CII Two-Wheeler Industry Summit
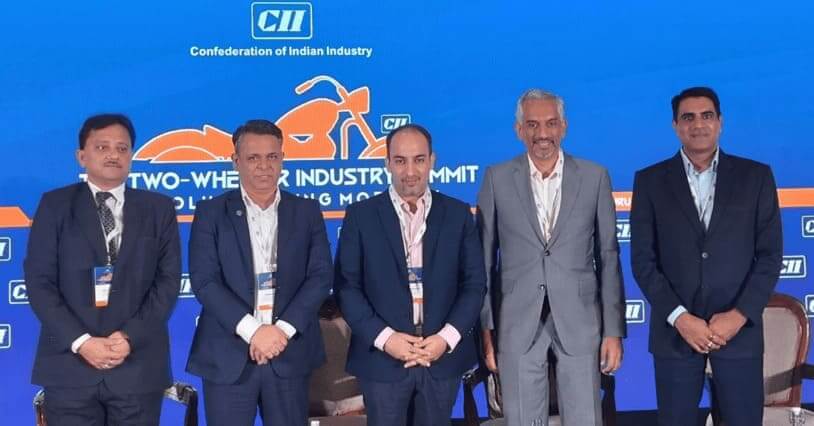
CII Two-Wheeler Industry Summit
Date: Sep 21st , 2023
Organizer: CII
About the Event: Mr. Mukund Vasudevan, Managing Director at Moglix, recently shared his insights during the ‘CII Two-Wheeler Industry Summit: Revolutionizing Mobility,’ where the focus was on ‘Building India into a Global Manufacturing Hub for Two-Wheelers: Addressing Challenges and Seizing Opportunities.’
IMT Round Table Discussions on `Sustainable Supply Chain Strategies`
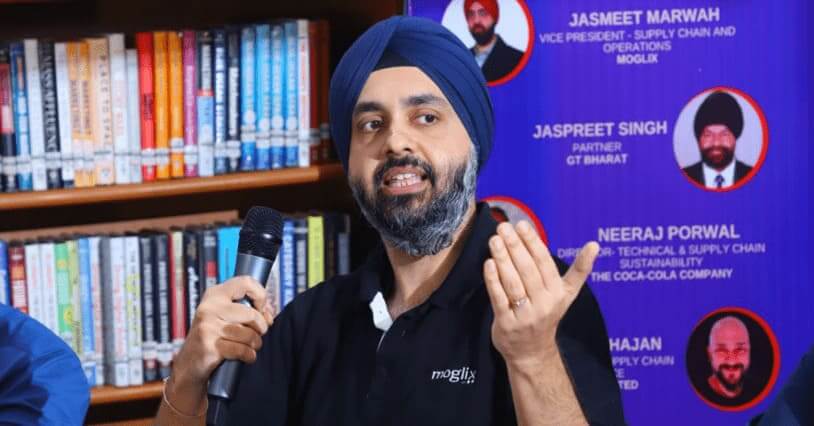
IMT Round Table Discussions on `Sustainable Supply Chain Strategies`
Date: Aug 25th , 2023
Organizer: IMT
About the Event: Mr. Jasmeet Marwah, Vice President of Moglix, recently participated in an Industry-Academia Round Table event centered around the theme of “Sustainable Supply Chain Strategies.” The event was organized by the Institute of Management Technology, Ghaziabad.
Seminar on Various Financing Options in International Trade for Engineering Industries
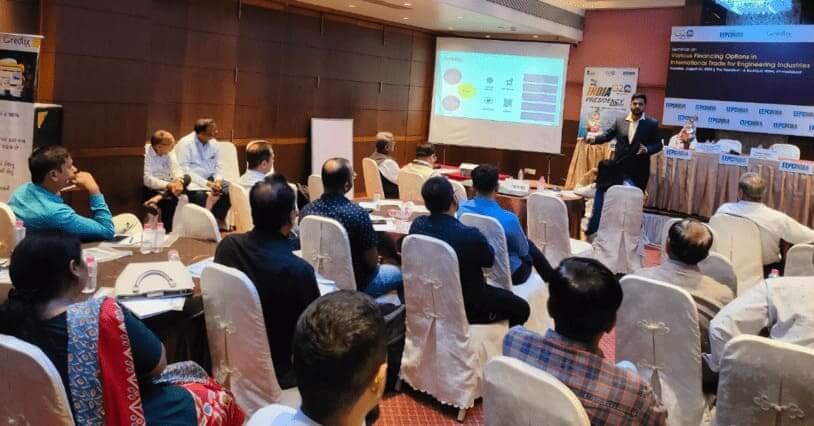
Seminar on Various Financing Options in International Trade for Engineering Industries
Date: Aug 24TH 2023
Organizer: EEPC India
About the Event: Mr. Aakash Mulchandani, Senior Manager, Credlix recently had an opportunity to present on “Achieve Rapid Business Growth through Export Financing” at the seminar on Various Financing Options in International Trade for Engineering Industries organized by EEPC INDIA.
TechManch 2023
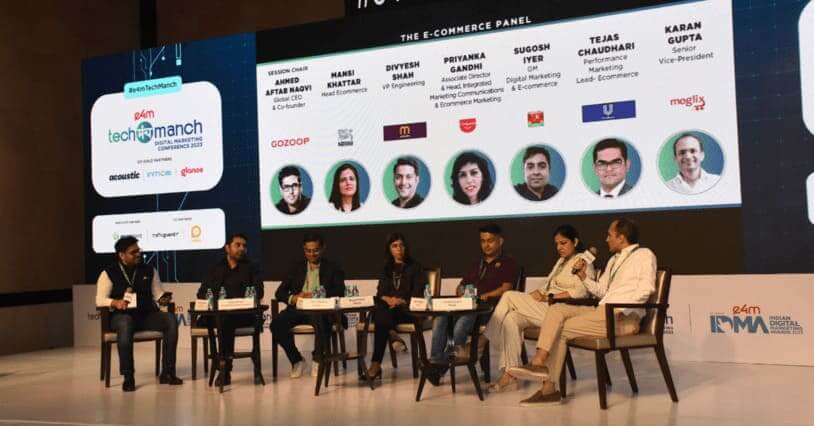
TechManch 2023
Date: Aug 10th 2023
Organizer: Exchange4media
About the Event: Karan Gupta (Senior Vice President, Moglix), graced the spotlight to share profound insights into ‘Building E-Commerce for the Bharat’ at the distinguished TechManch 2023 event, hosted by exchange4media.
Entrepreneur Live India 2023
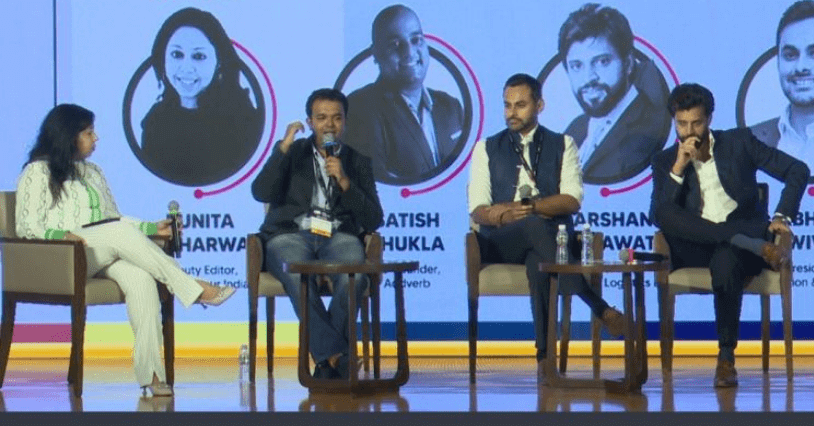
Entrepreneur Live India 2023
Date: 20th November 2023
Organizer: Entrepreneur India
About the Event:Mr. Abheet Dwivedi, Vice President at Moglix, shared his insights on “The Made in India Big Promise Towards the Making of Manufacturing Powerhouse at the Entrepreneur Live x India Investment Forum 2023
All Roads Lead Cricket Fans to the Narendra Modi Stadium: The ICC Men`s World Cup 2023 Final

All Roads Lead Cricket Fans to the Narendra Modi Stadium: The ICC Men`s World Cup 2023 Final
Mark your calendars for an electrifying spectacle in the world of cricket as the grand finale of the ICC Men’s World Cup 2023 Final is set to light up the Narendra Modi Stadium in Ahmedabad on Thursday, November 19. This guide details how to reach Ahmedabad and the stadium seamlessly and also explores the city’s rich tapestry of cuisine, history, and shopping.
How Cricket Fans Can Reach Ahmedabad and Return to Their Base?
Having set the stage for what awaits in Ahmedabad during the cricket World Cup final, let us guide you through the practicalities of your journey. From the moment you land in this bustling city, the avenues to reach your cricket destination are manifold and well-facilitated.
Read on to discover the most efficient modes of transport to enhance your World Cup experience.
Sardar Vallabhbhai Patel International Airport
Visitors attending the ICC Men’s World Cup 2023 at the Narendra Modi Stadium in Ahmedabad, boasting a capacity of 132,000, can expect seamless travel via the Sardar Vallabhbhai Patel International Airport (SVPI), which accommodated over 10 million passengers and managed upwards of 80,000 aircraft movements in the 2022-23 fiscal year. As the seventh-busiest airport in India, SVPI offers an array of domestic and international flights, ensuring a convenient journey for cricket fans.
With all seats likely to be filled for the final, a full house will enjoy the facilities and services of this airport, located just 8.4 km from the stadium—a short 17-minute drive along the Gandhinagar-Ahmedabad Road.
Ahmedabad Railway Station
Ahmedabad Railway Station connects travelers directly to the excitement of cricket matches. Efficiently linking major Indian cities such as Mumbai, Delhi, Jaipur and Udaipur, the station has essential services and helpful staff to ensure a smooth and pleasant journey for all cricket fans.
Road: National Expressway 1
For fans driving to the matches, National Expressway 1 offers a quick link between Ahmedabad and Vadodara, cutting down travel time and ensuring a fast track to the cricketing action.
How Can Cricket Fans Reach the Narendra Modi Stadium?
The final leg to the Narendra Modi Stadium is straightforward. Opt for a quick taxi ride, use the local metro service with a stop close to the stadium, or hop on the Bus Rapid Transport System (BRTS) for a direct route. These convenient options ensure that fans can reach the excitement of the match with ease.
For those arriving by air or train, Ahmedabad Metro connects key points like the airport and railway station to the stadium area, ensuring no fan misses the opening toss. With the Gujarat State Road Transport Corporation (GSRTC) providing extensive bus services and a plethora of taxis and rickshaws on standby, accessing the stadium from any part of the city is convenient and efficient. Whether you prefer the independence of a private car or the local flavor of a bus ride, reaching the cricketing action is straightforward and hassle-free.
For cricket fans planning to witness the electrifying atmosphere at Narendra Modi Stadium, here’s how to get there by local means like metro railway networks in India:
Metro Rail
The closest metro stop is the Motera Metro Station, a mere 1.5 kilometers from the stadium. A short taxi or auto-rickshaw ride can bridge the gap with ease.
Road: Bus/Cab
Indiranagar, the nearest bus stand, offers frequent services, while taxis or app-based cabs provide a more direct route to the stadium.
What to Explore in Ahmedabad?
Ahmedabad offers a cornucopia of experiences for visitors, from delectable culinary delights to sports tourism and vibrant markets for the ultimate shopping experience.
For Foodies:
Manek Chowk Food Court in Ahmedabad: It’s home to a wide variety of street food vendors, serving up everything from dabeli to dhokla to jalebi. The atmosphere is electric, and the food is delicious and affordable.
Agashiye restaurant in Ahmedabad: This rooftop restaurant offers stunning views of the city and serves up some of the best Gujarati thalis in Ahmedabad.
Vishalla restaurant in Ahmedabad: This popular restaurant is known for its authentic Gujarati cuisine. The menu features a wide variety of dishes, from Gujarati specialties like dhokla and khaman to more traditional Indian dishes like butter chicken and biryani.
Swati Snacks restaurant in Ahmedabad: This vegetarian snack shop is a popular spot for a quick bite. The menu features a variety of snacks, from samosas to dahi puri to sev puri.
House of MG restaurant in Ahmedabad: This restaurant is located in a 1920s-era mansion and serves up some of the best fine dining in Ahmedabad.
For History Buffs:
History enthusiasts can delve into India’s heritage at the Sabarmati Ashram, the tranquil abode of Mahatma Gandhi, and wander through the ancient Bhadra Fort. Kankaria Lake offers picturesque views, and the intricate carvings of Adalaj Stepwell are a testament to the architectural prowess of bygone eras.
For Shoppers:
Shoppers can revel in the bustling Lal Darwaja and Sindhi markets for textiles and handicrafts. Dhalgarwad’s traditional attire and Law Garden Night Market’s vibrant atmosphere offer a treasure trove for those seeking the essence of Gujarati craft and apparel. These markets present an array of items reflecting Gujarat’s rich tapestry of culture.
As the final of the ICC Men’s Cricket World Cup draws near there will be a surge in the number of fans heading to Narendra Modi Stadium in Ahmedabad. Businesses across the city need to step up their game and make sure they have supplies for hospitality, and urban transport infrastructure. With railway stations, roads and top airports in India expected to experience an influx of people it is crucial to have seamless coordination and sufficient materials to manage crowds efficiently and ensure everyone’s safety.
In this scenario, Moglix stands out as a specialist in procurement. They are well equipped to offer a range of supplies and infrastructure supply chain solutions that will help businesses meet the demands of this exciting sporting event with the utmost efficiency. If you want information about how Moglix can assist with construction raw materials procurement solutions, visit the website.
The Road to Eden Gardens, Kolkata: How Cricket Fans Can Maximize Semi Final 2, ICC Men`s World Cup 2023
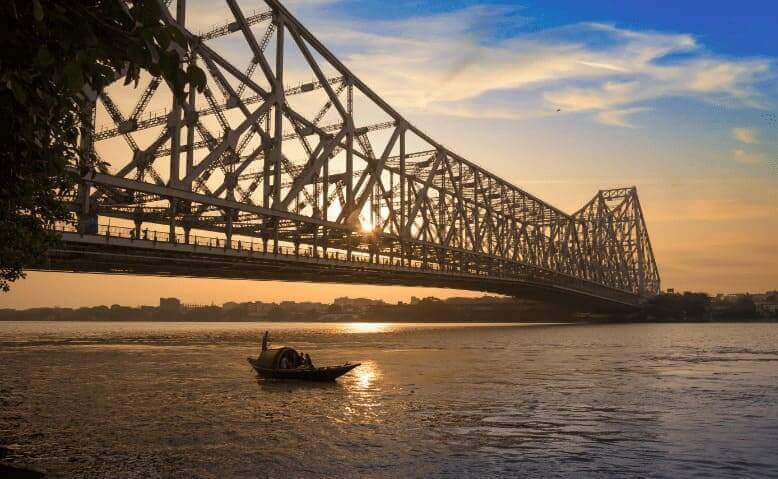
The Road to Eden Gardens, Kolkata: How Cricket Fans Can Maximize Semi Final 2, ICC Men`s World Cup 2023
ICC Men’s World Cup 2023 Semi-Final 2 is set to occur at the Eden Gardens on November 16, 2023, and is expected to burst at the seams despite its capacity to accommodate 66,000 spectators.
Read along as we talk about how you can reach Eden Gardens during what we can call is going to be one of the most nail-biting cricket matches.
How Cricket Fans Can Reach Kolkata and Return to Their Base?
To reach Kolkata during the ICC Men’s World Cup 2023, you can choose from any of the following options:
By Air
Netaji Subhash Chandra Bose International Airport is one of the top airports in India, connected to major cities worldwide. While it is 20 km from Eden Gardens, you can easily flag a cab or bus.
By Rail
While Kolkata has a large railway network, the major railway stations are Howrah and Sealdah, which connect with all major cities of India. Remember that Howrah is India’s busiest railway station, with 600 trains passing daily. So, take care of yourselves and the luggage.
By Road
If you want a road trip adventure, take the National Highway (NH) 19 route. Part of the Golden Quadrilateral, NH 19 connects Kolkata to three major metropolitan cities — Delhi, Mumbai, and Chennai. Moreover, NH 19 is also a part of the Grand Trunk Road—Asia’s oldest and longest road—that connects Kolkata and Agra.
How Cricket Fans Can Reach the Eden Gardens?
Now that you’ve reached Kolkata, here’s how to reach Eden Gardens:
Metro
Kolkata metro is not only India’s first metro rail network but is also the first underground metro railway network in India.
The closest metro stations to Eden Gardens are:
- Esplanade
- Chandi Chowk
- Park Street
Road
Get a bus to Eden Gardens or a yellow taxi to Babughat to get to Eden Gardens. You can quickly board these from the Howrah Bridge (Rabindra Setu) or the second Hooghly Bridge (Vivekananda Setu).
You can also get a cab directly to Eden Gardens.
Train
Eden Gardens has its railway station called the Eden Gardens Circular Railway Station. You can ask any local about Chakra Rail for more information.
What to Explore in Kolkata?
Along with enjoying the Semi-Finals 2 in Eden Gardens, here are some other things that you can do in Kolkata:
For Foodies
Every food lover’s paradise, Kolkata, has shops that offer the most delicious food. Some restaurants that you cannot miss out on are:
- Street food (Esplanade)
- Girish Chandra Dey & Nakur Chandra Nandi (near Bethune College)
- Sen Mahasay (Shibdas Bhaduri Street near Mohun Bagan Lane)
For History Buffs
Kolkata has a rich history, and some tourist places that you can visit to experience are:
- Netaji Bhavan (Bose’s birthplace)
- Jorasanko Thakurbari (Tagore’s birthplace)
- 105 Vivekananda Road (Vivekananda’s Birthplace)
- Belvedere Road (Ray’s birthplace)
- Gurudwara Bara Sikh Sangat (Guru Nanak Dev Ji stayed here for a brief period)
For Shoppers
Kolkata is a shopper’s paradise, and there are so many street shops that sell a variety of products, from clothes and jewellery to electronics and handicrafts. Some areas you should visit for street shopping are:
- Gariahat
- New Market
- Shyam Bazaar
The ICC World Cup contributes significantly to the country’s economy; sports tourism benefits the local economy with the footfall rising by 5–10%. Similarly, raw materials procurement benefits the local economy as well, as seen by how the construction of the Golden Quadrilateral resulted in a 43% increase in manufacturing activities and increased employment.
At Moglix, we help improve India’s urban transport infrastructure by streamlining the accessibility and affordability of construction raw materials procurement for building various India’s infrastructure projects. Contact us at info@moglixbusiness.com to learn how we can help you enhance your infrastructure initiatives.
The Road to Wankhede, Mumbai: How Cricket Fans Can Maximize Semi Final 1, ICC Men`s World Cup 2023
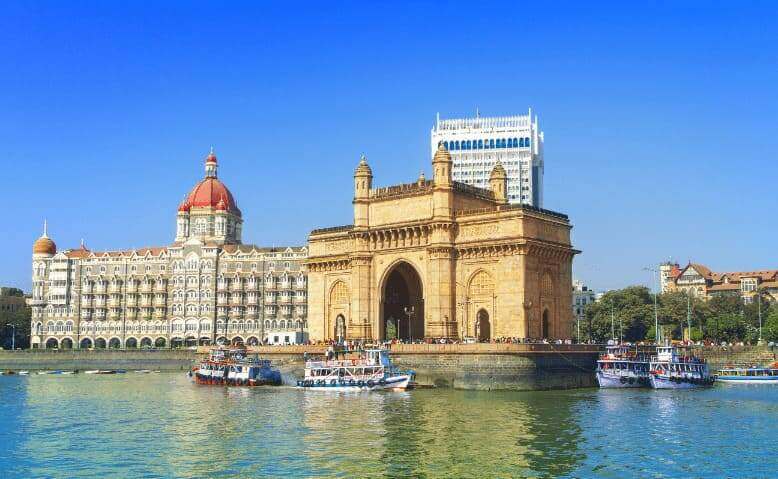
The Road to Wankhede, Mumbai: How Cricket Fans Can Maximize Semi Final 1, ICC Men`s World Cup 2023
On November 15, 2023, Wankhede Stadium, Mumbai will host the first semi-final of the ICC Men’s World Cup 2023. Wankhede Stadium has a capacity of 33,000 and has seen some historic performances, including India’s legendary victory in the ICC Cricket World Cup 2011 final against Sri Lanka.
Keep reading to discover how you can travel to Wankhede Stadium, Mumbai to witness what could be another legendary victory.
Reaching Mumbai
It’s ICC Men’s World Cup 2023 Semi-Final 1, so expect high travel-ticket prices, but you still have options to choose from:
Air
Chhatrapati Shivaji International Airport, one of the top airports in India, has an average footfall of 140,000 passengers across more than 880 flights. It is also the second busiest; pre-book your cabs to avoid rushing.
Train
The Mumbai metro railway network in India carries about 7 million commuters daily, making it the world’s busiest railway system. For easy commuting, the National High-Speed Rail Corporation Limited is working on its bullet train project, connecting Mumbai and Ahmedabad.
Road
You can use the National Highway (NH) 48, part of the Golden Quadrilateral, to reach Mumbai by road. While the highway connects Mumbai to Delhi and Chennai, it passes through cities like Ahmedabad, Pune, Jaipur, and Bhubaneswar.
The traffic congestion on the highway could ease up, as in 2022, Nitin Gadkari—Transport Minister—laid the foundation for 19 projects worth ₹1,000 crore to prevent traffic and accidents on the NH 48.
Navigating the City to Reach Wankhede Stadium
Once you’ve reached Mumbai, it won’t be long before you experience its infamous traffic. Here are some tips to avoid getting stuck:
Metro
Mumbai Metro operates a line between Ghatkopar and Versova from 5:30 am to 11:20 pm. It stops on the following major points:
- Ghatkopar
- Jagrutinagar
- Asalpha
- Saki Naka
- Marol Naka
Bus/Cab
Flag a cab or auto or board a bus for travelling to and from Wankhede Stadium. Some key transit points that you can follow when travelling by road are:
- Vashi bus and metro station
- Apna Bazar Vashi Sector 17
- Vashi Highway
You could also take the Mumbai Trans Harbor Link, India’s longest sea link bridge, as it connects the stadium to Navi Mumbai.
Local Train
Take any train to Churchgate Railway Station, just 600 m from the stadium.
Places You Cannot Miss in Mumbai
Just because you’re here to see India win the Semi-Final 1 doesn’t mean you cannot explore Mumbai. Mumbai has something for everyone:
For Foodies
Some iconic spots you should try are:
- Muhammad Ali Road (kebabs)
- Cafe Madras Matunga (South Indian)
- Gaylord Marine Drive (fine dining)
- Sahibaan Worli (North Indian)
- Martin’s Colaba (Goan food)
- Sarvi Nagpada (Mughlai food)
For History Buffs
Visit the following historic tourist spots:
- Elephanta Caves
- Gateway of India
- Kanheri Caves
- Ajanta Caves
For Shoppers
Mumbai is known for its colorful markets; some you could try are:
- Zaveri Bazaar (jewelry)
- Lokhandwala Market (branded clothes and accessories)
- Crawford Market (dry fruits and spices)
- Mangaldas Market (textiles)
- Linking Road (Fashion)
- Hill Road (street shopping)
- Chor Bazaar (antiques)
Sporting events such as the ICC World Cup increase consumer spending across industries such as hospitality. For example, in the IPL 2023 (Q2), customers spent 1.5% more than other quarters.
Besides sports tourism, the procurement of construction raw materials also contributes to the local economy. For example, the bullet train project has created over 90,000 jobs.
At Moglix, we streamline the infrastructure for first mile and mid-mile logistics, contributing to India’s urban transport infrastructure. To understand how we can facilitate your infrastructure projects, email us at info@moglixbusiness.com.
Semiconductors: Pioneering Sustainability and Cost-Effectiveness in Chip-Making
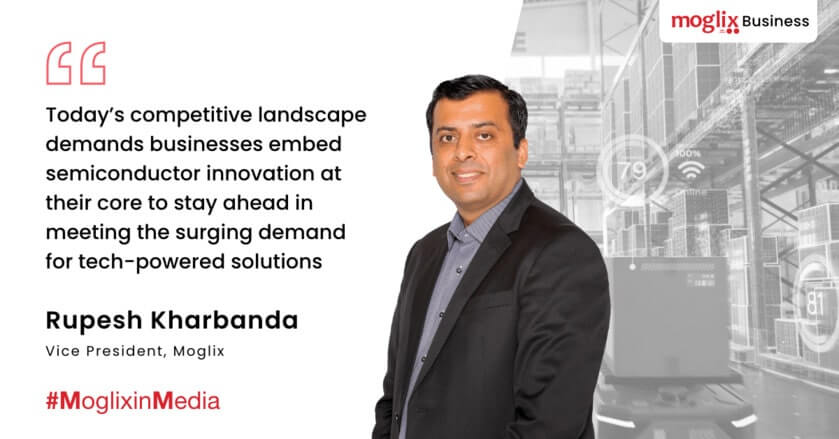
Semiconductors: Pioneering Sustainability and Cost-Effectiveness in Chip-Making
The automotive and manufacturing sectors are experiencing a remarkable acceleration of innovations, primarily attributed to the advent of Industry 4.0. This fourth industrial revolution is founded on cutting-edge technologies such as the Internet of Things (IoT), Artificial Intelligence (AI), and smart manufacturing practices.
And semiconductors are the heart (literally) of this revolution. So, be it a fitness watch, or a self-driving car, microprocessors are the brain of every intelligent system.
Read More“In an era marked by the relentless march of technology, semiconductor innovation stands as the unsung hero powering high-tech manufacturing and the automotive industry.“
Rupesh Kharbanda
India`s Green Hydrogen Ambition: Reshaping the Global Supply Chain
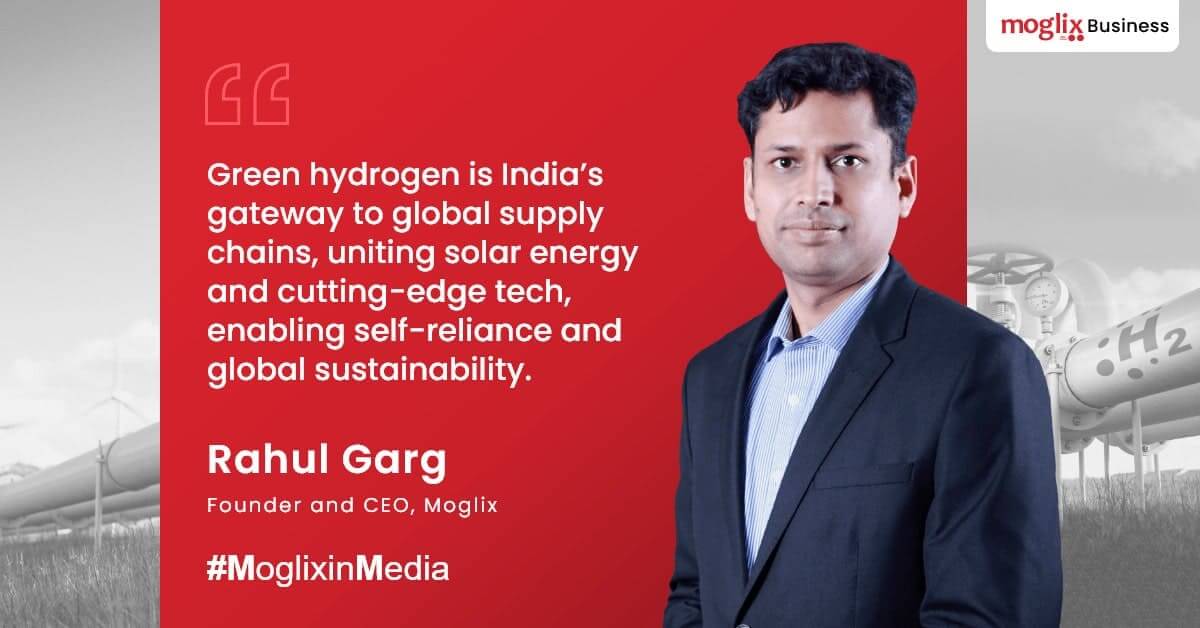
India`s Green Hydrogen Ambition: Reshaping the Global Supply Chain
If you are an independent power producer, infrastructure project developer, sub-contractor or a supplier, will you bet on the chances of scaling green hydrogen?
Like all things manufacturing that travel from the lab scale scientific prototype to industrial scale commercial prototype, green hydrogen too has an inflexion point beyond which it will attain critical mass.