How CEOs of EPC Project Developers Can Improve EBITDA Through Use of Prefabricated Structures?
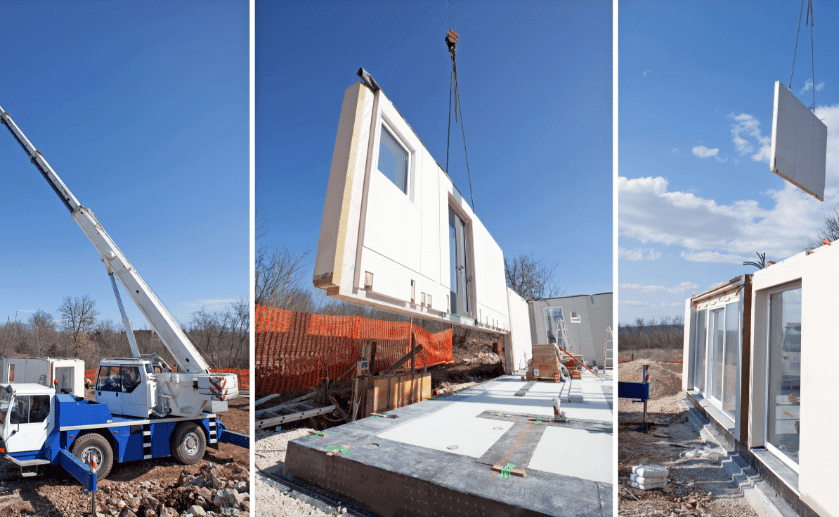
Can adopting prefabrication enhance the EBITDA for the EPC sector?
The answer is Yes. These days EPC project developers are already harnessing the benefits of Prefabrication.
In fact, in China, a famous construction company erected a structure in just 5 days. When research was conducted on the construction analysis, it revealed that prefabrication reduces construction timelines—by up to 36.04% for timber frameworks and 25.53% for masonry activities.
This evidence really makes it clear why firms should start leaning into prefabrication—it’s all about getting better results, both financially and operationally.
Let’s dive into how you can make that happen in this blog.
Boosting EBITDA with Prefabrication: A Strategic Shift for EPC Leaders
Think about it: prefabricated structures are quickly becoming the go-to for fast-tracking projects like schools, hospitals, and homes. And for the CEOs of EPC Project Developers, there’s a golden opportunity here to boost your EBITDA.
Enhanced Project Scheduling and Planning
Incorporating prefabricated structures into the infrastructure supply chain emerges as a strategic maneuver for CEOs of EPC Project Developers aiming to boost EBITDA, underscored by the tangible predictability enhancements it brings.
A pivotal productivity indicator, the project schedule, sees a notable uplift from prefabrication/modularization techniques.
According to feedback from industry stakeholders, 66% of respondents attest to a positive influence on project timelines due to Prefabrication, with 35% of them reporting schedule reductions of four weeks or more. A prime example of this is the assembly of the CitizenM Hotel in New York City using 210 prefabricated modules within 19 days, underscoring the profound efficiency and time-saving potential of prefabricated structures in meeting tight project deadlines and accelerating market readiness.
Improved Cost optimization
EPC CPOs aiming to boost EBITDA find a valuable ally in prefabricated structures, known for slashing project costs. According to Dodge Data and Analytics, 65% of over 800 AEC professionals surveyed report budget reductions, with 41% noting cuts of 6% or more. EVgo’s venture into prefabricated DC fast chargers, reducing installation times by 50% and costs by 15%, exemplifies this efficiency.
This approach acts as a strategic tool for financial and operational optimization in EPC ventures.
Risk Mitigation
Adopting Prefabrication offers CPOs a strategic path to enhance EBITDA through improved safety, a critical concern in the construction industry.
According to McGraw-Hill Construction, 34% of users report enhanced site safety with prefabrication, attributing this to fewer needs for high-risk activities like scaffolding work and minimizing tight-space operations.
Notably, CPOs, especially those in EPC firms, observe the most significant safety improvements, aligning risk management with financial optimization, thereby indirectly boosting EBITDA through reduced accidents and associated costs.
End Game: The Impact of Adopting Prefabricated Structures on EBITDA of EPC Project Developers
Prefabrication and modularization represent key strategies for EPC CPOs aiming to enhance EBITDA, offering benefits in efficiency, cost reduction, and site safety. As these construction methodologies gain traction, they are pivotal for competitive advantage and financial success.
For in-depth insights and implementation strategies, Moglix Business provides expert consultation. With a solid history in significant EPC projects and a comprehensive design-build-delivery framework, Moglix Business is a valuable resource for EPC professionals looking to optimise project outcomes through Prefabrication. Explore more to discover how you can transform your project delivery and achieve unparalleled success with Moglix Business custom fabrication solutions.