Reducing Coronavirus Led Supply Chain Disruptions Now and Building Resilience for the Future
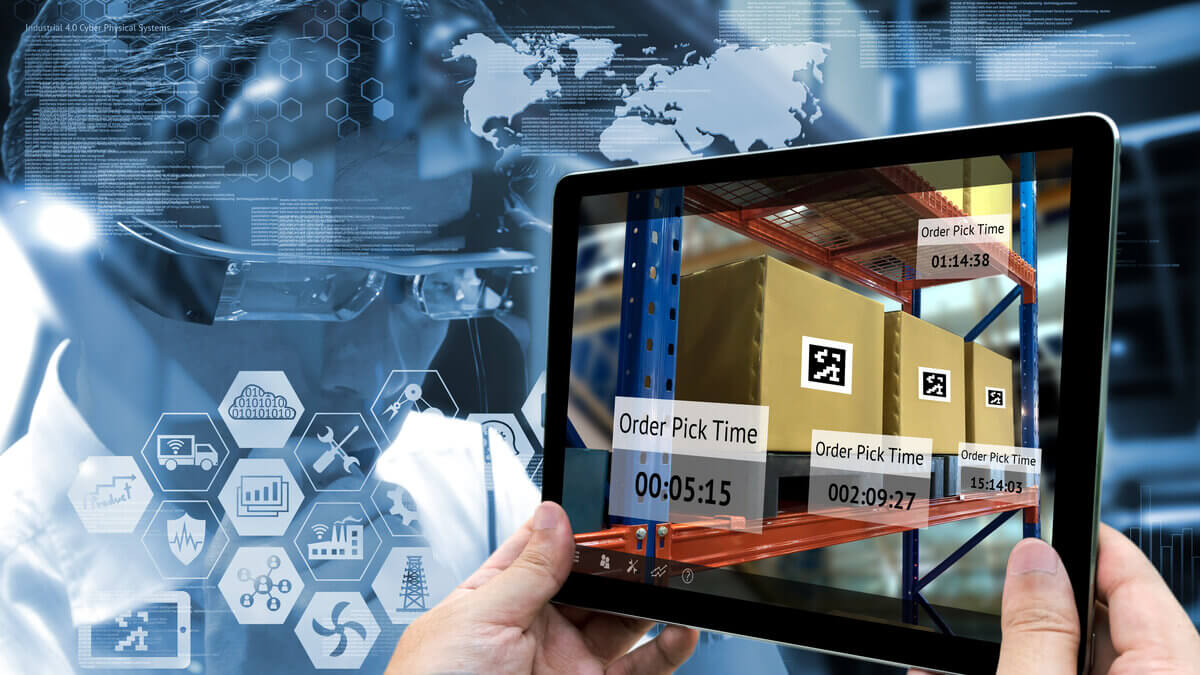
Credit ratings agency Fitch that had earlier pegged India’s real GDP growth rate for FY 2020-21 at 5.6% has now projected that the disruption caused by the contagion of the Novel Coronavirus throughout an integrated global economy could slow India’s real GDP growth rate by 0.5-1%. This projection notwithstanding, visibility into the impact on the global economy has been hard to come by. Josef Oehmen, associate professor at the Technical University of Denmark (DTU), Engineering Systems Design Group asserts that the Covid19 pandemic has no precedence that businesses can point to, no personal experience that corporate leaders can count on, no historical data for consultants to call on and therefore: there is no risk-adjusted value for businesses to act upon.
In fact, not since the end of the Second World War have countries and corporations experienced a supply chain disruption of such global scale and magnitude coupled with loss of lives of such tragic proportions.Prof. Patrick Hanohan from Trinity College Dublin asserts that even if the death rate is as low as in the case of flu deaths due to effective containment, there shall be repercussions: supply chain challenges in the short term and weakening of demand and spending cuts in the intermediate-term.
Wading Through Troubled Waters Now: Mitigating the Supply Chain Disruptions Due to Covid19
Given the spread of the pandemic across the globe, several industry verticals in the manufacturing sector are faced with immediate supply chain challenges.
First, is the dependence of some of the world’s largest companies or their suppliers that either has supply chain and procurement exposure to quarantined areas across three major economies: China, Italy, and South Korea. A study published in the Harvard Business Review asserts that 1000 such companies or their suppliers own more than 12000 facilities in such quarantined areas. Industry verticals with the highest supply chain and procurement exposure to quarantined areas in China, Italy, and South Korea include automotive, industrial engineering and heavy machinery (2,730), high tech and consumer electronics (3,238), healthcare (1,562) and consumer goods(1,139).
Second, in the context of the lockdowns announced by several regimes across the globe to suppress the spread of the contagion, enterprises in industry verticals like life sciences, healthcare, pharmaceuticals, and medical devices that need to produce “essential goods” urgently have been affected adversely. Major categories of supplies of these enterprises procured from quarantined areas include packaging, personal protection, medical dispensers, sterilized dressing pads, cables, and active ingredients.
What Needs to Be Done Immediately to Minimize Supply Chain Risks?
Given the supply chain disruptions facing enterprises in the manufacturing sector, the following contingency measures may be deployed on a war footing to save the lives of people and ensure the availability of goods:
First, enterprises need to create a contingency organizational structure to respond to the situation with a central leadership team at the corporate level showing the way. The central leadership team may be supported by a customer response team and most importantly a supply chain planning and operations team.
Second, the central leadership team shall have to ensure visibility into layered supply chains. They can do so by creating a database of components that are “critical to the mission”, trace the origin and flow of procurement and explore substitute suppliers.
Third, the customer response team may be entrusted to objectively assess the available inventory, calculate quantities of spare parts and after-sales-stock to keep manufacturing up and running and ensure downstream supply chain mobility and distribution to customers.
Fourth, the supply chain planning and operations team may be tasked with ensuring the first ring of personal safety for people by providing personal protective equipment (PPE) and collaborating with people on the production floor shop, warehouses, and nodal points in the supply chain to regularly monitor infection-risk levels. Further, the supply chain planning and operations team can do well to engage in logistics planning, identify points of risk, ensure the safety of goods during transit through effective sanitization and packaging and push for faster delivery of goods.
Recovering from the Economic Impacts on Covid 19 in the Intermediate-Term
Coming out of the Coronavirus crisis, business engagements will likely to be transformed forever.
First, enterprises that sail through the crisis shall like to adopt some of the major elements of their contingency measures to create a supply-chain risk function team. Such supply chain risk teams may be entrusted with the responsibility to map supply chain risks continuously and provide objective assessments to aid decision making in the domain of supply chain management and oversee risk governance.
Second, moving forward it shall be imperative for enterprises to strengthen supplier collaboration and work with entire supplier ecosystems that can provide a de-risked, geographically spread out and diverse model for global procurement.
Third, in the aftermath of the Coronavirus crisis, as enterprises shall stagger back to a new normal, they should ideally invest in the digitization of their supply chains to augment efforts of the supply chain risk team to anticipate the road ahead. Given the impact that the pandemic has had on supplier collaborations and contract compliance and obligation management of the manufacturing sector, it shall make enormous good sense for enterprises to invest in early warning systems, forecasting tools and comprehensive contract automation software suites that leverage artificial intelligence and machine learning capabilities. Returns from such investments in supply chain digitization assets shall manifest in the form of predictability of supplier capacity, turnaround times and rational expectations of risk factors and thus enable them to adjust their position in the market with time at hand.
Parting Comments and Epilogue: A Window into Supply Chains Post Coronavirus
Even as enterprises across the global economy continue to grapple with the challenges of the Coronavirus pandemic it is still unclear what the supply chain of the future would look like. However, amidst all uncertainties, one thing is clear: business won’t be business as usual and those that survive shall have to look at the supply chain function through a completely different lens that shall resemble the challenges and solutions of the future.
As Prof. Hua Lee, from the Department of Information and Technology at Stanford Graduate School of Business has observed, it shall not be enough to know what’s happening in your supply chain. Enterprises would need visibility outside their supply chain, know the capacity of other suppliers and modes to deploy them immediately when needed. Operational hedging shall be a necessity in the supply chains of the future with global suppliers being managed by inclusive procurement ecosystems driven by vendor consolidation. Parallely there shall be a greater need to increase logistical flexibility, design alternate transit routes and expand the geographical spread of warehousing facilities.