts have forced businesses around the world to rethink their strategies. Many are now focusing on diversifying supply chains, and India has emerged as a highly attractive destination for manufacturing and sourcing. With its cost advantages, a growing and skilled workforce, and its improving infrastructure, India is positioning itself as the go-to hub for companies looking to optimize their supply chain operations.
The shift toward India has been accelerated by several factors, including the disruptions caused by the global pandemic.. In the wake of these disruptions, companies have been forced to reconsider their reliance on China, often called the “world’s factory,” and look for alternatives. India, with its strategic location, robust domestic market, and expanding manufacturing base, has naturally attracted multinational companies seeking stability and growth.
Is India a better bet than China for supply chains?
Global supply chains have historically been highly centralized, with many key manufacturing processes concentrated in specific regions like East Asia, particularly China. However, the rise of trade barriers, ongoing geopolitical tensions, and challenges related to the pandemic have made it clear that supply chain stability needs to be prioritized.
India offers several advantages that make it a compelling alternative to traditional manufacturing hubs. First and foremost is the cost advantage. While labor costs in China have risen significantly over the past few years, India still offers relatively low labor costs, which makes it an attractive destination for businesses looking to lower manufacturing costs while maintaining quality.
India’s infrastructure has also been improving steadily, with significant investments in roads, ports, and industrial corridors. The government has launched several initiatives aimed at boosting manufacturing capabilities, such as the “Make in India” campaign, which encourages both domestic and foreign companies to invest in local manufacturing. Additionally, India’s geographic location is favorable for global trade, with access to major shipping routes and proximity to the Middle East, Africa, and Southeast Asia.
Finally, India’s domestic market is vast and growing, providing manufacturers with a large base of consumers to cater to. This expanding market offers the dual advantage of serving both domestic needs and the potential to export goods across the globe.
Which sectors are booming in India’s manufacturing?
India’s manufacturing boom is already underway across various sectors, establishing the country as a key global player.
The automotive industry, in particular, has seen growth due to U.S. auto tariffs pushing manufacturers to find alternatives to China. With an established sector, skilled workforce, and improving infrastructure, India has attracted global companies like Ford, General Motors, and Hyundai, making it a hub for vehicle production.
The energy sector is also thriving, with Saudi Aramco investing in India’s refinery and petrochemical industries. This strengthens India’s role in the global supply chain for energy and raw materials.
Similarly, India’s aerospace and defense sectors are growing, with global companies increasingly sourcing components and assembling products there, thanks to the country’s technological expertise, skilled labor, and competitive cost structures.
What Challenges India faces in becoming a global hub?
India’s potential as a manufacturing hub is clear, but challenges remain. One major obstacle is infrastructure. Despite recent improvements, gaps in logistics, supply chain connectivity, and quality standards persist. Ports are often overcrowded, and rail and road networks can delay deliveries. While initiatives like the Bharatmala Project are underway, it will take time to see significant improvements in efficiency.
Policy consistency is another challenge. Frequent changes in tax laws and regulations create uncertainty, discouraging long-term investments. Simplifying these processes is essential for attracting sustained foreign investment.
Additionally, India’s manufacturing sector must enhance production efficiency and quality standards to stay competitive with established hubs like China. While cost advantages are a strength, further advancements in technology and automation are needed to maintain a competitive edge.
How can India strengthen its position in global supply chains?
India’s role in global supply chains is set to grow rapidly in the coming years. With its cost advantages, skilled labor force, improving infrastructure, and expanding manufacturing capabilities, India is well-positioned to become a global manufacturing leader. The opportunities in key sectors such as automotive, aerospace, and energy offer strong growth potential, and India’s growing importance in these industries signals a bright future for its manufacturing sector.
However, to fully realize this potential, India must address the challenges of infrastructure, regulatory consistency, and production efficiency. With the right investments and policies, India can secure its place as a global supply chain powerhouse.
How Moglix can help?
If you are looking to explore the benefits of sourcing or manufacturing from India, Moglix can help you navigate the complexities of India’s manufacturing sector. By partnering with us, you can access the best sourcing options and leverage India’s manufacturing potential to streamline your global supply chain.
Get in touch with Moglix today to explore how we can support your business in harnessing the power of India’s manufacturing boom.
Tier 2 and Tier 3 Supplier Digitization: Unlocking India’s Manufacturing Depth
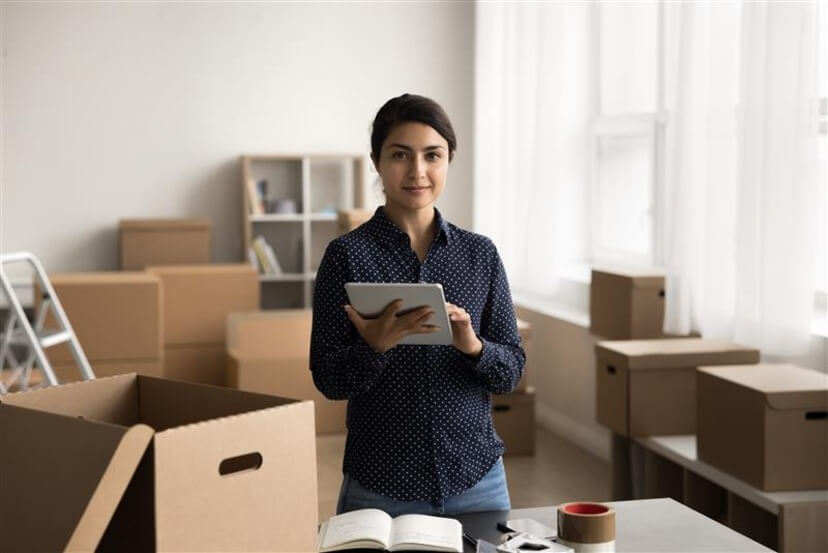
Tier 2 and Tier 3 Supplier Digitization: Unlocking India’s Manufacturing Depth
When we talk about India’s manufacturing strength, most of the spotlight falls on large factories, industrial clusters, and export-driven giants. But look a little deeper, and you’ll find the true engine of India’s industrial ecosystem: the Tier 2 and Tier 3 suppliers. These micro, small, and medium enterprises (MSMEs) form the backbone of regional manufacturing, often supplying critical parts and components to larger manufacturers.
Yet, despite their importance, these vendors are still largely dependent on manual systems, fragmented communication, and informal processes. That’s where MSME digitization comes into play not just as an efficiency upgrade, but as a national priority.
The Problem: Outdated Systems and Low Visibility
India has more than 63 million MSMEs, and a large portion of them operate without digital tools. Procurement is done over calls or paper. Orders are tracked manually. Quality checks and audits rely on physical visits. Payments are delayed due to lack of transparency.
This lack of digitization results in:
- Low visibility across the supply chain
- Inconsistent quality control
- Informal workflows that hinder collaboration
- Missed integration with enterprise-level buyers
The result? India’s deep supply network remains under-leveraged, under-utilized, and unprepared to scale in a competitive global market.
Missed Opportunity: Untapped Capacity and Potential
Many Tier 2 and Tier 3 vendors have the physical infrastructure and workforce to deliver more but without digital systems, they lack access to consistent business, quality certifications, and enterprise demand.
Without integration into digital supply chains, these vendors:
- Fail to meet the compliance standards required by large corporations
- Miss out on government schemes or institutional procurement opportunities
- Struggle with working capital due to irregular payments and poor documentation
Simply put, the absence of supplier enablement is costing India both in economic output and supply chain resilience.
The Digital Difference: A Shift from Informal to Integrated
Digitization doesn’t mean large IT overhauls; it can begin with simple tools and scale gradually. Here’s how digital adoption transforms the MSME supplier ecosystem:
1. E-Catalogs & Digital Onboarding
Standardized product listings and transparent pricing help buyers discover and transact with small vendors easily. It improves visibility and simplifies sourcing decisions.
2. Digital Audits & Quality Dashboards
Real-time quality tracking and digital checklists ensure consistent outputs. It builds trust and reduces dependency on physical site visits.
3. Order & Payment Visibility
Integrated procurement platforms allow suppliers to track POs, delivery schedules, and payments reducing disputes and improving cash flow.
4. Performance Analytics
Small vendors can now measure delivery timelines, rejection rates, and customer satisfaction driving a culture of continuous improvement.
National Benefit: A Stronger Manufacturing Backbone
When MSMEs are digitally enabled, the entire ecosystem benefits:
- Large enterprises gain access to more reliable and diverse suppliers
- Local sourcing becomes more viable, reducing import dependency
- Supply chain inclusion expands, bringing rural and semi-urban businesses into mainstream manufacturing
- Job creation increases as small businesses scale confidently
In short, digitizing Tier 2 and Tier 3 suppliers is not just a matter of convenience, it’s a lever for national competitiveness.
Final Thoughts
India’s manufacturing future isn’t just about building new mega-factories. It’s about unlocking the potential of millions of small, often-overlooked suppliers. Through MSME digitization and thoughtful supplier enablement, India can create a truly inclusive, agile, and globally competitive manufacturing base.
It’s time to stop treating Tier 2 and Tier 3 vendors as peripheral players and start enabling them as digital-first partners in India’s industrial growth story.
Sheet Metal Fabrication: Why Material Selection Matters for Manufacturers & Procurement Professionals
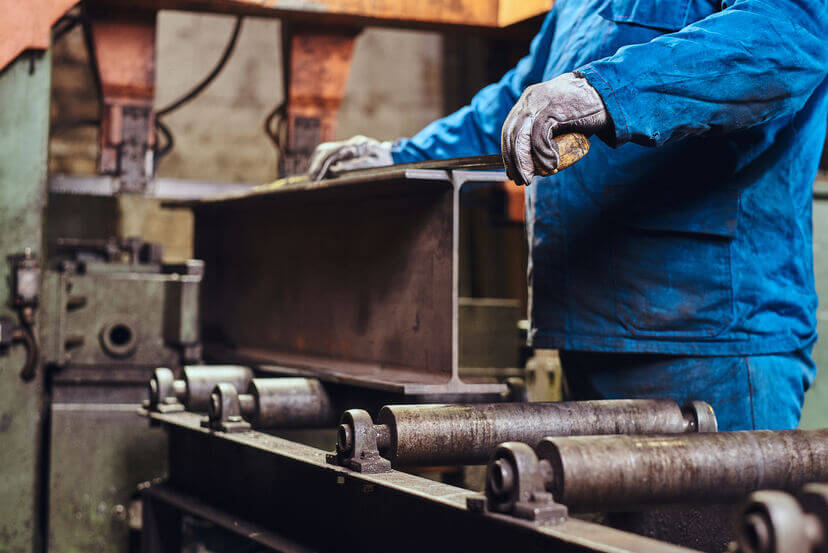
Sheet Metal Fabrication: Why Material Selection Matters for Manufacturers & Procurement Professionals
In the realm of sheet metal fabrication, material selection is a pivotal factor influencing the quality, performance, and cost-effectiveness of the final product. Choosing the appropriate material ensures that the fabricated component meets industry standards and functions optimally in its intended application. In sectors such as infrastructure, public sector undertakings (PSUs), automotive, and aerospace, the right material choice can define the success of a project.
This article delves into the significance of material selection, exploring key considerations, common materials, and industry best practices to ensure efficiency and durability in sheet metal fabrication.
The Importance of Material Selection
Material selection is integral to the fabrication process, impacting various aspects such as manufacturability, durability, and overall performance. Here’s why it matters:
- Compliance with Industry Standards: Various industries follow strict regulatory standards for materials used in fabrication. For instance, the automotive sector adheres to ISO/TS 16949, while the aerospace sector follows AS9100 standards. The wrong material selection can lead to compliance issues, product failures, and financial losses.
- Structural Integrity: The selected material must possess mechanical properties like tensile strength, hardness, and impact resistance to ensure the component withstands operational stresses over time. Industries such as construction, railways, and defense require materials that can endure harsh conditions without compromising integrity.
- Manufacturing Efficiency: Different materials respond differently to fabrication processes such as cutting, bending, welding, and forming. A material that is easier to process contributes to efficient production workflows, reducing lead times and minimizing material waste.
- Cost Management: Balancing performance with cost-effectiveness is critical. While high-performance materials like stainless steel offer superior benefits, they may not be feasible for budget-sensitive projects. Smart material selection allows manufacturers to optimize costs without compromising quality.
- Environmental Resistance: Industries such as marine, aerospace, and infrastructure require materials with high x to withstand environmental exposure. The right choice ensures longevity, reducing maintenance costs and preventing premature failure.
Factors Influencing Material Selection
Selecting materials for sheet metal fabrication involves evaluating multiple parameters:
- Mechanical Properties
Understanding a material’s tensile strength, hardness, ductility, and impact resistance is crucial to ensuring it meets the performance demands of the application.
- Formability & Ductility
A material’s ability to be bent, stretched, or formed without breaking determines its suitability for complex shapes and intricate designs. Industries like automotive and consumer electronics rely heavily on materials that offer excellent formability.
- Weldability
Many fabrication projects require welding for assembly and reinforcement. Materials must be compatible with welding techniques like TIG, MIG, or resistance welding to ensure strong, defect-free joints.
- Surface Finish Requirements
For industries where aesthetics matter, such as architecture, interior design, and appliances, materials must be capable of achieving desired surface finishes like polishing, anodizing, or powder coating.
- Environmental & Chemical Resistance
Projects in chemical plants, oil & gas, and marine industries demand materials that can resist corrosion, oxidation, and chemical exposure to enhance longevity and performance.
Common Materials in Sheet Metal Fabrication
Several materials are commonly used in sheet metal fabrication, each offering unique properties suitable for various applications:
Carbon Steel
- Strength & Durability: Ideal for structural applications.
- Cost-Effective: More affordable compared to stainless steel.
- Requires Coatings: Susceptible to rust if left untreated.
- Used In: Construction, heavy machinery, automotive.
Stainless Steel
- Corrosion & Heat Resistance: Ideal for harsh environments.
- Hygienic: Used in food processing and medical applications.
- High Strength: Withstands mechanical stress.
- Used In: Food industry, aerospace, medical equipment.
Aluminum
- Lightweight & Corrosion-Resistant: Perfect for weight-sensitive applications.
- High Conductivity: Used in electronics and heat exchangers.
- Excellent Formability: Easily shaped into complex designs.
- Used In: Aerospace, automotive, consumer electronics.
Copper
- Superior Electrical & Thermal Conductivity: Essential for electrical applications.
- Antimicrobial: Suitable for hospitals and public spaces.
- High Malleability: Allows intricate designs.
- Used In: Electrical components, HVAC, medical applications.
Brass
- Corrosion-Resistant & Aesthetic Appeal: Common in decorative applications.
- Good Machinability: Allows precise detailing.
- Used In: Plumbing, musical instruments, hardware fittings.
Industry Best Practices for Material Selection
1. Project-Specific Selection
Different industries have unique material requirements. Conducting a thorough analysis of project needs ensures that materials align with performance expectations.
2. Supplier Collaboration
Engaging with reliable material suppliers helps in sourcing high-quality materials with consistent properties and certified compliance.
3. Material Testing & Prototyping
Before full-scale fabrication, materials should undergo testing for mechanical performance, formability, and resistance to environmental stressors.
4. Sustainability Considerations
With industries shifting toward eco-friendly practices, selecting recyclable materials like aluminum and stainless steel contributes to sustainable manufacturing.
Case Study: Moglix Business’s Approach to Custom Fabrication
Moglix Business demonstrates the importance of material selection in custom fabrication. Their end-to-end fabrication solutions encompass:
- Material sourcing aligned with project specifications.
- Design engineering with a focus on cost-effective, durable materials.
- Onsite fabrication & assembly backed by robust quality assurance.
Moglix Business has contributed to infrastructure projects of national importance, such as India’s first bullet train corridor, showcasing expertise in strategic material selection to enhance project success.
Conclusion
Material selection is a cornerstone of successful sheet metal fabrication, influencing performance, durability, and cost-effectiveness. By carefully considering factors like mechanical properties, manufacturability, and environmental resistance, manufacturers can ensure optimal results for their applications.
Contact Moglix Business for Your Custom Fabrication Needs
Looking for a custom fabrication partner that prioritizes material selection and quality assurance?
📩 Email: info@moglixbusiness.com
Discover how Moglix Business can enhance your fabrication projects with industry-leading expertise!
Moglix in 2020: The Year of Supply Chain
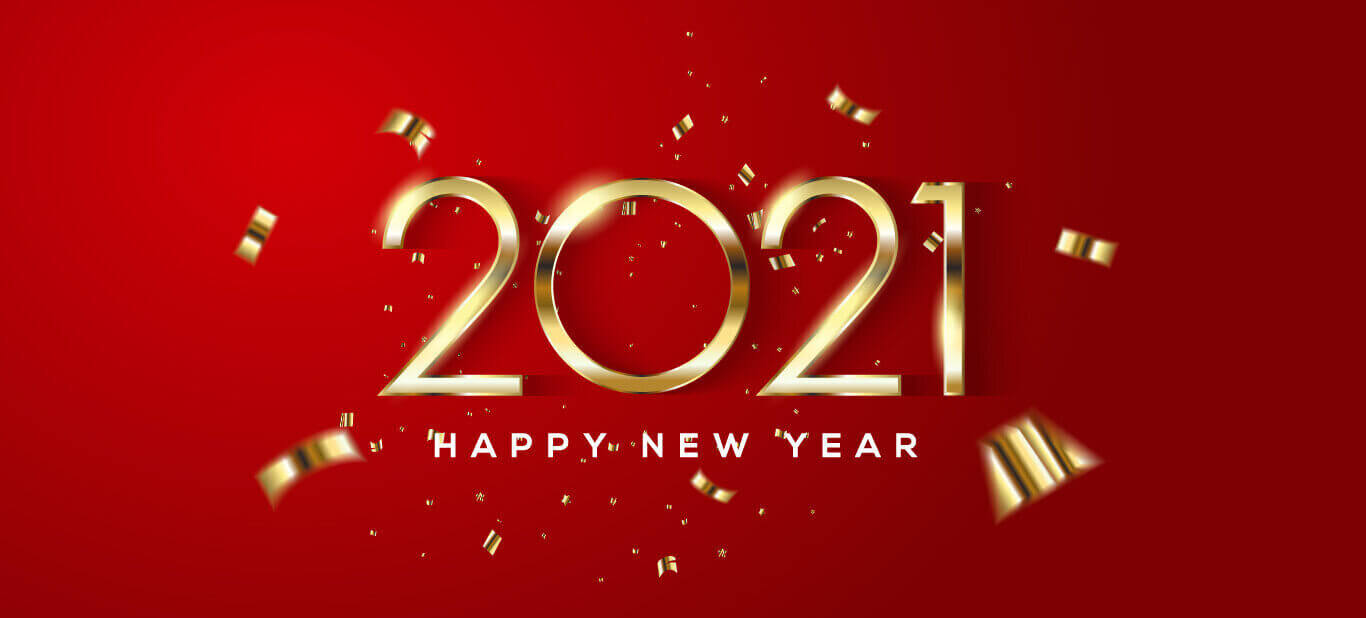
Moglix in 2020: The Year of Supply Chain
Everything that we reimagined at Moglix in 2020Read More
3 Reasons Why Every Multiplant Manufacturing Business Needs a Packaging Audit
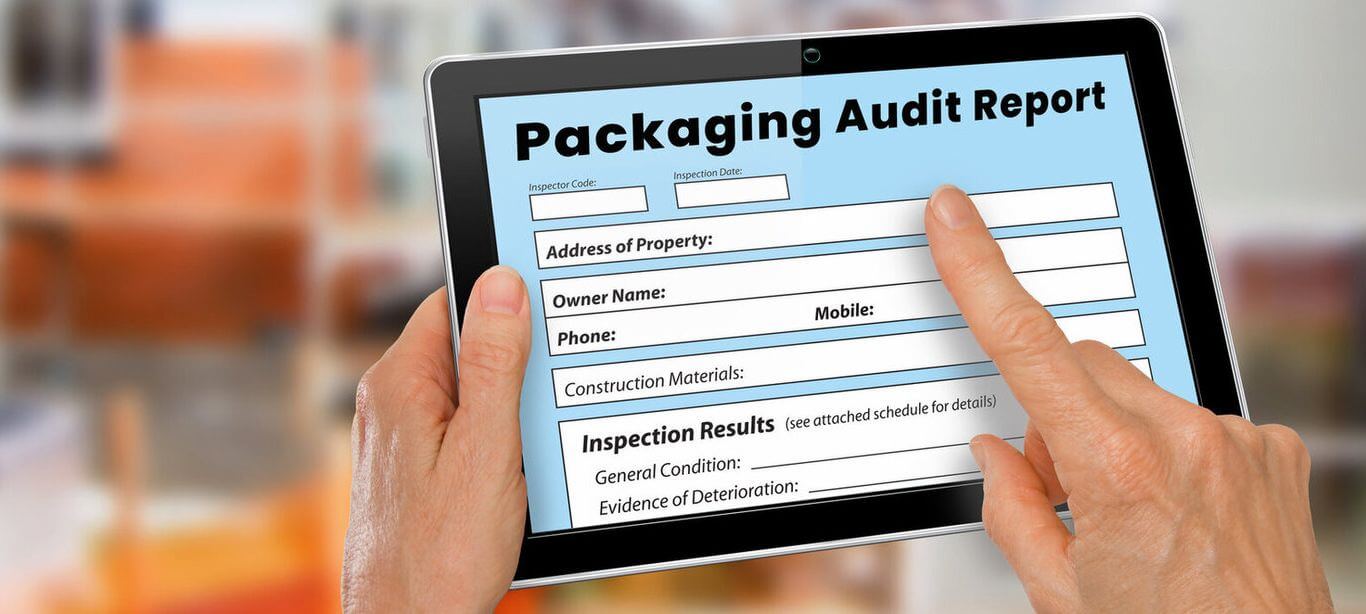
3 Reasons Why Every Multiplant Manufacturing Business Needs a Packaging Audit
If you are a manufacturer, your packaging supply chain manager is likely to list three significant packaging challenges.
- How do I reduce packaging costs?
- How do I identify and reduce the in-transit losses of my goods?
- How do I put my enterprise on track for continuous improvement?
If you face any or all of the above challenges, you are looking for a robust and periodic packaging audit program with the following benefits for your enterprise.
Explore the Cost Advantage of a Lean Supply Chain for Packaging
Optimizing the packaging inventory is a significant challenge. Holding high inventories of packaging SKUs can block your enterprise’s working capital. On the other hand, an inventory stock-out can directly affect your distribution and reduce revenue through lost sales. A packaging audit can enable you to rightsize your packaging inventory, unlock working capital, and reduce indirect costs. You can also explore EOQ levels of inventory by using artificial intelligence-enabled analytics and migrate towards a lean supply chain.
Reduce Wastage and Losses in Transit During the Supply Chain Journey
Pilferage, wear and tear, and spoilage during transit can lead to formidable losses to your enterprise. One way to reduce such wastage and losses is to re-engineer packaging as per the logistics lens. A packaging audit can enable you to map the logistical challenges across multiple modes of transportation and choose packaging solutions that provide the best fit for each stage of your supply chain journey.
Continuously Improve Through Total Quality Management in Packaging
The COVID19 pandemic has ushered in a new normal. How do you explore new avenues to stay competitive? Class C spend items like packaging cater to less than 10% of the unit costs of end products but are likely to affect more than 10X of the value of your goods if you get it wrong. A packaging audit can help you to discover the most significant opportunities to enable continuous improvement and total quality management in packaging.
Are you exploring a Packaging Audit for your Manufacturing Plant(s)? Testing and diagnosis are integral to both human and enterprise health. With a packaging audit across your plant locations, you can detect challenges early and adopt remedial measures with agility to reimagine your packaging.
If you feel that your packaging could be improved but don’t know where to start, please get in touch with us here. You can also learn more about our packaging solutions by clicking here.
5 Priorities for CXOs to Unlock the Manufacturing Supply Chain
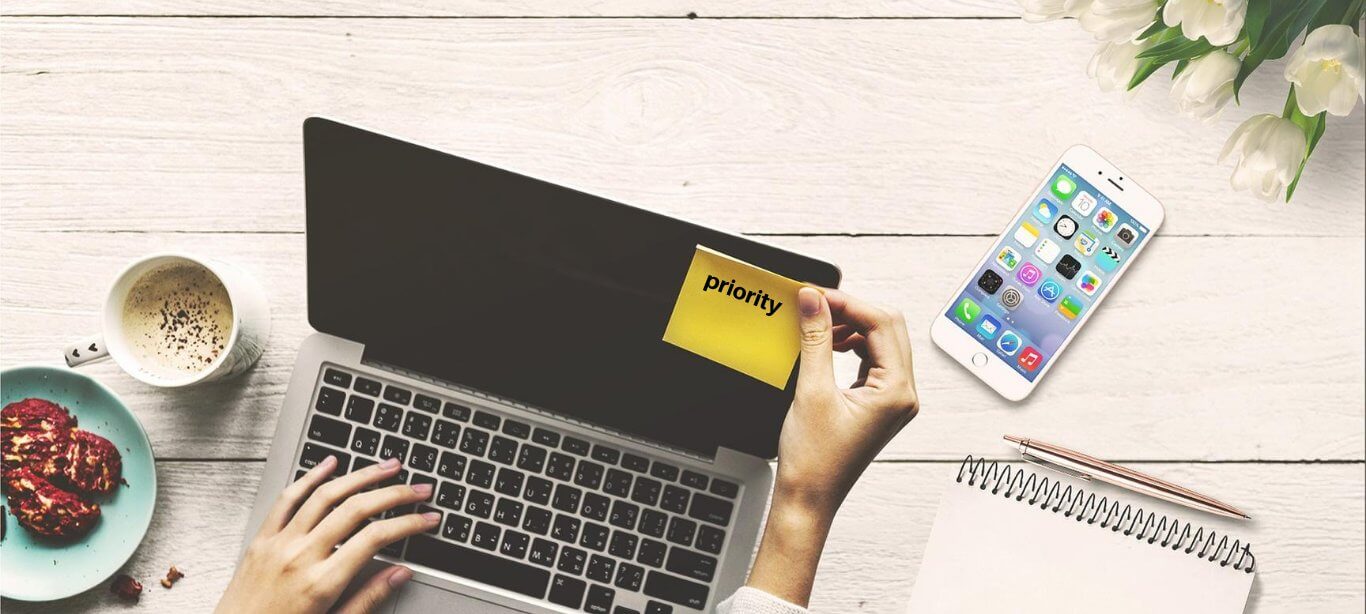
5 Priorities for CXOs to Unlock the Manufacturing Supply Chain
Is a turnaround just around the corner for the manufacturing supply chain in India? Insights from various manufacturing indices suggest that while aggregate performance continues to be sub-optimal, the upward plateauing of some verticals suggest that distant signs of recovery may not be too far away after all despite the weak sentiments prevailing now. The dip in the Nomura Business Resumption Index from 70 to 66 over the first fortnight of July, suggests the manufacturing engine cooling down. Despite the Markit PMI rising from 31 in May to 47 in June 2020, industry verticals have continued to grapple with challenges of constrained capacity, weak demand, contraction of the workforce and lack of alternate supplier sites for import substitution. Moglix Business is partnering with manufacturing enterprises to make sense of these emerging patterns and identify the priorities that CXOs need to address to unlock the manufacturing supply chain. Explore these top 5 priorities here.
Read:COVID19: The Three Phases of Recovery in Manufacturing
Map Supplier Clusters, Demand Centers and Labor CorridorsThrough the Pandemic
In India, manufacturing supply chains are highly intertwined and consist of a complex matrix of supplier clusters, demand centers, and highly concentrated labor corridors. CXOs in manufacturing enterprises need to map the exposure of their respective supplier clusters, demand corridors, and labor corridors to the contagion to identify their supplier downtime, time to recovery (TTR), and the spikes in logistics and supply chain management costs. One hundred thirty districts in the country account for 38% of manufacturing output, 50% of final private consumption, and 40% non-farm employment. Many of these districts are still in the red zones. These insights explain the contraction of output and the sub-optimal capacity utilization in the range of 28-63%. Moreover, 50% of truckers in the logistics and construction sectors come from just 15 of these districts. It explains why workforce deployment has continued to be 33-57% and why consumer demand is yet to pick up.
Read: How to Reduce Coronavirus-led Supply Chain Disruptions
Track and Trace Opex Regularly Amidst Shrinking Revenue and Output
Keeping track of the OPEX and managing indirect and direct expenses is imperative to create new avenues of efficiency. The rise in direct and indirect costs facing manufacturing enterprises is due to higher overhead costs of safety protocols, loss of economies of scale due to a drastic reduction in volumes, high freight charges, and other logistic expenses, increased costs of raw materials, power cost and high costs of debt financing. CXOs in Indian manufacturing enterprises need to pivot their management of indirect costs on line items like MRO inventory, packaging materials, packaging design, maintenance, and interest payments on suppliers spend analytics through digital procurement platforms. Digital platforms that run on artificial intelligence and machine learning can enable CXOs to stay informed on evolving developments in the supply chain, exercise higher control on strategic sourcing, and regularly track and trace OPEX from anywhere and at any time.
Realign Supplier Networks to Facilitate Import Substitution
Manufacturing enterprises have continued to witness a decline in exports for four consecutive months during the pandemic. Trade wars and geopolitics have already weakened the global trading environment. The pandemic has caused further supply chain disruptions for several verticals like automotive, textiles machinery, leather goods, footwear, electronics, and electrical equipment. Consequently, these verticals have continued to register abysmal manufacturing output thus far. The erosion of trust in supplier networks with high exposure to one country calls for CXOs to explore import substitution opportunities for their strategic sourcing. While import substitution and realignment of global supply chains are strategic actions, Indian manufacturing enterprises need to avoid further procurement risks. CXOs need to explore strategic partnerships with local industrial suppliers through digital supplier collaboration models to achieve agility at scale in their import substitution efforts and hit the ground running.
Digitize Procurement Processes to Reduce Fixed Costs and De-Leverage
One of the significant challenges facing CXOs in Indian manufacturing enterprises is the resilience of their balance sheets and cost structures. Research suggests that fixed costs account for 20-35% of the total costs for Indian manufacturers due to a high CAPEX on investments in land, plant, equipment, and machinery.CXOs of Indian manufacturing enterprises need to rationalize costs in the short term while creating opportunities to move towards leaner fixed cost models in the long run. Leveraging digital models for the automation of cost centers like procurement organization, supplier collaboration, and quality control can enable supply chain leaders in manufacturing to transform fixed costs incurred on these functions into variable costs and achieve the targeted balance sheet impacts. At Moglix Business, we have seen enterprises that have migrated towards e-procurement models save up to 5% on direct and indirect costs.
Read: What Does Procurement Transformation for the Next Decade Looks Like
Digitize Sales and Distribution Processes to Open New Revenue Streams
The unlocking of the economy has shifted from a cold turkey and holistic approach to a more decentralized and localized one. The uneven spread of the contagion across regions in the country makes it difficult for Indian manufacturers to operate their sales and distribution functions. Technology penetration in Indian manufacturing enterprises is below 5%. One of the significant opportunities for CXOs in Indian manufacturing is to leverage digital B2B commerce models to restart the engines of revenue enablement while ensuring that sales and distribution people, distributors, and customers continue to collaborate from the protected environments of their homes. Research shows that OEMs and authorized distributors of industrial supplies that have leveraged digital B2B commerce models are likely to stay ahead of their contemporaries as the economy continues to move towards recovery gradually.
COVID19: The Three Phases of Recovery in Manufacturing
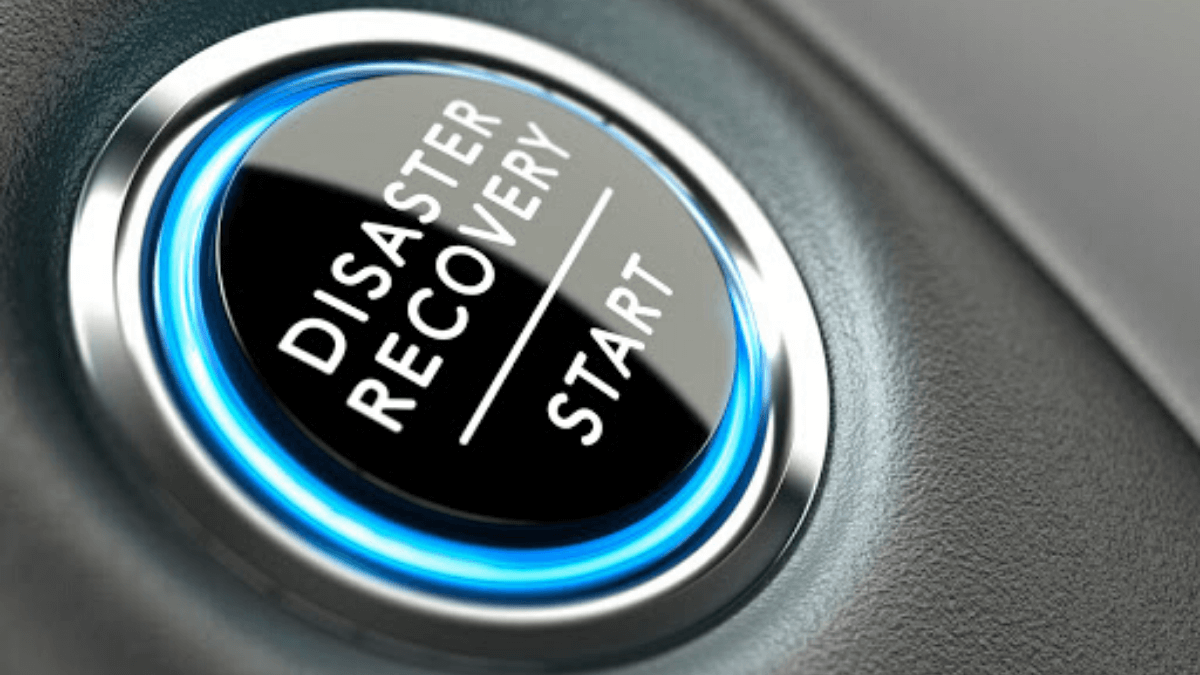
COVID19: The Three Phases of Recovery in Manufacturing
How badly has the manufacturing sector been hit by the COVID19 pandemic? Is recovery from the current situation even possible? Given the huge costs imposed by the lockdown and the unpredictable contours of the spread of the contagion, what can manufacturers do to resume their business once the first signs of ‘Unlock 1.0’ are visible? If so, what trajectory will enterprises in manufacturing need to take to make up for the significant losses that have already occurred and the ones that are anticipated to emerge over a period of time?
The United Nations (UN) has projected that the global economy will shrink by 3-4% in the year 2020. As an outcome, manufacturing enterprises need to introspect on the steps that they need to take today, tomorrow, and over the course of time, leading into the future of a post-pandemic world. At Moglix, we believe that enterprises need to visualize the road to recovery by first rebuilding trust today, enabling businesses processes with technology for tomorrow, and building futuristic supply chains using advanced technology for the foreseeable future beyond COVID19.
What Manufacturers Need to Do Today?
Rebuilding Trust: The Great Lockdown in 2020 has lent a major shock to public healthcare systems and has created an enormous trust deficit at both individual and institutional levels. In the manufacturing sector, trust erosion has emancipated in many forms, including withdrawal of labor from participation in production processes, opaqueness in supplier collaboration, and a lack of visibility into insights on key performance indicators of cost, quality, and expected timelines of delivery. As such decisions to deploy resources and engage them into manufacturing during ‘Unlock 1.0’ must be pivoted on addressing the trust deficit secularly first within enterprises and then scaling up across all enterprises constituting the supply chain in the manufacturing sector.
- Ensuring Health Protection: At the enterprise level, this calls for ensuring the availability of quality rated personal protective equipment (PPE) kits, and medical kits for all employees and the creation of fool-proof systems for implementation of standard operating procedures for regular sanitization of the physical environment at the workplace. The second imperative is to ensure transparency in sharing information on the deployment of such social distancing and contact tracing measures on a “need to know basis” among all stakeholders in the supply chain while staying within the ambit of data privacy.
- Fixing the Broken Fragments with Data: Reviewing supplier collaboration and manufacturing workflows today will play a huge role in creating an open and transparent dialog among OEMs, CMs, EPC enterprises, MSMEs, and suppliers across multiple tiers in the supply chain. A pilot project for mapping the supplier network can follow a template similar to the one used by bankers to conduct a stress test of debtors during the Great Meltdown of 2007 and focus on three Cs: character, capability, and credibility. One way to do this is by creating a similar stress test in manufacturing and encompassing the three Cs can be of paramount importance:
- What is the site location of the supplier including the city, region, and country? Do we have insights into the real-time status of COVID19 spread there?
- Is the supplier adhering to social distancing and contact tracing practices to steer clear of COVID19 risks?
- What are the parts procured from this site? What is the part number and description, part cost, annual volume for this part, rate of replenishment of inventory for this part, and the total spend (per year) from this site?
- What is the end product including the OEM’s end product(s) that uses this part? What is the profit margin for the end product(s)?
- What are the lead times from the supplier site to OEM sites in days?
- What is the Time to Recovery (TTR)? What time would it take for a site to be restored to full functionality if the supplier site is down, but the tooling is not damaged or if the tooling is lost?
- What is the cost of loss if expediting components from other locations is possible? If so, at what cost?
- Can additional resources (overtime, more shifts, alternate capacity) be organized to satisfy demand? If so, what is the cost?
- Does the supplier produce only from a single source? Could alternate vendors supply the part? Is the supplier financially stable? Is there variability in performance (lead time, fill rate, quality)?
- What are the mitigation strategies for this supplier-part combination? Who are the alternate suppliers? How to arrange excess inventory?
What Manufacturers Need to Do Tomorrow?
Enabling Business Processes with Technology: As enterprises in manufacturing and supply chain operations look to move beyond the immediate impact of the COVID19 pandemic over the next financial quarter, it shall make sense for them to scale up the best practices from the peak of the recessionary phase and integrate siloed data repositories for multiple functions into a compact source to pay (S2P) platform for a single-window approach to manage approvals and authorization for procurement decisions. This shall serve the purpose of augmenting enterprise-wide transparency and building greater efficiencies by facilitating multi-tenant models for collaboration spanning across the nerve center leadership, customer relationship, and supply chain teams to optimize costs. Small steps towards instituting a digital “cost control tower” to prioritize urgent and important payments and define clear reporting metrics for managers to track the liquidity status in real-time may over the period of the next financial quarter evolve into rolling forecasts to identify major areas of EBITDA risks and finally implement zero-based budgeting (ZBB) to achieve greater fiscal prudence for discretionary expenditures and indirect procurement. Authorization and access to such information systems may slowly be devolved amongst mid-level managers to move the enterprise forward along the lines of supply chain digitization and learning curve from a strategic to a tactical level
What Manufacturers Need to Do in the Future?
Build Futuristic Supply Chains using Advanced Tech: One of the major lessons coming out of the COVD19 pandemic for enterprises in manufacturing shall be gaining visibility into the next steps and future-proofing their supply chains. They will have learned the value of anticipating the next supply chain disruption in advance and adjusting their positions in the market while they still have time to do so.
Using Advanced technologies like contract management and predictive analytics that allow enterprises to stay informed on their supplier relationships, map the contributions of suppliers by value and volume, and assess their exposure to volatile business environments are likely to emerge as the enablers of de-risking supply chains. With AI, ML, and advanced analytics being able to capture deeper insights on the next steps in the supply chain right up to the end consumer, the direction of supply chain automation is likely to direct towards demand-driven planning and forecasting (DDPF).
While temptations to stay in denial of the challenges in a post COVID19 world and to retain the status quo may still be strong, enterprises shall do well not to risk a return to pre-COVID19 coordinates of workflow, collaboration, and distribution. Instances such as the Y2K, the subprime crisis of 2007, and climate change should serve an adequate warning to enterprises to steer clear of the lure of wishing away a rebound of challenges and then waking up to grave realities. A future that is driven by a high degree of technology enablement for information sharing, engaging in transparent dialogs to drive outcomes, and creating coordinated responses to a crisis may present us with a vertical upward shift in costs. Irrespective of how steep the shift in costs may be, it shall be prudent for enterprises to believe that they shall be able to pass on such incremental costs of technology enablement across the downstream of the supply chain right up to the end consumer.