Overheating of Switchgear Components and How to Mitigate It
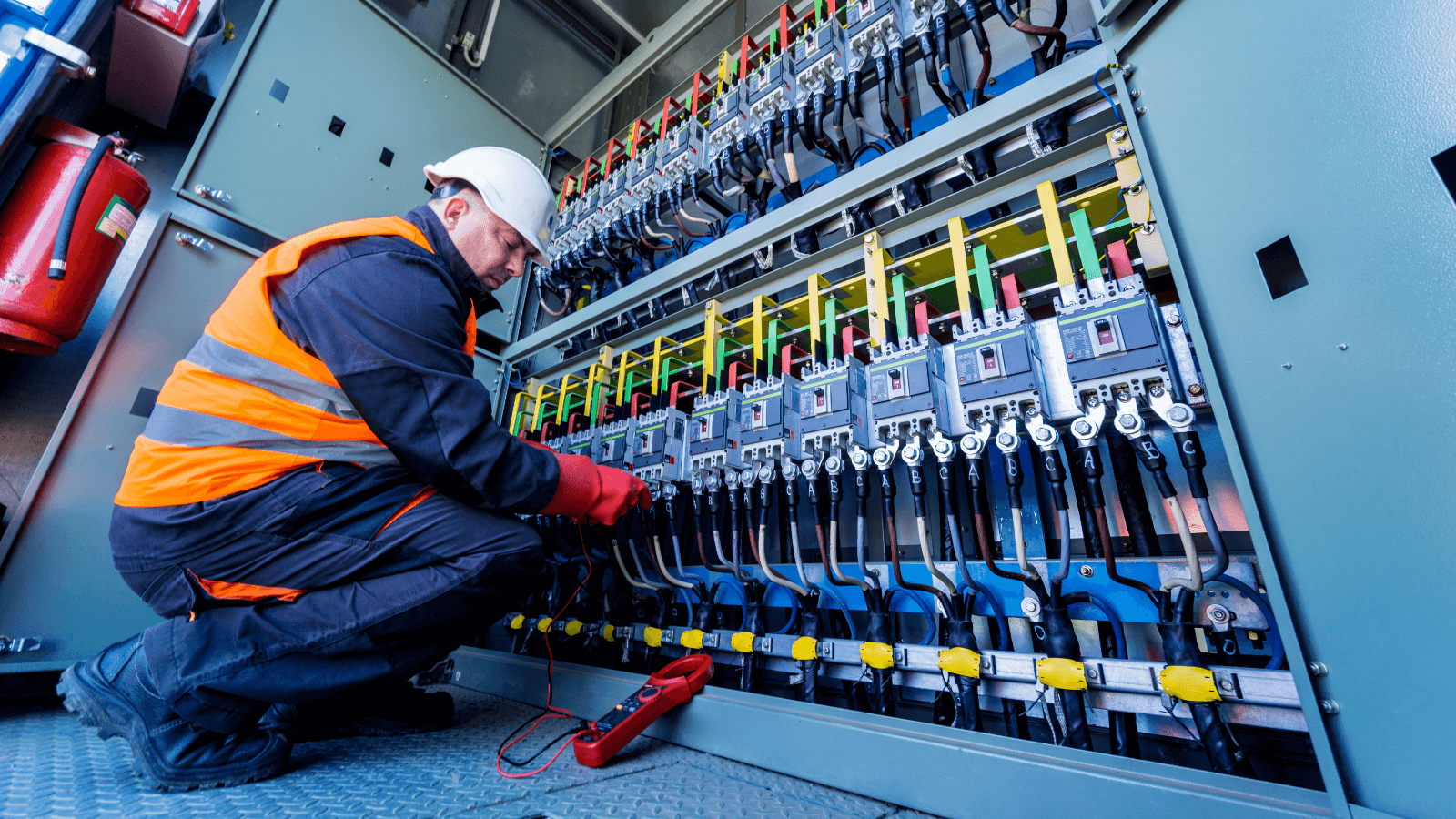
Overheating of Switchgear Components and How to Mitigate It
Switchgear components are essential for the safe and reliable operation of power distribution systems. However, like any electrical equipment, they can be susceptible to overheating. This not only leads to equipment failure and downtime but also poses safety hazards. Therefore, it’s crucial to maintain proper temperature control for switchgear components. Lets understand common causes of switchgear overheating and some practical tips and advanced solutions for mitigating it.
Common Causes of Switchgear Overheating
Overheating of switchgear components can occur due to various reasons, including:
Overloaded circuits: When the electrical load on a switchgear component exceeds its rated capacity, it generates excess heat, leading to overheating.
Poor ventilation: Switchgear components require adequate ventilation to dissipate the heat they generate. Poor ventilation can cause the heat to build up, resulting in overheating.
High ambient temperatures: When the ambient temperature exceeds the switchgear component’s rated temperature, it can lead to overheating.
Inadequate maintenance: Dirty and corroded contacts, worn-out insulation, and loose connections can all cause increased resistance and heat generation, leading to overheating.
Best Practices for Mitigating Switchgear Overheating
To mitigate switchgear overheating, the following best practices should be followed:
Regular inspection and maintenance: Switchgear components should be inspected and maintained regularly to detect any signs of overheating early on.
Proper ventilation: Adequate ventilation is crucial to dissipate the heat generated by switchgear components. The ventilation system should be designed and installed to meet the switchgear manufacturer’s recommendations.
Thermal imaging: Thermal imaging can be used to detect hot spots in switchgear components, enabling early detection and mitigation of overheating.
Load management: Electrical loads should be managed to ensure that they don’t exceed the switchgear component’s rated capacity.
Advanced Solutions for Switchgear Temperature Control
In addition to the best practices mentioned above, the following advanced solutions can be used for switchgear temperature control:
Active cooling systems: Active cooling systems, such as air conditioning and liquid cooling, can be used to cool switchgear components and maintain their temperature within the rated range.
Intelligent temperature monitoring: Intelligent temperature monitoring systems can be used to continuously monitor switchgear components’ temperature and adjust the cooling system as required.
Automated load shedding: Automated load shedding systems can be used to shed excess electrical loads automatically, preventing switchgear components from overheating.
Use Cases
To illustrate the practical applications of the solutions discussed above, let’s look at a few use cases:
- A switchgear component at a manufacturing plant was consistently overheating due to high ambient temperatures. To mitigate this, the plant installed an active cooling system that maintained the component’s temperature within the rated range.
- A thermal imaging survey detected hot spots in a switchgear component at a data center. The hot spots were caused by overloaded circuits. To prevent overheating, the data center implemented load shedding, shedding excess loads automatically to keep the switchgear component within its rated capacity.
Moving Forward
As technology advances, new solutions and innovations for switchgear temperature control are emerging. These include:
Advanced sensors: Advanced sensors can provide more accurate temperature readings, enabling better temperature control and more efficient cooling.
Artificial intelligence: Artificial intelligence can be used to predict when switchgear components are likely to overheat, enabling proactive mitigation.
Renewable energy sources: As more renewable energy sources, such as solar and wind, are integrated into power distribution systems, switchgear temperature control will become even more critical to ensure safe and reliable operation.
Overheating of switchgear components can lead to equipment failure, downtime, and safety hazards. Hence it’s important to identify the common causes of overheating and implement best practices. For all your switchgear supplies you can get in touch with us. Moglix, has the most comprehensive range of switchgear supplies and our pan india network of partners and warehouses ensure no place is remote for us to reach. Know more.
How to Prevent Workplace Electrical Fires: Root Causes and Actionable Strategies
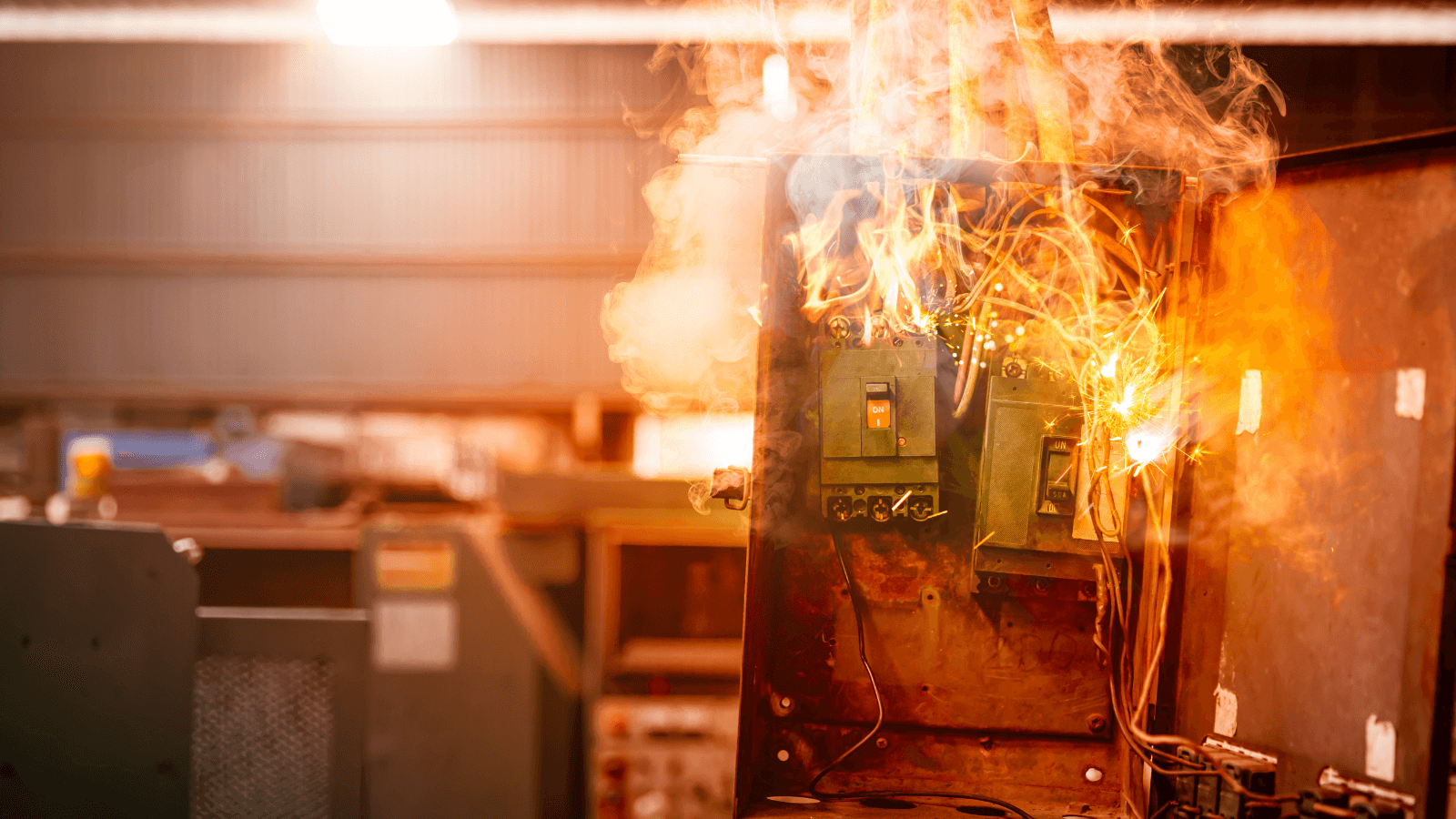
How to Prevent Workplace Electrical Fires: Root Causes and Actionable Strategies
Electrical fires are a common and devastating occurrence in the workplace. A study by the National Crime Records Bureau reveals that workplace electrical fires claimed the lives of 1,808 individuals in 2021 alone, equating to nearly five fatalities per day. However, as with many catastrophic events, the true cost extends beyond mere figures. Lives are forever changed, families grapple with loss, and businesses may never fully recover.
Understanding the causes of workplace electrical hazards and taking proactive measures to mitigate the risks can make all the difference. This blog delves into the causes and costs of workplace electrical fires and explores actionable strategies for businesses to prioritize workplace safety.
Connecting the Dots: Causes of Workplace Electrical Fires
Workplace electrical fires are often caused by faulty electrical equipment, poor electrical installation, improper grounding, overhead power lines, and misuse of electrical equipment. These factors can lead to electrical arcing, igniting nearby flammable materials, and causing a fire. Other common causes of workplace electrical hazards include overloaded circuits, exposed electrical wiring, and improper use of extension cords.
Fanning the Flames: How Workplace Electrical Fires Impact the Bottom Line
The financial cost of workplace electrical fires can be substantial. Beyond the apparent property damage, businesses may also experience a domino effect of losses, from decreased productivity and business interruption to increased insurance premiums. The cost of fire damage restoration and replacement of damaged equipment can quickly add up, and some businesses may not be able to recover from the financial impact of an electrical fire.
Recent studies show that workplace fires account for a staggering USD 328 billion in annual costs in the US alone, with 22% of these fires resulting from electrical sources. With such high stakes, companies must engage in business continuity planning to safeguard their financial health and long-term viability.
Shock-Proof Your Business: Best Practices for Preventing Workplace Electrical Fires
Businesses must prioritize electrical safety to mitigate the risk of workplace electrical fires. This can be achieved by implementing proper electrical installation and maintenance procedures, employee training programs, and regular equipment inspections. Here are some steps that businesses can take to minimize the risk of workplace electrical fires:
Conduct regular electrical safety inspections: Regular inspections of electrical equipment and wiring can help identify potential hazards before they result in a fire and enable electric fire prevention.
Develop an electrical safety program: A comprehensive electrical safety program can provide employees with the knowledge and tools they need to use electrical equipment safely.
Provide regular training: Ongoing training can help employees stay informed about the latest electrical safety practices and guidelines.
Invest in Quality electrical supplies – Invest in high quality electrical supplies like switchgears, wires and cables etc. Best would be to source it from a one stop solution provider like Moglix so that you have access the comprehensive product range from bets in class brands
Ensure proper installation and maintenance: Proper installation and maintenance of electrical equipment can help prevent electrical fires caused limited product understanding. Moglix has on roll electrical experts that can guide through procurement, installation and maintenance cycles.
Promote a culture of workplace safety: Encourage employees to prioritize safety and report any potential hazards immediately.
OSHA Compliance: Ensuring compliance with Occupational Safety and Health Administration standards can also help in fire risk management.
Wiring a Safer Future
Mitigating the risks of workplace electrical fires requires a comprehensive approach that prioritizes electrical safety through regular inspections, employee safety training, and proper equipment installation and maintenance. By taking these steps, businesses can create a safer work environment for their employees and minimize the risks and costs associated with electrical hazards. At Moglix, we are committed to the cause of employee safety in the workplace. Contact us today to explore supplies and solutions that keep your workplace safe from fire related accidents
Breaking Barriers: How Manufacturing and Start-Ups are Paving the Way for B2B Success in Uttar Pradesh
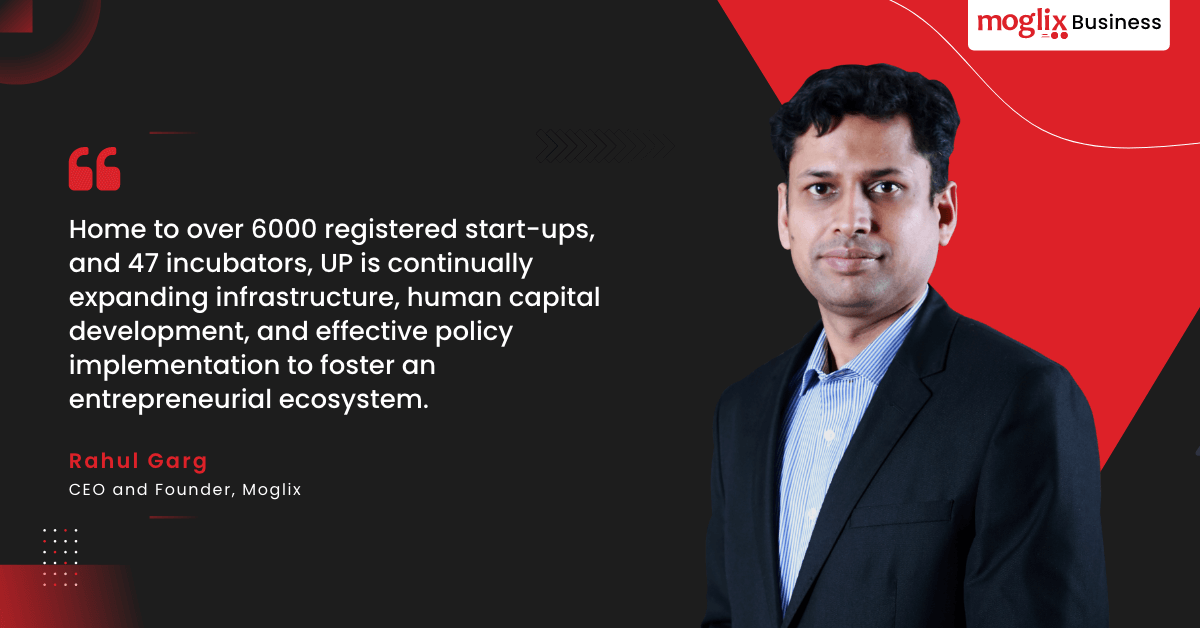
Breaking Barriers: How Manufacturing and Start-Ups are Paving the Way for B2B Success in Uttar Pradesh
By virtue of its investor-friendly policies and ease of doing business, Uttar Pradesh is fast emerging as the most preferred investment destination . Supported by a robust and growing start-up environment, the state is on the road to achieve its target of 1 trillion USD economy by 2030.
By 2030, India will have the manufacturing potential to export goods worth $1 trillion, putting it on the global manufacturing map. One of India’s most important economic pillars is the manufacturing industry, which employs over 27.3 million people and accounts for 17 percent of GDP.
Breaking Boundaries: An Interview with Sandeep Goel, MD of Moglix on the Power of Getting Uncomfortable
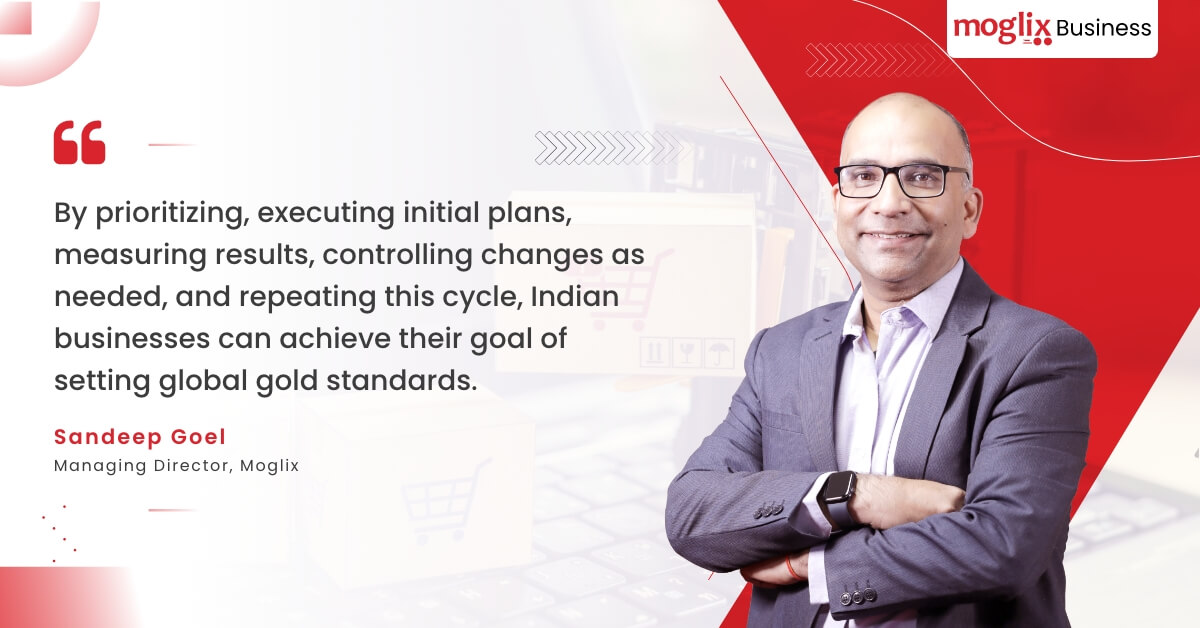
Breaking Boundaries: An Interview with Sandeep Goel, MD of Moglix on the Power of Getting Uncomfortable
Late November in 2022, I boarded a flight from Delhi to Hyderabad, and walked through the aerobridge, as I was greeted by a smiling airhostess “Sir, welcome aboard” it suddenly struck me that I was without mask, and she did not ask me to put one either. I had an almost instant smile on my face as the realisation dawned that Covid is now officially a thing of the past. The realization triggered a series of happy feelings – freedom, excitement, relief and above all finally “being normal”. And I reflected what a year it has been – 2022, a year of challenges and triumphs.
Prioritization was to ensure we spend our time on the right set of things, and rigor was required to ensure we do a good job of delivering on selected priorities when you run things on high rigor, conflicts are bound to come up.
Sandeep Goel said
Why We Need to Rethink PPE for Women in Industry?
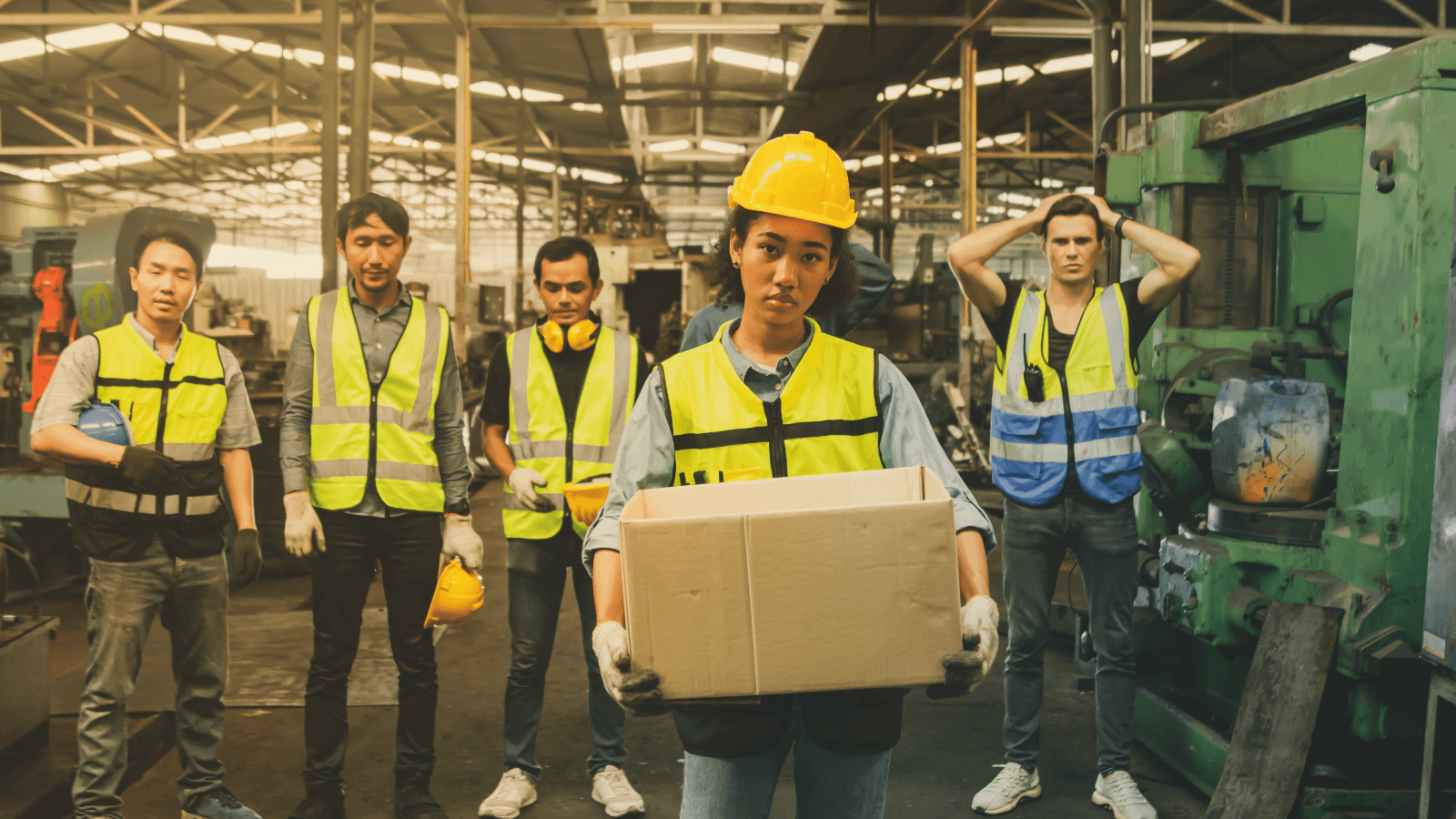
Why We Need to Rethink PPE for Women in Industry?
When we think of personal protective equipment (PPE) in the industrial sector, we will likely picture a bulky suit and helmet on a male worker. However, this image fails to acknowledge the millions of women working in industries that require PPE. Women face unique challenges in the workplace, including ill-fitting PPE and inadequate safety gear, which can expose them to dangerous working conditions.
Despite the pressing need for gender-specific PPE, a recent Women in Global Health study(1) reveals that about three-quarters of the women surveyed experienced problems with PPE fit, and a mere 14% reported using exclusively fit-tested PPE. This alarming finding is a cause for concern as poorly fitting PPE can lead to reduced productivity, injuries, and in severe cases, fatalities. The fact that women face such challenges in obtaining appropriate PPE should be treated as a critical issue that requires our immediate attention to ensure women’s safety at manufacturing facilities.
One Size Does Not Fit All: The Gender Gap in PPE Procurement
The lack of awareness within some organizations of women’s unique PPE needs and female-friendly safety equipment is a primary challenge women face. The all too common “one size fits all” strategy is often employed in PPE procurement, leading to employers neglecting the purchase of PPE designed for women and displaying indifference towards their safety.
Additionally, the male-dominated construction industry culture presents another significant barrier to women’s access to adequately fitting PPE. Women are frequently expected to make do with PPE designed for men, modify their gear, or purchase their PPE outright. This culture of indifference must be challenged, and solutions must be sought to provide female worker safety in the manufacturing sector.
Procuring for Diversity: The Importance of Gender-Specific PPE
The importance of addressing PPE challenges for women cannot be overstated. In many industries, women are exposed to the same risks as men, including exposure to chemicals, heat, and electrical hazards. Without adequate protection, women are at risk of injury or even death. To be effective, the safety-oriented design and production of PPE must cater to the distinct requirements of every gender.
In addition to the moral imperative of ensuring women’s safety, there are practical reasons to address PPE challenges for women. When workers feel safe and protected, they are more likely to be productive and engaged in their work, leading to a more positive and efficient work environment.
Empowering Women with Innovative PPE Solutions: Join the Revolution
Unfortunately, many women still face unique challenges regarding selecting and using PPE in the workplace. To bridge this gap, employers must engage women in the PPE selection process and thoroughly assess their needs.
Thankfully, some manufacturers have recognized the need for gender-specific PPE and are leading the charge toward innovation in this area. Women’s PPE is now being designed to fit the female body shape, with adjustments made for height, waist size, and shoulder width differences. The use of softer materials and more flexible fabrics not only improves comfort and range of motion but also promotes safety.
Moreover, In order increase adoption women’s PPE is now being made more practical and appealing, with various colors, patterns, and form-fitting designs. This is a welcome change as it encourages women to wear their PPE more often, improving safety and reducing the risk of workplace accidents.
At Moglix, you have access to the most comprehensive range of safety supplies and solutions. You can find a range of PPE solutions specifically designed for women at workplace. Contact us today and partner with us to build a safer environment for women.
The Digital Revolution of Receivables Finance in GIFT City
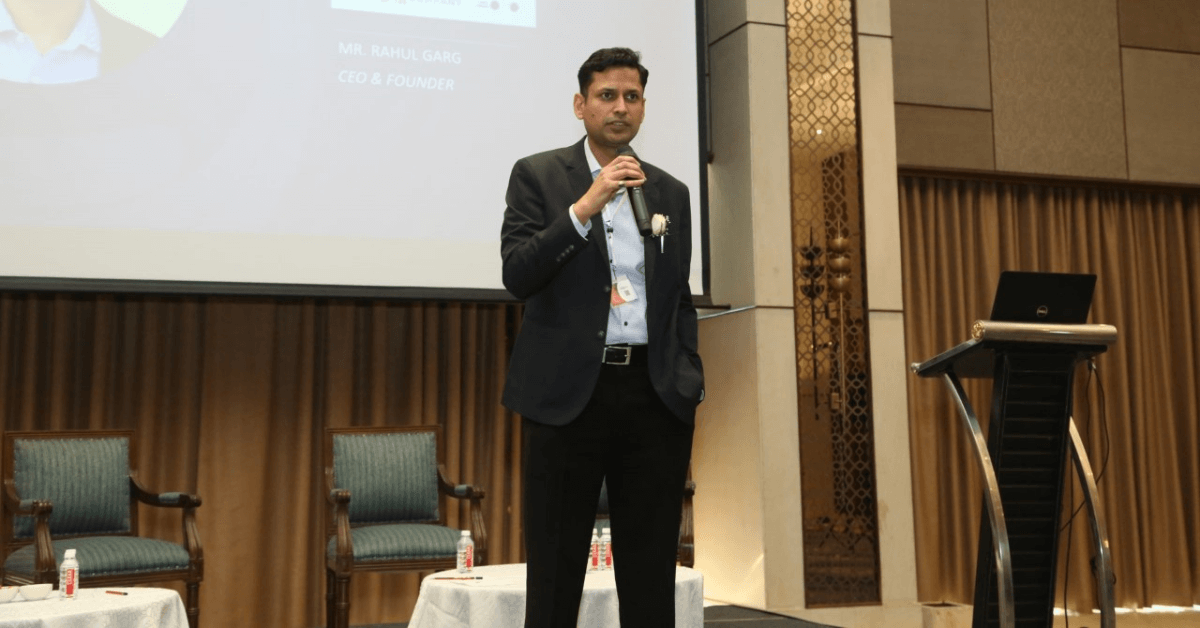
The Digital Revolution of Receivables Finance in GIFT City
Date : February 27, 2023
Organizer:FCI
About the Event: Mr. Rahul Garg, Founder & CEO, Moglix & Credlix, recently shared his experiences on “Manufacture in India, for the World: Export Factoring led Growth” at The Digital Revolution of Receivables Finance in GIFT City, Gujarat.
Indian Automotive Value Chain Summit
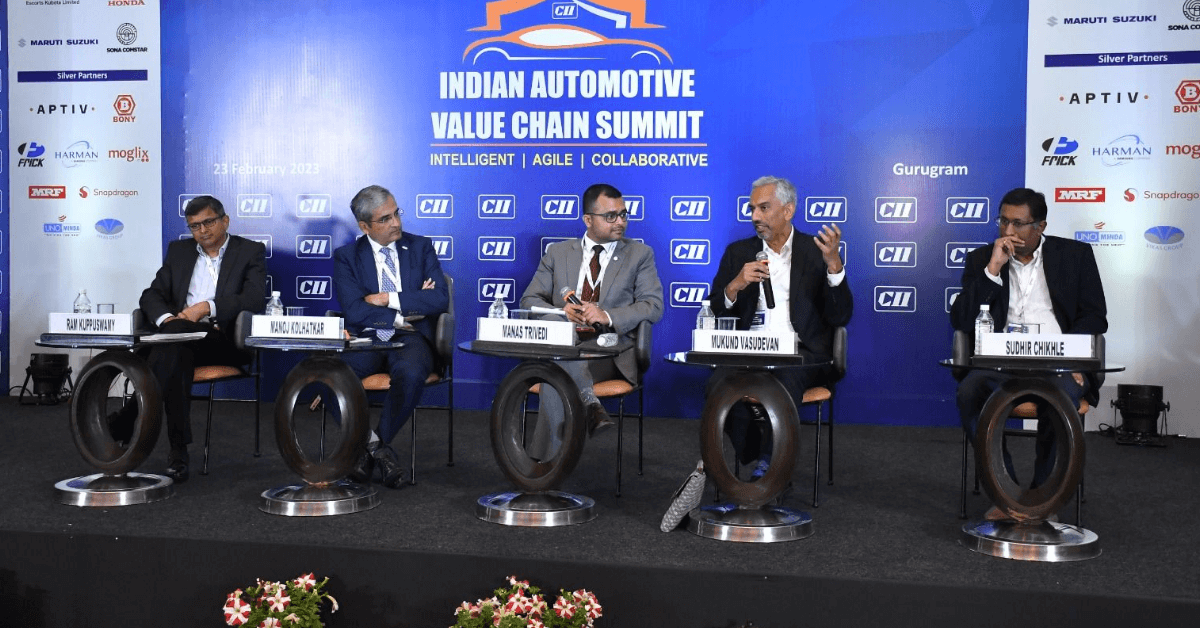
Indian Automotive Value Chain Summit
Date : February 23, 2023
Organizer: CII
About the Event:Mr. Mukund Vasudevan, Managing Director, Moglix recently shared his perspective on ‘Transforming Indian Automotive Industry – Supply Chain Strategy, For Now, Next & Beyond’ at the Indian Automotive Value Chain Summit organized by Confederation of Indian Industry in Gurugram.
9th CFO Vision and Innovation Summit and Awards
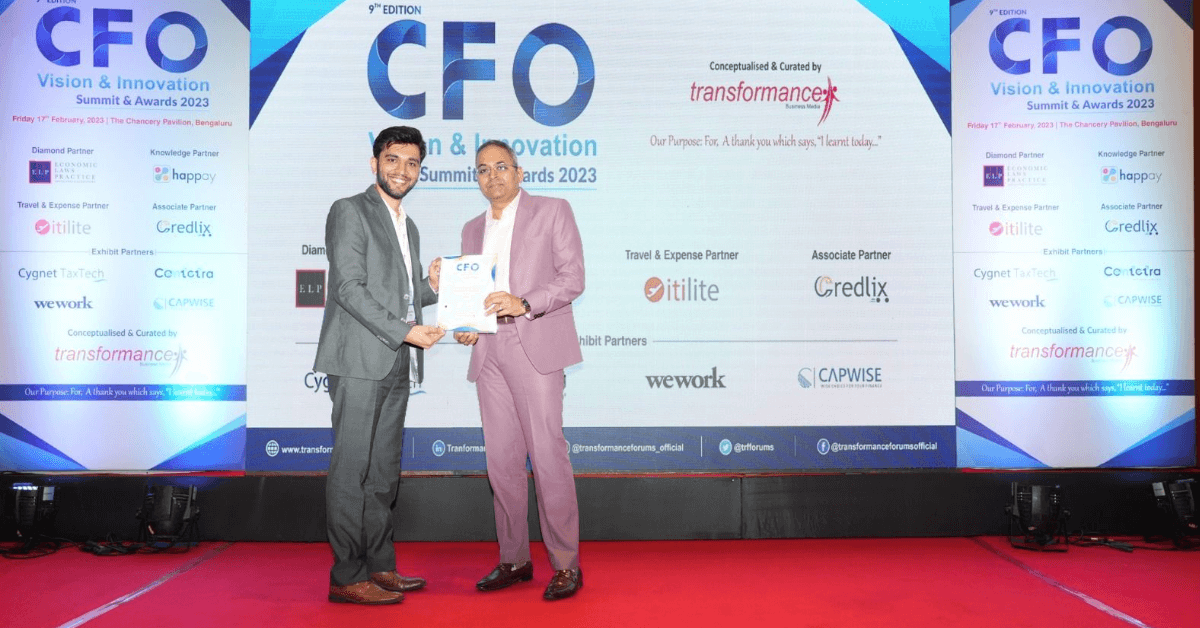
9th CFO Vision and Innovation Summit and Awards
Date : February 17, 2023
Organizer: IMA
About the Event:: Mr. Kailash Rathi, Director, Credlix recently shared their perspective on “Choosing the right digital supply chain finance platform” at the 9th edition of CFO Vision & Innovation Summit and Awards 2023 organized by Transformance Forums.
CEO Forum Session: Tech@Core: Building a Digitally Mature Organisation
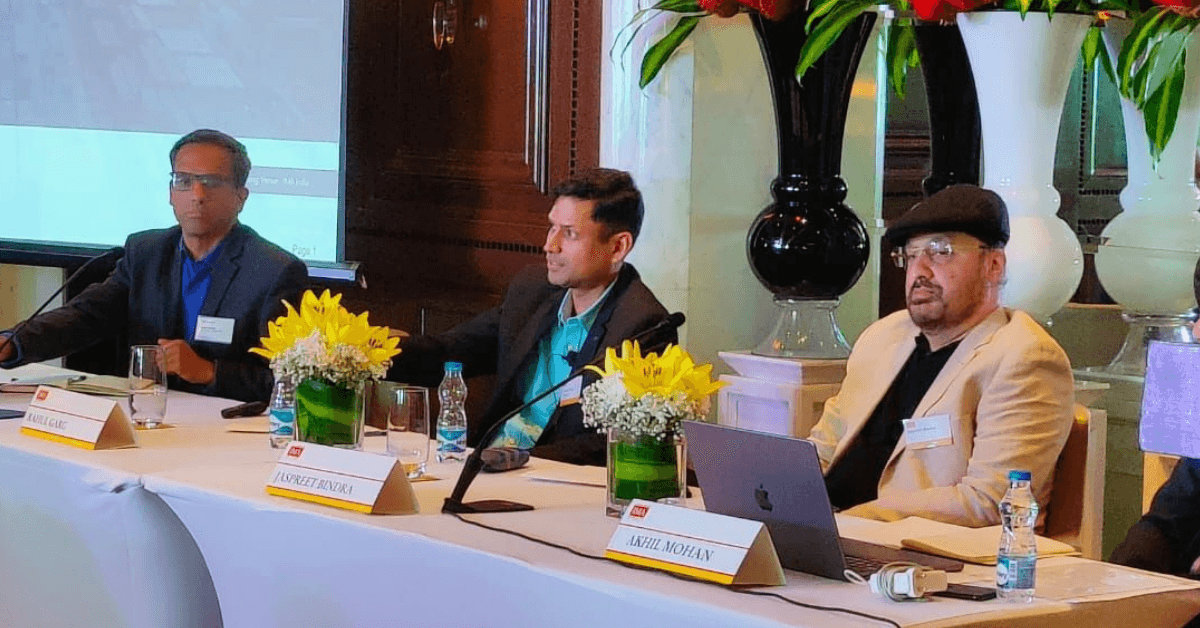
CEO Forum Session: Tech@Core: Building a Digitally Mature Organisation
Date : February 15, 2023
Organizer: IMA
About the Event:Mr. Rahul Garg, Founder & CEO, Moglix shared his thoughts on ‘Tech@Core: Building a Digitally Mature Organization’ at IMA India’s CEO Forum Session in Delhi.
Uttar Pradesh Global Investors Summit 2023
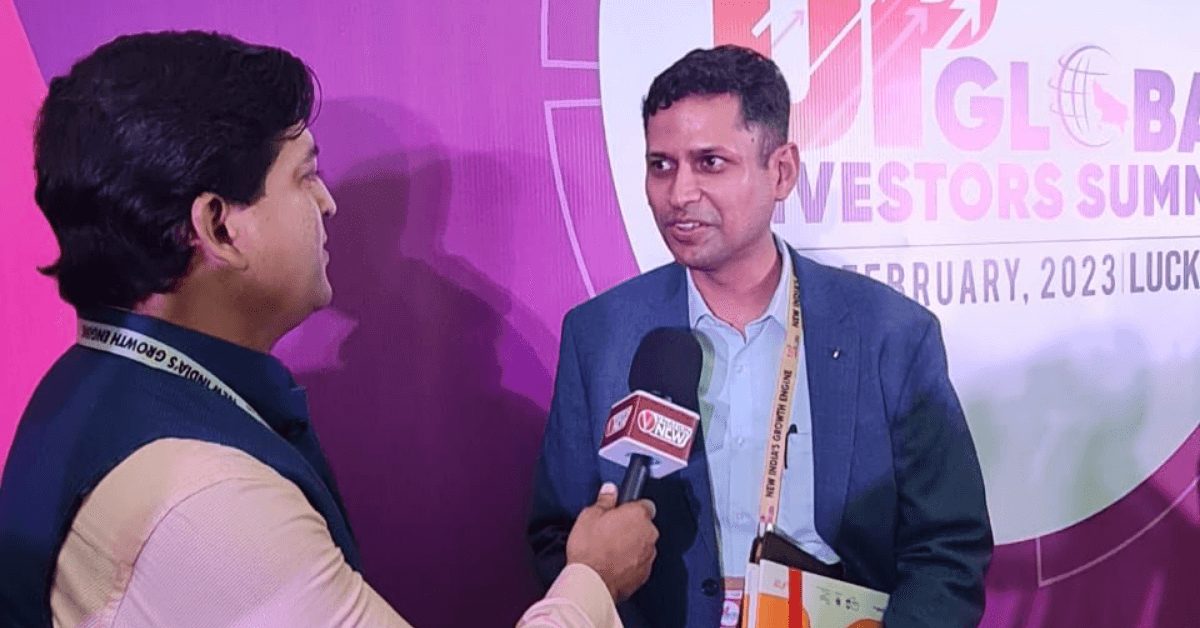
Uttar Pradesh Global Investors Summit 2023
Date : February 11, 2023
Organizer: Invest UP
About the Event:Mr. Rahul Garg, Founder & CEO, Moglix shared his thoughts on ‘Gearing for Start-up Revolution – The Next Big Opportunity in UP’ at Uttar Pradesh Global Investors Summit 2023 in Lucknow.