Warehouse Efficiency 101: Strategies for Avoiding the Most Common Pitfalls
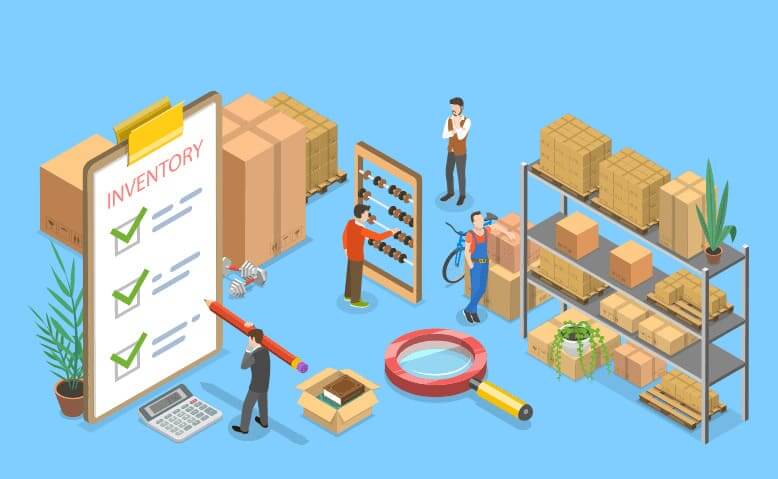
Are you struggling with warehouse efficiency and feeling like it’s holding back your business growth? Don’t worry, you’ve come to the right place! In this article, we’ll provide you with valuable insights on how to optimize your operations and overcome the stumbling blocks that are hindering your warehouse efficiency. Whether it’s the imbalanced stock, warehouse layout, employee training or even tech and equipment, we’ve covered it all! Get ready to unleash the proven strategies to propel your business forward!
Table of Contents
- Introduction
- Messy Warehouse Layout
- Imbalanced stock
- Not looking after equipment
- Not using tech right
- Deficiency in employee training
- Conclusion
Introduction
In the world of B2B supply chains, time is like gold in your pocket. Surprisingly, only about 22% of businesses have really dialed in their supply chain game. Imagine the potential waiting to be unlocked! It’s like having a treasure trove of opportunities just waiting for the taking.
And every second wasted due to inefficiencies costs you financially and gives your competitors an edge. Let’s see the common pitfalls in the warehouse and how to avoid them.
- Messy Warehouse Layout
A confusing layout can slow things down for a manufacturing industry. Instead, focus on optimizing your warehouse layout. In the realm of manufacturing, an inefficient layout can significantly impede productivity. Therefore, it’s crucial to optimize your warehouse layout for seamless operations.
- Aisles: Much like well-maintained paths in a park, ensure your aisles are narrow enough. When designing warehouse aisles, it’s important to strike a balance between width and efficiency. Narrow aisles can help facilitate efficient movement and access to different sections of the warehouse.
- Product Placement: Prioritize proximity to the exit for high-demand products. Placing frequently requested items near the exit streamlines the retrieval process, enhancing efficiency.
- Signage: Think of signage as the street signs within your warehouse. Clear, visible labels and signs help workers locate items swiftly, reducing search times and increasing productivity.
- Adaptability: Embrace a culture of adaptability. Regularly assess and, if needed, reconfigure your layout based on evolving demands. This flexibility ensures that your warehouse remains optimized for current production needs.
By paying attention to these key factors, you can significantly enhance the efficiency and productivity of your manufacturing warehouse.
- Imbalanced Stock OR Uneven inventory
- Good Systems: Establish a robust tracking system to monitor inventory levels within the warehouse. Utilize advanced software solutions tailored to the manufacturing industry, ensuring accurate and real-time stock visibility.
- Rotate Stock: Prioritize a “first in, first out” (FIFO) approach. Ensure older materials or products are positioned at the front while newer items are placed at the back. This rotation helps to keep inventory fresh and minimizes the risk of obsolete goods.
- Regular Checks: Conduct routine inspections to validate physical inventory against digital records. This practice helps identify discrepancies early, allowing for prompt corrective action and preventing potential production delays.
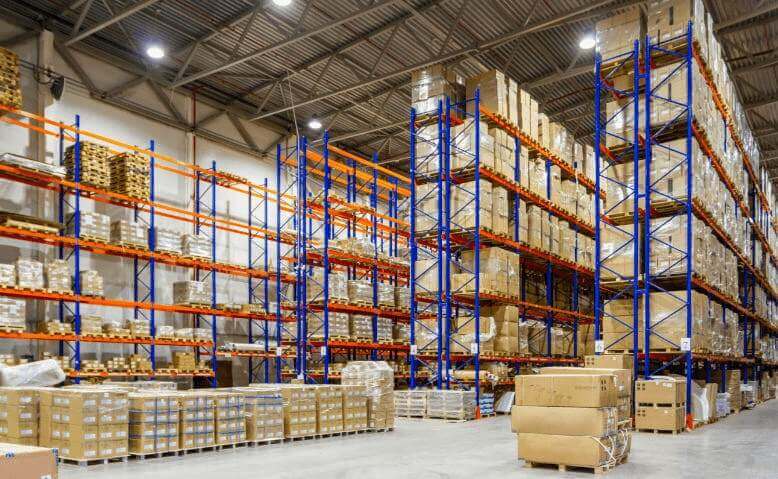
- Lagging on equipment care
- Update Equipment: Periodically evaluate the condition of your machinery. In some cases, retiring older machines in favor of newer, more efficient models is a strategic move to enhance productivity.
- Fix Problems Fast: Promptly address any malfunctions or breakdowns. Swift repairs prevent disruptions to the production process and curtail potential complications.
- Regular Checks: Implement routine maintenance checks akin to health check-ups for machines. This proactive approach helps identify and address potential issues before they escalate.
- Not Using Tech Right
Tech can help, but only if used properly. Only 63% of businesses have tech solutions in place.
- Pick Wisely: Get tech tools that fit your needs.
- Train Everyone: Make sure everyone knows how to use new tools.
- Have a Plan B: If tech breaks down, know what to do next. For example, if a warehouse relies on automated conveyor systems for transporting goods, a backup plan could involve having manual conveyor systems available in case of a breakdown.
- Deficit in staff training
The people who work in your warehouse are on the front lines. They know the ins and outs of daily operations and can provide invaluable insights:
- Training: Ensure everyone is well-trained and up-to-date with the latest best practices and technology.
- Feedback Loop: Create a system where employees can easily share their observations and suggestions. They might spot potential problems or have ideas for improvements that have yet to cross your mind.
- Reward System: Recognise and reward employees for their ideas and efforts to improve warehouse efficiency. A motivated team can make a significant difference in achieving operational excellence.
- Open Communication: Foster an environment where communication flows freely. When everyone is on the same page, avoiding and addressing common pitfalls becomes a collective effort.
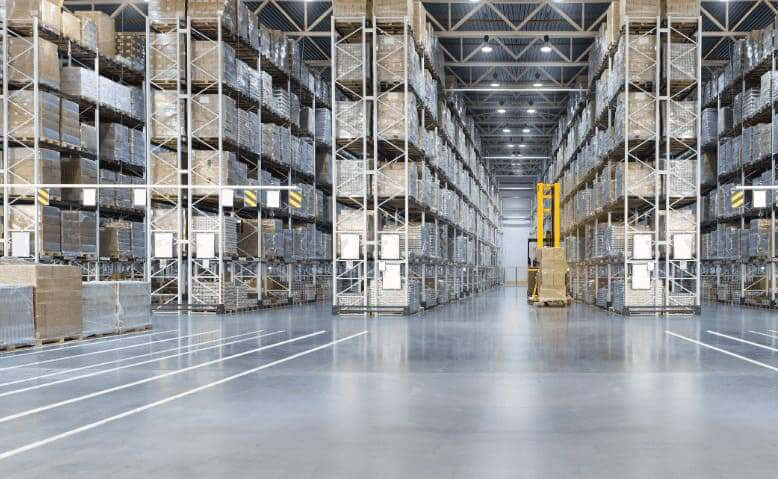
Conclusion
Warehouse inefficiency can cause 34% of delays in shipping, which causes unnecessary business costs. Here is one case in which Moglix has solved the problems of un-optimised inventory, data discrepancies and a fragmented vendor base. You can achieve a streamlined, efficient warehouse operation by avoiding these pitfalls. Regularly review processes, embrace data-driven decision-making and adjust proactively to stay ahead in the competitive B2B supply chain management world.