Reimagining Customer Experience in Custom Manufacturing
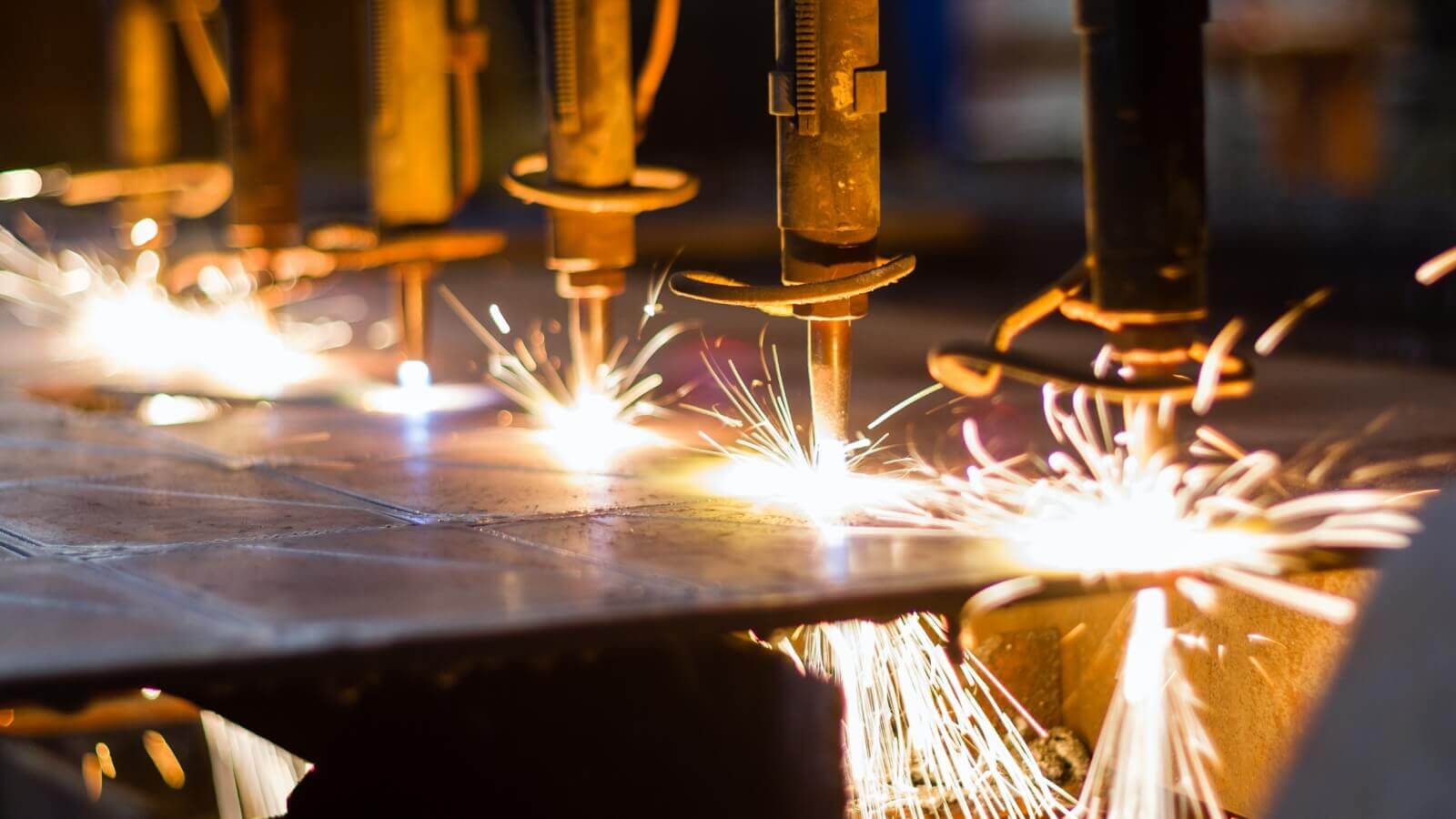
When a butterfly flaps its wings on one side of the world, its ripple effect is felt on the other side—a simple explanation of the complex Chaos Theory, which purports that a small change can have far-reaching implications. After the pandemic, the industry returned to normal, and the rush to build back better meant that infrastructure project completion was a high priority.
Where Does the Infrastructure Boom Come Back to EPC Companies?
For EPC companies in India, the last month has been a roller coaster ride. India’s largest iron ore producer, the state-controlled National Mineral Development Corporation (NMDC), raised prices for a second consecutive month. Cement producers have also had to raise prices due to the disruption in coal and pet coke supply due to the war escalation in Eastern Europe.
What is the Balance Sheet Impact on EPC Companies?
The implications of this unpredictability have immense top-line effects for EPC companies. For example, short delays of even one week in the execution of infrastructure projects in India lead to a 0.01% hike in costs. Over a year, this can lead to 10-12% liquidated damage charges for the EPC contractor.
What Does This Have to Do with Customer Experience in Custom Manufacturing?
Today, a high-quality customer experience is all about outcomes. For an EPC company, unpredictability in material prices, logistics delays, and manual vendor management create a less than ideal user experience. This applies equally to their teams and the customer, usually a public entity.
How Do Moglix Digital Project Management Solutions for Manufacturing Make a Difference?
Global engineering, procurement, and construction companies bank on our digital project solution to transform their custom manufacturing. We provide a wide range of solutions that bring large amounts of spend under control by streamlining your supply chain operations.
The Moglix manufacturing-as-a-service solution is built to enable near real-time visibility into the order-to-delivery of custom manufacturing requirements. Our digital project management platform allows EPC contractors to stay in control of their projects’ custom manufacturing requirements. Our digital track and trace capabilities bring tremendous benefits in planning, price standardization, and collaboration on a single platform. Add an extended network of 40+ multimodal logistics partners and 38+ warehouses which results in seamless collaboration across all stakeholders and keeps project budget overshoot down to the minimum.
The Future of Customer Experience in Custom Manufacturing
Extended features like track and trace, vendor management, and data analytics to predict price fluctuations, supply chain bottlenecks, and material shortfall are ushering the EPC ecosystem into a modern age of transparency and customer-centricity. Many EPC contractors and large infrastructure project companies that are building India’s National Infrastructure Pipeline are already reaping the benefits of our global supply chain expertise combined with our dependable manufacturing network. An efficient and profitable end-to-end project management experience is the key to EPC companies delivering a superior customer experience. It is the future of custom manufacturing and it is unfolding now.