13th Procurement excellence summit & Awards 2025
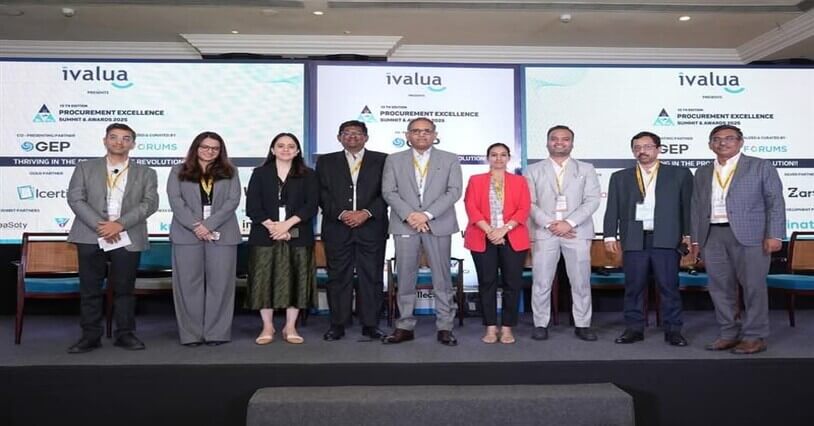
13th Procurement excellence summit & Awards 2025
Date: 20th Febuary ‘2025
Organizer: UBS Forums
About the event: Mr. Anshul Khandelwal, Director at Moglix, recently addressed the 13th Edition Procurement Excellence Summit and Awards 2025, organized by UBS Forums Pvt. Ltd.. In the session, ‘Procurement Innovation and Digital Transformation: End to End Visibility in the Procurement Process,’ he highlighted the pivotal role of generative AI in procurement, emphasizing its usage in driving process innovation and efficiency.
3rd MIDDLE EAST PROCURETECH SUMMIT & AWARDS 2025
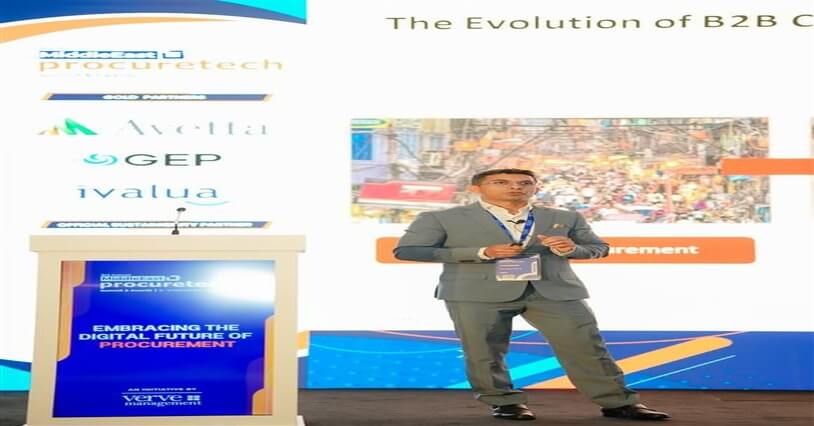
3rd MIDDLE EAST PROCURETECH SUMMIT & AWARDS 2025
Date: 18th – 19th February
Organizer: Verve Management
About the event: Mr. Piyush Malviya, Vice President & Head – MEA at Moglix, took the stage at the 3rd Annual Middle East Procuretech Summit & Awards 2025 to discuss “Smart Procurement Marketplaces: The Future of B2B Commerce” in Dubai. From digital procurement transformation to AI-driven efficiencies, he shared key insights on how smart marketplaces are reshaping global supply chains and empowering businesses with seamless, data-driven procurement.
Rahul Garg, Founder and CEO of Moglix, recently shared his insights on NDTV Profit about the company’s pivotal role in India’s energy transition
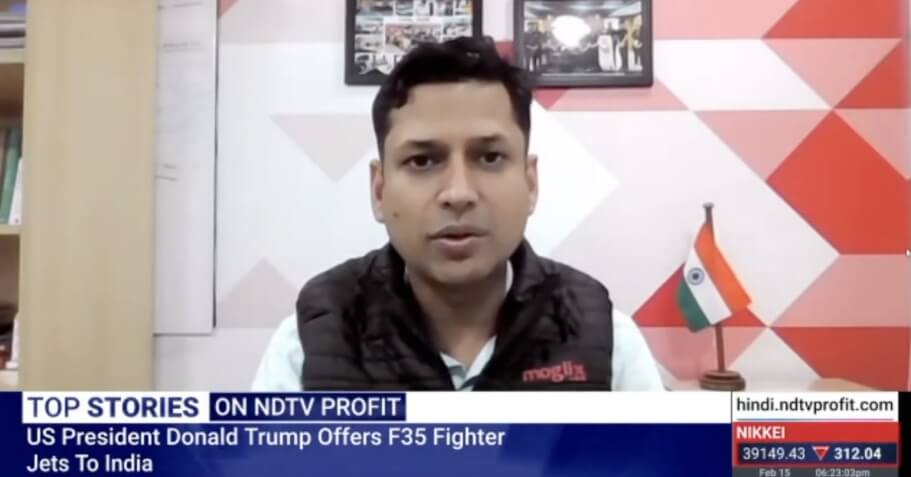
Rahul Garg, Founder and CEO of Moglix, recently shared his insights on NDTV Profit about the company’s pivotal role in India’s energy transition
Rahul Garg, Founder and CEO of Moglix, recently shared his insights on NDTV Profit about the company’s pivotal role in India’s energy transition. He emphasized how Moglix is leveraging technology and innovation to drive sustainability across industrial supply chains. Garg highlighted that the company is committed to providing businesses with cost-effective and eco-friendly solutions, which are essential for decarbonizing logistics and manufacturing. As India moves towards cleaner energy, Moglix is positioning itself at the forefront of this transformation, ensuring industries embrace a sustainable, efficient, and future-ready approach to energy use and industrial operations.
Read MoreIndia Energy Week
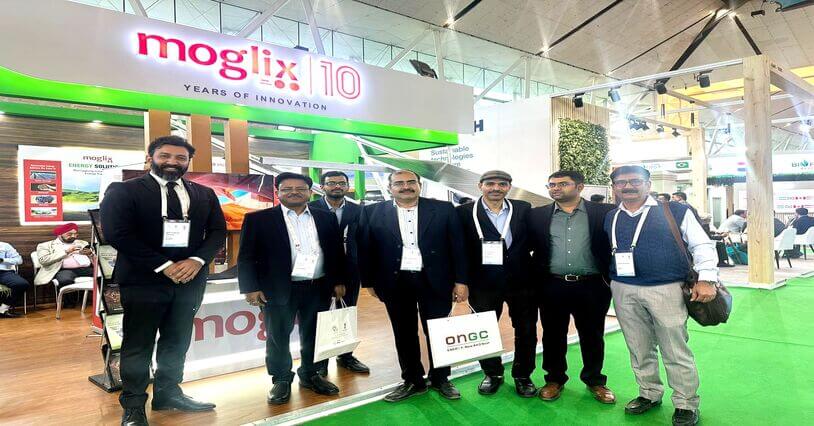
India Energy Week
Date: 11th – 14th February
Organizer: DMG Events
About the event: From groundbreaking innovations to inspiring conversations, this week was a powerful reminder of how collaboration and technology are shaping the future of energy. It’s been an honor to be part of this dynamic exchange of ideas and solutions, driving sustainable progress forward.A look back at the best moments from the event—because the journey to a smarter, greener future is just getting started!
Budget 2025 Expectations: Fostering a startup ecosystem for India’s manufacturing renaissance
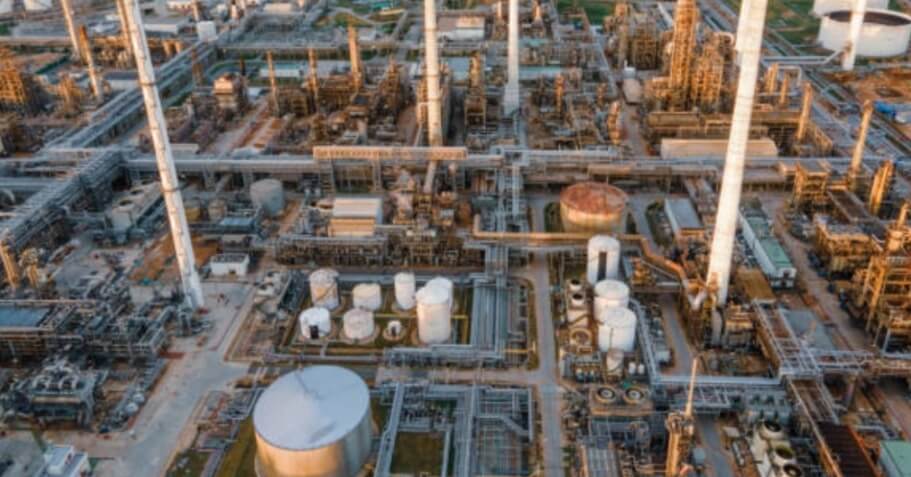
Budget 2025 Expectations: Fostering a startup ecosystem for India’s manufacturing renaissance
Regarding budget expectations 2025, Rahul Garg highlighted the importance of accelerating emerging industries, with India’s growing semiconductor sector leading the way. As initiatives like the India Semiconductor Mission gain momentum, Garg emphasized how semiconductor startups are poised for success. He also pointed out the India Electronics and Semiconductor Association’s proposal to extend the PLI scheme with an additional $20 billion allocation over the next five years, further bolstering India’s manufacturing growth in 2025.
Read MoreBudget 2025 Expectations Highlights: From tax relief to capex boost, all eyes on FM Nirmala Sitharaman on February 1
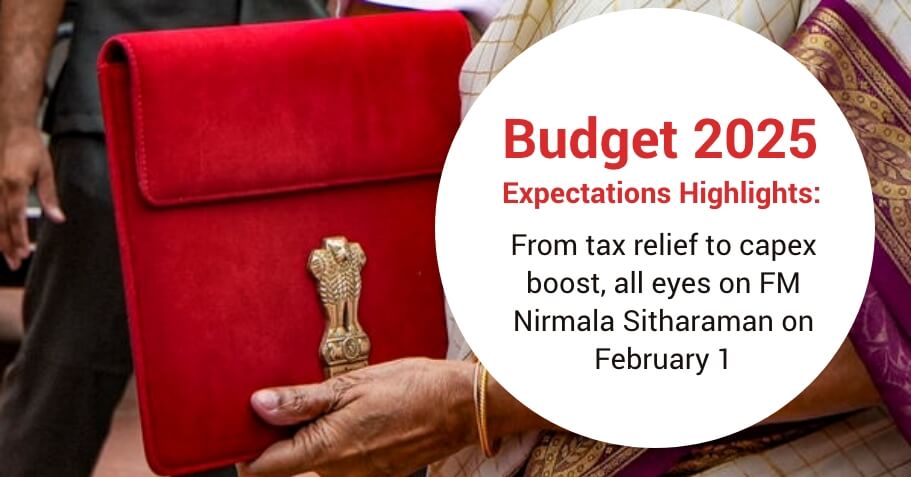
Budget 2025 Expectations Highlights: From tax relief to capex boost, all eyes on FM Nirmala Sitharaman on February 1
Rahul Garg shared his insights on Budget 2025, highlighting the immense potential of semiconductors, sustainable manufacturing, and automation in driving India’s trillion-dollar economy vision. He emphasized that these sectors are vital for industrial growth and offer exciting opportunities for startups to lead in innovation and technology. As India strengthens its global position, focusing on these areas will transform manufacturing, boost economic growth, and position the country as a leader in the global supply chain ecosystem.
“Dedicated funding pools, tax incentives for investors, and streamlined implementation frameworks are crucial to achieving this vision,” said Garg.
Read MoreFIEO and Credlix Sign MoU to Empower Indian Exporters with Financial and Logistical Support
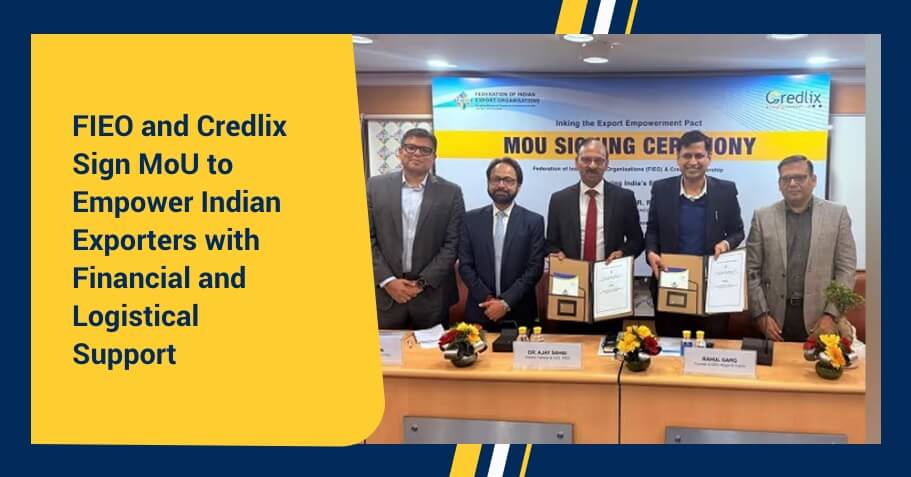
FIEO and Credlix Sign MoU to Empower Indian Exporters with Financial and Logistical Support
Credlix partners with the Federation of Indian Export Organisations (FIEO) through a landmark Memorandum of Understanding (MoU) to empower Indian exporters with smarter financial tools and seamless logistics. This collaboration aims to simplify international trade for Indian businesses by offering access to cutting-edge supply chain financing solutions, enhanced logistical capabilities, and essential support systems. By bridging financial gaps and reducing operational complexities, Credlix and FIEO plans to enable Indian exporters to scale globally, improve cash flow efficiency, and strengthen their competitiveness in international markets.
Read MoreMoglix Supplier meet – Bangalore
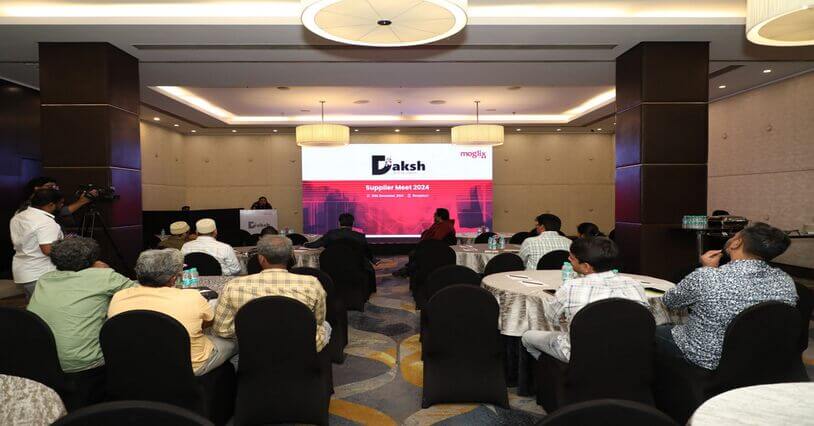
Moglix Supplier meet – Bangalore
Date: 20th December’2024
Organizer: Moglix
About the Event: We recently hosted Moglix Supplier Meet – Daksh in Bangalore, bringing together our esteemed suppliers for a day of collaboration, knowledge sharing, and valuable feedback under the theme “Winning Together.”Mr. Chaitanya Kulkarni, Director at Moglix, and Mr. Nikesh Bhanti, Bangalore Head at Moglix, presented innovative strategies to enhance partnerships and foster growth.
Supply Chain event
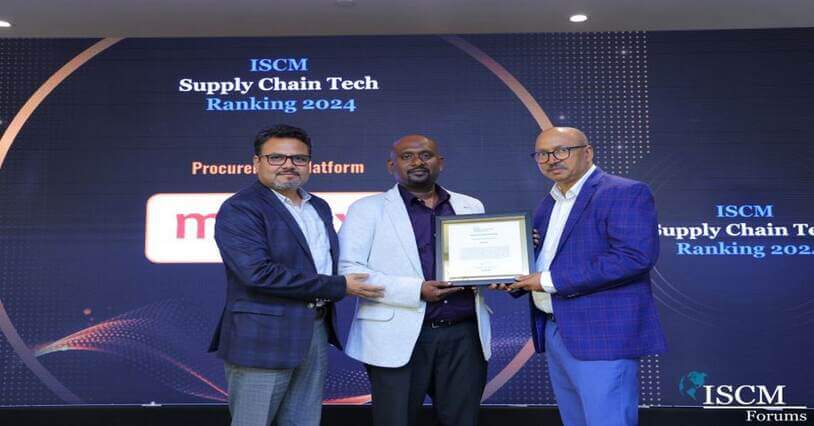
Supply Chain event
Date: 18th December’2024
Organizer: ISCM
About the Event: We are happy to share that Moglix was recently recognized as one of the Top 10 Technology Solution Providers in Procurement domain by ISCM Forums at the 2nd India Supply Chain Tech Senate 2024. The event celebrated the remarkable achievements of India’s Supply Chain Technology Champions, bringing together the best minds and innovations in the industry.
9th ETAuto EV Conclave
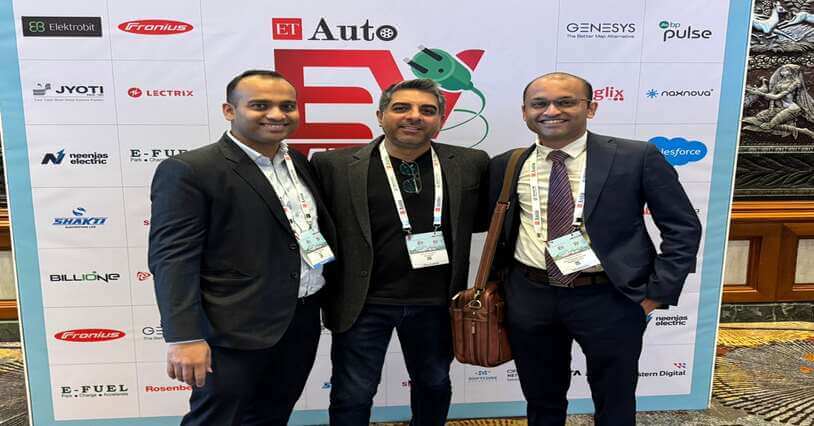
9th ETAuto EV Conclave
Date: 11th – 12th December’2024
Organizer: ET Auto
About the Event: Moglix recently participated in the 9th ETAuto EV Conclave in New Delhi, where industry leaders discussed strategies to accelerate India’s EV transition.The event highlighted key trends and strategies driving EV adoption, focusing on advancing technology, expanding infrastructure, shaping policies, and navigating market dynamics to achieve India’s ambitious EV goals by 2030.