Stepping Up Safety: A Comprehensive Guide to Choosing the Right Workplace Shoes
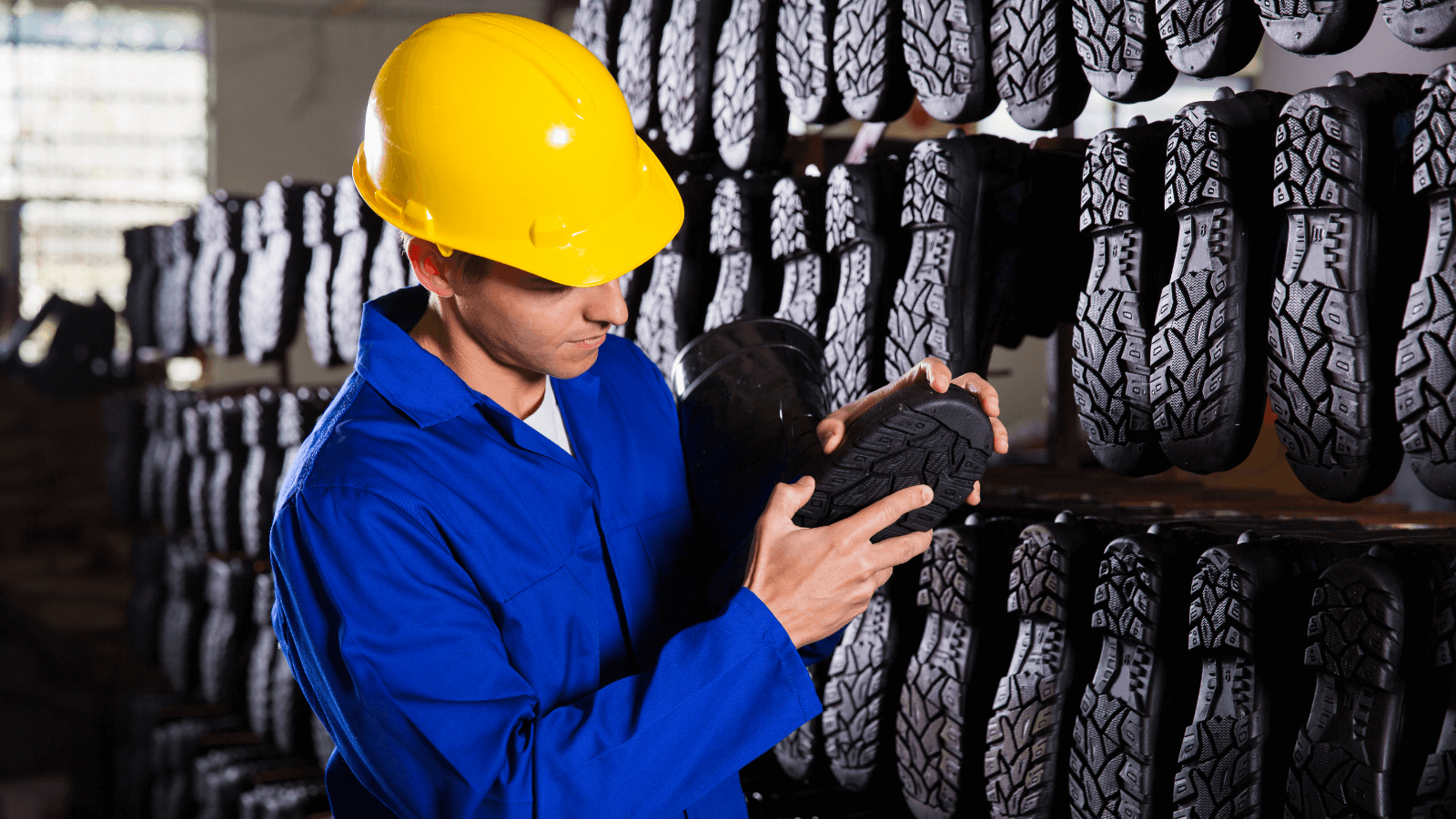
Stepping Up Safety: A Comprehensive Guide to Choosing the Right Workplace Shoes
Wearing safety shoes in the workplace is necessary to prevent injuries and protect workers from hazards such as falling debris, sharp objects, electrical hazards, and more. According to the Occupational Safety and Health Administration (OSHA), employers are responsible for providing employees with protective OSHA-compliant safety shoes when necessary. With various industries having different safety requirements, choosing the right type of safety shoe for the job is crucial.
Types of safety shoes
Steel Toe Shoes: These shoes are ideal for heavy-duty work environments where workers are exposed to heavy impacts and falling objects. The steel plate in the toe cap protects the feet from injuries caused by such impacts.
Composite Toe Shoes: Composite-toe shoes offer the same level of protection as steel-toe shoes but with a lighter weight and increased comfort. The composite material in the toe cap is lightweight and flexible, making it ideal for workers who need to be on their feet for long hours.
Slip-Resistant Shoes: Slip-resistant shoes are designed for workers who work on slippery surfaces or in wet conditions. These shoes are ideal for workers in the food and hospitality industry, construction workers, and those who work in wet environments.
Puncture-Resistant Shoes: These are engineered for workers often exposed to sharp objects, such as nails and broken glass. These shoes are ideal for construction workers, roofers, and those who work in environments with sharp objects.
Electrical Hazard Shoes: Electrical hazard safety shoes are designed for electrical workers and those who work near live wires. These shoes are made with non-conductive materials and are designed to keep the electrical current from flowing through the wearer’s body by providing necessary insulation.
Finding the perfect fit
Essential safety features: The most crucial aspect to consider when buying safety shoes is their ability to provide adequate protection against hazards. Shoes should be constructed with reliable and durable materials, including metatarsal guards, safety toe caps, and steel plate soles.
Comfort as a priority: Since safety shoes are primarily designed for use in adverse conditions, comfort is crucial. Shoes should have ample room for the toes, support the arch and heel, and be suitable for use in warm and cool climates.
Proper fit for optimal performance: Proper fit and ergonomics are crucial for the effectiveness of safety shoes in the long haul. The instep should fit snugly, and the ball of the boot should hold the ball of the foot for adequate grip.
Durable outsole offerings: In addition to insole safety measures, it is also important to consider the outsole features of safety shoes. Shoes should have a robust build that provides resistance against heat, chemicals, etc.
Balancing cost and quality: While purchasing from a trustworthy brand is recommended, it is also important to ensure that their features and capabilities justify the price of the shoes.
A stepping stone to a safer workplace
To ensure optimal foot safety, having the right pair matters the most. With Moglix as your trusted partner, you have access to wide variety of safety products & services across industries, addressing all types of applications with strong focus on quality and cost efficiency. TRUST MOGLIX for certified & complaint industrial safety products delivered, anywhere in India.
The Evolution of Industrial Piping Systems: Advancements and Innovations
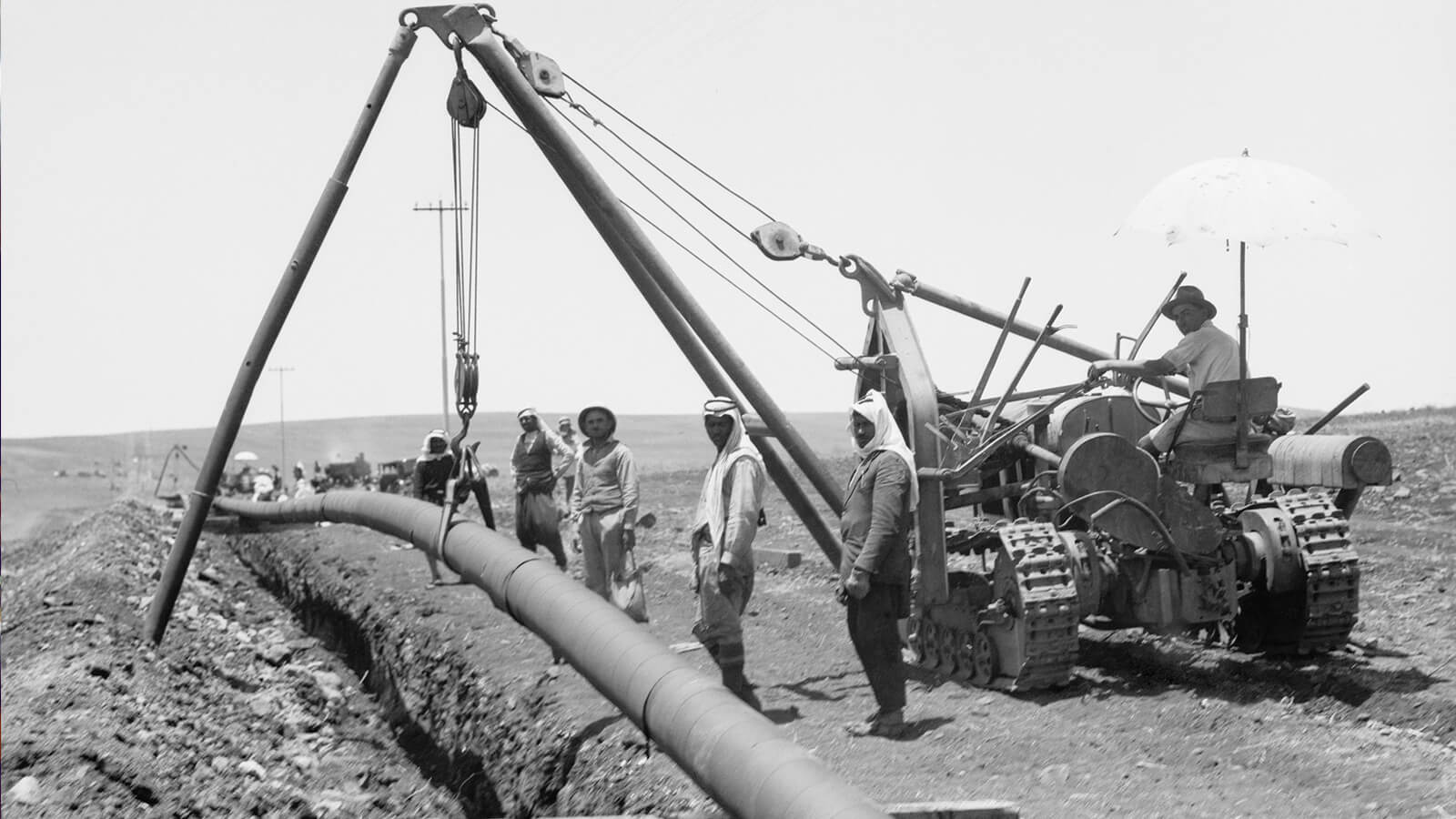
The Evolution of Industrial Piping Systems: Advancements and Innovations
From a limited choice of materials centuries ago to futuristic technology today, our piping systems have evolved tremendously. When the first known pipes were laid, metals were the most preferred industrial pipe materials for various applications. Let us take a trip down memory lane and discover how piping technology has evolved since then.
What the past tells us: A history of industrial piping solutions
A quick history review reveals interesting insights about different types of pipes. The ancient Egyptians had extensive copper piping in place as early as 3000 BCE, connecting and transporting water between their pyramids and temples. Historians and archeologists have discovered that despite the deteriorating conditions of the ancient structures, the copper piping remains nearly intact.
The Romans were another ancient civilization with impressive industrial piping solutions, like the use of aqueducts to source fresh water from mountain springs. However, with the collapse of the Roman civilization, the knowledge of industrial piping applications was lost briefly until modern piping solutions became necessary.
The rise of modern pipes as we know it
With the advent of The Industrial Revolution in the 18th century, the industrial piping sector witnessed various necessary advancements to keep pace with modern needs. Industrial piping solutions then evolved to transport gas and oil commercially.
Today, innovations in piping technology have given us various advantages over the vulnerabilities of ancient and mid-modern piping. Anti-corrosion technology and rustproofing techniques have extended the lives of industrial pipes tremendously. Sensors along industrial piping pathways make it easier to identify damages or leaks promptly.
And the use of different industrial pipe materials for specific applications has dramatically improved overall efficiency. For instance, copper remains in use to transport potable water, while steel may be a better fit for transporting natural gas and sewerage. On the other hand, high-density polyethylene (HDPE) is ideal for gas and oil undersea pipes.
What will the future of industrial piping be like?
The future of industrial pipes looks promising, with new technologies and materials being developed to improve the efficiency of industrial piping systems. Industries are also prioritizing more energy-efficient solutions with a smaller carbon footprint.
One area of focus is using advanced materials like composites to improve strength, durability, and corrosion resistance. 3D printing technology is also being explored to create custom pipes on demand and reduce lead times and costs.
Get a headstart on the journey to the future with innovative piping solutions.
Choosing the right industrial pipe materials is imperative to remain ahead of the curve and future-proof your business. Moglix can help you here with our comprehensive piping solutions that include various types of pipes and pipe fittings sourced from a plethora of top brands in the business. Get in touch with us to know more.
Common Errors in Industrial Pipe Handling and How to Avoid Them
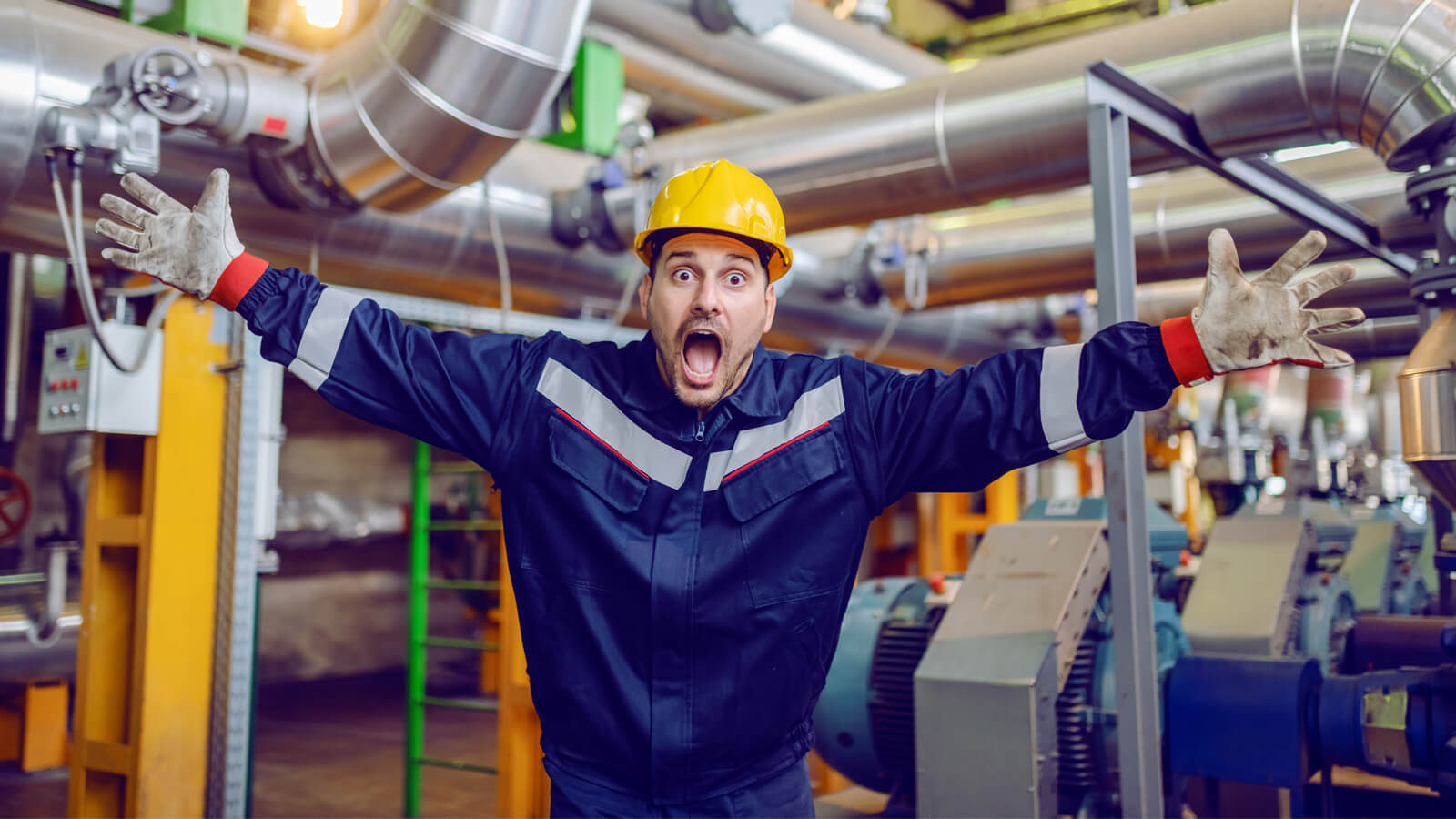
Common Errors in Industrial Pipe Handling and How to Avoid Them
As we take giant leaps into the future today, industrial pipes remain the arteries fueling progress across different sectors of the global economy. They are crucial for transporting water, chemicals and gases over long distances, across borders and even undersea along the ocean floor. The rising importance of industrial piping solutions is reflected in the growth predicted for the global pipe market, which could increase at a CAGR of 4.6% by 2032 (according to Future Market Insights).
That said, it is also vital to pay close attention to the common mistakes when laying, surveying and maintaining industrial pipes for different applications. Data from the U.S. Department of Transportation (DOT) lists several potential causes for leaks and accidents, including corrosion, welding defects, operator error and pipe defects.
If you are working with industrial pipes, it pays to be aware of the common pitfalls to avoid.
3 errors to avoid in industrial pipe handling
Several common mistakes can occur during industrial piping system design, installation, and maintenance. Here is a preview of the top vulnerable areas and how to avoid them.
Mistake #1: Improper cleaning and fitting
Installation of industrial piping requires tremendous precision and adherence to safety practices. To optimize their usable lives, the pipes need to be cleaned and prepared correctly before they are installed in the infrastructural framework. Furthermore, it’s also imperative that the piping is fitted in the right manner, so it remains free from potential damages and vulnerabilities.
The silver lining is that such mistakes can be avoided simply through proper and thorough planning before laying the pipes. You can seek expert assistance in this regard to ensure the pipes are fitted faultlessly.
Mistake #2: Choosing the wrong kind of pipe fittings
There are different kinds of pipe fittings, such as elbows, reducers, unions, couplings, crosses, plugs, adapters and caps. Each type of fitting has its own unique function, and using the wrong type of fittings, such as a reducer unit in place of bushings, can lead to the failure of the piping system sooner or later.
The solution to avoid this error is to seek the relevant expertise and use the right fittings for the right purpose.
Mistake #3: Ignoring manufacturer recommendations
Manufacturer recommendations for industrial pipe fittings may include information on proper installation and maintenance, suggested operating conditions and pressure ratings, and compatibility with specific types of pipes and fluids.
Additionally, manufacturers may also provide guidelines for the handling and storage of the pipe fittings. It is important to follow these recommendations diligently to ensure the safe and efficient operation of the pipe fittings.
A reliable sourcing partner can make your industrial piping solutions fail-safe.
You can avoid the costly errors discussed above by choosing a comprehensive piping solutions partner like Moglix. We provide various types of industrial pipes and pipe fittings from a variety of brands. In addition to being a one-stop solution for all your piping requirements, we also offer safety audit solutions.
Pipe Dreams: How Industrial Piping can aid a circular economy
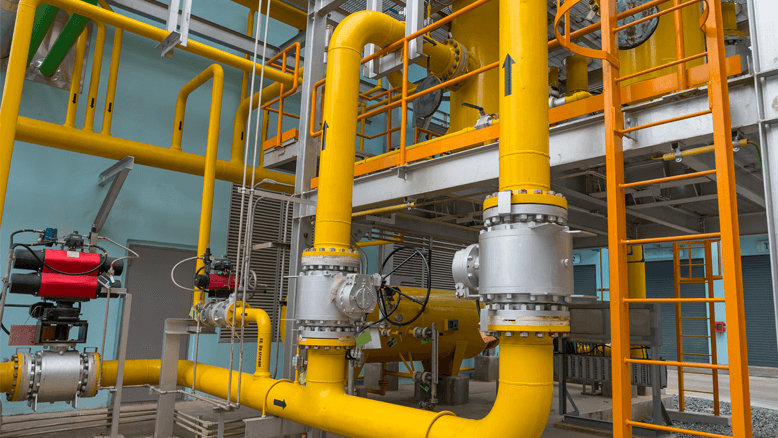
Pipe Dreams: How Industrial Piping can aid a circular economy
With sustainability and environmental awareness becoming hot topics in various industries today, the term ‘circular economy’ is becoming increasingly common. At its core, a circular economy is an economic system that aims to keep resources in use for as long as possible, extracting the maximum value from them while minimizing waste and pollution. Interestingly, there’s an unlikely but essential area to focus for commercial enterprises, while making the journey from a linear to a circular system — Industrial pipes.
Industrial pipes: A crucial piece of the puzzle in achieving circularity
Industrial piping is an indispensable part of modern infrastructure. Poor choice of industrial pipe materials could not only cost your business lakhs of rupees in extensive maintenance and repair but could also have severe and far-reaching environmental consequences.
Copper pipes, for instance, are particularly vulnerable to pinhole leaks arising from pitting corrosion. Debris can also be incredibly harmful in copper piping, resulting in uneven corrosion and causing some parts to decompose faster. Galvanized steel is a bit more rust-resistant, but piping in this category with threaded ends can be prone to leaks.
Water leakage from such industrial piping can cause the wastage of precious resources. And if the materials that leak into the surrounding environment are harmful industrial chemicals and gases, they could affect the immediate ecosystem severely.
Sustainability in different types of industrial pipes
Your business can avoid these grim prospects by choosing the right type of industrial pipes. Industrial pipes can also contribute to a circular economy in many ways. For example, pipes made from recycled plastic or metal can save on the use of virgin resources and reduce wastage.
Pipes made from durable and long-lasting materials can also be used longer, further extending the use of resources. They can also be efficiently processed at the end of their usable life, avoiding additional environmental harm. The bottom line is that the right kind of industrial pipes could pave the way for a circular economy by conserving resources, decreasing waste, and curbing pollution, all while efficiently facilitating the recycling and reuse of materials.
Choose sustainable industrial piping solutions today
Sustainability is the mantra driving the journey into the future, and industries today need to focus on choosing industrial pipe materials that check this box. Partnering with a comprehensive piping solutions partner like Moglix can make this much easier for your business. We help businesses in various industries find the right type of industrial pipes and pipe fittings for multiple applications from various brands without compromising the overall profitability of your venture. Know more
10th Task Force Meeting & Brand Connect, Bhubaneswar
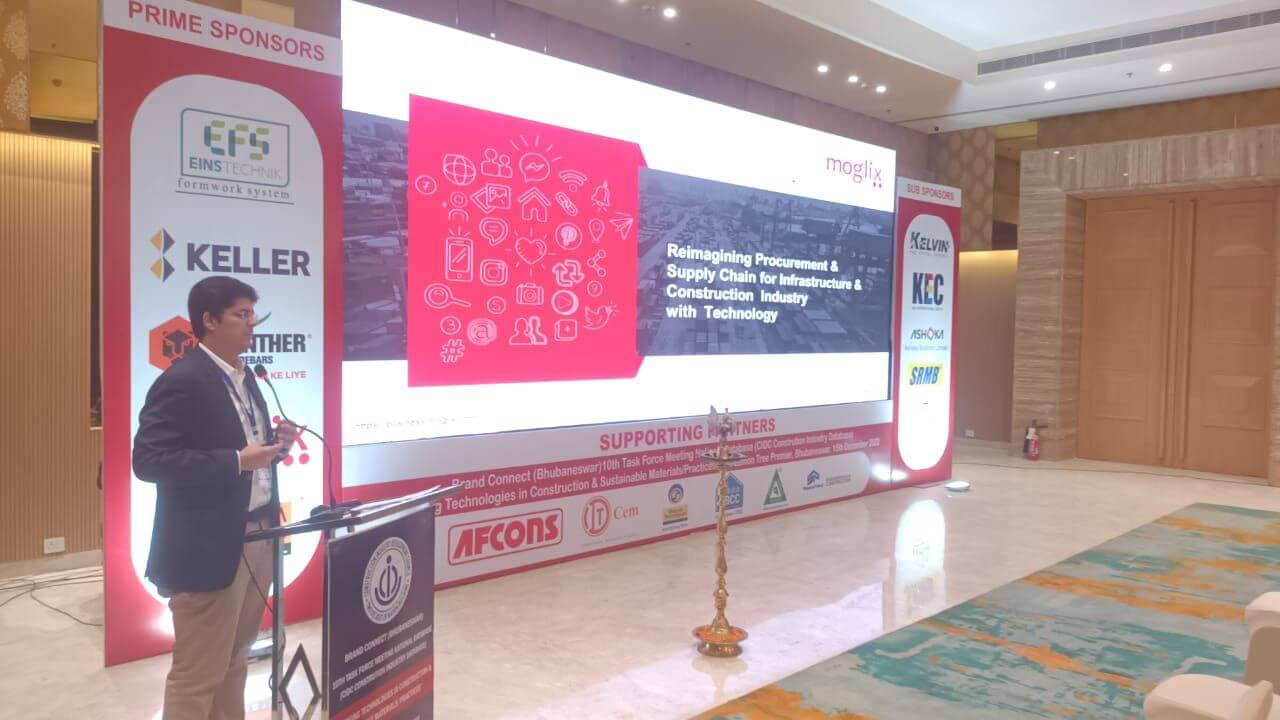
10th Task Force Meeting & Brand Connect, Bhubaneswar
Date : December 15, 2022
Organizer: Construction Industry Development Council (CIDC)
About the Event: Mr. Adhyan Anand, Associate Director, Infra & PSU, Moglix Business recently addressed the community of EPC companies and OEMs that are building India’s infrastructure, at the Bhubaneswar Chapter of the 10th Task Force Meeting & Brand Connect of the Construction Industry Development Council (CIDC).
Common types of Safety Audits: What are they?
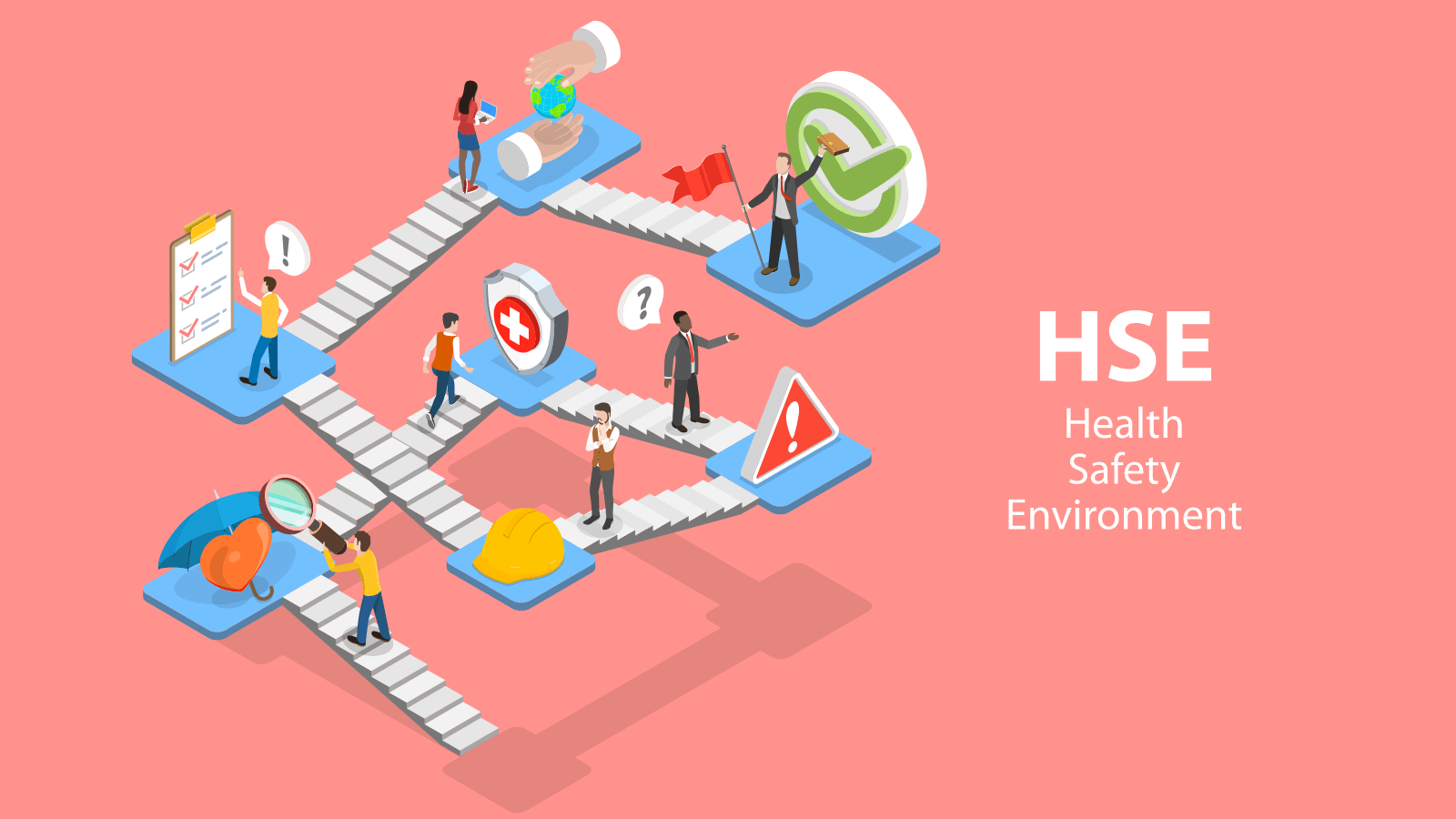
Common types of Safety Audits: What are they?
Every organization has several processes to ensure workplace safety, such as fire safety protocols and emergency exit routes. Adherence to workplace safety norms is one of the most significant indicators of an organization’s operational efficiency and commitment to the safety and health of its workforce. Since workplace safety is affected by many factors, it is pivotal to conduct safety audits periodically.
What is A Safety Audit?
A safety audit is an inspection to ascertain the efficacy of an organization’s workplace safety and health management systems. During a safety audit, data about an organization’s existing workplace safety and health protocols are recorded, analyzed, and compared to the regulatory compliance norms. In the previous blog on safety audit 101 we delt with broader types of audits, in this blog we go a little granular.
Types of Safety Audits
There are five major types of audits, namely, Electrical Safety Audit, Fire Safety Audit, Environment Safety Audit, Occupational Health & Safety Audit (OSHA), and Wash Audit. Each of these safety audits has a different scope and purpose; you must have clarity on your audit requirements to choose the right type of safety audit.
Electrical Safety Audits
Electrical Safety audits evaluate the safety and security of electrical installations prone to fire hazards. This encompasses a thorough inspection, testing, and verification of all kinds of electrical equipment and appliances in a facility. It also aims to identify possible hotspots, review emergency procedures and mitigate future risks to ensure compliance with applicable Safety Standards and Regulations. Reach out to us if you need to conduct a electrical safety audit.
Fire Safety Audits
Fire safety audits encompass various elements, like a review of your organization’s fire safety policy, assessing the level of competence of personnel in fire safety roles, and compliance with national legal regulations. These audits include onsite visits, interviews with different people in the organization, mock drills, document reviews, and more. Businesses of different sizes and sectors can benefit from fire safety audits. Reach out to us if you need to conduct a Fire safety audit.
Environmental Safety Audit
With sustainability increasingly prioritized across all industries globally, environmental safety audits are growing more relevant by the day. This kind of audit is suitable for all businesses — no matter their ecological management stage. It involves assessing the current policies and processes, identifying gaps in compliance, improving environmental responsibility, and implementing best practices. Reach out to us if you need to conduct an environmental safety audits.
Occupational Health and Safety (OSHA) Audit
Occupational Health and Safety audits identify risks and hazards in general workplace safety. This covers various aspects of today’s workplace, such as ventilation, waste management, housekeeping, medical aid, workstation ergonomics, and even management safety. Audit teams review OSHA elements, offer recommendations, and facilitate benchmarking against industry best practices. Reach out to us if you need to conduct a OSHA audit.
WASH Audit
An acronym for Workplace Assessment for Safety and Hygiene, WASH audits ensure that your organization adheres to the safety and hygiene guidelines notified by the Ministry of Home Affairs and other local, state, or national governmental entities. In addition, WASH audits assess how accessible and safe your company’s sanitation and water facilities are, identify areas for improvement and eliminate the risks associated with poor workplace hygiene. Reach out to us if you need to conduct a WASH audit.
Invest In Periodic Safety Audits
Since safety audits are instrumental in identifying gaps in an organization’s workplace safety norms, it is pivotal to ensure that such audits are carried out periodically. Should you require certified professionals to conduct any type of safety audit you can contact our team. At Moglix, we partner with organizations to provide safety solutions that go beyond just procurement of safety supplies. Our understanding of the entire value chain allows us to assist in essential actions like safety audits & end user training, that are often ignored, but important to create a safety culture within any organization. Reach out to us to know more on conducting safety audits for your facility or workplace
Safety audits 101: What are they, and why does your workplace need them?
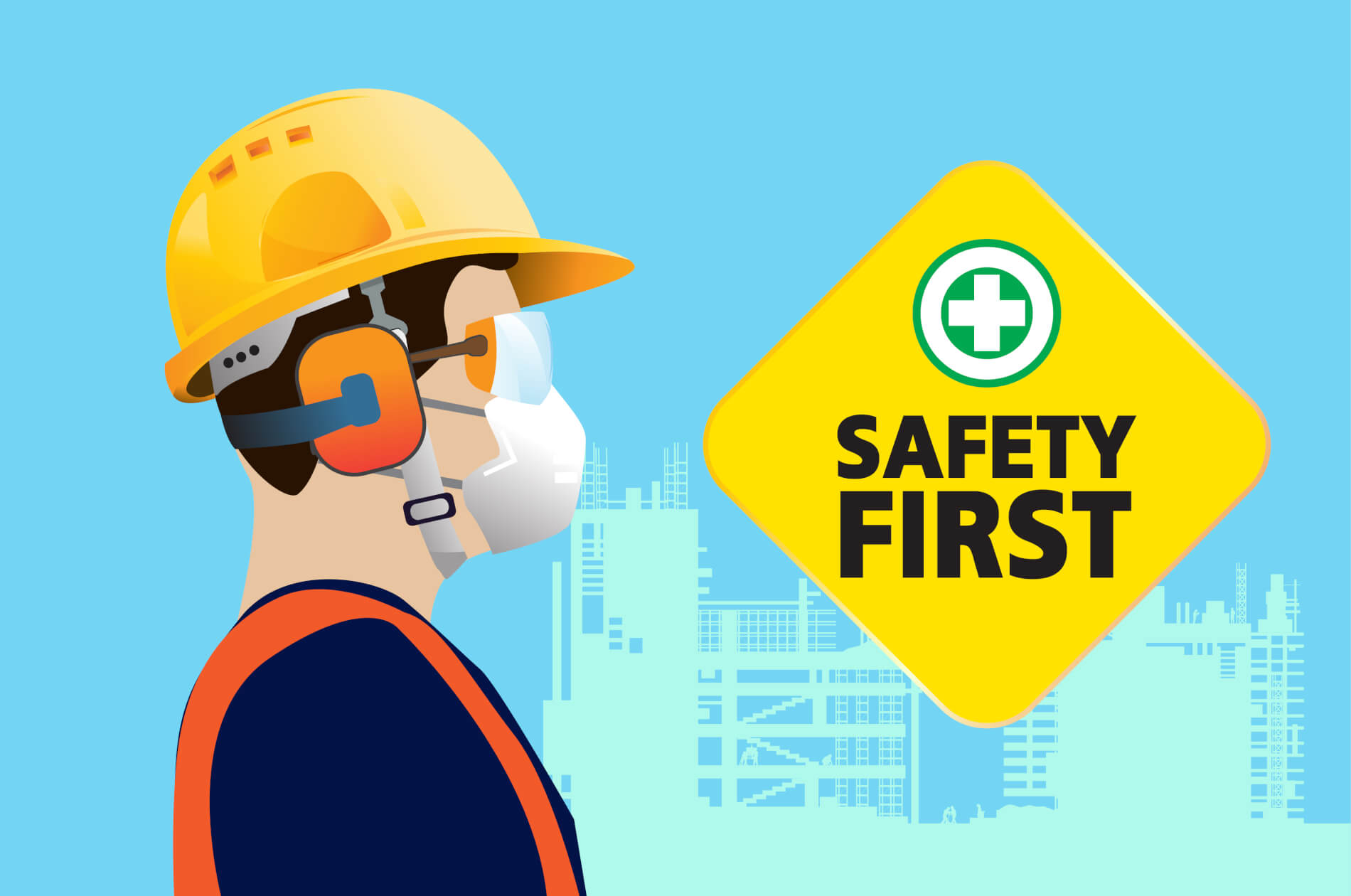
Safety audits 101: What are they, and why does your workplace need them?
Think your workplace is safe?
The International Labour Organization may have some grim news to put things in perspective — it estimates that around 2.3 million worldwide are yearly victims of work-related accidents or diseases. Regardless of the size of your business or the industry in which you operate, your organization may inadvertently be putting employees at risk.
Fortunately, a workplace safety audit can help you identify vulnerable areas in your corporate safety program and take timely measures to fix the gaps revealed. Here’s a closer look at what a safety audit entails and why it is an essential aspect of occupational health and safety (OHS) at your workplace.
Safety audits: What are they, and what do they entail?
A safety audit is a comprehensive process where the auditing entity gathers material information about the level of safety in a corporate workplace. Various aspects of safety, such as health risks, fire safety, and exposure to workplace hazards, are all evaluated as a part of this process. Typically, an audit of this kind is performed on the existing safety plan in the organization. The audit findings can help streamline the safety plan and bring it up to industry standards if needed.
Safety audits can be one of three kinds, as outlined below.
Compliance audits:
Here, the existing safety programs in your organization are reviewed to ensure they adhere to the local OHSA guidelines in place in your country.
Program audits:
These audits gather inputs from employees and workplace staff and evaluate how adequate your existing safety protocols and programs are.
Management system audits:
Management system audits combine both compliance and program audits. They simultaneously assess the adequacy of your safety programs and compare them against the regulations in place.
Three key reasons to prioritize periodic safety audits
Many businesses view safety audits through an anxious or skeptical lens. However, in the best interests of your employees and your business, a safety audit isn’t just optional — but essential today. Here’s why your business needs it.
To ensure regulatory compliance.
Depending on where your business has been established, you may have to comply with various local, federal/state, and central laws pertaining to OHSA. Timely audits allow you to comply with these regulations and avoid potential penalties.
To avoid lawsuits
Any harm caused to an employee can be a potential lawsuit, mainly if it involves legal non-compliance that directly or indirectly leads to harm. Safety audits by a competent partner can help you steer clear of these legal pitfalls by strengthening your company’s safety protocols.
To promote employee well-being.
Safety audits promote employee well-being, which is an oft-overlooked asset. A Harvard-MIT study revealed that, proactive safety audits increased sales by 37% and productivity by 31%. By regularly conducting safety audits, you can gain the advantage of improved revenue and decreased costs.
Bridge the gaps in workplace safety with a comprehensive audit partner today
Workplace safety is a complex target, requiring a healthy collaboration between your company and your audit partner. Moglix works with certified safety consultants and safety auditors to help you design proactive and periodic audit plans. Be it electrical, fire, OSHA or wash audit, we have certified professionals who can help you with any type of audit. Know More
Energizing India at 75 The Renewable Energy Supply Chain Transformation We Need to Fight Climate Change
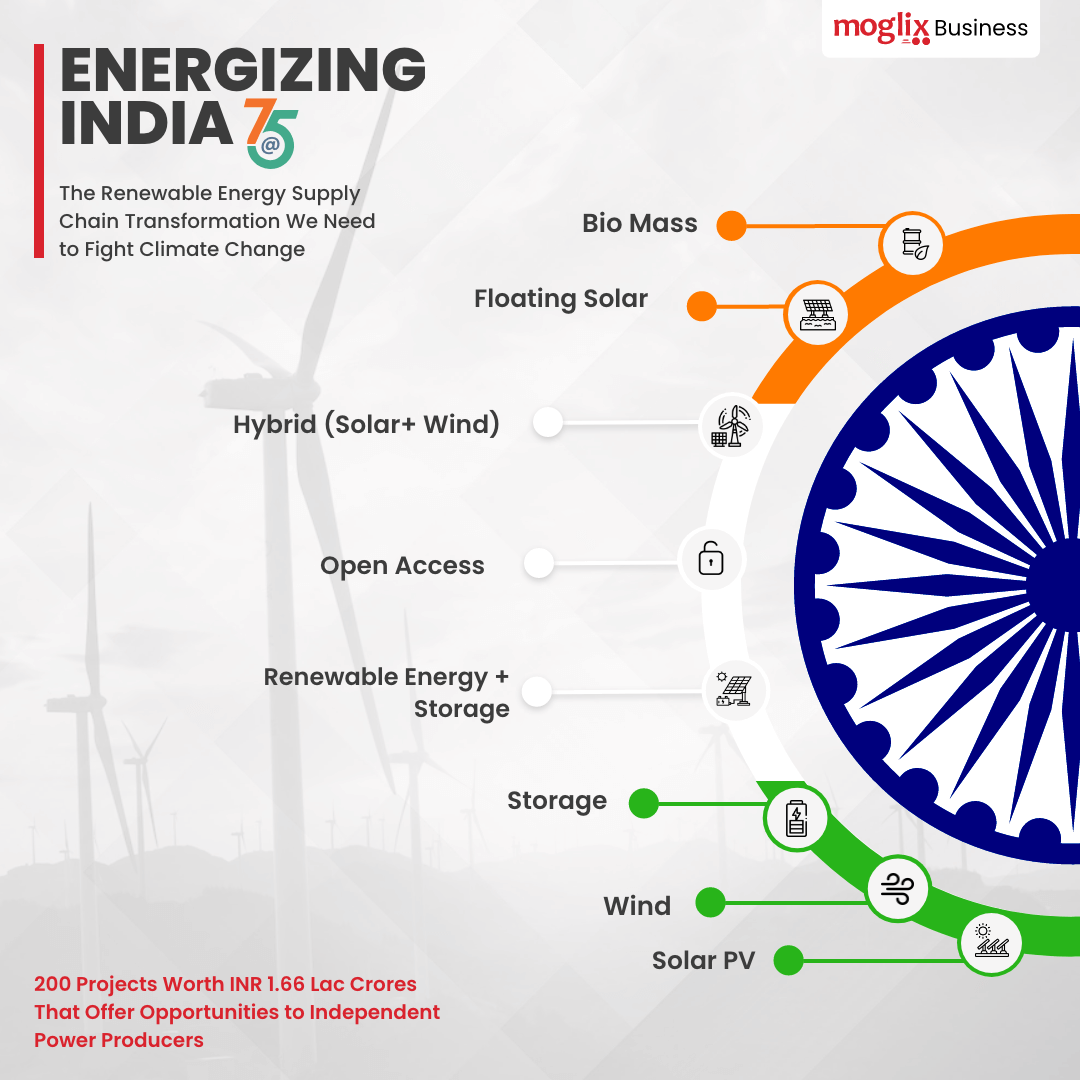
Energizing India at 75 The Renewable Energy Supply Chain Transformation We Need to Fight Climate Change
Back in December 2021, while writing an article for guest column of a leading business tabloid soon after the COP26 Glasgow Summit on climate change, we had commented on the next steps.
Our observation was that supply chain transformation will enable the smooth reconfiguration of value to reflect the real reprioritization of climate change in corporate value chains and value systems.
Governments will start clearing out carbon content from the supply chain, manufacturers will have to roll out innovative solutions with speed and scale to cash in on the opportunities. Everyone will have an active role to play.
The time for such a supply chain transformation has come. What makes each one of us at Moglix Business so confident about the renewable energy supply chain transformation? The answer to this question is in the e-book “Energizing India@75: The Renewable Energy Supply Chain Transformation We Need to Fight Climate Change”.
The Future of Renewable Energy Supply Chain in India; Digital and Made to Order for Agility at Scale
India’s next generation renewable energy mix to fight climate change will require a whole new approach to handling the manufacturing supply chain. From supplier capability mapping, quality management of made to order equipment like solar PV modules, solar PV cells, wafers/INGOTs to poly silicon, and monitoring work in progress, everything should come together on digitally integrated ecosystems and centralized data governance platforms.
It will ensure that all stakeholders in the ecosystem like IPPs, EPC companies, OEMs, MSMEs, lenders, and investors are relying on the same numbers to look from their respective vantage points.
Energizing India at 75: The Significance of the E-Book
We have tried to answer some difficult questions in this e- book. These include answers to the lenders’ checklist for offering credit to independent power producers, the debt equity ratio for such projects, and which sector offers the greatest incentives to IPPs?
True to the best of our knowledge, we believe that solar PV projects have an advantage. We have therefore done an end-to-end value chain analysis of the solar PV projects.
Complete Guide to Sustainability in Procurement
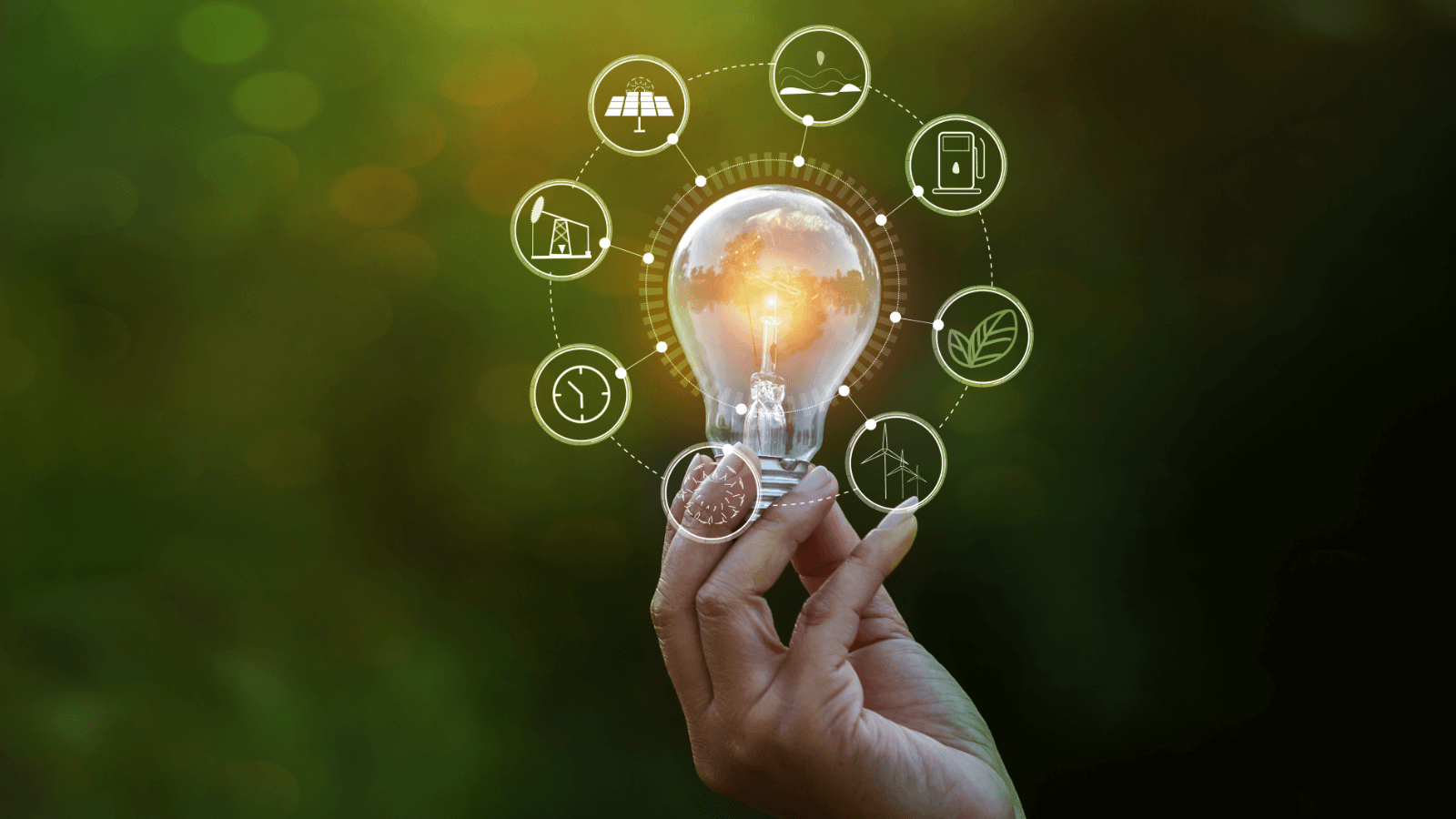
Complete Guide to Sustainability in Procurement
As per a study conducted by Mckinsey, only 20% of the CPOs surveyed said their companies used sustainability as a key criterion to make sourcing decisions. This is far from encouraging because sustainability is the future. Most industry leaders across the globe make the shift towards future-proofing their operations with sustainability at the core. Additionally, an increasing number of organizations are also driving their efforts toward tackling Environment, Social, and Governance (ESG) issues.
Against the backdrop of these developments, sustainability is the way forward for all facets of supply chain management, including procurement. Sustainable practices are crucial for procurement leaders who want to align their strategies with their organization’s overall principles.
With ‘sustainability’ being the buzzword here, let’s understand how MRO procurement can be transformed to accommodate this necessary principle.
Upgrade to Sustainable Procurement with 3 Simple Steps
Procurement is one of the most important functions in an organization’s supply chain. To implement end-to-end sustainability in your organization’s procurement function, it is pivotal to assess the status quo. Furthermore, you must detect the missing links and devise a comprehensive strategy to address these issues.
Here are the steps that you can adopt for a sustainable approach to all aspects of procurement, including MRO categories.
1. Take stock and ascertain the status quo/weigh up and mark the status quo: The first step is assessing where your supply chain stands and ascertaining its ESG impact. Once you have established the status quo, you must identify the elements of the supply chain which can be optimized. You may be faced with several bottlenecks in the process, for instance, the challenges in MRO procurement.
2. Develop a core strategy and plans to implement it: Having established the areas of improvement in the supply chain function, you must move on to the next step. Develop a strategy to incorporate sustainable practices and processes in procurement. This strategy should encompass all the elements of procurement, ranging from supplier selection to data management and visibility.
3. Drive a phased implementation of the sustainable procurement strategy: Implement an organization-wide sustainable approach to procurement in a phased manner, and make course corrections wherever necessary. It is critical to monitor every step of the transition and compare actual results with the planned ones. Subsequently, you must ensure that the necessary rectifications are implemented in a timely manner.
Switch To Sustainable Procurement Now!
Driving a shift from legacy systems in procurement to sustainable practices is a comprehensive undertaking. Therefore, assistance from experts can help streamline the transition. At Moglix, we can help you streamline your procurement function, including MRO procurement. Download our exclusive e-book to get your hands on an exclusive guide to help you nail the procurement game!
Are you looking to transform your procurement function? Send us your business queries at info@moglixbusiness.com.
Beware of committing the 5 Deadly Sins of Procurement
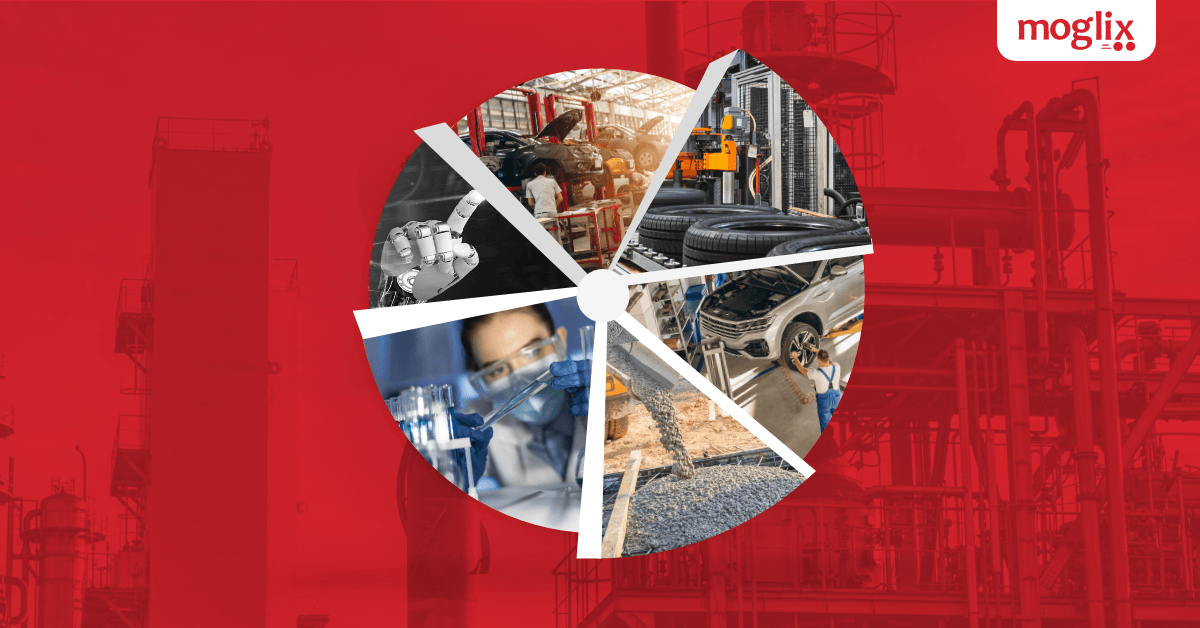
Beware of committing the 5 Deadly Sins of Procurement
Did you know that over 60% of enterprises rely on manual MRO procurement? But just because it’s prevalent, it doesn’t mean it’s the best strategy. If your organization is also yet to automate and upgrade its procurement process, here are two questions for you:
- Are you struggling to minimize expenses and keep track of costs?
- And are you piling inventory or facing material shortages?
It’s highly likely that you may have answered yes to either of these questions. Unfortunately, such gaps in the procurement process can cause consequential disruptions to your business operations.
Effective management of procurement, especially indirect procurement like MRO (Maintenance, Repair, and Operations), can considerably reduce unnecessary costs. However, curtailing costs alone is not enough. If the COVID-19 pandemic has taught us anything, it is that procurement dynamics are changing as rapidly as technology. Today, procurement spans across departments in companies — from finance to operations — advocating the need for a sound procurement strategy.
So, this Dussehra may be the perfect time for your organization to identify and steer clear of the fundamental errors in the procurement process. After all, the festival is all about the triumph of good over evil, and what better time than now to draw up a plan and fight the cardinal sins of MRO procurement?
5 Sins of Procurement
1. Getting your Sourcing wrong? Think Again
Indulging in any procurement activity without a robust sourcing strategy is calling trouble. From picking out the sellers, negotiating contracts, and buying the materials, vital sourcing channels and effective supply chain management are necessary. Many times there is a spike in demand for goods. You might need to procure from global networks to ensure timely delivery of the product. But, global markets are susceptible to volatility in the currency exchange market, time constraints, and import limitations.
You can mitigate supply risks by diversifying the sourcing channels and selecting the most suitable products and services you require to run the business.
2. Manual Processes are so last decade. What You can do instead?
Living in a digital world and relying on manual processes is outdated and inefficient. Doing things the old way can be comforting but waste time and money. One of the significant challenges in MRO procurement stems from investing time in manual tasks. They make procurement cycles lengthy and lead to increased operational costs.
By digitizing the procurement process, you can safeguard yourself from task burnout and working with poor-quality data. The advent of mobile apps and catalog-based buying ensures you undergo smooth procuring.
3. Streamlined Supplier Base
You might have a business where there is a need for specialized demands and unique materials. Often these necessities are met with a fragmented supplier pool and a decentralized procurement network. Such networks pose significant risks in carefully monitoring the procurement process and lead to massive costs, specifically in MRO categories. Additionally, a decentralized system leaves room for errors because individual departments/stakeholders purchase materials separately. It also results in poor management of data, thus suboptimal business analysis.
To reduce cost, waste, and risks associated with multiple supplier bases, you should opt for supplier consolidation and standardized pricing to beat the latent costs of the procurement: which will allow you with greater buying power and higher long-term returns.
4. Inadequate Analysis of Internal Needs
Faulty decisions always arise when you are uncertain about the company’s requirements and goals. Today, data is the world’s most critical resource, and its improper conduct will lead to inaccurate business forecasting. It paves the way for piling inventories because you cannot gauge the market demand and estimate necessary sales. It results in short budgeting and inferior overall outcomes.
Safeguard your business from the misery of inventory pile-up by strategic optimization. Avail of the benefits of vendor-managed inventory and enjoy the perks of an entirely data-driven process and demand-supply optimization. Also, with the help of an MRO aggregator, you can automate the procurement process and indulge in cost savings.
5. Shoddy Inspection in Contract Agreements
The biggest obstacle to the seamless procurement flow is the lags caused due to breaches in service and contract agreements. SLA breaches can result in delayed delivery of goods or subpar service performance. Moreover, seeking redressal from vendors becomes difficult if you do not follow proper contract management practices.
To avoid such violations, look at the finer points of the contract. Inspect the supplier proposal to keep away from making the wrong decisions.
Get Cracking with the proper steps
Managing MRO in procurement can get overwhelming if not tackled correctly. You can reimagine your procurement process with guided assistance from experts. Moglix, with its digital solution, can assess the pain points of your procurement process and elevate it to a new digital paradigm. Download this exclusive e-book, as it can be a helpful ally in your journey to ease the hassles of procurement.
Looking forward to transforming your procurement? Just send your business query to info@moglixbusiness.com.